Introduction to D356 IPC Testpoints
D356 IPC testpoints are an essential component in the manufacturing and assembly of printed circuit boards (PCBs). These testpoints provide a convenient and reliable way to test and troubleshoot PCBs during the production process, ensuring the quality and functionality of the final product.
What are D356 IPC Testpoints?
D356 IPC testpoints are standardized testpoints defined by the IPC (Association Connecting Electronics Industries) in their IPC-D-356 standard. This standard specifies the design, placement, and nomenclature of testpoints on PCBs to ensure consistency and compatibility across different manufacturers and assembly processes.
Testpoints are small, exposed pads on a PCB that allow test probes to make contact with specific points in the circuit. They are used to measure voltages, currents, and other electrical parameters during testing and debugging. D356 IPC testpoints have specific dimensions, spacing, and labeling requirements to ensure proper functionality and ease of use.
Benefits of Using D356 IPC Testpoints
Using standardized D356 IPC testpoints offers several benefits in PCB manufacturing and assembly:
-
Consistency: By following the IPC-D-356 standard, manufacturers ensure that testpoints are placed and labeled consistently across different PCB designs. This consistency makes it easier for operators to locate and use the testpoints during testing and troubleshooting.
-
Compatibility: D356 IPC testpoints are compatible with standard test equipment and probes, allowing for seamless integration into existing test processes and setups.
-
Efficiency: With clearly defined and labeled testpoints, operators can quickly identify and access the points they need to test, reducing the time and effort required for testing and debugging.
-
Quality Assurance: By facilitating thorough testing and troubleshooting, D356 IPC testpoints help ensure the quality and reliability of the final PCB product.
Incorporating D356 IPC Testpoints into PCB Design
To effectively use D356 IPC testpoints, it is crucial to incorporate them into the PCB design from the early stages. This section will discuss the key considerations and best practices for integrating testpoints into your PCB layout.
Testpoint Placement
Proper placement of testpoints is essential for ensuring accessibility and ease of use during testing. When placing D356 IPC testpoints on your PCB, consider the following guidelines:
-
Accessibility: Place testpoints in easily accessible locations on the PCB, avoiding areas that may be obstructed by components or connectors. Testpoints should be reachable by test probes without the need for special tools or equipment.
-
Clearance: Ensure sufficient clearance around each testpoint to accommodate test probes and prevent accidental contact with nearby components or traces. The IPC-D-356 standard specifies minimum clearance requirements for testpoints.
-
Signal Integrity: Place testpoints close to the signals or components they are intended to test, minimizing the distance between the testpoint and the target location. This helps maintain signal integrity and reduces the impact of probe loading on the circuit.
-
Logical Grouping: Group related testpoints together in a logical manner, such as by functional block or signal type. This makes it easier for operators to locate and test related points during the debugging process.
Testpoint Labeling
Clear and consistent labeling of testpoints is crucial for efficient testing and troubleshooting. Follow these best practices when labeling your D356 IPC testpoints:
-
Unique Identifiers: Assign unique identifiers to each testpoint, such as TP1, TP2, etc. These identifiers should be clearly visible on the PCB silkscreen and in the accompanying documentation.
-
Descriptive Labels: In addition to the unique identifier, consider adding descriptive labels to testpoints, indicating their purpose or the signal they are connected to. This can be helpful for operators unfamiliar with the specific PCB design.
-
Consistent Nomenclature: Use a consistent naming convention for testpoints across all your PCB designs. This consistency makes it easier for operators to understand and navigate the testpoints, even when working with different PCB versions or variants.
-
Legibility: Ensure that testpoint labels are legible and easily readable on the PCB silkscreen. Use a font size and style that is clear and distinct, even in low-light conditions or when viewed through magnification.
Testpoint Documentation
Proper documentation is essential for effective use of D356 IPC testpoints. Include the following information in your PCB documentation:
-
Testpoint List: Provide a comprehensive list of all testpoints on the PCB, including their unique identifiers, descriptive labels, and locations. This list serves as a reference for operators during testing and troubleshooting.
-
Schematic Diagrams: Include testpoints in your schematic diagrams, clearly indicating their connections to the circuit. This helps operators understand the purpose and function of each testpoint.
-
Assembly Drawings: Show the locations and labels of testpoints in your PCB assembly drawings. This visual representation aids operators in locating and accessing the testpoints during the assembly process.
-
Test Procedures: Develop detailed test procedures that include steps for using the testpoints to verify the functionality of the PCB. These procedures should guide operators through the testing process, specifying which testpoints to use and what measurements to take.
By incorporating testpoints into your PCB design and providing comprehensive documentation, you can streamline the testing and debugging process, ultimately improving the quality and reliability of your PCB products.
