What is Crosstalk and Why is it a Problem?
Crosstalk refers to the unwanted coupling of signals between adjacent traces on a PCB. When a signal on one trace induces noise onto a neighboring trace, it can lead to signal integrity issues, logic errors, and even complete circuit failures.
Some of the negative effects of crosstalk include:
- False switching of digital signals
- Reduced noise margins
- Timing errors and setup/hold violations
- Electromagnetic interference (EMI)
As data speeds increase and PCB traces are routed closer together, crosstalk becomes an increasingly serious design challenge. Fortunately, PCB design tools like Altium Designer provide features and techniques to analyze and mitigate crosstalk.
How Does Crosstalk Occur?
Crosstalk is a form of electromagnetic coupling between neighboring traces. There are two main coupling mechanisms:
-
Capacitive coupling – Electric fields from one trace induce voltages on an adjacent trace. Depends on the voltage swing, edge rates, and spacing between traces.
-
Inductive coupling – Magnetic fields from current flowing in one trace induce voltages on an adjacent trace. Depends on the current magnitude, edge rates, and loop areas.
The amount of crosstalk is determined by:
- Spatial separation between aggressor and victim traces
- Parallel run length
- Signal edge rates (faster edges produce more crosstalk)
- Characteristic impedance of traces
- Termination of victim traces
Techniques for Eliminating Crosstalk
Increase Spacing Between Traces
One of the most straightforward ways to reduce crosstalk is to increase the spacing between signal traces. Crosstalk falls off rapidly with increased separation.
Recommended minimum spacing between traces:
Signal Type | Minimum Spacing |
---|---|
Digital | 3 * trace width |
Analog | 5 * trace width |
High-speed | 10 * trace width |
In Altium Designer, use the PCB Rules and Constraints editor to specify minimum clearances between objects:
- Design -> Rules
- Electrical -> Clearance
- Create a new clearance rule
- Specify object match criteria and minimum clearance
Route Critical Traces on Different Layers
Another effective way to eliminate crosstalk is to route sensitive traces on different layers, orthogonal to each other. This minimizes capacitive and inductive coupling.
- Route critical traces on layers with ground planes in between for shielding
- Route sensitive signals on stripline layers embedded in the PCB stackup
- Use a ground layer adjacent to high-speed signal layers
In Altium, use the layer stack manager to set up an appropriate layer stackup:
- Design -> Layer Stack Manager
- Add dedicated signal and ground layers
- Arrange layers to minimize coupling
Minimize Parallel Run Lengths
The magnitude of crosstalk is proportional to the parallel run length between traces. Avoid long parallel runs, especially for sensitive or high-speed signals.
- Route signals orthogonal to each other whenever possible
- Stagger trace segments to minimize parallel runs
- Use curved or diagonal traces to avoid parallelism
Use Altium’s interactive routing tools to minimize parallelism:
- Route -> Interactive Routing
- Enable Advanced -> Avoid Parallel Routing
- Set the maximum uncoupled length
Match Trace Impedances
Mismatched trace impedances can worsen the impact of crosstalk by causing reflections. Matching the characteristic impedances of aggressor and victim traces minimizes this effect.
To set controlled impedance for traces in Altium:
- Design -> Rules -> Routing
- Routing Width -> Constraints
- Enable Width and Impedance Control
- Specify target impedance and trace width
The PCB editor will display real-time impedance information and DRC violations.
Terminate Traces Properly
Proper termination of traces is critical for maintaining signal integrity and minimizing crosstalk. Unterminated traces act as antennas for induced noise.
Types of termination:
- Series – Resistor in series with signal near driver
- Parallel – Resistor in parallel at end of trace
- AC – Series capacitor and pull-up/down
- Differential – Parallel resistor between diff pair
Use Altium’s termination tools:
- Place -> Terminators
- Select termination type, value, and footprint
- Automatically places and connects to net
Simulate and Analyze Crosstalk
Advanced PCB tools like Altium have built-in signal integrity simulation and analysis features. These allow you to predict and resolve crosstalk issues before fabrication.
