Introduction to PCB Footprints
A PCB footprint, also known as a land pattern or pad layout, is the arrangement of copper pads and associated information on a printed circuit board (PCB) that corresponds to the pins or leads of a specific electronic component. The footprint defines the size, shape, and spacing of the pads, as well as any additional features such as silkscreen markings, solder mask openings, and keepout areas.
Creating accurate and reliable PCB footprints is crucial for ensuring proper component placement, solderability, and overall PCB manufacturability. Incorrect footprints can lead to assembly issues, poor electrical connections, and even component damage.
Types of PCB Footprints
There are several common types of PCB footprints, each designed to accommodate different component packages:
-
Through-Hole Footprints: These footprints are used for components with leads that pass through holes drilled in the PCB. Examples include DIP (Dual Inline Package) and TO (Transistor Outline) packages.
-
Surface Mount Footprints: These footprints are designed for components that are soldered directly onto the surface of the PCB. Common surface mount footprints include QFP (Quad Flat Package), QFN (Quad Flat No-lead), and BGA (Ball Grid Array).
-
Mixed Technology Footprints: Some components, such as connectors and switches, may have both through-hole and surface mount versions, requiring footprints that accommodate both mounting styles.
Importance of Accurate PCB Footprints
Creating accurate PCB footprints is essential for several reasons:
-
Manufacturing Compatibility: Footprints must adhere to the design rules and tolerances specified by the PCB manufacturer to ensure that the board can be successfully fabricated.
-
Component Fit: The footprint must match the dimensions and tolerances of the component to ensure proper fit and alignment during assembly.
-
Solderability: Properly designed footprints promote good solderability by providing adequate pad size, shape, and spacing for the component’s leads or pins.
-
Electrical Integrity: Footprints play a role in maintaining signal integrity and minimizing electromagnetic interference (EMI) by controlling factors such as pad size, copper pour, and ground plane connections.
PCB Footprint Design Considerations
When creating PCB footprints, several key factors must be considered to ensure compatibility, reliability, and manufacturability.
Component Dimensions and Tolerances
The first step in creating a footprint is to obtain accurate dimensional information for the target component. This data can be found in the component’s datasheet, which typically includes a mechanical drawing with dimensions, tolerances, and recommended footprint layout.
It is crucial to pay attention to the tolerances specified in the datasheet, as these account for variations in component manufacturing and ensure proper fit. When designing the footprint, the pad sizes and spacings should be chosen to accommodate the worst-case scenario within the given tolerances.
Pad Size and Shape
Pad size and shape play a significant role in footprint design. Pads must be large enough to provide sufficient area for soldering and to accommodate any variations in component placement during assembly. However, pads that are too large can lead to issues such as bridging (unwanted connection between adjacent pads) or reduced space for routing traces.
The pad shape is also important, particularly for surface mount components. Common pad shapes include rectangular, rounded rectangular, and oval. The choice of pad shape can impact solderability, as well as the overall footprint size and routing options.
Solder Mask and Paste Openings
Solder mask is a polymer coating applied to the PCB surface that protects the copper traces and prevents accidental short circuits. Openings in the solder mask, known as solder mask openings (SMOs), expose the pads for soldering.
When designing a footprint, it is essential to specify the appropriate solder mask openings. The openings should be slightly larger than the pads to accommodate manufacturing tolerances and to ensure that the solder mask does not encroach on the solderable area.
In addition to solder mask openings, solder paste openings (SPOs) are used for surface mount components. These openings in the solder paste stencil define the area where solder paste will be applied during the assembly process. SPOs are typically smaller than the pads to prevent solder paste bridging and to control the amount of paste deposited.
Courtyard and Keepout Areas
The courtyard is a virtual boundary around the component footprint that defines the minimum clearance required for placement and assembly. It is essential to include a courtyard in the footprint design to ensure that components are not placed too close together, which could lead to assembly issues or electrical interference.
Keepout areas are regions within the footprint where other components, traces, or copper pours are not allowed. These areas are used to maintain electrical clearance, prevent mechanical interference, or to accommodate component-specific requirements such as heat dissipation or shielding.
Silkscreen and Reference Designators
Silkscreen is a printed layer on the PCB surface that provides visual information for component placement, orientation, and identification. When creating a footprint, it is important to include silkscreen markings that clearly indicate the component’s outline, pin 1 location, and any other relevant information.
Reference designators are alphanumeric identifiers assigned to each component on the PCB. These designators are typically included in the silkscreen layer and are used to match components to their corresponding footprints during assembly. The footprint should include a placeholder for the reference designator, usually located near the component outline.
PCB Footprint Creation Tools and Methods
There are several tools and methods available for creating PCB footprints, ranging from manual layout to automated generation using specialized software.
