Introduction to DFM and DFA
Design for Manufacturing (DFM) and Design for Assembly (DFA) are two essential concepts in modern product development and manufacturing. These methodologies aim to optimize product design to improve manufacturability, reduce costs, and enhance overall product quality. By considering manufacturing and assembly processes during the design phase, companies can streamline their operations, minimize errors, and bring products to market more efficiently.
What is Design for Manufacturing (DFM)?
Design for Manufacturing (DFM) is a product design approach that focuses on simplifying the manufacturing process while maintaining product functionality and quality. The primary goal of DFM is to design products that are easy to manufacture, using readily available materials and processes, and minimizing the number of parts and assembly steps required.
Some key principles of DFM include:
- Simplifying product design
- Standardizing components and materials
- Minimizing the number of parts
- Designing for ease of fabrication and assembly
- Considering manufacturing processes and capabilities
By applying DFM principles, companies can reduce manufacturing costs, improve product quality, and decrease time-to-market.
What is Design for Assembly (DFA)?
Design for Assembly (DFA) is a methodology that focuses on optimizing product design to simplify and streamline the assembly process. The goal of DFA is to reduce the number of parts, minimize assembly time and costs, and improve overall product quality and reliability.
Some key principles of DFA include:
- Minimizing the number of parts
- Designing parts for easy insertion and alignment
- Eliminating fasteners or reducing their number
- Using modular designs and subassemblies
- Considering ergonomics and accessibility for assemblers
By implementing DFA principles, companies can reduce assembly time, minimize errors and rework, and improve product consistency and quality.
Benefits of Implementing DFM and DFA
Implementing DFM and DFA principles in product design and manufacturing offers numerous benefits for companies, including:
-
Cost reduction: By simplifying product design, minimizing parts, and optimizing manufacturing processes, companies can significantly reduce production costs.
-
Improved quality: DFM and DFA help minimize manufacturing and assembly errors, leading to more consistent and reliable products.
-
Faster time-to-market: Streamlined manufacturing and assembly processes enable companies to bring products to market more quickly, gaining a competitive edge.
-
Enhanced collaboration: DFM and DFA encourage cross-functional collaboration between design, engineering, and manufacturing teams, fostering innovation and problem-solving.
-
Increased flexibility: Modular designs and standardized components facilitate product variations and updates, allowing companies to respond more effectively to changing market demands.
Implementing DFM and DFA in the Product Development Process
To successfully implement DFM and DFA, companies must integrate these methodologies throughout the product development process. Here are the key steps involved:
1. Concept Development
During the concept development stage, designers should consider manufacturing and assembly processes when generating and evaluating product ideas. This includes identifying potential challenges and opportunities for simplification and standardization.
2. Design Refinement
As the product design progresses, designers should continuously refine the design with DFM and DFA principles in mind. This involves simplifying the design, minimizing parts, and selecting materials and processes that optimize manufacturability and assembly.
3. Design Reviews
Regular design reviews with cross-functional teams, including manufacturing and assembly experts, are essential for identifying and addressing potential issues early in the development process. These reviews should focus on evaluating the design’s adherence to DFM and DFA principles and identifying opportunities for improvement.
4. Prototyping and Testing
Prototyping and testing help validate the design’s manufacturability and assembly ease. By creating physical prototypes and conducting assembly trials, teams can identify and address any issues before finalizing the design.
5. Production Ramp-Up
As the product moves into production, it is crucial to monitor and optimize manufacturing and assembly processes continuously. This involves collecting data, analyzing performance, and implementing improvements to further enhance efficiency and quality.
