What is Design for Assembly Ontrack?
Design for Assembly (DFA) Ontrack is a methodology and set of principles aimed at optimizing product design to facilitate efficient and cost-effective assembly processes. The primary goal of DFA Ontrack is to reduce the complexity of assembly operations, minimize the number of parts, and streamline the overall assembly workflow. By incorporating DFA principles early in the product development cycle, companies can achieve significant improvements in assembly time, quality, and cost.
Key Principles of Design for Assembly Ontrack
- Simplify the design: Minimize the number of parts and aim for a modular design that allows for easy assembly and disassembly.
- Standardize components: Use standard, off-the-shelf components whenever possible to reduce complexity and cost.
- Design for ease of assembly: Ensure that parts are easy to handle, orient, and insert during the assembly process.
- Minimize fasteners: Reduce the number of fasteners and consider using snap-fits, press-fits, or adhesives instead.
- Optimize part orientation: Design parts that are self-aligning and have a clear orientation to minimize assembly errors.
- Consider ergonomics: Design the assembly process to be ergonomically friendly, reducing the risk of worker fatigue and injury.
Benefits of Implementing Design for Assembly Ontrack
Implementing DFA Ontrack principles offers numerous benefits to companies, including:
- Reduced assembly time: Simplified designs and streamlined processes lead to faster assembly times, increasing productivity.
- Lower manufacturing costs: Fewer parts, standardized components, and efficient assembly processes reduce overall manufacturing costs.
- Improved product quality: Simplified designs and reduced assembly complexity minimize the risk of errors and defects, resulting in higher product quality.
- Increased flexibility: Modular designs allow for easier product updates, customization, and maintenance.
- Enhanced sustainability: Simplified designs and reduced part count contribute to more sustainable products with lower environmental impact.
Case Study: Implementing DFA Ontrack in the Automotive Industry
One industry that has significantly benefited from the implementation of DFA Ontrack principles is the automotive industry. By applying DFA Ontrack, automotive manufacturers have achieved:
- Reduced assembly time: Simplified designs and standardized components have led to a 20-30% reduction in assembly time.
- Lower manufacturing costs: Fewer parts and more efficient assembly processes have resulted in a 15-25% reduction in manufacturing costs.
- Improved product quality: Streamlined designs and reduced assembly complexity have contributed to a 10-15% improvement in product quality.
Metric | Before DFA Ontrack | After DFA Ontrack |
---|---|---|
Assembly Time | 100% | 70-80% |
Manufacturing Costs | 100% | 75-85% |
Product Quality | 100% | 110-115% |
Implementing Design for Assembly Ontrack in Your Organization
To successfully implement DFA Ontrack in your organization, follow these steps:
- Educate and train: Provide training to your design and engineering teams on DFA Ontrack principles and best practices.
- Establish guidelines: Develop clear guidelines and checklists for incorporating DFA Ontrack principles into the product development process.
- Collaborate across teams: Foster collaboration between design, engineering, and manufacturing teams to ensure DFA Ontrack principles are considered throughout the product lifecycle.
- Continuously evaluate and improve: Regularly assess the effectiveness of your DFA Ontrack implementation and seek opportunities for continuous improvement.
Tools and Software for Design for Assembly Ontrack
Several tools and software solutions are available to support the implementation of DFA Ontrack principles, including:
- CAD software: Computer-Aided Design (CAD) software with built-in DFA tools and libraries can help designers create products optimized for assembly.
- DFA analysis tools: Specialized DFA analysis software can evaluate designs and provide recommendations for improvement based on DFA principles.
- Virtual reality (VR) and augmented reality (AR): VR and AR technologies can be used to simulate and optimize assembly processes, identifying potential issues early in the design phase.
