Understanding Wireless PCB Design Requirements
Before diving into the design process, it is crucial to understand the specific requirements of your wireless PCB project. Consider the following factors:
-
Wireless standard: Determine the wireless standard (e.g., Wi-Fi, Bluetooth, Zigbee, NFC) that your PCB needs to support. Each standard has its own set of specifications and requirements.
-
Frequency band: Identify the frequency band(s) in which your wireless PCB will operate. Common bands include 2.4 GHz, 5 GHz, and sub-GHz frequencies.
-
Range and power consumption: Define the desired range and power consumption targets for your wireless PCB. These factors will influence component selection and layout decisions.
-
Form factor and mechanical constraints: Consider the physical dimensions and mechanical constraints of your PCB, such as size limitations, mounting requirements, and enclosure design.
Selecting the Right Components for Your Wireless PCB
The success of your wireless PCB heavily depends on the selection of appropriate components. Pay attention to the following key components:
Wireless Module or Chipset
Choose a wireless module or chipset that supports your target wireless standard and frequency band. Consider factors such as:
- Compatibility with your chosen microcontroller or processor
- Integrated vs. discrete solutions
- Certified vs. non-certified modules
- Power consumption and sleep modes
- Antenna interface (e.g., single-ended, differential)
Antenna
The antenna is a critical component in any wireless PCB design. Select an antenna that matches your frequency band and offers the desired radiation pattern. Options include:
- Chip antennas
- PCB trace antennas
- External antennas (e.g., dipole, monopole)
Consider the antenna’s gain, efficiency, and polarization to ensure optimal wireless performance.
Passive Components
Pay attention to the selection of passive components, such as resistors, capacitors, and inductors. Use high-quality components with tight tolerances to minimize variations and ensure consistent performance. Consider the following:
- Impedance matching networks
- Decoupling capacitors
- RF chokes and inductors
- Filtering components
PCB Layout Techniques for Wireless Designs
Proper PCB layout is essential for achieving optimal wireless performance and minimizing interference. Follow these layout techniques:
Component Placement
- Place the wireless module or chipset close to the antenna to minimize signal loss and reflections.
- Keep high-frequency components away from noise-sensitive analog circuits.
- Provide adequate spacing between components to avoid coupling and interference.
Grounding and Power Distribution
- Use a solid ground plane to provide a low-impedance return path for high-frequency signals.
- Implement proper power supply decoupling near active components to reduce noise and ensure stable power delivery.
- Use power planes or wide traces to distribute power evenly across the PCB.
Signal Routing
- Route high-frequency signals using controlled impedance traces to maintain signal integrity.
- Minimize the length of high-frequency traces to reduce losses and reflections.
- Avoid sharp bends and discontinuities in high-frequency traces to prevent impedance mismatches.
- Use via stitching or guard traces to isolate sensitive signals from interference.
Antenna Placement and Routing
- Place the antenna away from noise sources and metal objects that may affect its performance.
- Ensure proper clearance around the antenna to avoid detuning and distortion of the radiation pattern.
- Follow the manufacturer’s guidelines for antenna placement and routing.
- Use impedance-controlled traces to route signals to and from the antenna.
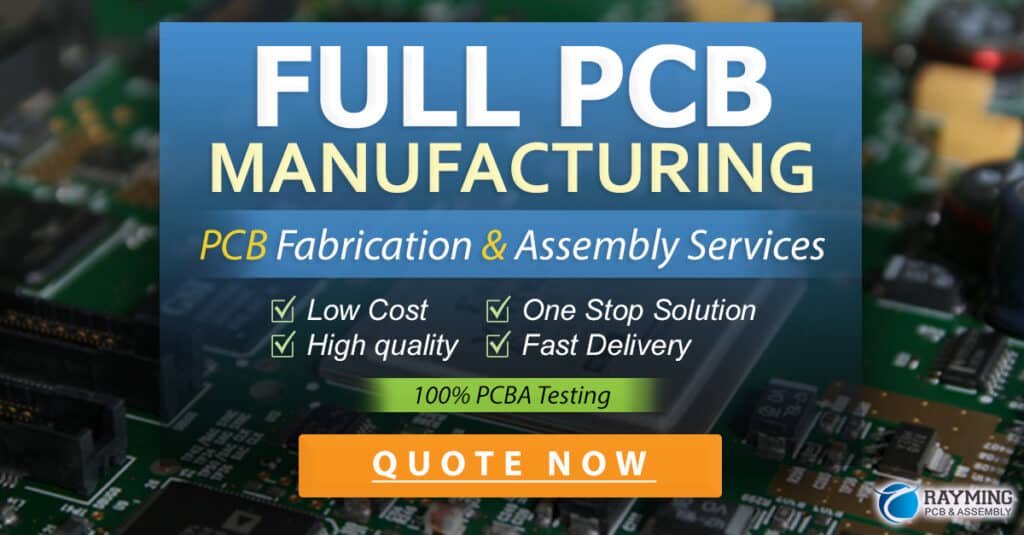
Signal Integrity Considerations
Signal integrity is crucial in wireless PCB design to ensure reliable communication and minimize signal distortion. Consider the following:
Impedance Matching
- Match the impedance of the antenna, transmission lines, and components to minimize reflections and ensure maximum power transfer.
