What is HDI?
High-Density Interconnect (HDI) is a printed circuit board (PCB) design that incorporates higher wiring density per unit area than conventional PCBs. HDI technology enables the miniaturization of electronic devices by allowing for smaller vias, fine pitch components, and thinner materials. This results in improved electrical performance, reduced signal interference, and enhanced reliability.
Key Features of HDI PCBs
- Microvias (µVias)
- Fine pitch components
- Thin dielectric materials
- Copper-filled vias
- Sequential lamination
Benefits of HDI PCB Design
Implementing HDI technology in PCB design offers several advantages:
- Miniaturization: HDI allows for smaller form factors, enabling the development of compact electronic devices.
- Improved Signal Integrity: Shorter signal paths and reduced crosstalk lead to better signal quality and higher speed performance.
- Increased Functionality: With higher component density, HDI PCBs can accommodate more features and functions within a limited space.
- Cost Reduction: Although the initial manufacturing costs may be higher, HDI can reduce overall system costs by minimizing the number of layers and facilitating assembly processes.
HDI Design Guidelines
To ensure successful HDI PCB design, consider the following guidelines:
1. Material Selection
Choose appropriate materials for HDI PCBs, considering factors such as:
- Dielectric constant (Dk)
- Dissipation factor (Df)
- Thermal expansion coefficient (CTE)
- Thermal conductivity
- Moisture absorption
Some commonly used materials for HDI PCBs include:
Material | Dk | Df | CTE (ppm/°C) | Thermal Conductivity (W/mK) | Moisture Absorption (%) |
---|---|---|---|---|---|
FR-4 | 4.5 | 0.02 | 14-18 | 0.3 | 0.1-0.2 |
Polyimide | 3.5 | 0.002 | 12-16 | 0.2 | 1.5-2.0 |
Rogers RO4000 Series | 3.3-3.5 | 0.0027-0.0037 | 11-16 | 0.6-0.7 | 0.06-0.1 |
Isola IS410 | 3.8-4.0 | 0.008-0.01 | 12-14 | 0.6-0.7 | 0.1-0.2 |
2. Via Types and Sizes
HDI PCBs utilize various types of vias, including:
- Through vias
- Blind vias
- Buried vias
- Microvias (µVias)
Consider the following guidelines for via sizes:
Via Type | Diameter (mm) | Depth (mm) |
---|---|---|
Through | 0.3-0.5 | Board thickness |
Blind | 0.1-0.2 | 0.1-0.3 |
Buried | 0.1-0.2 | 0.1-0.3 |
Microvia | 0.05-0.1 | 0.05-0.1 |
3. Trace Width and Spacing
To minimize signal integrity issues, follow these trace width and spacing guidelines:
Signal Type | Trace Width (mm) | Trace Spacing (mm) |
---|---|---|
Digital | 0.075-0.1 | 0.075-0.1 |
Analog | 0.1-0.2 | 0.1-0.2 |
Power | 0.2-0.5 | 0.2-0.5 |
High-speed | 0.075-0.1 | 0.1-0.2 |
4. Component Placement
When placing components on an HDI PCB, consider the following:
- Group components by function and signal type
- Place decoupling capacitors close to power pins
- Minimize the distance between high-speed components
- Avoid placing components under BGA packages
- Ensure proper clearance for assembly and rework
5. Signal Integrity and EMI Reduction
To improve signal integrity and reduce electromagnetic interference (EMI):
- Use controlled impedance traces for high-speed signals
- Implement differential pair routing for high-speed interfaces
- Add ground planes and power planes for shielding and reference
- Avoid routing traces parallel to board edges
- Use via shielding and stitching vias to minimize EMI
6. Thermal Management
Effective thermal management is crucial for HDI PCBs due to their high component density. Consider the following:
- Use thermal vias to dissipate heat from high-power components
- Implement copper pours and ground planes for heat spreading
- Choose materials with high thermal conductivity
- Ensure adequate airflow and cooling solutions in the final assembly
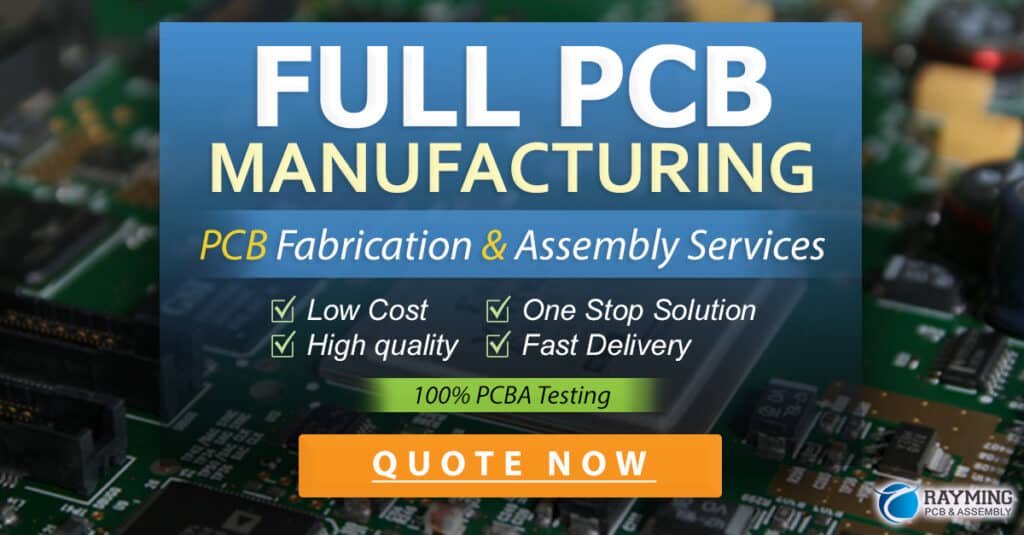
HDI PCB Manufacturing Process
The manufacturing process for HDI PCBs involves several key steps:
- Material Selection: Choose appropriate materials based on the design requirements and product specifications.
