What is a Bill of Materials (BOM)?
A Bill of Materials (BOM) is a comprehensive list of raw materials, components, and instructions required to manufacture, assemble, or repair a product. It serves as a crucial document for any manufacturing process, as it ensures that all necessary parts are accounted for and that the final product meets the desired specifications. A well-structured BOM helps streamline production processes, reduce errors, and improve overall efficiency.
Components of a BOM
A typical BOM consists of the following components:
- Part Number: A unique identifier assigned to each component or sub-assembly in the BOM.
- Part Name: A brief description of the component or sub-assembly.
- Quantity: The number of units required for each component or sub-assembly.
- Unit of Measure: The standard unit used to quantify the component (e.g., pieces, liters, kilograms).
- Phase: The stage of the production process in which the component is used.
- Reference Designators: Identifiers that link the components to their respective locations in the product’s design files or schematics.
Reasons for Deleting a Line from a BOM
There are several reasons why you might need to delete a line from a BOM:
- Obsolete Components: As technology advances or product designs change, certain components may become obsolete and need to be removed from the BOM.
- Design Changes: Modifications to the product design may result in the elimination of specific components, requiring their removal from the BOM.
- Supplier Changes: If a supplier discontinues a component or if a more suitable alternative is found, the original component may need to be deleted from the BOM.
- Error Correction: Occasionally, errors may occur during the creation of a BOM, such as duplicate entries or incorrect quantities, which require the removal of the erroneous lines.
Steps to Delete a Line from a BOM
The process of deleting a line from a BOM may vary depending on the software or system you are using. However, the general steps are as follows:
Step 1: Identify the Line to be Deleted
Carefully review the BOM and identify the line containing the component or sub-assembly you wish to remove. Ensure that you have selected the correct line to avoid unintentionally deleting essential components.
Step 2: Verify the Impact of Deletion
Before proceeding with the deletion, assess the potential impact on the overall product and production process. Consider the following:
- Are there any dependencies on the component being deleted?
- Will the deletion affect the functionality or quality of the final product?
- Are there any alternative components that can replace the one being deleted?
Step 3: Update Related Documents
If the component being deleted is referenced in other documents, such as design files, schematics, or work instructions, ensure that these documents are updated accordingly to reflect the change.
Step 4: Delete the Line from the BOM
Using your BOM management software or system, locate the line you wish to delete and follow the appropriate steps to remove it from the BOM. This process may involve:
- Selecting the line and clicking a “Delete” button
- Right-clicking the line and choosing “Delete” from the context menu
- Using a keyboard shortcut, such as “Ctrl+D” or “Cmd+D” (depending on your operating system)
Step 5: Review and Verify the Updated BOM
After deleting the line, carefully review the updated BOM to ensure that the correct line was removed and that no unintended changes were made. Verify that the remaining components and quantities are accurate and that the BOM still represents the complete and correct list of materials required for the product.
Step 6: Save and Distribute the Updated BOM
Once you have confirmed that the BOM is accurate, save the changes and distribute the updated version to all relevant stakeholders, such as production teams, procurement departments, and suppliers. Ensure that everyone is working with the most current version of the BOM to avoid confusion and potential errors.
