What is a Layer Stackup?
A layer stackup, also known as a PCB stackup, is a detailed description of the arrangement of copper and insulating layers within a printed circuit board (PCB). It is a crucial aspect of PCB design, as it determines the board’s electrical properties, signal integrity, and manufacturing process. A well-designed layer stackup ensures that the PCB functions as intended while minimizing electromagnetic interference (EMI) and signal integrity issues.
Key Components of a Layer Stackup
- Copper Layers:
- Signal layers: Used for routing signals between components
- Power and ground planes: Provide stable power supply and reference ground
- Insulating Layers:
- Core: Rigid insulating material, typically FR-4, that provides structural support
- Prepreg: Pre-impregnated fiberglass used to bond copper layers together
- Solder Mask: Protective coating applied to the outer layers to prevent short circuits
- Silkscreen: Text and symbols printed on the PCB for component identification and assembly instructions
Types of Layer Stackups
Single-Layer PCB Stackup
A single-layer PCB consists of a single copper layer on one side of an insulating substrate. This type of stackup is suitable for simple, low-density designs with minimal components and routing requirements. Single-layer PCBs are the most cost-effective option but have limited functionality compared to multi-layer boards.
Layer | Material | Thickness (mm) |
---|---|---|
Top Solder Mask | Epoxy | 0.025 |
Top Copper | Copper | 0.035 |
Core | FR-4 | 1.500 |
Bottom Solder Mask | Epoxy | 0.025 |
Double-Layer PCB Stackup
Double-layer PCBs have two copper layers, one on each side of the insulating substrate. This stackup allows for more complex routing and higher component density compared to single-layer boards. Double-layer PCBs are commonly used in consumer electronics, such as remote controls and simple appliances.
Layer | Material | Thickness (mm) |
---|---|---|
Top Solder Mask | Epoxy | 0.025 |
Top Copper | Copper | 0.035 |
Core | FR-4 | 1.500 |
Bottom Copper | Copper | 0.035 |
Bottom Solder Mask | Epoxy | 0.025 |
Multi-Layer PCB Stackup
Multi-layer PCBs consist of three or more copper layers separated by insulating layers. As the number of layers increases, so does the complexity of the design and the board’s capability to handle high-speed signals and dense routing. Multi-layer PCBs are essential for advanced applications, such as smartphones, computers, and aerospace systems.
A typical 4-layer PCB stackup might look like this:
Layer | Material | Thickness (mm) |
---|---|---|
Top Solder Mask | Epoxy | 0.025 |
Top Copper (Signal) | Copper | 0.035 |
Prepreg | FR-4 | 0.200 |
Inner Copper 1 (Ground) | Copper | 0.035 |
Core | FR-4 | 1.000 |
Inner Copper 2 (Power) | Copper | 0.035 |
Prepreg | FR-4 | 0.200 |
Bottom Copper (Signal) | Copper | 0.035 |
Bottom Solder Mask | Epoxy | 0.025 |
Designing a Layer Stackup
Step 1: Determine the Required Number of Layers
The first step in designing a layer stackup is to determine the number of layers needed based on the complexity of the circuit, routing requirements, and signal integrity considerations. As a general rule, use the minimum number of layers that can accommodate the design to minimize cost and manufacturing complexity.
Step 2: Assign Layer Functions
Once the number of layers is determined, assign specific functions to each layer. Typically, outer layers are used for signal routing, while inner layers are dedicated to power and ground planes. This arrangement helps to minimize EMI and improve signal integrity by providing a stable reference plane for signals.
Step 3: Select Materials
Choose the appropriate materials for the insulating layers based on the desired electrical properties, thermal stability, and cost. FR-4 is the most common choice for the core and prepreg layers due to its excellent mechanical and electrical properties.
Step 4: Specify Layer Thicknesses
Determine the thickness of each layer based on the desired board thickness, signal integrity requirements, and manufacturing capabilities. Thicker copper layers can carry more current but may increase the overall board thickness and cost.
Step 5: Define Copper Weights and Trace Widths
Specify the copper weights and trace widths for each layer based on the current carrying requirements and signal integrity considerations. Higher copper weights and wider traces can accommodate higher currents and improve signal integrity but may increase manufacturing costs.
Step 6: Specify Drill Pairs and Via Spans
Define the drill pairs and via spans for each layer to ensure proper connectivity between layers. Drill pairs specify the layers that are connected by a via, while via spans determine the distance between the connected layers.
Step 7: Review and Optimize
Review the layer stackup design for manufacturability, signal integrity, and cost-effectiveness. Optimize the design by adjusting layer thicknesses, copper weights, and trace widths as needed to achieve the desired performance and cost targets.