- Copper Patterning: Create the desired conductor pattern on the PCB using photolithography and etching processes.
- Lamination: Stack and bond the patterned layers together using heat and pressure.
- Drilling: Drill through holes, blind vias, and buried vias using mechanical or laser drilling techniques.
- Plating: Plate the vias and holes with copper to create electrical connections between layers.
- Solder Mask Application: Apply a solder mask to protect the copper traces and prevent short circuits during assembly.
- Surface Finish: Apply a surface finish, such as ENIG (Electroless Nickel Immersion Gold) or OSP (Organic Solderability Preservative), to enhance solderability and protect the exposed copper.
- Electrical Testing: Perform electrical tests to ensure the PCB meets the specified requirements and functions as intended.
HDI Design Software and Tools
Several software tools are available for HDI PCB design, including:
- Altium Designer: A comprehensive PCB design software that supports HDI design features and 3D modeling.
- Cadence Allegro: An advanced PCB design solution that offers HDI capabilities and signal integrity analysis tools.
- Mentor Graphics PADS: A PCB design software that provides HDI design rules and constraints management.
- Zuken CR-8000: A PCB design platform that supports HDI design, 3D modeling, and multi-board design.
These tools offer features such as:
- HDI design rule checking (DRC)
- Signal integrity analysis
- 3D visualization and modeling
- Automatic via placement and optimization
- Constraint-driven design and routing
Future Trends in HDI PCB Design
As technology advances, HDI PCB design will continue to evolve to meet the growing demands for miniaturization, high-speed performance, and increased functionality. Some future trends in HDI PCB design include:
- Embedded Components: Integrating passive components, such as resistors and capacitors, directly into the PCB substrate to further reduce size and improve performance.
- 3D Printing: Utilizing 3D printing technologies to create complex PCB structures and enable new design possibilities.
- Advanced Materials: Exploring new materials with improved electrical, thermal, and mechanical properties to enhance HDI PCB performance and reliability.
- 5G and Beyond: Designing HDI PCBs that can support the high-frequency and high-bandwidth requirements of emerging wireless technologies like 5G and future 6G networks.
- AI-Assisted Design: Leveraging artificial intelligence and machine learning algorithms to optimize HDI PCB layouts, component placement, and signal routing.
Frequently Asked Questions (FAQ)
-
What is the difference between HDI and traditional PCBs?
HDI PCBs have higher wiring density per unit area compared to traditional PCBs. They feature smaller vias, finer pitch components, and thinner materials, enabling miniaturization and improved electrical performance. -
What are the benefits of using HDI technology in PCB design?
The benefits of HDI technology include miniaturization, improved signal integrity, increased functionality, and potential cost reduction through reduced layer count and simplified assembly processes. -
What materials are commonly used for HDI PCBs?
Common materials for HDI PCBs include FR-4, polyimide, Rogers RO4000 series, and Isola IS410. These materials offer suitable dielectric properties, thermal characteristics, and moisture resistance for HDI applications. -
What are microvias, and why are they important in HDI PCB design?
Microvias (µVias) are small vias with diameters typically ranging from 0.05mm to 0.1mm. They enable higher interconnect density, shorter signal paths, and improved signal integrity in HDI PCBs. -
What software tools are available for HDI PCB design?
Popular software tools for HDI PCB design include Altium Designer, Cadence Allegro, Mentor Graphics PADS, and Zuken CR-8000. These tools offer features such as HDI design rule checking, signal integrity analysis, 3D modeling, and constraint-driven design.
Conclusion
HDI technology has revolutionized PCB design by enabling miniaturization, improved performance, and increased functionality in electronic devices. By understanding the key features, benefits, and design guidelines of HDI PCBs, engineers and designers can create compact, high-performance electronic products that meet the demands of today’s rapidly evolving market.
As technology continues to advance, HDI PCB design will play a crucial role in shaping the future of electronics, from 5G and IoT devices to artificial intelligence and beyond. By staying up-to-date with the latest trends and best practices in HDI design, engineers can unlock new possibilities and drive innovation in their respective fields.
Leave a Reply