Understanding the Basics of PDN Design
Before we dive into the specifics of DC analysis, it is essential to grasp the fundamental concepts of PDN design. A PDN comprises a network of power and ground planes, decoupling capacitors, and interconnects that distribute power from the source to the various components within a digital system. The primary goal of a PDN is to maintain a stable voltage level across all the components while minimizing noise and ensuring an adequate supply of current.
Key Components of a PDN
- Power and Ground Planes: These are the conductive layers within a PCB that distribute power and provide a low-impedance return path for the current.
- Decoupling Capacitors: These capacitors are strategically placed near the power pins of digital components to provide local energy storage and reduce high-frequency noise.
- Interconnects: These include vias, traces, and connectors that facilitate the flow of current between the power source and the components.
Challenges in PDN Design
Designing an effective PDN comes with its own set of challenges. Some of the primary concerns include:
- Voltage Drop: As current flows through the PDN, the inherent resistance of the conductors leads to a voltage drop across the network. This voltage drop must be minimized to ensure that each component receives the required voltage level.
- Current Density: The PDN must be capable of handling the expected current demands of the digital system without experiencing excessive current density, which can lead to electromigration and reliability issues.
- Noise: High-frequency noise, such as simultaneous switching noise (SSN), can propagate through the PDN and cause signal integrity issues. Proper decoupling and layout techniques are crucial for mitigating noise.
The Importance of DC Analysis
DC analysis is a critical step in the PDN design process, as it allows designers to assess the network’s performance under steady-state conditions. By conducting a thorough DC analysis, designers can identify potential issues early in the design cycle and make necessary modifications to ensure the PDN meets the required specifications.
Objectives of DC Analysis
The primary objectives of DC analysis include:
- Verifying Voltage Levels: DC analysis helps designers determine whether the PDN can maintain the required voltage levels at all the component power pins, taking into account the voltage drop across the network.
- Assessing Current Handling Capability: By analyzing the current density distribution across the PDN, designers can identify potential hotspots and ensure that the network can handle the expected current demands without exceeding the maximum allowable current density.
- Optimizing PDN Design: DC analysis results can guide designers in making informed decisions about PDN layout, layer stackup, and component placement to achieve optimal performance.
Tools for DC Analysis
There are various tools available for conducting DC analysis of PDNs. Some of the most commonly used tools include:
- SPICE Simulators: SPICE (Simulation Program with Integrated Circuit Emphasis) simulators, such as LTspice and PSpice, can be used to perform DC analysis of PDNs. These simulators allow designers to model the PDN as a network of resistors and voltage sources and analyze the voltage and current distribution.
- Finite Element Analysis (FEA) Tools: FEA tools, such as Ansys SIwave and Cadence Sigrity, provide a more comprehensive approach to DC analysis. These tools can model the 3D geometry of the PDN and simulate the current flow and voltage distribution across the network.
- PCB Design Software: Many modern PCB design software packages, such as Altium Designer and Cadence Allegro, include built-in tools for conducting DC analysis of PDNs. These tools often provide a streamlined workflow for setting up and running the analysis.
Conducting DC Analysis: A Step-by-Step Approach
To perform a comprehensive DC analysis of a PDN, designers can follow these key steps:
Step 1: Define the PDN Requirements
The first step in conducting DC analysis is to clearly define the PDN requirements. This includes specifying the voltage levels, current demands, and allowable voltage drop for each power domain in the digital system. These requirements serve as the foundation for the subsequent analysis steps.
Step 2: Create a PDN Model
Once the requirements are defined, designers need to create a model of the PDN. This model should include the power and ground planes, decoupling capacitors, and interconnects. The model can be created using a SPICE simulator, FEA tool, or PCB design software, depending on the level of detail and accuracy required.
Step 3: Apply Boundary Conditions and Loads
With the PDN model in place, designers must apply the appropriate boundary conditions and loads. This involves specifying the voltage sources, current loads, and any external resistances or inductances that may impact the PDN’s performance. It is crucial to ensure that the boundary conditions and loads accurately represent the real-world operating conditions of the digital system.
Step 4: Run the DC Analysis
After setting up the model and applying the necessary conditions, designers can run the DC analysis. The analysis will simulate the steady-state behavior of the PDN and provide results such as voltage distribution, current density, and power dissipation. Designers should pay close attention to any areas of the PDN that exhibit excessive voltage drop or current density, as these may indicate potential issues.