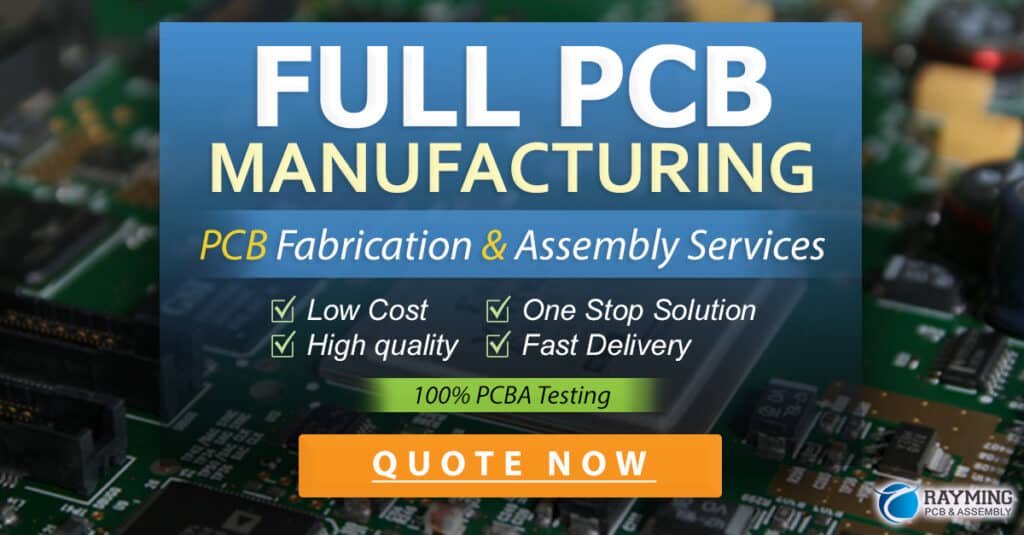
Tools and Techniques for DFM and DFA
Several tools and techniques can support the implementation of DFM and DFA principles in product development and manufacturing. Some of these include:
-
CAD/CAM software: Computer-aided design (CAD) and computer-aided manufacturing (CAM) software help designers create and optimize product designs for manufacturability and assembly.
-
FMEA: Failure Mode and Effects Analysis (FMEA) is a systematic approach to identifying and mitigating potential failures in product design and manufacturing processes.
-
Value Engineering: Value Engineering is a methodology that focuses on improving product value by optimizing functionality while reducing costs.
-
Poka-Yoke: Poka-Yoke is a technique for mistake-proofing manufacturing and assembly processes, minimizing errors and defects.
-
Modular Design: Modular design involves creating products with interchangeable components, facilitating assembly, maintenance, and upgrades.
By leveraging these tools and techniques, companies can more effectively implement DFM and DFA principles and achieve the associated benefits.
Case Studies: Successful Implementation of DFM and DFA
To illustrate the practical application and benefits of DFM and DFA, let’s explore two case studies from different industries.
Case Study 1: Automotive Industry
An automotive manufacturer sought to reduce the production costs and assembly time of a new vehicle model. By applying DFM and DFA principles, the company:
- Simplified the design of various components, such as the dashboard and door panels
- Standardized fasteners and connectors across the vehicle
- Implemented modular subassemblies for easier installation
- Optimized the assembly sequence to minimize handling and movement
As a result, the manufacturer achieved:
- 15% reduction in production costs
- 20% reduction in assembly time
- Improved product quality and consistency
Case Study 2: Consumer Electronics Industry
A consumer electronics company aimed to streamline the manufacturing and assembly of a new smartphone model. By implementing DFM and DFA methodologies, the company:
- Minimized the number of parts in the phone’s design
- Utilized snap-fit connections and eliminated screws where possible
- Designed components for easy insertion and alignment
- Optimized the layout of the PCB for automated assembly
The results of these efforts included:
- 25% reduction in assembly time
- 10% reduction in manufacturing costs
- Faster time-to-market and increased market share
These case studies demonstrate the tangible benefits that companies can achieve by successfully implementing DFM and DFA principles in their product development and manufacturing processes.
Challenges and Best Practices for DFM and DFA Implementation
While implementing DFM and DFA offers significant benefits, companies may face various challenges during the process. Some common challenges include:
- Resistance to change from designers and engineers
- Insufficient cross-functional collaboration and communication
- Lack of expertise in DFM and DFA methodologies
- Balancing product functionality with manufacturing and assembly optimization
To overcome these challenges and ensure successful implementation of DFM and DFA, consider the following best practices:
-
Educate and train teams: Provide comprehensive training on DFM and DFA principles to designers, engineers, and manufacturing personnel to build a shared understanding and commitment to these methodologies.
-
Foster cross-functional collaboration: Encourage regular communication and collaboration among design, engineering, manufacturing, and other relevant teams to ensure a holistic approach to product development.
-
Set clear goals and metrics: Establish specific, measurable goals for DFM and DFA implementation, and track progress using relevant metrics such as cost reduction, assembly time, and quality improvements.