PCB Design Software
Most PCB design software packages, such as Altium Designer, KiCad, and Eagle, include footprint creation tools. These tools typically provide a graphical interface for defining pad sizes, shapes, and spacings, as well as options for adding silkscreen, solder mask, and other layers.
When using PCB design software to create footprints, it is essential to follow the software’s specific guidelines and best practices. This includes setting up the appropriate grid and units, defining layer stackups, and adhering to the software’s naming conventions and library management systems.
IPC-7351 Standard and Calculators
The IPC-7351 standard, developed by the Association Connecting Electronics Industries (IPC), provides guidelines and recommendations for the design and creation of PCB footprints. This standard covers a wide range of component types and packages, and includes formulas for calculating pad sizes, spacings, and other footprint dimensions.
Many PCB design software packages include built-in IPC-7351 calculators that automatically generate footprints based on the standard’s guidelines. These calculators simplify the footprint creation process and help ensure consistency and compliance with industry best practices.
Footprint Libraries and Online Resources
There are numerous online resources and libraries that offer pre-designed PCB footprints for a wide range of components. These resources can save significant time and effort, as they eliminate the need to create footprints from scratch.
However, it is important to exercise caution when using third-party footprints. Always verify that the footprint dimensions and tolerances match the specific component being used, and ensure that the footprint adheres to the PCB manufacturer’s design rules and requirements.
Some popular online footprint resources include:
-
SnapEDA: A comprehensive library of PCB footprints, symbols, and 3D models, with support for multiple PCB design software packages.
-
PCB Libraries: A collection of free, open-source PCB footprint and symbol libraries for various PCB design tools.
-
Component Manufacturer Websites: Many component manufacturers provide recommended footprints and PCB design resources on their websites.
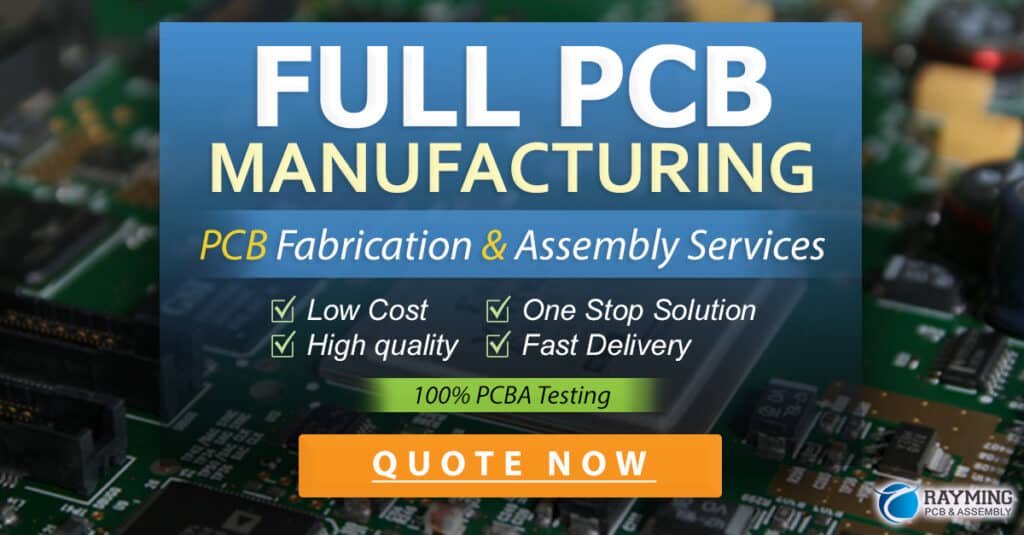
PCB Footprint Verification and Testing
Once a PCB footprint has been created, it is crucial to verify its accuracy and test its compatibility with the target component and manufacturing process.
Footprint Verification Checklist
Use the following checklist to verify the accuracy and completeness of a PCB footprint:
-
Dimensions: Ensure that pad sizes, spacings, and overall footprint dimensions match the component datasheet and tolerances.
-
Solder Mask and Paste Openings: Verify that solder mask and paste openings are correctly sized and positioned relative to the pads.
-
Courtyard and Keepout Areas: Check that the footprint includes appropriate courtyard and keepout areas, and that these areas do not interfere with other components or routing.
-
Silkscreen and Reference Designators: Confirm that the footprint includes clear and accurate silkscreen markings and reference designator placeholders.
-
Layer Assignments: Ensure that all footprint elements are assigned to the correct PCB layers (e.g., copper, silkscreen, solder mask).
