Introduction to Manufacturing Single Mouse Devices
The computer mouse has become an indispensable tool in the modern world, allowing users to navigate digital interfaces with ease and precision. As technology continues to advance, the demand for efficient and cost-effective manufacturing processes for single mouse devices has grown significantly. In this article, we will explore the design and manufacturing aspects of single mouse devices, focusing on the latest trends, techniques, and innovations in the industry.
The Evolution of the Computer Mouse
Since its invention in the 1960s, the computer mouse has undergone numerous transformations to become the sleek and functional device we know today. The first mouse, developed by Douglas Engelbart, used two perpendicular wheels to track movement and had a single button. Over the years, the design has been refined to include optical sensors, wireless connectivity, and ergonomic features to enhance user comfort and productivity.
The Importance of Single Mouse Manufacturing
Single mouse devices are essential for a wide range of applications, from personal computing to professional design and gaming. The manufacturing process plays a crucial role in ensuring that these devices are reliable, durable, and cost-effective. By optimizing the design and manufacturing processes, companies can produce high-quality single mouse devices that meet the needs of diverse users.
Key Components of a Single Mouse Device
To understand the manufacturing process of a single mouse device, it is essential to familiarize oneself with its key components. A typical single mouse consists of the following parts:
- Housing: The outer shell of the mouse, usually made of plastic or other lightweight materials.
- Buttons: The primary input mechanism, typically consisting of left and right-click buttons and a scroll wheel.
- Optical sensor: A light-emitting diode (LED) and a complementary metal-oxide-semiconductor (CMOS) sensor that tracks movement.
- Circuit board: The electronic component that processes input from the buttons and sensor and communicates with the computer.
- Cable or wireless receiver: The connection between the mouse and the computer, either through a USB cable or a wireless receiver.
Materials Used in Single Mouse Manufacturing
The choice of materials used in the manufacturing of single mouse devices is crucial to their performance, durability, and overall quality. Some of the most common materials include:
- Acrylonitrile Butadiene Styrene (ABS) plastic: A lightweight, durable, and cost-effective material used for mouse housings.
- Polycarbonate (PC) plastic: A stronger and more heat-resistant alternative to ABS, often used in high-end mouse devices.
- Thermoplastic Elastomer (TPE): A soft, rubber-like material used for mouse grips and scroll wheels to enhance user comfort.
- Polytetrafluoroethylene (PTFE): A low-friction material used for mouse feet to ensure smooth gliding on various surfaces.
Material | Properties | Applications |
---|---|---|
ABS plastic | Lightweight, durable, cost-effective | Mouse housings |
PC plastic | Strong, heat-resistant | High-end mouse devices |
TPE | Soft, rubber-like | Mouse grips, scroll wheels |
PTFE | Low-friction | Mouse feet |
Single Mouse Manufacturing Processes
The manufacturing of single mouse devices involves several key processes, each contributing to the final product’s quality and performance. These processes include:
Injection Molding
Injection molding is the most common method for manufacturing plastic mouse housings. This process involves melting plastic pellets and injecting the molten material into a mold cavity. Once cooled, the plastic takes the shape of the mold, creating the desired housing shape. Injection molding offers several advantages, such as high production rates, consistent quality, and the ability to create complex geometries.
PCB Assembly
The printed circuit board (PCB) is the heart of a single mouse device, responsible for processing input and communicating with the computer. The PCB assembly process involves several steps:
- Solder paste application: A thin layer of solder paste is applied to the PCB using a stencil.
- Component placement: Surface-mount devices (SMDs) and other electronic components are placed onto the solder paste using pick-and-place machines.
- Reflow soldering: The PCB is heated in a reflow oven, melting the solder paste and creating a strong bond between the components and the board.
- Inspection: The assembled PCB undergoes visual and automated optical inspection (AOI) to ensure proper component placement and soldering quality.
Final Assembly
Once the housing and PCB are ready, the final assembly process brings all the components together to create a functional single mouse device. This process typically involves the following steps:
- Installing the PCB into the housing.
- Connecting the buttons and scroll wheel to the PCB.
- Attaching the optical sensor and cable (for wired mice) or wireless receiver (for wireless mice).
- Sealing the housing and performing final quality checks.
