Introduction to PCB Substacks
Printed Circuit Board (PCB) substacks are an essential component in modern electronics design and manufacturing. A PCB substack refers to a stack of multiple PCB layers that are laminated together to form a single, compact unit. This technique allows for increased functionality and miniaturization of electronic devices by enabling the integration of more components and interconnections within a limited space.
In this article, we will dive deep into the world of PCB substacks, exploring their benefits, design considerations, manufacturing processes, and applications across various industries.
Benefits of PCB Substacks
Space Optimization
One of the primary advantages of using PCB substacks is the ability to optimize space within electronic devices. By stacking multiple PCB layers on top of each other, designers can significantly reduce the overall footprint of the circuit board without compromising on functionality. This space optimization is particularly crucial in industries such as consumer electronics, where compact and lightweight devices are in high demand.
Enhanced Functionality
PCB substacks enable designers to incorporate more features and functions into a single circuit board. With multiple layers available, it becomes possible to route more complex circuits, add additional components, and create intricate interconnections between different sections of the board. This enhanced functionality allows for the development of sophisticated electronic devices that can perform a wide range of tasks.
Improved Signal Integrity
Signal integrity is a critical factor in the performance and reliability of electronic devices. PCB substacks offer several advantages in terms of signal integrity:
- Shorter signal paths: By stacking layers, the distance between components can be reduced, resulting in shorter signal paths and minimized signal degradation.
- Controlled impedance: Substacks allow for better control over the impedance of the signal traces, ensuring proper matching and reducing signal reflections.
- Shielding: Layers within the substack can be dedicated to power and ground planes, providing effective shielding against electromagnetic interference (EMI) and crosstalk.
Cost-Effectiveness
While the initial design and manufacturing costs of PCB substacks may be higher compared to single-layer boards, they offer long-term cost benefits. By consolidating multiple circuits into a single substack, the overall component count and assembly time can be reduced, leading to lower production costs. Additionally, the space optimization achieved through substacks allows for smaller device enclosures, further reducing material and manufacturing expenses.
PCB Substack Design Considerations
Designing a PCB substack requires careful consideration of various factors to ensure optimal performance, manufacturability, and reliability. Some key design considerations include:
Layer Stack-Up
The layer stack-up refers to the arrangement and order of the individual PCB layers within the substack. It is essential to plan the stack-up carefully, taking into account factors such as signal integrity, power distribution, and manufacturability. The stack-up design should consider the following:
- Number of layers required
- Thickness of each layer
- Material selection for each layer (e.g., FR-4, Rogers, etc.)
- Copper weight and trace width
- Dielectric constant and loss tangent of the insulating materials
Via Management
Vias are conductive holes drilled through the PCB layers to establish electrical connections between different layers. In PCB substacks, via management becomes crucial to ensure proper connectivity and signal integrity. Designers need to consider the following aspects:
- Via types (e.g., through-hole, blind, buried)
- Via sizes and drill diameters
- Via placement and spacing
- Via stubs and their impact on signal integrity
- Via-in-pad design for component mounting