Altium’s Signal Integrity Simulator:
- Tools -> Signal Integrity -> SIS Simulation
- Define stimulus waveforms and models
- Run coupled simulation
- View results in waveform viewer
Tips for crosstalk analysis:
- Focus on critical and high-speed nets
- Analyze multiple aggressor scenarios
- Verify at slow and fast corners
- Compare with and without crosstalk
- Iterate design until results are acceptable
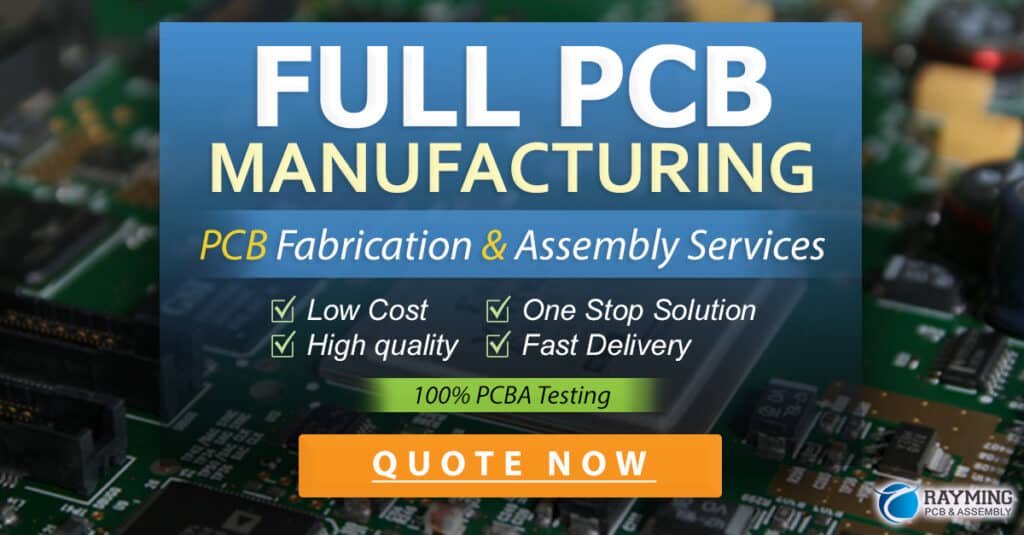
Crosstalk Elimination Checklist
Use this checklist to ensure you are following best practices for crosstalk elimination in your Altium PCB designs:
- [ ] Identify critical and sensitive nets
- [ ] Define clearance rules for minimum spacing
- [ ] Set up appropriate layer stackup
- [ ] Use ground planes for shielding
- [ ] Minimize parallel run lengths
- [ ] Route orthogonal on adjacent layers
- [ ] Define controlled trace impedances
- [ ] Properly terminate traces
- [ ] Simulate and analyze crosstalk
- [ ] Verify crosstalk meets required specs
Frequently Asked Questions
What is the difference between crosstalk and EMI?
Crosstalk is coupling between traces within a PCB, while EMI is radiated emissions that can interfere with external devices. However, crosstalk can lead to EMI if not properly contained.
How much crosstalk is acceptable?
The acceptable amount of crosstalk depends on the specific circuit requirements and signal integrity budget. In general, crosstalk should be kept below 10% of the signal swing to avoid false switching and timing errors.
Can I use autorouting to minimize crosstalk?
While autorouters can be set up with rules to minimize crosstalk, they may not always find the optimal routing solution. It is best to manually route critical traces and use autorouting for less sensitive signals.
What if I can’t increase spacing between traces?
If increasing trace spacing is not feasible due to PCB size constraints, focus on other techniques such as routing on different layers, minimizing parallel runs, and using ground shields.
How do I choose the right termination scheme?
The appropriate termination scheme depends on the signal characteristics and transmission line effects. In general, use series termination for short traces, parallel termination for long traces, and differential termination for differential pairs. Simulation can help determine the optimal termination values.
Leave a Reply