What is Multi-Board Assembly?
Multi-board assembly, also known as a multi-board system or a multi-board module, is a technique used in electronics manufacturing where multiple printed circuit boards (PCBs) are interconnected to form a single functional unit. This approach is commonly employed when a single PCB cannot accommodate all the necessary components or when the design requires modular functionality, enhanced performance, or improved reliability.
In a multi-board assembly, individual PCBs are designed to perform specific functions and are connected through various methods such as connectors, cables, or board-to-board stacking. This modular design allows for easier maintenance, upgrades, and troubleshooting, as each board can be replaced or modified independently without affecting the entire system.
Advantages of Multi-Board Assembly
- Modularity: Multi-board assembly enables a modular design approach, allowing for easier upgrades, maintenance, and customization of the electronic system.
- Increased Functionality: By distributing components and functions across multiple boards, designers can incorporate more features and capabilities into the system.
- Improved Performance: Separating critical components and signal paths onto different boards can minimize electromagnetic interference (EMI) and improve overall system performance.
- Enhanced Reliability: Multi-board assembly can improve reliability by isolating potential points of failure and allowing for easier replacement of faulty modules.
- Space Optimization: Splitting a large PCB into smaller, interconnected boards can help optimize space utilization in compact electronic devices.
Design Considerations for Multi-Board Assembly
When designing a multi-board assembly, several key factors must be considered to ensure proper functionality, reliability, and manufacturability.
Board Interconnection
Choosing the appropriate method for connecting the individual boards is crucial in multi-board assembly. The most common interconnection methods include:
- Connectors: Various types of connectors, such as board-to-board, wire-to-board, or cable-to-board connectors, can be used to establish electrical connections between boards.
- Cables: Flexible cables, such as ribbon cables or coaxial cables, can be used to interconnect boards when a certain degree of flexibility is required or when boards are physically separated.
- Board Stacking: Boards can be stacked vertically using board-to-board connectors, pins, or sockets, allowing for a compact and space-efficient assembly.
When selecting the interconnection method, consider factors such as signal integrity, power requirements, mechanical stability, and ease of assembly and maintenance.
Signal Integrity
Maintaining signal integrity is essential in multi-board assembly to ensure proper communication between boards and to minimize interference. Consider the following aspects:
- Impedance Matching: Ensure that the impedance of the interconnections matches the impedance of the signal traces on the boards to minimize reflections and signal distortion.
- Shielding: Use shielding techniques, such as ground planes or shielded cables, to minimize crosstalk and electromagnetic interference between boards.
- Length Matching: Match the lengths of critical signal paths across boards to minimize timing skew and ensure synchronous communication.
Power Distribution
Proper power distribution is crucial in multi-board assembly to ensure that each board receives a stable and reliable power supply. Consider the following:
- Power Sequencing: Determine the proper power-up and power-down sequences for the boards to prevent damage and ensure proper initialization.
- Decoupling: Use decoupling capacitors near power entry points on each board to minimize power supply noise and provide local energy storage.
- Voltage Regulation: Implement voltage regulation techniques, such as using voltage regulators or power management ICs, to provide stable and accurate voltage levels to each board.
Mechanical Considerations
When designing a multi-board assembly, mechanical aspects play a significant role in ensuring proper fit, stability, and reliability. Consider the following:
- Enclosure Design: Design the enclosure to accommodate the multi-board assembly, considering factors such as board dimensions, interconnections, and cooling requirements.
- Mounting and Fastening: Determine the appropriate methods for mounting and fastening the boards within the enclosure, such as using standoffs, screws, or snap-fit mechanisms.
- Vibration and Shock: Assess the expected vibration and shock levels in the intended operating environment and design the assembly to withstand these conditions.
Manufacturing and Assembly Process
The manufacturing and assembly process for multi-board assemblies involves several steps to ensure proper functionality and reliability.
PCB Fabrication
Each individual board in the multi-board assembly undergoes the standard PCB fabrication process, which typically includes the following steps:
- PCB Design: The PCB layout is designed using electronic design automation (EDA) tools, considering factors such as component placement, signal routing, and manufacturing constraints.
- Gerber File Generation: The PCB design is exported as a set of Gerber files, which contain the necessary information for PCB fabrication, such as copper layers, solder mask, and silkscreen.