Making Room for the Bill of Material
When designing a PCB with D356 IPC testpoints, it is important to consider the impact on the bill of material (BOM). Testpoints require additional space on the PCB and may affect component placement and routing. This section will discuss strategies for making room for the BOM while incorporating testpoints.
Optimizing PCB Layout
To accommodate testpoints without compromising the BOM, consider the following PCB layout optimization techniques:
-
Component Placement: Carefully plan the placement of components on the PCB, taking into account the space required for testpoints. Arrange components in a way that minimizes the impact of testpoints on the overall layout.
-
Routing Strategies: Use efficient routing strategies to maximize the available space on the PCB. Consider using smaller trace widths and spacing where appropriate, and route signals in a way that avoids congestion around testpoints.
-
Layer Stackup: Optimize your PCB layer stackup to make the most of the available space. Consider using additional layers to route signals and power, freeing up space on the outer layers for testpoints and components.
-
Design Rule Checks (DRC): Perform thorough DRC checks to ensure that your PCB layout meets the required clearance and spacing rules for testpoints and components. Identify and resolve any conflicts or violations early in the design process.
Component Selection
The selection of components can also impact the space available for testpoints on your PCB. Consider the following factors when choosing components:
-
Package Size: Opt for smaller component packages wherever possible. Smaller components take up less space on the PCB, leaving more room for testpoints and other necessary features.
-
Functionality: Evaluate the functionality of each component and consider whether it is essential for the design. Eliminating unnecessary components can free up valuable space on the PCB.
-
Integration: Look for opportunities to integrate multiple functions into a single component, such as using a microcontroller with built-in peripherals instead of separate ICs. Integration helps reduce the overall component count and saves space on the PCB.
Testpoint Optimization
In addition to optimizing the PCB layout and component selection, there are strategies specific to testpoints that can help make room for the BOM:
-
Shared Testpoints: Where possible, consider using shared testpoints for multiple signals or components. By carefully planning the placement of testpoints, you can reduce the total number required, saving space on the PCB.
-
Testpoint Size: Use the smallest testpoint size that is practical for your design. Smaller testpoints take up less space, allowing for more efficient use of the available PCB area.
-
Alternate Placement: In some cases, it may be possible to place testpoints on the bottom side of the PCB or in areas that are not typically used for components. Explore alternative placement options to maximize the available space.
-
Testpoint Prioritization: Prioritize the placement of testpoints based on their criticality for testing and debugging. Place the most essential testpoints first, and consider omitting or relocating less critical ones if space is limited.
By carefully optimizing your PCB layout, component selection, and testpoint placement, you can effectively make room for the BOM while incorporating D356 IPC testpoints into your design.
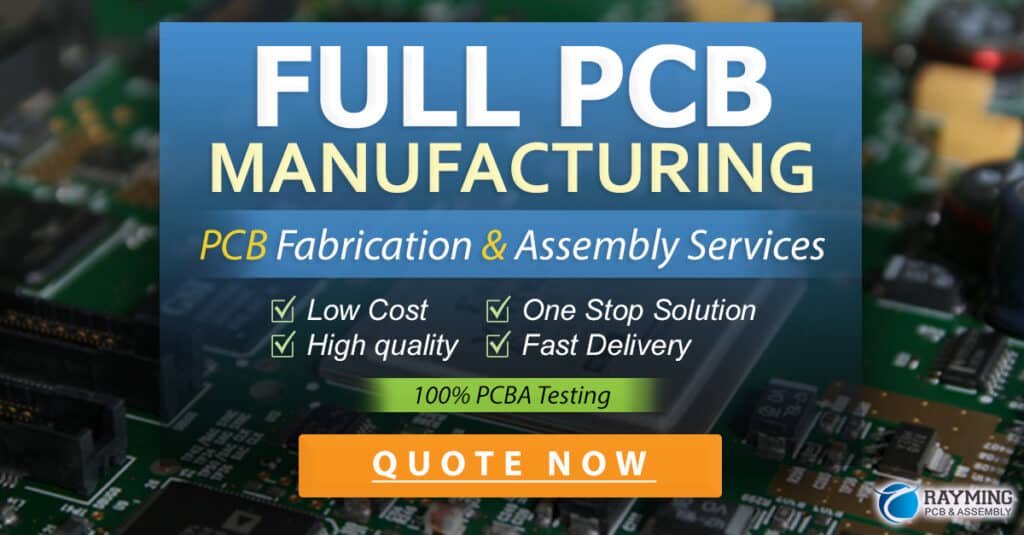
Best Practices for Using D356 IPC Testpoints
To ensure the effective use of D356 IPC testpoints in your PCB manufacturing and assembly process, follow these best practices:
-
Operator Training: Provide comprehensive training to your assembly and test operators on the proper use of testpoints. Ensure that they understand the purpose of each testpoint, how to locate them on the PCB, and the correct techniques for probing and measuring.
