Introduction to Current Monitoring
Current monitoring is a crucial aspect of electrical and electronic systems, as it allows for the accurate measurement and control of the flow of electric current. In various applications, such as power management, battery charging, motor control, and overcurrent protection, monitoring the current is essential to ensure the proper functioning and safety of the system.
This article will explore the concepts behind current monitoring, discuss various methods and technologies used for current sensing, and delve into the design and implementation of a current monitor and controller project.
Importance of Current Monitoring
Current monitoring plays a vital role in numerous applications, including:
-
Power Management: By monitoring the current consumption of different components in a system, power management techniques can be employed to optimize energy efficiency and prevent overloading.
-
Battery Charging: Current monitoring is essential in battery charging systems to ensure safe and efficient charging, preventing overcharging or undercharging, which can damage the battery or reduce its lifespan.
-
Motor Control: In motor control applications, current monitoring helps detect abnormal conditions, such as stalls or overloads, allowing for protective measures to be taken to prevent damage to the motor or the system.
-
Overcurrent Protection: Current monitoring enables the implementation of overcurrent protection mechanisms, such as fuses or circuit breakers, to safeguard the system and its components from excessive current that can cause damage or pose safety risks.
Current Sensing Techniques
To monitor current, various current sensing techniques can be employed. Each technique has its own advantages and limitations, and the choice of the appropriate method depends on factors such as accuracy, range, isolation, and cost. Some common current sensing techniques include:
Shunt Resistor
A shunt resistor is a low-value, high-precision resistor placed in series with the load. The current flowing through the shunt resistor creates a voltage drop proportional to the current, which can be measured using a voltage-sensing circuit. The voltage across the shunt resistor is given by Ohm’s law:
V = I × R
Where V is the voltage drop, I is the current, and R is the resistance of the shunt resistor.
Advantages:
– Simple and cost-effective
– Suitable for DC and low-frequency AC current measurement
– High accuracy and linearity
Limitations:
– Introduces a small voltage drop in the circuit
– Limited isolation between the sensing circuit and the load
– May require amplification for low current measurements
Current Transformer (CT)
A current transformer is a device that uses the principle of electromagnetic induction to measure alternating current (AC). It consists of a primary winding (the conductor carrying the current to be measured) and a secondary winding wound around a magnetic core. The primary current induces a proportional current in the secondary winding, which can be measured using a burden resistor.
Advantages:
– Provides galvanic isolation between the primary and secondary circuits
– Suitable for measuring high AC currents
– Wide measurement range
Limitations:
– Not suitable for DC current measurement
– Requires a minimum current for accurate measurement
– Can be affected by magnetic saturation of the core
Hall Effect Sensor
Hall effect sensors utilize the Hall effect principle to measure magnetic fields generated by electric currents. A Hall effect sensor consists of a thin semiconductor material with current flowing through it. When the sensor is placed in a magnetic field perpendicular to the current flow, a voltage called the Hall voltage is generated across the semiconductor material, proportional to the magnetic field strength.
Advantages:
– Provides galvanic isolation between the sensed current and the output signal
– Suitable for both DC and AC current measurement
– Wide frequency range
– Compact size
Limitations:
– Requires a magnetic core or concentrator for optimal performance
– Susceptible to external magnetic interference
– May exhibit offset and temperature drift
Rogowski Coil
A Rogowski coil is an air-core toroidal coil used for measuring alternating current. It consists of a helical coil of wire with one end returning through the center of the coil. When placed around a conductor carrying an alternating current, the magnetic field induces a voltage in the coil proportional to the rate of change of the current.
Advantages:
– Provides galvanic isolation
– Suitable for measuring high AC currents
– Wide frequency range
– Flexible and easy to install
Limitations:
– Requires an integrator circuit to convert the coil output to a voltage proportional to the current
– Not suitable for DC current measurement
– May be affected by external magnetic fields
Designing a Current Monitor and Controller
When designing a current monitor and controller, several key considerations must be taken into account to ensure accurate and reliable current measurement and control. These considerations include:
Selecting the Appropriate Current Sensing Technique
The choice of the current sensing technique depends on factors such as the type of current (AC or DC), the current range, the required accuracy, and the isolation requirements. For example, a shunt resistor may be suitable for low-current DC applications, while a current transformer or Hall effect sensor may be preferred for high-current AC applications.