- Use impedance matching networks, such as LC networks or pi networks, to achieve the desired impedance.
Crosstalk and Interference
- Minimize crosstalk between adjacent traces by providing adequate spacing or using guard traces.
- Use shielding techniques, such as ground planes or shielding cans, to reduce interference from external sources.
- Avoid routing sensitive signals parallel to high-speed or noisy traces.
Electromagnetic Compatibility (EMC)
- Ensure that your wireless PCB complies with relevant EMC standards and regulations.
- Implement proper filtering and shielding techniques to minimize electromagnetic interference (EMI) and susceptibility.
- Use ferrite beads, EMI filters, and shielding gaskets as needed.
Testing and Validation
Thorough testing and validation are essential to ensure the performance and reliability of your wireless PCB. Consider the following tests:
Functional Testing
- Verify that your wireless PCB performs its intended functions, such as establishing connections, transmitting and receiving data, and handling various operating modes.
- Perform range tests to ensure the PCB meets the desired coverage requirements.
RF Performance Testing
- Measure key RF parameters, such as transmit power, receiver sensitivity, and antenna gain, to validate the PCB’s wireless performance.
- Use specialized RF test equipment, such as spectrum analyzers and vector network analyzers, for accurate measurements.
EMC Testing
- Conduct EMC tests to ensure that your wireless PCB meets the relevant EMC standards and regulations.
- Perform both radiated and conducted emissions tests to verify that the PCB does not cause excessive interference to other devices.
- Perform immunity tests to ensure that the PCB can operate reliably in the presence of external electromagnetic disturbances.
Environmental Testing
- Subject your wireless PCB to various environmental conditions, such as temperature extremes, humidity, and vibration, to assess its durability and reliability.
- Perform accelerated life testing to identify potential long-term reliability issues.
Wireless PCB Design Checklist
To summarize the key points covered in this article, refer to the following checklist when designing your wireless PCB:
- [ ] Define wireless standard, frequency band, range, and power consumption requirements.
- [ ] Select appropriate wireless module or chipset, antenna, and passive components.
- [ ] Follow best practices for component placement, grounding, power distribution, and signal routing.
- [ ] Implement proper antenna placement and routing techniques.
- [ ] Address signal integrity considerations, including impedance matching, crosstalk, and EMC.
- [ ] Perform thorough testing and validation, including functional, RF performance, EMC, and environmental tests.
Frequently Asked Questions (FAQ)
1. What are the most common wireless standards used in PCB design?
Common wireless standards include Wi-Fi (IEEE 802.11), Bluetooth, Zigbee, and NFC (Near Field Communication). The choice of standard depends on the specific application requirements, such as range, data rate, power consumption, and compatibility with existing devices.
2. How do I select the right antenna for my wireless PCB?
When selecting an antenna for your wireless PCB, consider factors such as frequency band, gain, efficiency, polarization, and form factor. Chip antennas and PCB trace antennas are popular choices for compact designs, while external antennas offer higher gain and flexibility. Consult antenna manufacturers’ datasheets and application notes for guidance on selection and placement.
3. What are the key considerations for PCB layout in wireless designs?
Key considerations for PCB layout in wireless designs include component placement, grounding, power distribution, signal routing, and antenna placement. Proper component placement minimizes signal loss and interference, while a solid ground plane provides a low-impedance return path. Controlled impedance routing and careful antenna placement ensure optimal wireless performance.
4. How can I minimize crosstalk and interference in my wireless PCB?
To minimize crosstalk and interference in your wireless PCB, provide adequate spacing between adjacent traces, use guard traces or ground planes for isolation, and avoid routing sensitive signals parallel to high-speed or noisy traces. Shielding techniques, such as ground planes or shielding cans, can also help reduce interference from external sources.
5. What types of testing are essential for wireless PCB validation?
Essential tests for wireless PCB validation include functional testing, RF performance testing, EMC testing, and environmental testing. Functional testing verifies the PCB’s intended functions, while RF performance testing measures key parameters such as transmit power and receiver sensitivity. EMC testing ensures compliance with relevant standards and regulations, and environmental testing assesses the PCB’s durability and reliability under various conditions.
By following these design guidelines and addressing the common questions, you can enhance the performance, reliability, and compliance of your wireless PCB design. Remember to stay updated with the latest industry trends and regulations to ensure the success of your wireless projects.
Wireless Standard | Frequency Band | Typical Range | Key Features |
---|---|---|---|
Wi-Fi (802.11) | 2.4 GHz, 5 GHz | Up to 100m | High data rates, widespread adoption |
Bluetooth | 2.4 GHz | Up to 10m | Low power, short-range, audio streaming |
Zigbee | 2.4 GHz, 915 MHz | Up to 100m | Low power, mesh networking, home automation |
NFC | 13.56 MHz | Up to 10cm | Short-range, contactless payment, data exchange |
Table 1: Comparison of common wireless standards
Component | Considerations |
---|---|
Wireless module | Standard compatibility, power consumption |
Antenna | Frequency band, gain, efficiency, form factor |
Passive components | Impedance matching, decoupling, filtering |
Table 2: Key components in wireless PCB design
By carefully selecting components, following layout best practices, and conducting thorough testing, you can create a reliable and high-performance wireless PCB that meets your application requirements.
Leave a Reply