-
Engage suppliers and partners: Involve suppliers and manufacturing partners early in the product development process to leverage their expertise and ensure alignment with DFM and DFA principles.
-
Continuously review and improve: Regularly assess the effectiveness of DFM and DFA implementation, gather feedback from teams, and identify opportunities for further improvement.
By addressing these challenges and adopting best practices, companies can successfully implement DFM and DFA and realize the full potential of these methodologies in their product development and manufacturing processes.
The Future of DFM and DFA
As technology advances and market demands evolve, the application of DFM and DFA principles will continue to play a crucial role in product development and manufacturing. Some emerging trends and future directions for DFM and DFA include:
-
Additive manufacturing: The growing adoption of additive manufacturing (3D printing) technologies will require new approaches to DFM, focusing on design optimization for these processes.
-
Industry 4.0: The integration of smart technologies, such as the Internet of Things (IoT), artificial intelligence (AI), and robotics, will enable more intelligent and adaptive manufacturing systems, requiring DFM and DFA methodologies to evolve accordingly.
-
Sustainable design: As sustainability becomes an increasingly critical concern, DFM and DFA will need to incorporate eco-design principles, such as material selection, energy efficiency, and end-of-life considerations.
-
Mass customization: The trend towards mass customization will require DFM and DFA to support more flexible and agile manufacturing processes, enabling the efficient production of personalized products.
-
Virtual and augmented reality: The use of virtual and augmented reality technologies will enhance the design and validation processes, allowing for more immersive and interactive DFM and DFA evaluations.
By staying attuned to these trends and adapting DFM and DFA methodologies accordingly, companies can remain competitive and innovative in the face of evolving market demands and technological advancements.
Conclusion
Design for Manufacturing (DFM) and Design for Assembly (DFA) are essential methodologies for optimizing product design, streamlining manufacturing and assembly processes, and ultimately driving business success. By implementing DFM and DFA principles throughout the product development process, companies can reduce costs, improve quality, and bring products to market more efficiently.
To successfully implement DFM and DFA, organizations must foster cross-functional collaboration, provide training and education, set clear goals and metrics, and continuously review and improve their processes. By embracing best practices and staying attuned to emerging trends, companies can harness the full potential of DFM and DFA in their product development and manufacturing operations.
As technology and market demands continue to evolve, the application of DFM and DFA principles will remain crucial for companies seeking to maintain a competitive edge and deliver high-quality, cost-effective products to their customers.
Frequently Asked Questions (FAQ)
-
What are the main differences between DFM and DFA?
DFM focuses on optimizing product design for efficient manufacturing, while DFA emphasizes simplifying product design to streamline the assembly process. DFM considers factors such as material selection, fabrication processes, and manufacturing capabilities, while DFA focuses on reducing the number of parts, designing for easy insertion and alignment, and minimizing assembly time and costs. -
How can companies get started with implementing DFM and DFA?
To get started with DFM and DFA implementation, companies should: - Educate and train their teams on DFM and DFA principles
- Establish cross-functional collaboration among design, engineering, and manufacturing teams
- Set clear goals and metrics for DFM and DFA implementation
- Start with pilot projects to demonstrate the benefits and refine processes
-
Continuously review and improve DFM and DFA practices based on feedback and results
-
What are some common challenges in implementing DFM and DFA?
Some common challenges in implementing DFM and DFA include resistance to change from designers and engineers, insufficient cross-functional collaboration, lack of expertise in DFM and DFA methodologies, and balancing product functionality with manufacturing and assembly optimization. To overcome these challenges, companies should focus on education, fostering collaboration, setting clear goals, and engaging suppliers and partners. -
How can DFM and DFA help reduce production costs?
DFM and DFA help reduce production costs by: - Simplifying product design and minimizing the number of parts
- Standardizing components and materials
- Optimizing manufacturing processes and minimizing scrap and rework
- Reducing assembly time and costs through design for easy insertion and alignment
-
Minimizing the need for specialized tools and equipment
-
What role will DFM and DFA play in the future of manufacturing?
DFM and DFA will continue to play a crucial role in the future of manufacturing, adapting to emerging trends such as additive manufacturing, Industry 4.0, sustainable design, mass customization, and virtual and augmented reality. As technology and market demands evolve, DFM and DFA methodologies will need to incorporate new principles and tools to support more flexible, agile, and sustainable manufacturing processes.
Leave a Reply