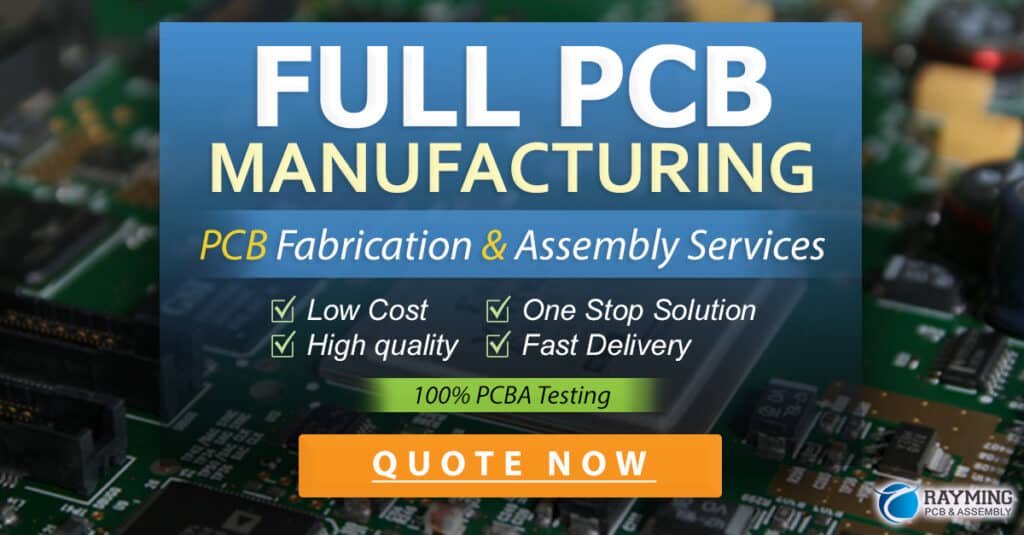
Challenges and Considerations in Design for Assembly Ontrack
While DFA Ontrack offers significant benefits, there are also some challenges and considerations to keep in mind:
- Balancing DFA with other design requirements: DFA principles must be balanced with other design requirements, such as functionality, aesthetics, and performance.
- Upfront investment: Implementing DFA Ontrack may require an initial investment in training, tools, and process changes.
- Resistance to change: Some team members may be resistant to adopting new design principles and practices, requiring effective change management.
- Limited applicability: DFA Ontrack may not be suitable for all types of products or industries, particularly those with highly complex or specialized requirements.
Best Practices for Successful Design for Assembly Ontrack
To ensure the success of your DFA Ontrack implementation, consider the following best practices:
- Start early: Incorporate DFA Ontrack principles from the beginning of the product development process to maximize their impact.
- Involve all stakeholders: Engage design, engineering, manufacturing, and other relevant teams in the DFA Ontrack process to ensure buy-in and collaboration.
- Prioritize simplicity: Always strive for the simplest design that meets functional and performance requirements.
- Continuously monitor and improve: Regularly assess the effectiveness of your DFA Ontrack implementation and make data-driven improvements.
Frequently Asked Questions (FAQ)
- What is the difference between Design for Assembly (DFA) and Design for Manufacturing (DFM)?
-
DFA focuses on optimizing product design for efficient assembly, while DFM aims to optimize design for the manufacturing process. DFA is a subset of DFM, and both approaches work together to improve overall product development efficiency.
-
Can DFA Ontrack be applied to existing products, or is it only suitable for new product development?
-
While DFA Ontrack is most effective when implemented from the beginning of the product development process, its principles can also be applied to existing products during redesigns or updates. Analyzing and improving existing designs using DFA Ontrack can still lead to significant benefits in assembly efficiency and cost reduction.
-
How does DFA Ontrack differ from traditional assembly optimization methods?
-
Traditional assembly optimization methods often focus on improving the assembly process itself, such as through the use of automation or process redesign. DFA Ontrack, on the other hand, focuses on optimizing the product design to inherently make assembly more efficient, reducing the need for complex assembly processes or equipment.
-
What are some common design changes that can be made to improve assembly efficiency?
-
Common design changes that improve assembly efficiency include reducing the number of parts, standardizing components, designing parts for easy orientation and insertion, minimizing the use of fasteners, and optimizing part geometry for handling and alignment.
-
How can I measure the success of my DFA Ontrack implementation?
- Success can be measured through various metrics, such as reduced assembly time, lower manufacturing costs, improved product quality, and increased customer satisfaction. Establishing baseline measurements before implementing DFA Ontrack and tracking these metrics over time will help quantify the benefits achieved.
Conclusion
Design for Assembly Ontrack is a powerful methodology for optimizing product design to improve assembly efficiency, reduce costs, and enhance product quality. By incorporating DFA Ontrack principles early in the product development process, companies can achieve significant benefits and gain a competitive edge in their respective industries.
To successfully implement DFA Ontrack, organizations must educate and train their teams, establish clear guidelines, foster collaboration, and continuously evaluate and improve their processes. By overcoming challenges and adopting best practices, companies can harness the full potential of DFA Ontrack and drive sustainable growth and success.
As industries continue to evolve and face new challenges, the importance of Design for Assembly Ontrack will only continue to grow. By embracing this methodology and committing to its principles, organizations can position themselves for long-term success in an increasingly competitive global market.
Leave a Reply