Step 5: Interpret the Results and Optimize the Design
The final step in the DC analysis process is to interpret the results and make necessary optimizations to the PDN design. Designers should compare the analysis results against the predefined requirements and identify any areas that need improvement. This may involve adjusting the layer stackup, modifying the placement of decoupling capacitors, or increasing the width of power and ground traces.
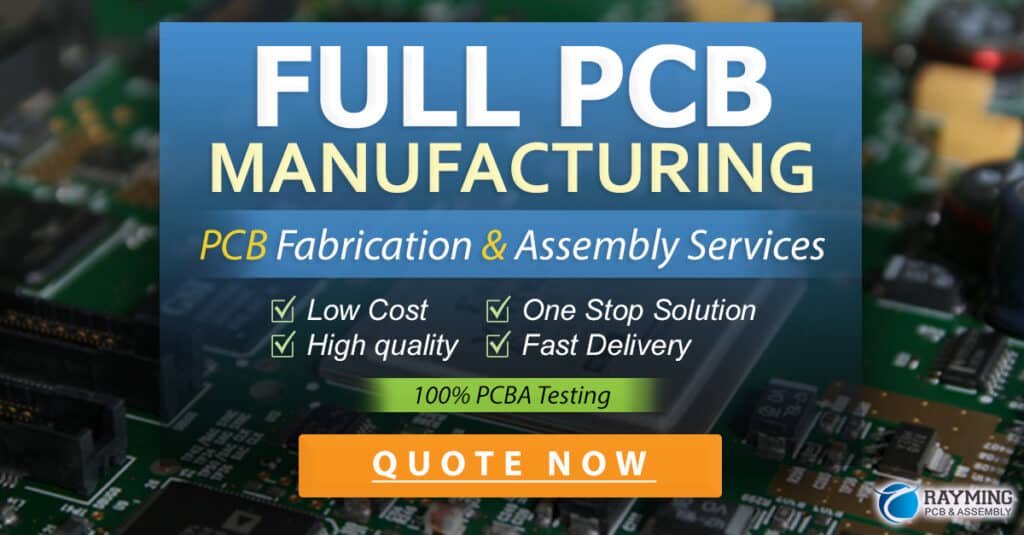
Best Practices for DC Analysis
To ensure accurate and meaningful results from DC analysis, designers should follow these best practices:
- Use Accurate Material Properties: When creating the PDN model, it is essential to use accurate material properties, such as the conductivity and thickness of the copper layers. Inaccurate material properties can lead to misleading analysis results.
- Consider Temperature Effects: The electrical properties of materials can vary with temperature, which can impact the PDN’s performance. Designers should consider the expected operating temperature range of the digital system and incorporate temperature effects into the analysis.
- Validate the Model: Before relying on the DC analysis results, designers should validate the PDN model against real-world measurements. This can be done by comparing the simulated results with actual voltage and current measurements taken from a prototype or test board.
- Collaborate with PCB Fabricators: Designers should collaborate closely with PCB fabricators to ensure that the manufactured board meets the intended PDN design specifications. This includes discussing layer stackup, material selection, and manufacturing tolerances.
Case Study: DC Analysis of a High-Speed Digital Board
To illustrate the importance of DC analysis in real-world scenarios, let’s consider a case study of a high-speed digital board designed for a telecommunications application.
Board Specifications
- Voltage Levels: 1.2 V, 1.8 V, and 3.3 V power domains
- Current Demands: 10 A for the 1.2 V domain, 5 A for the 1.8 V domain, and 2 A for the 3.3 V domain
- Maximum Allowable Voltage Drop: 5% for each power domain
PDN Design and Analysis
The PDN was designed using a 6-layer PCB stackup, with dedicated power and ground planes for each voltage domain. Decoupling capacitors were strategically placed near the power pins of the digital components to minimize high-frequency noise.
A DC analysis was conducted using a SPICE simulator to assess the voltage distribution and current density across the PDN. The analysis results revealed that the 1.2 V power domain experienced a voltage drop of 8% near the center of the board, exceeding the maximum allowable limit.
Design Optimization
Based on the DC analysis results, the PDN design was optimized by making the following changes:
- The width of the power and ground traces for the 1.2 V domain was increased to reduce the voltage drop.
- Additional decoupling capacitors were placed near the high-current components to improve local power delivery.
- The layer stackup was modified to reduce the distance between the power and ground planes, minimizing the loop inductance.
