What is Design Manufacturing and Assembly (DFMA)?
Design for Manufacturing and Assembly (DFMA) is a systematic approach to designing products that are optimized for efficient manufacturing and assembly processes. The goal of DFMA is to reduce production costs, improve product quality, and shorten time-to-market by considering the manufacturing and assembly aspects during the early stages of product design.
DFMA involves two main components:
- Design for Manufacturing (DFM)
- Design for Assembly (DFA)
Design for Manufacturing (DFM)
DFM focuses on designing products that are easy to manufacture. This involves optimizing the product design to minimize the complexity of manufacturing processes, reduce the number of parts, and ensure the compatibility of materials and processes. By implementing DFM principles, companies can:
- Reduce manufacturing costs
- Improve product quality
- Minimize waste and scrap
- Shorten production lead times
Some key considerations in DFM include:
- Material selection
- Process capabilities and limitations
- Tolerances and dimensions
- Standardization of parts and processes
Design for Assembly (DFA)
DFA aims to simplify and optimize the assembly process by designing products that are easy to assemble. This involves reducing the number of parts, minimizing the need for specialized tools, and ensuring that parts are easy to handle and orient during assembly. By implementing DFA principles, companies can:
- Reduce assembly time and costs
- Improve product quality and reliability
- Enhance worker safety and ergonomics
- Facilitate automation and robotics integration
Key considerations in DFA include:
- Part count reduction
- Standardization of fasteners and connectors
- Minimizing the need for adjustments and alignments
- Designing for ease of insertion and handling
The Benefits of DFMA
Implementing DFMA principles in product design and development offers numerous benefits to manufacturers, including:
-
Cost reduction: By optimizing product designs for manufacturing and assembly, companies can significantly reduce production costs, including material, labor, and overhead expenses.
-
Improved product quality: DFMA helps to minimize manufacturing defects and assembly errors, resulting in higher product quality and customer satisfaction.
-
Shortened time-to-market: By considering manufacturing and assembly aspects early in the design process, companies can avoid costly design changes and tooling modifications, ultimately reducing development time and accelerating product launches.
-
Enhanced collaboration: DFMA encourages cross-functional collaboration between design, engineering, manufacturing, and supply chain teams, fostering a more integrated and efficient product development process.
-
Increased competitiveness: By delivering high-quality products at lower costs and shorter lead times, companies can gain a competitive edge in their respective markets.
Implementing DFMA in Product Development
To successfully implement DFMA in product development, companies should follow these key steps:
-
Establish DFMA guidelines and best practices: Develop a set of DFMA principles and guidelines that align with your company’s manufacturing capabilities, product requirements, and industry standards.
-
Train and educate teams: Provide training and education to design, engineering, and manufacturing teams on DFMA principles and best practices to ensure a common understanding and consistent application across the organization.
-
Integrate DFMA into the design process: Incorporate DFMA considerations into the early stages of product design, using tools such as design checklists, DFMA software, and cross-functional design reviews.
-
Collaborate with suppliers and partners: Engage with suppliers and manufacturing partners early in the design process to ensure that product designs are compatible with their capabilities and can be efficiently manufactured and assembled.
-
Continuously monitor and improve: Regularly assess the effectiveness of your DFMA implementation, collect feedback from teams and stakeholders, and identify areas for improvement to continuously refine your DFMA practices.