- PCB Manufacture: The Gerber files are sent to a PCB manufacturer, who fabricates the physical boards using processes such as etching, drilling, and plating.
Component Placement and Soldering
Once the individual boards are fabricated, the components are placed and soldered onto each board. This process can be done manually or using automated equipment, such as pick-and-place machines and reflow ovens.
- Solder Paste Application: Solder paste is applied to the component pads on the PCB using techniques such as stencil printing or dispensing.
- Component Placement: Components are placed onto the solder paste-coated pads, either manually or using automated pick-and-place machines.
- Soldering: The boards with placed components are passed through a reflow oven, which melts the solder paste and forms electrical connections between the components and the board.
Board Interconnection and Assembly
After the individual boards are populated with components, they are interconnected and assembled into the final multi-board assembly.
- Interconnection: The boards are interconnected using the chosen method, such as connectors, cables, or board stacking, ensuring proper alignment and secure connections.
- Mechanical Assembly: The interconnected boards are mounted and fastened within the enclosure, following the mechanical design considerations.
- Testing and Inspection: The multi-board assembly undergoes various tests and inspections to verify proper functionality, signal integrity, and reliability.
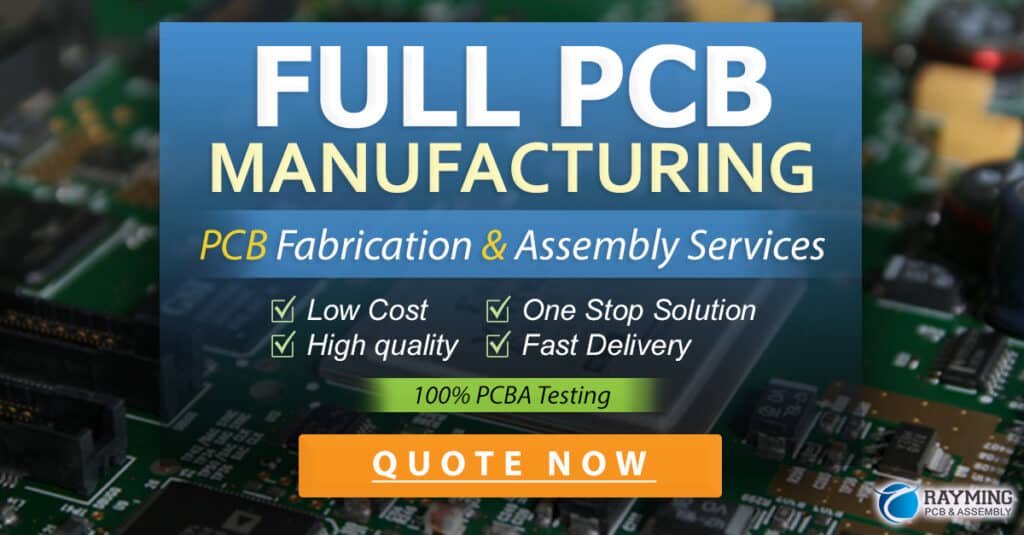
Testing and Quality Control
To ensure the reliability and functionality of a multi-board assembly, thorough testing and quality control measures are essential throughout the manufacturing process.
In-Circuit Testing (ICT)
In-circuit testing is performed on individual boards to verify the proper assembly and functionality of components. ICT involves using a bed-of-nails fixture to make electrical contact with specific test points on the board, allowing for the measurement of component values, presence, and orientation.
Functional Testing
Functional testing is conducted on the complete multi-board assembly to verify that it meets the specified performance and functionality requirements. This testing may include:
- Power-On Testing: Verifying proper power-up sequences, voltage levels, and current consumption.
- Signal Integrity Testing: Measuring signal quality, timing, and integrity across board interconnections.
- Functional Verification: Testing the assembly’s functionality under various operating conditions and scenarios.
Environmental Testing
Environmental testing is performed to ensure that the multi-board assembly can withstand the expected operating conditions, such as temperature, humidity, vibration, and shock. Common environmental tests include:
- Temperature Cycling: Exposing the assembly to alternating high and low temperature extremes to verify its ability to function and survive in the specified temperature range.
- Vibration and Shock Testing: Subjecting the assembly to specified levels of vibration and shock to ensure its mechanical integrity and functionality under these conditions.