Manufacturing and Assembly Testing
Before finalizing a PCB footprint, it is recommended to test its compatibility with the actual manufacturing and assembly processes. This can be done through several methods:
-
3D Modeling: Many PCB design software packages include 3D modeling capabilities that allow you to visualize the footprint and component in a virtual assembly. This can help identify potential issues with component fit, clearance, or orientation.
-
Prototype Fabrication: Fabricating a small batch of prototype PCBs with the new footprint can provide valuable insights into the footprint’s manufacturability and solderability. This allows for any necessary adjustments to be made before committing to a full production run.
-
Assembly Testing: Conducting assembly tests with the actual components can reveal any issues with component fit, solder paste application, or reflow soldering. This can be done using manual assembly methods or automated pick-and-place equipment, depending on the available resources and production requirements.
Frequently Asked Questions (FAQ)
-
What is the difference between a PCB footprint and a symbol?
A PCB footprint defines the physical arrangement of pads and other features on the PCB that correspond to a specific component. A symbol, on the other hand, is a graphical representation of the component used in schematic diagrams. The symbol defines the component’s electrical connections and functions, while the footprint defines its physical mounting and soldering requirements. -
Can I use the same footprint for different components?
In general, each component requires a specific footprint that matches its dimensions, pin arrangement, and mounting style. However, some components with similar packages and pin configurations may share a common footprint. It is essential to always verify the compatibility of a footprint with the specific component being used. -
What should I do if I can’t find a footprint for a specific component?
If a footprint is not readily available for a specific component, you have several options:
a. Create the footprint from scratch using the component datasheet and PCB design software.
b. Search for a similar component with an existing footprint and modify it to match the specific component’s requirements.
c. Contact the component manufacturer or distributor for assistance in obtaining or creating the footprint. -
How do I ensure that my PCB footprints are compatible with my manufacturer’s requirements?
To ensure compatibility with your PCB manufacturer’s requirements, follow these steps:
a. Obtain and review the manufacturer’s design rules and guidelines, which specify requirements for pad sizes, spacings, solder mask openings, and other footprint features.
b. Use the manufacturer’s recommended footprint creation tools or templates, if available.
c. Communicate with the manufacturer to clarify any specific requirements or constraints for your project.
d. Request a design review or manufacturability assessment from the manufacturer before finalizing your PCB design. -
What are some common mistakes to avoid when creating PCB footprints?
Some common mistakes to avoid when creating PCB footprints include:
a. Failing to account for component tolerances and variations in the footprint dimensions.
b. Neglecting to include appropriate solder mask and paste openings, or making them too small or too large.
c. Omitting or incorrectly placing silkscreen markings and reference designators.
d. Not adhering to the manufacturer’s design rules and guidelines for pad sizes, spacings, and other features.
e. Using incorrect or inconsistent units and grid settings in the PCB design software.
Conclusion
Creating accurate and reliable PCB footprints is a critical aspect of PCB design and manufacturing. By understanding the key considerations, tools, and methods involved in footprint creation, designers can ensure that their PCBs are compatible, manufacturable, and meet the required performance and reliability standards.
When creating PCB footprints, it is essential to start with accurate component data, follow industry standards and best practices, and use appropriate tools and resources. Designers should also prioritize footprint verification and testing to identify and address any issues before committing to production.
By following the guidelines and recommendations outlined in this article, PCB designers can streamline the footprint creation process, minimize design errors, and ultimately achieve successful PCB fabrication and assembly.
PCB Footprint Type | Characteristics | Example Components |
---|---|---|
Through-Hole | Pads with holes for component leads | DIP ICs, TO-220 packages, connectors |
Surface Mount | Pads on the PCB surface for component soldering | QFP ICs, chip resistors, capacitors |
Mixed Technology | Combines through-hole and surface mount pads | Connectors, switches, displays |
BGA | Grid of solder balls underneath the component for high-density wiring | Microprocessors, FPGAs, memory modules |
QFN | Leadless package with exposed thermal pad for improved heat dissipation | Voltage regulators, RF components |
Footprint Feature | Purpose | Considerations |
---|---|---|
Pad Size and Shape | Provides surface area for soldering and component attachment | Ensure compatibility with component and soldering process |
Solder Mask Opening | Exposes pads for soldering while protecting surrounding areas | Typically larger than the pad to allow for tolerances |
Solder Paste Opening | Defines the area for solder paste application in surface mount assembly | Usually smaller than the pad to control paste volume |
Courtyard | Defines the minimum clearance area around the component | Prevents interference with adjacent components and features |
Silkscreen | Provides visual identification and orientation markings | Ensure clarity and legibility without obscuring pads or openings |
By understanding and properly implementing these footprint types and features, PCB designers can create robust, manufacturable designs that meet the requirements of their specific components and applications.
Leave a Reply