After implementing these optimizations, a subsequent DC analysis confirmed that the voltage drop for the 1.2 V domain was reduced to 4%, meeting the specified requirement.
Frequently Asked Questions (FAQ)
-
Q: What is the difference between DC analysis and AC analysis of a PDN?
A: DC analysis focuses on the steady-state behavior of the PDN, assessing voltage levels and current handling capability under constant load conditions. AC analysis, on the other hand, examines the frequency-dependent behavior of the PDN, including impedance characteristics and power integrity issues related to high-frequency noise. -
Q: How often should DC analysis be performed during the PDN design process?
A: DC analysis should be conducted at multiple stages of the design process, starting from the initial concept phase and continuing through the detailed design and verification stages. It is essential to perform DC analysis whenever significant changes are made to the PDN design or when the power requirements of the digital system are updated. -
Q: Can DC analysis be used to assess the thermal performance of a PDN?
A: While DC analysis primarily focuses on electrical characteristics, it can provide insights into the power dissipation and current density distribution across the PDN. This information can be used as input for thermal simulations to assess the thermal performance of the digital system. However, a dedicated thermal analysis is necessary to comprehensively evaluate the thermal behavior of the PDN and the overall system. -
Q: What are the consequences of not conducting a thorough DC analysis of a PDN?
A: Failing to conduct a thorough DC analysis can lead to several issues, such as: - Inadequate voltage levels at the component power pins, resulting in functional failures or performance degradation.
- Excessive current density in the PDN, leading to electromigration and reliability concerns.
- Increased power dissipation and thermal issues, which can impact the overall system performance and reliability.
-
Costly design iterations and board respins due to unidentified PDN issues.
-
Q: How can designers ensure the accuracy of DC analysis results?
A: To ensure the accuracy of DC analysis results, designers should: - Use accurate material properties and dimensions when creating the PDN model.
- Apply realistic boundary conditions and loads that represent the actual operating conditions of the digital system.
- Validate the PDN model against real-world measurements from prototypes or test boards.
- Collaborate with PCB fabricators to ensure that the manufactured board meets the intended PDN design specifications.
Conclusion
DC analysis is a vital aspect of PDN design, enabling digital designers to assess the steady-state performance of the power distribution network. By conducting thorough DC analysis, designers can verify voltage levels, evaluate current handling capability, and optimize the PDN design to ensure reliable operation and optimal performance of the digital system.
As digital systems continue to push the boundaries of speed and complexity, the importance of DC analysis in PDN design will only continue to grow. By following best practices, utilizing appropriate tools, and staying updated with the latest techniques, digital designers can effectively tackle the challenges associated with PDN design and deliver robust, high-performance systems.
Tables
Table 1: Comparison of DC Analysis Tools
Tool Category | Examples | Advantages | Disadvantages |
---|---|---|---|
SPICE Simulators | LTspice, PSpice | – Easy to set up and use – Fast simulation times – Suitable for simple PDN models |
– Limited accuracy for complex 3D geometries – May not capture all physical effects |
FEA Tools | Ansys SIwave, Cadence Sigrity | – High accuracy for complex 3D geometries – Comprehensive analysis capabilities – Supports multi-physics simulations |
– Steep learning curve – Longer simulation times – Higher cost compared to SPICE simulators |
PCB Design Software | Altium Designer, Cadence Allegro | – Integrated with PCB design workflow – Enables early-stage PDN analysis – Facilitates design optimization |
– May have limitations in modeling complex 3D structures – Accuracy depends on the underlying simulation engine |
Table 2: Example DC Analysis Results for a PDN
Power Domain | Nominal Voltage (V) | Minimum Voltage (V) | Maximum Voltage (V) | Maximum Current Density (A/mm²) |
---|---|---|---|---|
1.2 V | 1.2 | 1.14 | 1.26 | 5.8 |
1.8 V | 1.8 | 1.75 | 1.85 | 3.2 |
3.3 V | 3.3 | 3.22 | 3.38 | 1.9 |
In this example, the DC analysis results show the minimum and maximum voltage levels for each power domain, as well as the maximum current density observed in the PDN. Designers can use this information to assess whether the PDN meets the specified voltage and current requirements and make necessary optimizations if needed.
By incorporating tables and real-world examples, digital designers can better understand the importance of DC analysis in PDN design and apply the concepts discussed in this article to their own projects. Through rigorous DC analysis and adherence to best practices, designers can create robust, high-performance digital systems that meet the ever-increasing demands of modern applications.
Leave a Reply