- Humidity Testing: Exposing the assembly to high humidity levels to check for potential issues such as corrosion or electrical leakage.
Quality Control and Inspection
Quality control measures are implemented throughout the manufacturing process to identify and prevent defects and ensure consistent quality. These measures may include:
- Visual Inspection: Visually examining the boards and assembly for defects such as poor soldering, component misalignment, or mechanical damage.
- Automated Optical Inspection (AOI): Using automated cameras and image processing software to detect assembly defects, such as missing or misplaced components, solder bridging, or incorrect component polarity.
- X-Ray Inspection: Employing X-ray imaging to inspect solder joints and components that are not visible from the surface, such as ball grid array (BGA) packages or hidden interconnections.
Best Practices for Multi-Board Assembly
To ensure a successful multi-board assembly, consider the following best practices:
- Design for Manufacturability (DFM): Follow DFM guidelines to ensure that the individual boards and the overall assembly can be manufactured efficiently and reliably.
- Collaborate with Manufacturers: Engage with PCB fabrication and assembly partners early in the design process to discuss design requirements, constraints, and potential manufacturing challenges.
- Prototype and Test Early: Build and test prototypes of the multi-board assembly as early as possible to identify and resolve any design or manufacturing issues.
- Use Standard Components: Whenever possible, use standard components and connectors to simplify sourcing, reduce costs, and improve reliability.
- Document Thoroughly: Maintain comprehensive documentation, including schematics, PCB layouts, assembly drawings, and test procedures, to ensure clear communication and facilitate future maintenance and upgrades.
- Plan for Scalability: Consider the potential for future upgrades, expansions, or variations of the multi-board assembly, and design with scalability in mind.
Frequently Asked Questions (FAQ)
-
Q: What are the main advantages of using a multi-board assembly approach?
A: The main advantages of multi-board assembly include modularity, increased functionality, improved performance, enhanced reliability, and space optimization. -
Q: How do I choose the best interconnection method for my multi-board assembly?
A: The choice of interconnection method depends on factors such as signal integrity, power requirements, mechanical stability, and ease of assembly and maintenance. Common methods include connectors, cables, and board stacking. -
Q: What are some key considerations for maintaining signal integrity in multi-board assemblies?
A: To maintain signal integrity, consider impedance matching, shielding, and length matching of critical signal paths across boards. -
Q: How can I ensure proper power distribution in a multi-board assembly?
A: Ensure proper power distribution by considering power sequencing, decoupling, and voltage regulation techniques for each board in the assembly. -
Q: What types of testing are typically performed on multi-board assemblies?
A: Common types of testing for multi-board assemblies include in-circuit testing (ICT), functional testing, and environmental testing (temperature, vibration, shock, and humidity). Additionally, quality control measures such as visual inspection, automated optical inspection (AOI), and X-ray inspection are employed.
Conclusion
Creating a physical multi-board assembly requires careful consideration of various design, manufacturing, and testing aspects. By following best practices and collaborating with experienced partners, designers can develop reliable, high-performance multi-board systems that meet the specific requirements of their applications.
Key considerations include board interconnection, signal integrity, power distribution, mechanical design, and thorough testing and quality control measures. By addressing these factors and adopting a modular, scalable approach, multi-board assemblies can provide enhanced functionality, improved performance, and increased reliability in a wide range of electronic applications.
Aspect | Key Considerations |
---|---|
Board Interconnection | Choose appropriate methods such as connectors, cables, or board stacking based on signal integrity, power, and mechanical requirements. |
Signal Integrity | Ensure impedance matching, shielding, and length matching of critical signal paths. |
Power Distribution | Consider power sequencing, decoupling, and voltage regulation techniques for each board. |
Mechanical Design | Design enclosure, mounting, and fastening methods to ensure proper fit, stability, and reliability. |
Testing | Perform in-circuit testing, functional testing, and environmental testing to verify functionality and reliability. |
Quality Control | Implement visual inspection, automated optical inspection, and X-ray inspection to identify and prevent defects. |
Best Practices | Follow design for manufacturability guidelines, collaborate with manufacturers, prototype early, use standard components, document thoroughly, and plan for scalability. |
By understanding and addressing these critical aspects of multi-board assembly, designers can create robust, reliable, and high-performance electronic systems that meet the demands of modern applications.
Leave a Reply