Introduction to 150W LED Drivers
A 150W LED driver is a specialized electronic device designed to provide a constant current source to power high-wattage LED lighting panels. These drivers are essential components in large-scale lighting applications, such as commercial signage, outdoor lighting, and industrial illumination. The primary function of a 150W LED driver is to convert AC power from the mains supply into a regulated DC current suitable for driving the LED array.
Key Features of 150W LED Drivers
- High power output: 150W drivers can supply sufficient current to illuminate large LED panels.
- Constant current regulation: Maintains a stable current output regardless of variations in voltage or load.
- Efficiency: High-quality 150W LED drivers offer power conversion efficiencies of up to 90% or more.
- Protection features: Over-voltage, over-current, and thermal protection to ensure safe operation.
- Dimming capabilities: Many 150W drivers support various dimming methods, such as 0-10V or PWM.
Designing a 150W LED Driver Circuit
Step 1: Determine the LED Panel Specifications
Before designing the driver circuit, it is crucial to know the specifications of the LED panel you intend to power. The key parameters include:
- Forward voltage (Vf) of the LED array
- Forward current (If) required by the LED array
- Number of LEDs in series and parallel configurations
Step 2: Select a Suitable Topology
There are several topologies to choose from when designing a 150W LED driver. Some popular options include:
- Buck converter: Step-down DC-DC converter, suitable for low-voltage LED arrays.
- Boost converter: Step-up DC-DC converter, ideal for high-voltage LED arrays.
- Flyback converter: Isolated topology for applications requiring galvanic isolation.
Consider factors such as efficiency, complexity, and cost when selecting the appropriate topology for your 150W LED driver.
Step 3: Calculate Component Values
Once you have chosen a topology, calculate the values of the various components required for the driver circuit. This typically involves determining:
- Inductor value: Based on the switching frequency, ripple current, and duty cycle.
- Output capacitor: Calculated to minimize output voltage ripple.
- Power MOSFET: Selected based on the maximum current and voltage ratings.
- Rectifier diode: Chosen for its forward voltage drop and current handling capability.
Use established formulas and design guidelines specific to the selected topology to calculate the component values accurately.
Step 4: Implement Protection Features
To ensure the reliable and safe operation of your 150W LED driver, incorporate essential protection features, such as:
- Over-voltage protection (OVP): Prevents damage to the LED array due to excessive voltage.
- Over-current protection (OCP): Limits the current to a safe level, protecting the driver and LEDs.
- Thermal shutdown (TSD): Disables the driver if the temperature exceeds a predetermined threshold.
These protection features can be implemented using dedicated ICs or discrete components, depending on the complexity and cost constraints of your design.
Step 5: Design the PCB Layout
A well-designed PCB layout is critical for the optimal performance and reliability of your 150W LED driver. Consider the following aspects when creating the PCB:
- Component placement: Arrange components to minimize trace lengths and optimize thermal management.
- Trace width: Ensure traces are wide enough to handle the expected current without excessive heating.
- Ground plane: Use a solid ground plane to reduce electromagnetic interference (EMI) and improve heat dissipation.
- Shielding: Implement proper shielding techniques to minimize EMI and ensure compliance with relevant standards.
Implementing Dimming Control in 150W LED Drivers
Dimming control is a desirable feature in many LED lighting applications, allowing users to adjust the brightness of the LED panel according to their preferences or requirements. There are several methods for implementing dimming control in 150W LED drivers:
1. 0-10V Dimming
0-10V dimming is an analog dimming method that uses a separate control voltage to adjust the output current of the LED driver. The dimming signal ranges from 0V (minimum brightness) to 10V (maximum brightness). To implement 0-10V dimming in your 150W LED driver:
- Add a 0-10V input circuit to the driver, typically consisting of a voltage divider and a buffer amplifier.
- Modify the driver’s control circuit to adjust the output current based on the 0-10V input signal.
- Ensure the driver maintains a stable current output across the entire dimming range.
2. PWM Dimming
Pulse-width modulation (PWM) dimming involves rapidly switching the LED current on and off to control the average brightness. The duty cycle of the PWM signal determines the perceived brightness of the LED panel. To incorporate PWM dimming in your 150W LED driver:
- Generate a high-frequency PWM signal using a microcontroller or a dedicated PWM controller IC.