Signal Conditioning and Amplification
The output signal from the current sensor may require conditioning and amplification to interface with the monitoring and control circuitry. Signal conditioning may involve filtering to remove noise or unwanted frequency components, while amplification may be necessary to boost the signal to a suitable level for further processing.
Analog-to-Digital Conversion (ADC)
To process the current measurement data digitally, an analog-to-digital converter (ADC) is required. The ADC converts the analog voltage or current signal from the sensor into a digital representation that can be read by a microcontroller or other digital processing unit. The resolution and sampling rate of the ADC should be chosen based on the required accuracy and bandwidth of the current measurement.
Microcontroller or Digital Signal Processor (DSP)
A microcontroller or digital signal processor (DSP) is typically used to process the digitized current measurement data and implement control algorithms. The microcontroller or DSP reads the digital output from the ADC, performs necessary calculations or signal processing, and generates control signals based on the measured current.
Control Algorithms and Feedback
The current monitor and controller may implement various control algorithms depending on the application requirements. These algorithms can include:
-
Overcurrent Protection: The controller continuously compares the measured current against a predefined threshold and takes protective action (e.g., shutting down the system or triggering an alarm) if the current exceeds the threshold.
-
Current Limiting: The controller adjusts the system’s operation to maintain the current within a specified limit, preventing damage to the components or ensuring safe operation.
-
Closed-Loop Control: The controller uses the measured current as feedback to adjust the system’s parameters (e.g., voltage, duty cycle) to achieve a desired current level or maintain a constant current.
User Interface and Communication
The current monitor and controller may include a user interface, such as a display or LEDs, to provide real-time information about the measured current and system status. Additionally, communication interfaces, such as UART, I2C, or wireless modules, can be incorporated to enable data logging, remote monitoring, or integration with other systems.
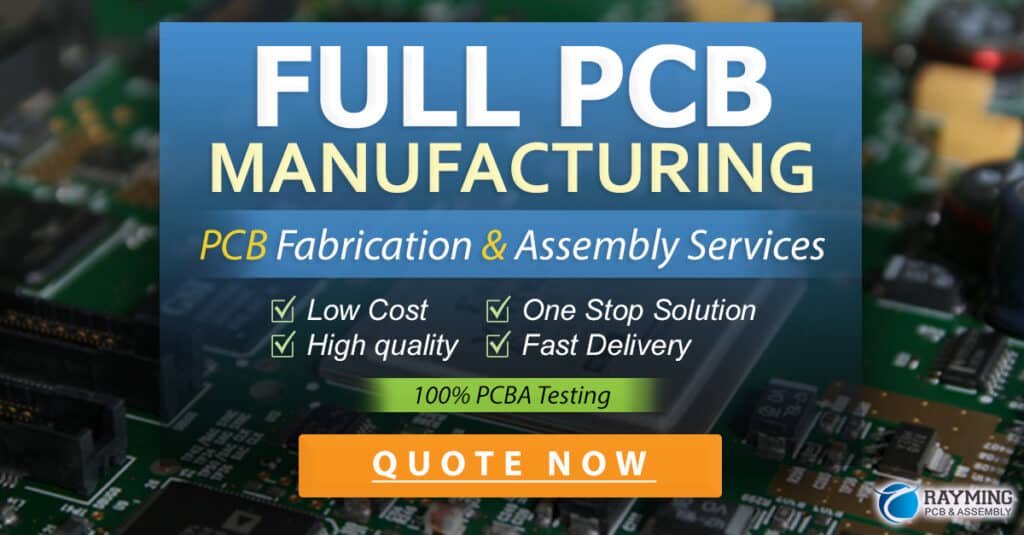
Implementing a Current Monitor and Controller
The implementation of a current monitor and controller involves several steps, including hardware design, software development, and system integration. Let’s explore each step in detail:
Hardware Design
-
Current Sensor Selection: Choose an appropriate current sensing technique based on the application requirements, such as the current range, accuracy, and isolation needs.
