Understanding ddr5 and Its Benefits
DDR5 offers several advantages over DDR4, including:
- Higher data rates: DDR5 supports data rates up to 6400 MT/s, compared to DDR4’s maximum of 3200 MT/s.
- Increased capacity: DDR5 modules can have up to 64 GB per DIMM, doubling the maximum capacity of DDR4.
- Improved power efficiency: DDR5 operates at a lower voltage (1.1V) than DDR4 (1.2V), reducing power consumption.
- On-die ECC: DDR5 introduces on-die Error Correction Code (ECC) for enhanced reliability.
DDR5 PCB Design Considerations
Signal Integrity Challenges
With higher data rates and tighter timing constraints, signal integrity becomes a critical concern in DDR5 PCB designs. Some of the key challenges include:
- Increased crosstalk: Higher signal speeds and closer trace spacing can lead to increased crosstalk between adjacent signals.
- Reflections: Impedance mismatches and discontinuities in the signal path can cause reflections, degrading signal quality.
- Jitter: Higher frequencies and reduced timing margins make jitter management more challenging.
PCB Stack-up and Material Selection
Choosing the right PCB stack-up and materials is crucial for maintaining signal integrity in DDR5 designs. Consider the following:
- Use low-loss dielectric materials to minimize signal attenuation and maintain signal quality.
- Employ a symmetrical stack-up to ensure balanced impedance and reduce crosstalk.
- Incorporate ground planes between signal layers to provide shielding and reduce electromagnetic interference (EMI).
Trace Routing and Matching
Proper trace routing and matching are essential for optimal DDR5 performance. Keep these guidelines in mind:
- Route DDR5 signals as matched-length differential pairs to maintain signal integrity and minimize skew.
- Adhere to the recommended trace widths and spacings provided by the DDR5 specification and PCB manufacturer.
- Avoid sharp bends and corners in trace routing to minimize reflections and impedance discontinuities.
Decoupling and Power Distribution
Robust power distribution and decoupling are critical for stable DDR5 operation. Follow these best practices:
- Place decoupling capacitors close to the DDR5 memory devices to minimize power supply noise and ensure a clean power delivery.
- Use a combination of bulk and ceramic capacitors to cover different frequency ranges and provide adequate decoupling.
- Implement a low-impedance power distribution network (PDN) to minimize voltage ripple and maintain signal integrity.
DDR5 Simulation and Validation
To ensure the success of a DDR5 PCB design, it is essential to perform thorough simulations and validations. This includes:
- Signal integrity simulations: Use specialized tools to analyze the signal quality, crosstalk, and reflections in the DDR5 interface.
- Power integrity simulations: Simulate the PDN to ensure stable power delivery and identify potential resonance issues.
- Timing analysis: Verify that the DDR5 interface meets the required timing constraints, including setup and hold times.
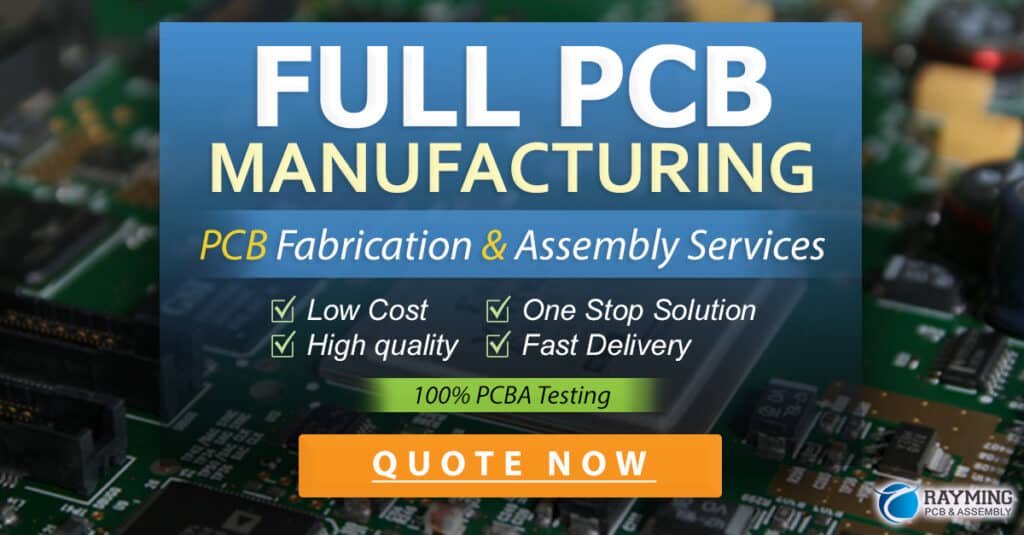
Frequently Asked Questions
Q1: Can I use the same PCB design rules for DDR5 as I did for DDR4?
A1: No, DDR5 has different design requirements due to its higher data rates and tighter timing constraints. You should follow the specific guidelines provided by the DDR5 specification and your PCB manufacturer.
Q2: Is it necessary to use a 4-layer PCB for DDR5 designs?
A2: While a 4-layer PCB can work for some DDR5 designs, it is recommended to use a 6-layer or 8-layer PCB to provide better signal integrity and power distribution. The additional layers allow for more effective shielding and reference planes.
Q3: How important is it to perform signal integrity simulations for DDR5?
A3: Signal integrity simulations are crucial for DDR5 designs due to the high data rates and tight timing margins. These simulations help identify potential issues early in the design process, allowing for necessary adjustments to be made before fabrication.
Q4: Can I use the same decoupling capacitors for DDR5 as I did for DDR4?
A4: While you can use similar types of decoupling capacitors, the values and placement may need to be adjusted for DDR5. It’s essential to follow the DDR5 specification and manufacturer recommendations to ensure proper decoupling and power distribution.
Q5: What are some common pitfalls to avoid in DDR5 PCB design?
A5: Some common pitfalls include:
1. Not following the DDR5 specification and manufacturer guidelines.
2. Inadequate signal integrity and power integrity simulations.
3. Improper trace routing and matching.
4. Insufficient decoupling and power distribution.
5. Neglecting the importance of a well-designed PCB stack-up.
Conclusion
Designing a PCB for DDR5 memory requires careful consideration of signal integrity, power distribution, and layout techniques. By understanding the challenges and best practices associated with DDR5 PCB design, designers can create robust and high-performance systems that take full advantage of the benefits offered by this next-generation memory technology.
Remember to follow the DDR5 specification, choose appropriate PCB materials and stack-up, perform thorough simulations, and adhere to best practices for trace routing, matching, and decoupling. By doing so, you can ensure optimal signal integrity and reliability in your DDR5 designs.
DDR Generation | Data Rate (MT/s) | Voltage (V) | Max. Capacity per DIMM (GB) |
---|---|---|---|
DDR4 | Up to 3200 | 1.2 | 32 |
DDR5 | Up to 6400 | 1.1 | 64 |
Table 1: Comparison of DDR4 and DDR5 key specifications
As DDR5 continues to gain adoption in the industry, staying up-to-date with the latest design techniques and best practices will be essential for PCB designers. By embracing the challenges and opportunities presented by DDR5, designers can create innovative and high-performance systems that push the boundaries of memory technology.
Leave a Reply