- Use the PWM signal to control the switching of the power MOSFET in the driver circuit.
- Adjust the duty cycle of the PWM signal to achieve the desired dimming level.
- Implement a smoothing capacitor to minimize flicker and ensure a stable light output.
3. DALI Dimming
Digital Addressable Lighting Interface (DALI) is a digital dimming protocol that allows for individual control of LED luminaires in a lighting network. To add DALI dimming functionality to your 150W LED driver:
- Incorporate a DALI communication interface, such as a DALI transceiver IC, into your driver design.
- Implement the necessary firmware to interpret DALI commands and adjust the driver’s output accordingly.
- Configure the driver to respond to DALI dimming commands and maintain the desired brightness levels.
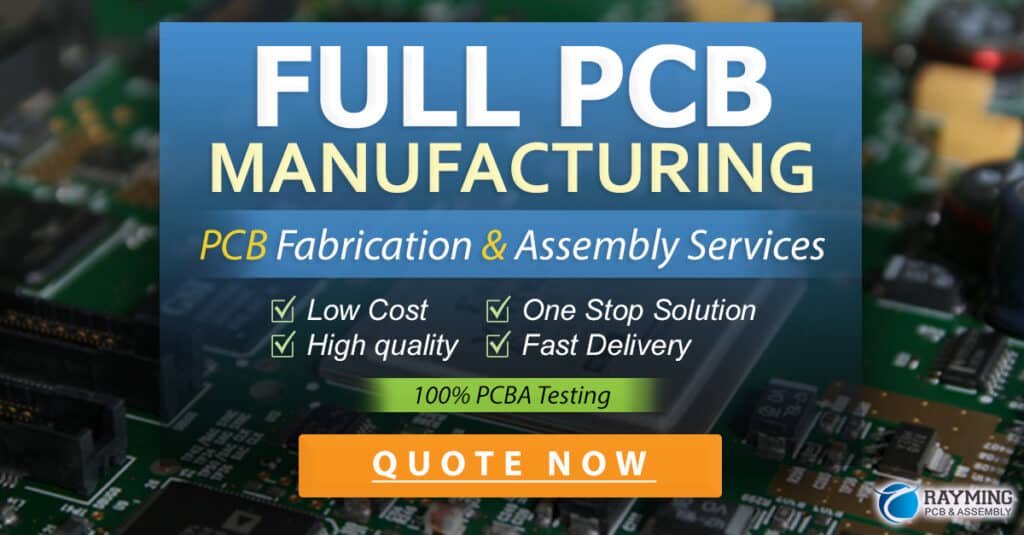
Thermal Management in 150W LED Drivers
Proper thermal management is essential for ensuring the long-term reliability and performance of your 150W LED driver. As the driver components generate heat during operation, it is crucial to implement effective heat dissipation techniques to prevent overheating and premature failure.
Heatsink Selection
Selecting an appropriate heatsink is the first step in managing the thermal performance of your 150W LED driver. Consider the following factors when choosing a heatsink:
- Thermal resistance: Ensure the heatsink has a low thermal resistance to efficiently transfer heat away from the driver components.
- Surface area: A larger surface area enables better heat dissipation, so choose a heatsink with ample surface area for your application.
- Material: Heatsinks made from materials with high thermal conductivity, such as aluminum or copper, are preferred for optimal heat transfer.
Thermal Interface Materials
Thermal interface materials (TIMs) are used to enhance the heat transfer between the driver components and the heatsink. Some common TIMs include:
- Thermal grease: A high-conductivity paste that fills the air gaps between the component and heatsink surfaces.
- Thermal pads: Pre-cut, compressible pads that provide electrical insulation and conformability to uneven surfaces.
- Phase-change materials: Compounds that melt and flow at operating temperatures, providing excellent thermal conductivity.
Select the appropriate TIM based on the specific requirements of your 150W LED driver design, such as thermal performance, ease of application, and cost.
Airflow and Ventilation
In addition to heatsinks and TIMs, ensuring adequate airflow and ventilation around the 150W LED driver is essential for effective thermal management. Consider the following techniques:
- Passive cooling: Use natural convection to promote airflow around the driver components and heatsink.