-
Signal Conditioning Circuit: Design the signal conditioning circuit to adapt the sensor output to the input requirements of the ADC. This may include amplification, filtering, or level-shifting stages.
-
ADC Selection: Select an ADC with suitable resolution, sampling rate, and interface compatibility with the microcontroller or DSP.
-
Microcontroller or DSP Selection: Choose a microcontroller or DSP with sufficient processing power, memory, and peripherals to handle the current monitoring and control tasks.
-
Power Supply: Design a stable and efficient power supply to provide the necessary voltage levels for the current sensor, signal conditioning circuit, ADC, and microcontroller or DSP.
-
PCB Design: Create a printed circuit board (PCB) layout that incorporates all the components, ensures proper grounding and shielding, and minimizes noise and interference.
Software Development
-
Initialization and Configuration: Write code to initialize and configure the microcontroller or DSP peripherals, such as GPIO pins, timers, and communication interfaces.
-
ADC Interfacing: Develop functions to read the digitized current measurement data from the ADC and convert it into meaningful values (e.g., current in amperes).
-
Control Algorithms: Implement the desired control algorithms, such as overcurrent protection, current limiting, or closed-loop control, using the measured current data as input.
-
User Interface: Develop code to update the user interface, such as displaying the current value on a screen or controlling LEDs based on the system status.
-
Communication Protocols: Implement communication protocols (e.g., UART, I2C) to enable data exchange between the current monitor and controller and external devices or systems.
System Integration and Testing
-
Hardware Assembly: Assemble the PCB, components, and enclosure according to the hardware design.
-
Software Integration: Integrate the developed software with the hardware, ensuring proper communication and functionality.
-
Calibration: Perform calibration procedures to ensure accurate current measurement and adjust any offset or gain errors.
-
Functional Testing: Conduct thorough testing to verify the current monitoring and control functionalities, including accuracy, response time, and stability.
-
Safety and Compliance Testing: Perform necessary safety and compliance tests to ensure the system meets the required standards and regulations.
-
Documentation: Prepare documentation, including schematics, PCB layouts, software code, and user manuals, for future reference and maintenance.
Applications and Case Studies
Current monitoring and control find applications in various domains, including:
Battery Management Systems (BMS)
In battery-powered devices, such as electric vehicles or portable electronics, current monitoring is crucial for ensuring safe and efficient battery charging and discharging. A BMS employs current sensors to measure the charging and discharging currents, and a microcontroller implements algorithms to control the charging process, prevent overcharging or undercharging, and estimate the battery’s state of charge (SoC) and state of health (SoH).
Case Study: Electric Vehicle BMS
In an electric vehicle, the BMS monitors the current flowing into and out of the battery pack using Hall effect sensors. The microcontroller processes the current data, along with voltage and temperature measurements, to determine the battery’s SoC, control the charging process, and ensure safe operation. The BMS may also communicate with other vehicle systems, such as the motor controller and charger, to optimize energy management and extend the battery’s lifespan.
Industrial Motor Control
Current monitoring is essential in industrial motor control applications to detect and protect against overcurrent conditions, such as motor stalls or overloads. By continuously measuring the motor current, the controller can implement protective measures, such as shutting down the motor or triggering an alarm, to prevent damage to the motor or the driven equipment.
Case Study: Conveyor Belt Motor Control
In a conveyor belt system, a current monitor and controller can be used to detect belt jams or blockages that cause the motor to draw excessive current. The controller continuously compares the measured current against a predefined threshold. If the current exceeds the threshold for a specified duration, the controller initiates a controlled shutdown of the motor and alerts the operator. This quick response helps prevent damage to the motor and minimizes downtime.