-
Test Equipment Calibration: Regularly calibrate your test equipment, including probes and measurement devices, to ensure accurate and reliable readings. Follow the manufacturer’s guidelines for calibration intervals and procedures.
-
Electrostatic Discharge (ESD) Protection: Implement appropriate ESD protection measures when handling and testing PCBs with testpoints. Use grounded wrist straps, ESD-safe workstations, and proper handling techniques to minimize the risk of ESD damage.
-
Probe Technique: Use the correct probing technique when accessing testpoints. Ensure that probes make proper contact with the testpoint pads without applying excessive pressure or damaging the PCB surface. Use probes with appropriate tip sizes and shapes for the specific testpoint design.
-
Documentation Updates: Keep your testpoint documentation up to date, reflecting any changes or revisions to the PCB design. Ensure that all relevant personnel have access to the latest documentation, including assembly drawings, schematics, and test procedures.
-
Continuous Improvement: Regularly review and assess your testpoint usage and effectiveness. Gather feedback from operators and analyze test results to identify areas for improvement. Continuously refine your testpoint design and placement to optimize the testing process and enhance the overall quality of your PCB products.
Testpoint Best Practices | Description |
---|---|
Operator Training | Provide comprehensive training on proper testpoint usage |
Test Equipment Calibration | Regularly calibrate test equipment for accurate measurements |
ESD Protection | Implement ESD protection measures when handling PCBs |
Probe Technique | Use correct probing technique to avoid damaging PCBs |
Documentation Updates | Keep testpoint documentation up to date |
Continuous Improvement | Regularly review and refine testpoint design and usage |
By adhering to these best practices, you can ensure the effective and efficient use of D356 IPC testpoints in your PCB manufacturing and assembly process, ultimately improving the quality and reliability of your products.
Frequently Asked Questions (FAQ)
-
What is the purpose of D356 IPC testpoints?
D356 IPC testpoints provide a standardized way to test and troubleshoot PCBs during the manufacturing and assembly process. They allow operators to measure voltages, currents, and other electrical parameters at specific points in the circuit, ensuring the functionality and quality of the PCB. -
How do D356 IPC testpoints differ from other testpoint standards?
D356 IPC testpoints are defined by the IPC-D-356 standard, which specifies the design, placement, and nomenclature of testpoints on PCBs. This standard ensures consistency and compatibility across different manufacturers and assembly processes. Other testpoint standards may have different requirements or specifications. -
What are the key considerations when placing D356 IPC testpoints on a PCB?
When placing D356 IPC testpoints, consider factors such as accessibility, clearance, signal integrity, and logical grouping. Testpoints should be easily reachable by test probes, have sufficient clearance from nearby components, be placed close to the signals they are testing, and be grouped logically for ease of use. -
How can I optimize my PCB layout to accommodate D356 IPC testpoints?
To optimize your PCB layout for testpoints, consider techniques such as careful component placement, efficient routing strategies, optimized layer stackup, and thorough design rule checks (DRC). These techniques help maximize the available space on the PCB while ensuring proper clearance and functionality of testpoints. -
What documentation is necessary for effective use of D356 IPC testpoints?
Comprehensive documentation is crucial for the effective use of D356 IPC testpoints. This includes a testpoint list with unique identifiers and descriptions, schematic diagrams showing testpoint connections, assembly drawings indicating testpoint locations, and detailed test procedures guiding operators through the testing process.
Conclusion
D356 IPC testpoints play a vital role in ensuring the quality and reliability of PCBs during the manufacturing and assembly process. By providing a standardized way to test and troubleshoot circuits, these testpoints help streamline the production process and improve the overall functionality of the final product.
To effectively incorporate D356 IPC testpoints into your PCB design, it is essential to consider factors such as testpoint placement, labeling, and documentation. By optimizing your PCB layout, component selection, and testpoint placement, you can make room for the bill of material while ensuring the accessibility and usefulness of the testpoints.
Furthermore, by following best practices such as operator training, test equipment calibration, ESD protection, proper probe technique, documentation updates, and continuous improvement, you can maximize the benefits of D356 IPC testpoints and enhance the efficiency and effectiveness of your PCB testing process.
As the electronics industry continues to evolve and demands for high-quality, reliable PCBs increase, the use of standardized testpoints like D356 IPC becomes increasingly important. By embracing these testpoints and incorporating them into your PCB design and manufacturing process, you can stay ahead of the curve and deliver products that meet the highest standards of performance and reliability.
Leave a Reply