- Active cooling: Incorporate fans or other forced-air cooling solutions to enhance heat dissipation in more demanding applications.
- Enclosure design: Optimize the driver enclosure to facilitate airflow and prevent heat buildup, using features such as vents or perforations.
Testing and Validation of 150W LED Drivers
Once you have designed and built your 150W LED driver, it is essential to perform thorough testing and validation to ensure its performance, reliability, and safety. Some key aspects to test include:
- Output current and voltage: Verify that the driver delivers the expected output current and voltage across the entire operating range.
- Efficiency: Measure the driver’s power conversion efficiency at various load levels and input voltages.
- Regulation: Confirm that the driver maintains a stable output current despite fluctuations in input voltage or load.
- Protection features: Test the over-voltage, over-current, and thermal protection mechanisms to ensure they function as intended.
- Dimming performance: Validate the dimming functionality, ensuring smooth and flicker-free operation across the entire dimming range.
- Electromagnetic compatibility (EMC): Conduct EMC testing to verify that the driver complies with relevant standards and regulations.
Document the test results and make any necessary adjustments or improvements to the driver design based on the findings.
Frequently Asked Questions (FAQ)
- What is the typical efficiency of a 150W LED driver?
-
High-quality 150W LED drivers can achieve power conversion efficiencies of 90% or higher, minimizing energy losses and reducing heat generation.
-
Can a 150W LED driver be used with different LED panel configurations?
-
Yes, a well-designed 150W LED driver can be compatible with various LED panel configurations, as long as the total forward voltage and current requirements fall within the driver’s specifications.
-
How do I select the appropriate heatsink for my 150W LED driver?
-
When selecting a heatsink, consider factors such as thermal resistance, surface area, and material. Ensure the heatsink can effectively dissipate the heat generated by the driver components without exceeding the maximum operating temperature.
-
What is the difference between 0-10V and PWM dimming in 150W LED drivers?
-
0-10V dimming uses an analog control voltage to adjust the output current, while PWM dimming rapidly switches the LED current on and off to control the average brightness. 0-10V dimming is simpler to implement, while PWM dimming offers more precise control and better compatibility with digital systems.
-
How can I ensure my 150W LED driver complies with relevant EMC standards?
- To ensure EMC compliance, implement proper PCB layout techniques, such as using a solid ground plane, minimizing loop areas, and incorporating EMI filters. Conduct thorough EMC testing and make necessary adjustments to the driver design to meet the required standards.
Conclusion
Designing and building a powerful 150W LED driver for driving large lighting panels requires careful consideration of various factors, including LED panel specifications, driver topology, component selection, protection features, and thermal management. By following the steps outlined in this article and implementing appropriate dimming control and testing procedures, you can create a reliable and efficient 150W LED driver tailored to your specific application requirements.
As LED lighting technology continues to advance, the demand for high-performance 150W LED drivers will only increase. By staying up-to-date with the latest design techniques and industry trends, you can develop innovative and competitive LED driver solutions that meet the ever-growing needs of the lighting market.
Component | Function |
---|---|
Power MOSFET | Switches the LED current on and off |
Rectifier Diode | Converts AC to DC and protects against reverse voltage |
Inductor | Stores energy and smooths the output current |
Output Capacitor | Reduces output voltage ripple |
Control IC | Regulates the output current and implements protection |
Heatsink | Dissipates heat generated by the driver components |
Table 1: Key components in a 150W LED driver and their functions
Dimming Method | Control Signal | Advantages | Disadvantages |
---|---|---|---|
0-10V | Analog voltage | Simple implementation, widely compatible | Limited resolution, requires extra wiring |
PWM | Digital pulses | Precise control, no additional wiring needed | Requires filtering to avoid flicker |
DALI | Digital data | Individual addressability, bidirectional communication | Higher complexity and cost |
Table 2: Comparison of common dimming methods for 150W LED drivers
By understanding the key components, dimming methods, and design considerations for 150W LED drivers, you can create efficient, reliable, and versatile lighting solutions for a wide range of applications. As the lighting industry continues to evolve, staying informed about the latest advancements in LED driver technology will be essential for success in this dynamic field.
Leave a Reply