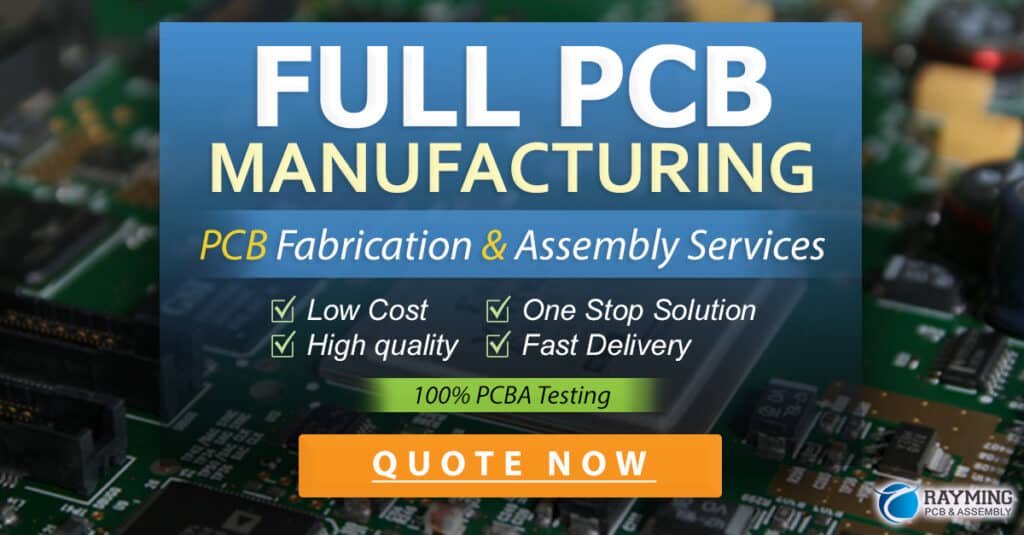
Advancements in Single Mouse Manufacturing
As technology continues to evolve, so do the manufacturing processes for single mouse devices. Some of the latest advancements in the industry include:
3D Printing
3D printing has emerged as a promising technology for rapid prototyping and low-volume production of single mouse devices. This process allows for greater design flexibility, enabling manufacturers to create complex shapes and customized features that would be challenging or impossible with traditional manufacturing methods. Additionally, 3D printing can significantly reduce lead times and costs associated with tooling and mold fabrication.
Automation and Robotics
Automation and robotics have revolutionized single mouse manufacturing, improving efficiency, accuracy, and consistency. Automated assembly lines, equipped with pick-and-place machines and robotic arms, can handle tasks such as component placement, soldering, and final assembly with incredible speed and precision. This not only reduces human error but also allows for higher production volumes and faster time-to-market.
Sustainable Manufacturing Practices
As environmental concerns continue to grow, manufacturers are increasingly adopting sustainable practices in the production of single mouse devices. This includes using eco-friendly materials, such as biodegradable plastics and recycled components, as well as implementing energy-efficient manufacturing processes. By embracing sustainability, companies can reduce their environmental impact while meeting the growing demand for eco-conscious products.
Frequently Asked Questions (FAQ)
-
Q: What is the typical lifespan of a single mouse device?
A: The lifespan of a single mouse device depends on various factors, such as the quality of components, frequency of use, and handling. On average, a well-manufactured mouse can last between 2 to 5 years with proper care and maintenance. -
Q: Are wireless single mouse devices more expensive to manufacture than wired ones?
A: Yes, wireless single mouse devices are generally more expensive to manufacture due to the additional components required, such as the wireless receiver and battery. However, the cost difference has been decreasing as wireless technology becomes more prevalent and cost-effective. -
Q: Can single mouse devices be manufactured using recycled materials?
A: Yes, many manufacturers are now incorporating recycled materials, such as post-consumer plastic, into the production of single mouse devices. This not only reduces the environmental impact but also appeals to eco-conscious consumers. -
Q: How do manufacturers ensure the quality and reliability of single mouse devices?
A: Manufacturers employ various quality control measures throughout the production process, including automated optical inspection (AOI), functional testing, and burn-in testing. These measures help identify and eliminate defects, ensuring that only high-quality products reach the end-users. -
Q: What are the main challenges faced by single mouse device manufacturers?
A: Some of the main challenges include keeping up with rapidly evolving technology, meeting demand for faster time-to-market, and ensuring cost-effectiveness while maintaining high quality standards. Additionally, manufacturers must adapt to changing consumer preferences and navigate an increasingly competitive market.
Conclusion
The design and manufacturing of single mouse devices have come a long way since the invention of the first computer mouse. Today, manufacturers employ advanced technologies, materials, and processes to create high-quality, reliable, and cost-effective products that meet the diverse needs of users worldwide. As technology continues to advance, we can expect to see further innovations in single mouse manufacturing, from 3D printing and automation to sustainable practices and beyond. By staying at the forefront of these developments, manufacturers can ensure that they remain competitive and continue to deliver the best possible products to their customers.
Leave a Reply