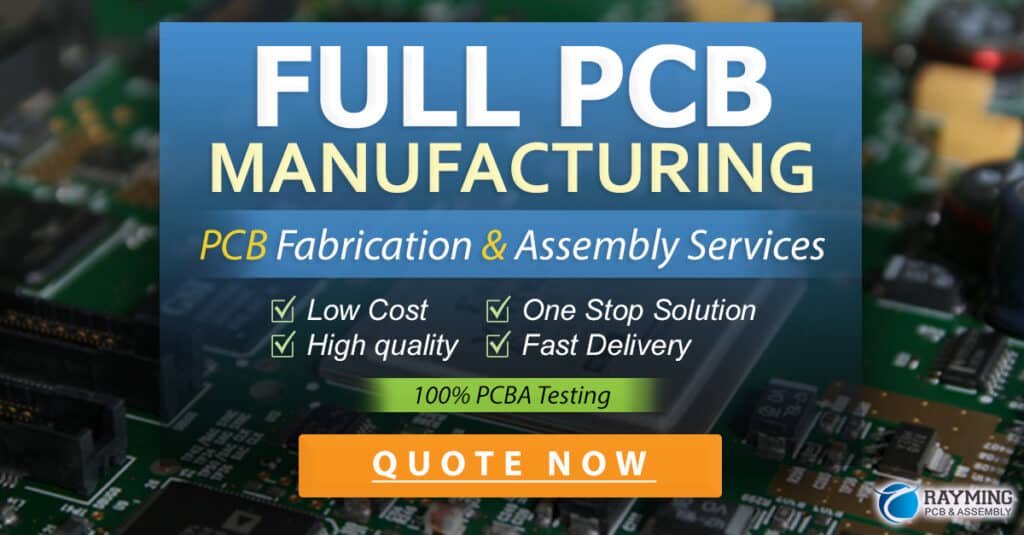
Best Practices for Managing BOMs
To minimize the need for deleting lines from a BOM and to maintain an efficient and accurate BOM management process, consider the following best practices:
-
Establish a Standardized BOM Format: Use a consistent format for your BOMs, including standard naming conventions, part numbering systems, and categorization methods. This consistency helps reduce errors and makes it easier to manage and update BOMs.
-
Regularly Review and Update BOMs: Conduct periodic reviews of your BOMs to identify any obsolete or redundant components, as well as opportunities for consolidation or optimization. Regularly updating your BOMs helps keep them accurate and up-to-date.
-
Use BOM Management Software: Implement a dedicated BOM management software or system to streamline the creation, maintenance, and distribution of BOMs. These tools often provide features such as version control, change tracking, and user access control, which can greatly improve the efficiency and accuracy of your BOM management process.
-
Collaborate with Cross-Functional Teams: Involve relevant stakeholders from various departments, such as engineering, procurement, and production, in the BOM management process. Collaboration ensures that all necessary perspectives are considered and that the BOM accurately reflects the needs of the entire organization.
-
Implement Change Control Processes: Establish a formal change control process for modifying BOMs to ensure that all changes are properly reviewed, approved, and communicated. This process helps maintain the integrity of your BOMs and reduces the risk of errors or unintended consequences.
Frequently Asked Questions (FAQ)
-
Q: What should I do if I accidentally delete the wrong line from a BOM?
A: If you accidentally delete the wrong line, you can usually undo the action using the “Undo” function in your BOM management software. If this is not possible, you may need to manually re-enter the deleted line using the original BOM or a backup copy as a reference. -
Q: Can I delete multiple lines from a BOM at once?
A: Yes, most BOM management software allows you to select and delete multiple lines simultaneously. However, exercise caution when deleting multiple lines to avoid accidentally removing essential components. -
Q: How can I ensure that all stakeholders are aware of the changes made to a BOM?
A: Establish a clear communication plan for distributing updated BOMs to all relevant stakeholders. This may involve sending email notifications, updating shared file repositories, or using a BOM management system with built-in notification features. -
Q: What if I need to delete a component that is used in multiple products?
A: If a component is used in multiple products, carefully assess the impact of deleting it from each product’s BOM. You may need to find a suitable alternative or update the design of the affected products before removing the component. -
Q: How often should I review and update my BOMs?
A: The frequency of BOM reviews depends on factors such as the complexity of your products, the pace of technological advancements, and the frequency of design changes. As a general guideline, review your BOMs at least once a year, or more frequently if your products or industry are subject to rapid changes.
In conclusion, deleting a line from a BOM is a crucial aspect of maintaining accurate and up-to-date product documentation. By following the steps outlined in this article and adhering to best practices for BOM management, you can ensure that your BOMs remain a reliable and efficient tool for guiding your manufacturing processes.
Leave a Reply