Thermal Management
PCB substacks, due to their compact nature, can generate significant heat during operation. Proper thermal management is essential to prevent overheating and ensure reliable performance. Designers should consider the following thermal management techniques:
- Thermal vias to conduct heat away from hot spots
- Copper pours and heat spreaders to dissipate heat
- Thermal interface materials (TIMs) between layers
- Ventilation and cooling solutions at the system level
Signal and Power Integrity
Maintaining signal and power integrity is crucial in PCB substack design. Designers need to address the following aspects:
- Impedance matching and controlled impedance traces
- Power and ground plane design for stable power distribution
- Decoupling and bypassing capacitors for noise reduction
- Electromagnetic compatibility (EMC) and EMI shielding
- Cross-talk and signal coupling analysis
DFM Considerations
Designing for manufacturability (DFM) is essential to ensure the successful fabrication and assembly of PCB substacks. Designers should adhere to the following DFM guidelines:
- Minimum feature sizes (e.g., trace width, spacing, drill sizes)
- Clearance and creepage distances
- Solder mask and silkscreen requirements
- Panelization and routing considerations
- Assembly process compatibility (e.g., reflow, wave soldering)
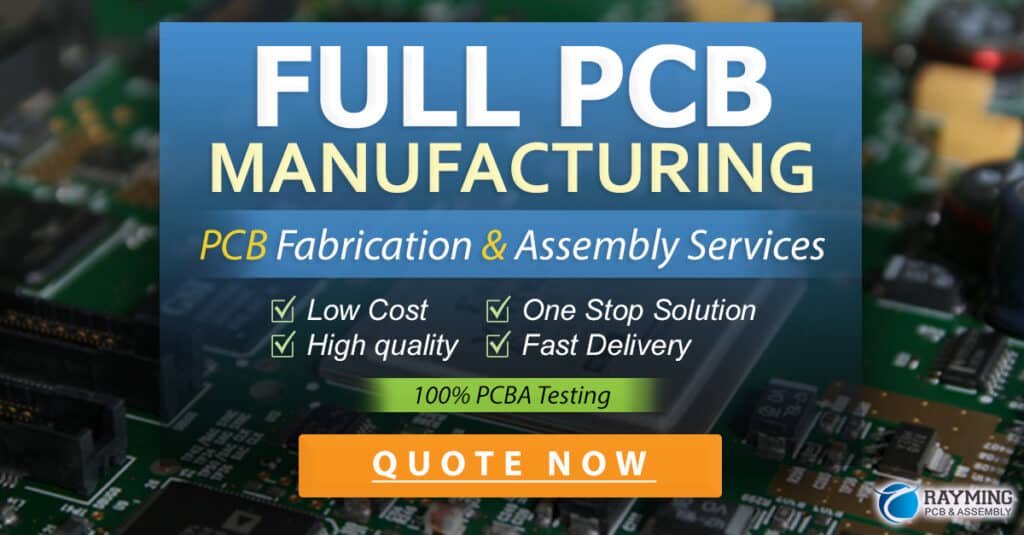
PCB Substack Manufacturing Process
The manufacturing process for PCB substacks involves several steps to ensure the accurate and reliable fabrication of the final product. The key stages in the manufacturing process include:
Layer Fabrication
Each individual layer of the PCB substack is fabricated separately using standard PCB manufacturing techniques. This involves the following steps:
- Copper cladding: A thin layer of copper is bonded to the base substrate material (e.g., FR-4).
- Patterning: The desired circuit pattern is transferred onto the copper layer using photolithography or direct imaging techniques.
- Etching: The unwanted copper is removed using chemical etching, leaving behind the desired circuit traces.
- Drilling: Holes are drilled through the layer for vias and component mounting.
Lamination
Once the individual layers are fabricated, they are stacked and aligned according to the designed layer stack-up. The layers are then laminated together using heat and pressure to form a solid, cohesive substack. The lamination process typically involves the following steps:
- Layer registration: The layers are precisely aligned using registration marks or pins.
- Prepreg application: Prepreg (pre-impregnated) materials, which are partially cured B-stage epoxy sheets, are placed between the layers to act as an adhesive and insulator.
- Lamination press: The stack-up is placed in a lamination press, where heat and pressure are applied to cure the prepreg and bond the layers together.
Drilling and Plating
After lamination, additional drilling and plating processes are performed on the substack:
- Via drilling: Holes are drilled through the substack to create vias that connect different layers.
- Plating: The drilled holes are plated with copper to establish electrical connections between layers.
- Copper capping: Additional copper is plated onto the surface of the substack to increase the thickness of the outer layers.
Finishing
The final steps in the manufacturing process involve applying protective coatings and finishes to the PCB substack:
- Solder mask application: A solder mask layer is applied to protect the copper traces and prevent short circuits during soldering.
- Surface finish: A surface finish, such as immersion gold (ENIG), immersion silver, or HASL (Hot Air Solder Leveling), is applied to the exposed copper areas to enhance solderability and protect against oxidation.
- Silkscreen printing: Text, logos, and component markings are printed onto the solder mask using silkscreen printing.