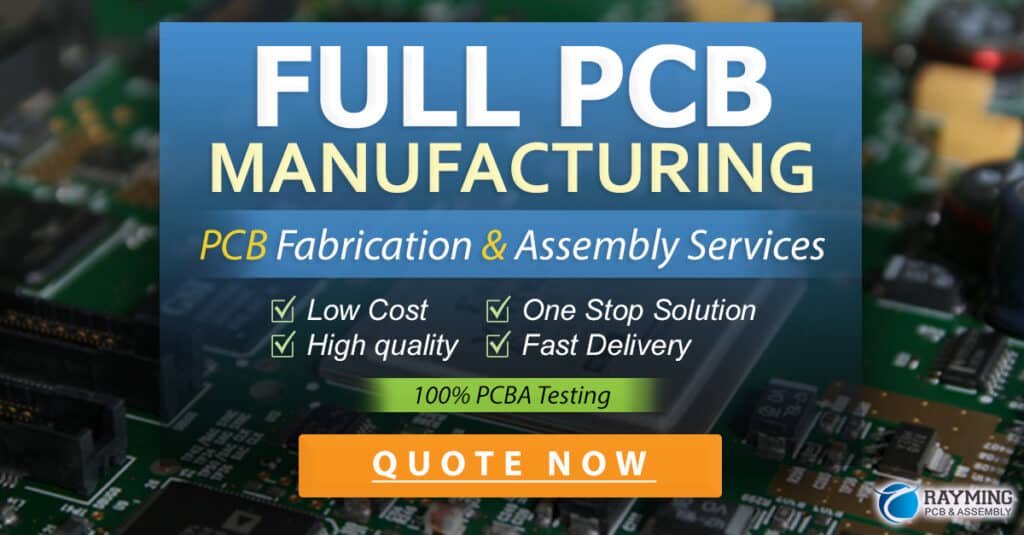
Case Studies and Examples
Case Study 1: Automotive Component Manufacturer
An automotive component manufacturer implemented DFMA principles in the design of a new engine control module. By optimizing the design for manufacturing and assembly, the company achieved the following results:
- Reduced part count from 120 to 85 components
- Shortened assembly time by 25%
- Decreased manufacturing costs by 18%
- Improved product quality and reliability
Case Study 2: Medical Device Company
A medical device company applied DFMA principles in the development of a new insulin delivery system. The benefits of DFMA implementation included:
- Simplified product design with fewer parts and standardized components
- Reduced assembly time by 30%
- Minimized manufacturing defects and assembly errors
- Shortened time-to-market by 20%
Predictive Engineering and DFMA
Predictive engineering is a complementary approach to DFMA that involves using advanced simulation and analysis tools to predict and optimize product performance, manufacturability, and assembly. By leveraging predictive engineering techniques, companies can:
- Identify potential design issues early in the development process
- Optimize product designs for specific manufacturing processes and assembly methods
- Reduce the need for physical prototypes and testing
- Minimize the risk of costly design changes and production delays
Predictive engineering tools and techniques include:
- Finite Element Analysis (FEA)
- Computational Fluid Dynamics (CFD)
- Topology optimization
- Virtual manufacturing simulation
By combining DFMA principles with predictive engineering, companies can achieve a more comprehensive and proactive approach to product design and development, ultimately leading to better products, lower costs, and faster time-to-market.
Frequently Asked Questions (FAQ)
- What is the difference between Design for Manufacturing (DFM) and Design for Assembly (DFA)?
-
DFM focuses on optimizing product designs for efficient manufacturing processes, while DFA aims to simplify and optimize the assembly process.
-
How does DFMA help to reduce production costs?
-
DFMA helps to reduce production costs by minimizing the complexity of manufacturing processes, reducing the number of parts, optimizing material usage, and streamlining assembly operations.
-
What are some key considerations in Design for Manufacturing (DFM)?
-
Key considerations in DFM include material selection, process capabilities and limitations, tolerances and dimensions, and standardization of parts and processes.
-
How can predictive engineering complement DFMA?
-
Predictive engineering complements DFMA by using advanced simulation and analysis tools to predict and optimize product performance, manufacturability, and assembly, helping to identify potential design issues early and reduce the risk of costly changes and delays.
-
What are the main benefits of implementing DFMA in product development?
- The main benefits of implementing DFMA in product development include cost reduction, improved product quality, shortened time-to-market, enhanced collaboration, and increased competitiveness.
Conclusion
Design for Manufacturing and Assembly (DFMA) is a powerful approach to product design and development that helps companies to optimize their products for efficient manufacturing and assembly processes. By considering manufacturing and assembly aspects early in the design process, companies can reduce production costs, improve product quality, and shorten time-to-market.
Implementing DFMA principles requires a systematic and collaborative approach, involving cross-functional teams, supplier engagement, and continuous improvement. When combined with predictive engineering techniques, DFMA can provide a comprehensive and proactive approach to product design and development, ultimately leading to better products, lower costs, and faster time-to-market.
As manufacturing technologies and customer requirements continue to evolve, the importance of DFMA will only continue to grow. By embracing DFMA principles and best practices, companies can position themselves for success in an increasingly competitive and dynamic market landscape.
Leave a Reply