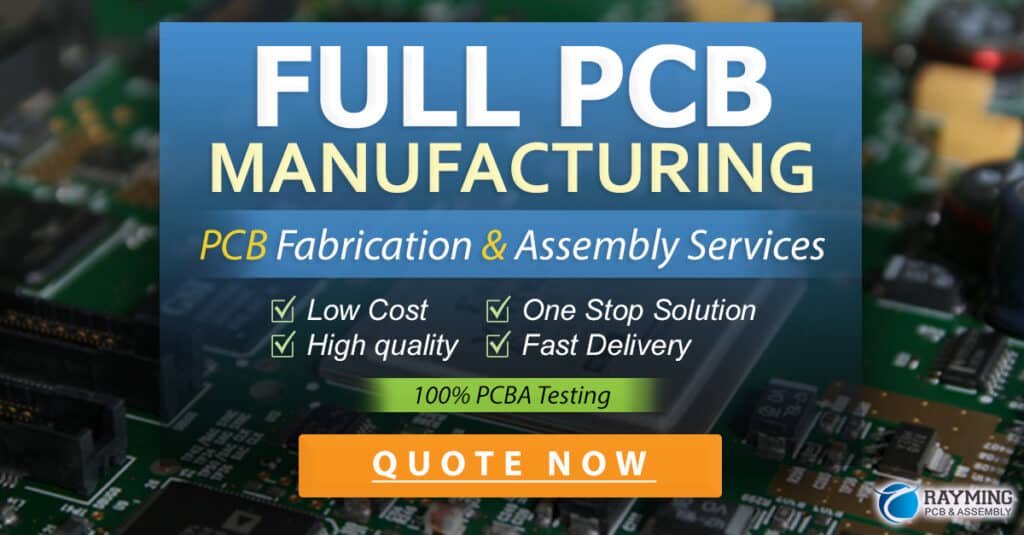
Best Practices for Layer Stackup Design
- Use dedicated power and ground planes to reduce EMI and improve signal integrity
- Minimize the number of layers to reduce cost and manufacturing complexity
- Keep signal traces as short as possible to reduce signal delay and attenuation
- Use appropriate trace widths and copper weights for the required current carrying capacity
- Avoid splitting ground planes to maintain a low-impedance return path for signals
- Use symmetrical stackups to minimize warpage and improve manufacturability
- Follow the manufacturer’s design guidelines and constraints for the chosen materials and processes
Frequently Asked Questions (FAQ)
1. What is the difference between a core and prepreg in a PCB stackup?
A core is a rigid, pre-cured insulating material that provides structural support to the PCB. Prepreg, short for pre-impregnated, is a partially cured insulating material used to bond copper layers together during the lamination process. Cores are thicker and more rigid than prepregs, which are typically used to separate inner copper layers in multi-layer PCBs.
2. How does the number of layers affect the cost and manufacturability of a PCB?
As the number of layers in a PCB increases, so does the cost and manufacturing complexity. Each additional layer requires more materials, processing steps, and time to manufacture, leading to higher costs. Furthermore, multi-layer PCBs are more susceptible to manufacturing defects, such as delamination and registration issues, which can impact yield and reliability. Therefore, it is essential to use the minimum number of layers required for the design to optimize cost and manufacturability.
3. What is the purpose of copper weight in a PCB stackup?
Copper weight refers to the thickness of the copper layer in a PCB, typically expressed in ounces per square foot (oz/ft²). A higher copper weight indicates a thicker copper layer, which can carry more current and improve signal integrity. However, thicker copper layers also increase the overall board thickness and manufacturing costs. The choice of copper weight depends on the specific requirements of the design, such as current carrying capacity, signal integrity, and cost constraints.
4. How does the choice of insulating material affect the performance of a PCB?
The choice of insulating material, such as FR-4, Rogers, or polyimide, can significantly impact the electrical, thermal, and mechanical properties of a PCB. Different materials have varying dielectric constants, loss tangents, thermal conductivities, and mechanical strengths, which can affect signal propagation, power dissipation, and reliability. For example, FR-4 is a common choice for general-purpose applications due to its good balance of properties and low cost, while Rogers materials are preferred for high-frequency applications due to their low dielectric loss and stable performance over temperature.
5. What are the benefits of using a symmetrical stackup in a PCB design?
A symmetrical stackup is a layer arrangement in which the copper and insulating layers are mirrored about the center of the board. This configuration offers several benefits, including:
- Reduced warpage: Symmetrical stackups minimize the difference in thermal expansion between layers, reducing the risk of warpage during manufacturing and operation.
- Improved signal integrity: Symmetrical arrangements provide a more consistent dielectric environment for signals, reducing the impact of impedance variations and signal reflections.
- Enhanced manufacturability: Symmetrical stackups are easier to fabricate and assemble, as they minimize the risk of registration errors and improve the overall stability of the board.
By using a symmetrical stackup, designers can improve the reliability, performance, and manufacturability of their PCB designs.
Conclusion
A well-designed layer stackup is essential for ensuring the proper functioning, reliability, and manufacturability of a PCB. By understanding the key components, types, and best practices for layer stackup design, engineers can create PCBs that meet the specific requirements of their applications while optimizing cost and performance. When designing a layer stackup, it is crucial to consider factors such as the number of layers, layer functions, materials, thicknesses, copper weights, and trace widths to achieve the desired electrical, thermal, and mechanical properties. By following best practices and collaborating closely with manufacturers, designers can create robust and cost-effective PCBs that drive innovation across a wide range of industries.
Leave a Reply