Electrical Testing
Before the PCB substack is released for assembly, it undergoes thorough electrical testing to ensure its functionality and reliability. This includes:
- Continuity testing: Checking for open and short circuits.
- Insulation resistance testing: Verifying the insulation between different layers and traces.
- High-potential (HiPot) testing: Applying high voltage to detect any insulation breakdowns or leakage currents.
Applications of PCB Substacks
PCB substacks find applications in a wide range of industries and products. Some notable applications include:
Consumer Electronics
PCB substacks are extensively used in consumer electronic devices such as smartphones, tablets, laptops, and wearables. The compact and multi-functional nature of substacks enables the development of sleek and feature-rich devices that meet consumer demands.
Automotive Electronics
The automotive industry relies heavily on PCB substacks for various electronic systems, including infotainment, navigation, advanced driver assistance systems (ADAS), and engine control units (ECUs). Substacks provide the necessary reliability and performance required in the harsh automotive environment.
Medical Devices
Medical devices, such as implantable devices, diagnostic equipment, and monitoring systems, utilize PCB substacks for their miniaturization and functionality. Substacks enable the integration of complex electronic circuits into compact and reliable medical devices.
Aerospace and Defense
PCB substacks are used in aerospace and defense applications, including avionics, radar systems, and military communication equipment. The high-density interconnect (HDI) capabilities of substacks allow for the development of advanced and ruggedized electronic systems that can withstand extreme conditions.
Industrial Automation
Industrial automation systems, such as programmable logic controllers (PLCs), sensors, and actuators, rely on PCB substacks for their compact size and robust performance. Substacks enable the integration of multiple functions into a single unit, simplifying installation and maintenance.
Frequently Asked Questions (FAQ)
-
Q: What is the difference between a PCB substack and a traditional single-layer PCB?
A: A PCB substack consists of multiple PCB layers laminated together, while a traditional single-layer PCB has only one layer. Substacks offer increased functionality, space optimization, and improved signal integrity compared to single-layer PCBs. -
Q: How many layers can be incorporated into a PCB substack?
A: The number of layers in a PCB substack can vary depending on the specific requirements of the application. Substacks can range from a few layers to over 50 layers in high-density designs. -
Q: What are the advantages of using blind and buried vias in PCB substacks?
A: Blind and buried vias in PCB substacks offer several advantages, such as increased routing density, improved signal integrity, and reduced overall board size. Blind vias connect an outer layer to an inner layer, while buried vias connect inner layers without reaching the outer layers. -
Q: How does the choice of dielectric material impact the performance of a PCB substack?
A: The choice of dielectric material in a PCB substack affects its electrical and thermal properties. Factors such as dielectric constant, loss tangent, and thermal conductivity should be considered based on the specific requirements of the application. Common dielectric materials include FR-4, Rogers, and polyimide. -
Q: What are the challenges associated with the assembly of PCB substacks?
A: The assembly of PCB substacks can present challenges such as alignment accuracy, thermal management, and soldering. Proper design considerations, such as via placement, component layout, and thermal management techniques, should be incorporated to ensure successful assembly. Additionally, specialized assembly processes, such as pin-in-paste or press-fit technology, may be required for certain substack designs.
Conclusion
PCB substacks have revolutionized the electronics industry by enabling the development of compact, high-performance, and multi-functional devices. By stacking multiple PCB layers together, designers can optimize space, enhance functionality, improve signal integrity, and achieve cost-effectiveness.
However, designing and manufacturing PCB substacks requires careful consideration of various factors, including layer stack-up, via management, thermal management, signal and power integrity, and DFM guidelines. By following best practices and collaborating with experienced PCB manufacturers, designers can successfully create PCB substacks that meet the demanding requirements of modern electronic applications.
As technology continues to advance, the use of PCB substacks is expected to grow across various industries, driving innovation and enabling the development of next-generation electronic devices. By staying up-to-date with the latest advancements in PCB substack design and manufacturing, engineers and designers can leverage this powerful technology to create cutting-edge products that push the boundaries of what is possible.
Leave a Reply