Power Monitoring and Energy Management
Current monitoring plays a vital role in power monitoring and energy management systems. By measuring the current consumption of individual loads or entire facilities, energy usage can be tracked, analyzed, and optimized. This data can be used to identify high-consuming devices, detect anomalies, and implement energy-saving strategies.
Case Study: Data Center Power Monitoring
In a data center, power monitoring is critical for ensuring the reliable operation of servers and cooling systems. Current sensors are installed at various points in the power distribution network, including uninterruptible power supplies (UPS), power distribution units (PDUs), and server racks. The current data is collected by a centralized monitoring system, which analyzes the power consumption patterns, detects any abnormalities, and provides insights for energy optimization. The system may also integrate with the data center’s cooling and ventilation controls to optimize energy efficiency.
Frequently Asked Questions (FAQ)
-
What is the difference between AC and DC current monitoring?
AC current monitoring involves measuring alternating current, which periodically reverses direction, while DC current monitoring deals with measuring direct current, which flows in a single direction. AC current monitoring typically requires current transformers or Rogowski coils, while DC current monitoring can be achieved using shunt resistors or Hall effect sensors. -
How does calibration affect the accuracy of current monitoring?
Calibration is the process of adjusting the current monitoring system to ensure accurate measurements. It involves comparing the measured current values against a known reference and correcting any offset or gain errors. Proper calibration is essential for maintaining the accuracy and reliability of the current monitoring system over time. -
Can a current monitor and controller be integrated with other systems?
Yes, a current monitor and controller can be integrated with other systems through various communication interfaces, such as UART, I2C, or wireless protocols. This integration allows the current monitoring data to be shared with other devices or systems for further analysis, control, or visualization purposes. -
What safety considerations should be taken when working with current monitoring systems?
When working with current monitoring systems, it is crucial to follow proper safety guidelines to prevent electrical hazards. This includes using appropriate personal protective equipment (PPE), such as insulated gloves and safety glasses, and ensuring that the system is properly grounded and protected against overcurrent conditions. Additionally, compliance with relevant electrical safety standards and regulations must be maintained. -
How can current monitoring help in predictive maintenance?
Current monitoring can provide valuable insights into the health and performance of electrical equipment. By analyzing current consumption patterns and detecting anomalies, potential faults or degradation can be identified before they lead to complete failures. This predictive maintenance approach allows for timely interventions, reducing downtime and maintenance costs.
Conclusion
Current monitoring and control are essential aspects of various electrical and electronic systems, enabling accurate measurement and regulation of electric current. By employing suitable current sensing techniques, signal conditioning, and digital processing, a current monitor and controller can be designed and implemented to meet the specific requirements of different applications.
The choice of the current sensing technique, such as shunt resistors, current transformers, Hall effect sensors, or Rogowski coils, depends on factors like the current type, range, accuracy, and isolation needs. Signal conditioning and amplification ensure that the sensor output is compatible with the ADC and microcontroller or DSP.
Software development plays a crucial role in implementing control algorithms, user interfaces, and communication protocols. The control algorithms can include overcurrent protection, current limiting, and closed-loop control, depending on the application requirements.
Current monitoring and control find applications in diverse domains, including battery management systems, industrial motor control, and power monitoring and energy management. These applications demonstrate the importance of accurate and reliable current measurement in ensuring safety, efficiency, and optimization.
When working with current monitoring systems, safety considerations, such as proper grounding, overcurrent protection, and compliance with relevant standards, are paramount. Additionally, calibration and regular maintenance are essential for maintaining the accuracy and reliability of the system over time.
As technology advances, current monitoring and control systems continue to evolve, integrating with other technologies like IoT, cloud computing, and artificial intelligence. These advancements enable remote monitoring, data analytics, and predictive maintenance, further enhancing the efficiency and reliability of electrical systems.
In conclusion, current monitoring and control play a vital role in ensuring the safe and efficient operation of electrical and electronic systems. By understanding the principles, techniques, and applications of current monitoring, designers and engineers can develop robust and reliable systems that meet the ever-growing demands of various industries.
Leave a Reply