What is a Ground Plane in PCB Design?
A ground plane is a large area of copper on a printed circuit board (PCB) that is connected to the ground (GND) of the circuit. It serves as a low-impedance return path for electric currents and helps to reduce electromagnetic interference (EMI) and improve signal integrity. In multi-layer PCBs, the ground plane is usually a dedicated layer, while in single-layer PCBs, it is often a large area of copper on the same side as the components.
Benefits of Using a Ground Plane in PCB Design
- Reduces EMI: A ground plane helps to reduce electromagnetic interference by providing a low-impedance return path for high-frequency currents.
- Improves signal integrity: By reducing the inductance and resistance of the return path, a ground plane helps to maintain the integrity of signals traveling through the PCB.
- Enhances thermal dissipation: The large area of copper in a ground plane helps to dissipate heat generated by components on the PCB.
- Simplifies routing: With a dedicated ground plane, routing of signals becomes simpler, as the return path is always readily available.
Designing a Ground Plane in Your PCB
Determine the Size and Shape of the Ground Plane
The size and shape of the ground plane depend on the size of your PCB and the placement of components. In general, the ground plane should cover as much of the PCB area as possible, while leaving room for signal traces and components.
PCB Size | Ground Plane Coverage |
---|---|
Small (< 50 cm²) | 70-80% |
Medium (50-100 cm²) | 60-70% |
Large (> 100 cm²) | 50-60% |
Connect Components to the Ground Plane
All components that require a ground connection should be connected to the ground plane using vias or through-hole connections. It is important to ensure that the ground connections are low-impedance and can handle the expected current.
Via Size and Spacing
The size and spacing of vias used to connect components to the ground plane should be chosen based on the current requirements and the manufacturing capabilities of your PCB fabricator.
Current | Via Diameter | Via Spacing |
---|---|---|
< 1 A | 0.3-0.5 mm | 1-2 mm |
1-3 A | 0.5-0.8 mm | 2-3 mm |
> 3 A | 0.8-1.2 mm | 3-4 mm |
Split the Ground Plane When Necessary
In some cases, it may be necessary to split the ground plane to isolate certain parts of the circuit. This is often done to prevent noise from one part of the circuit from affecting another part. When splitting the ground plane, it is important to ensure that the separate sections are still connected to the main ground at a single point to avoid creating ground loops.
Use Ground Plane Cutouts for High-Speed Signals
For high-speed signals, such as those found in RF and microwave circuits, it may be necessary to create cutouts in the ground plane to avoid coupling between the signal and the ground. These cutouts, also known as antipads, should be sized appropriately based on the signal frequency and the dielectric properties of the PCB material.
Antipad Size vs. Signal Frequency
Signal Frequency | Antipad Size |
---|---|
< 1 GHz | 0.5-1 mm |
1-5 GHz | 1-2 mm |
> 5 GHz | 2-3 mm |
Analyzing Your Ground Plane Design
Once you have designed your ground plane, it is important to analyze it to ensure that it meets your performance requirements. This can be done using simulation tools or by building a prototype and testing it.
Simulation Tools for Ground Plane Analysis
There are several simulation tools available for analyzing ground planes in PCB designs:
- Ansys SIwave: A powerful tool for simulating and analyzing power delivery networks (PDNs) and signal integrity in PCBs.
- Cadence Sigrity: Offers a range of tools for simulating and analyzing PDNs, signal integrity, and EMI in PCBs.
- Mentor Graphics HyperLynx: Provides tools for simulating and analyzing signal integrity, power integrity, and EMI in PCBs.
Building and Testing a Prototype
After simulating your ground plane design, it is recommended to build a prototype and test it to validate the simulation results. This can help identify any issues that may have been missed during the design and simulation phases.
Key Parameters to Test
- Ground plane impedance: Measure the impedance of the ground plane using a network analyzer or impedance analyzer to ensure that it meets your target values.
- Signal integrity: Test the integrity of signals passing through the PCB using an oscilloscope or signal analyzer to ensure that they are not being distorted by the ground plane.
- EMI: Measure the electromagnetic emissions from the PCB using an EMI receiver or spectrum analyzer to ensure that they are within acceptable limits.
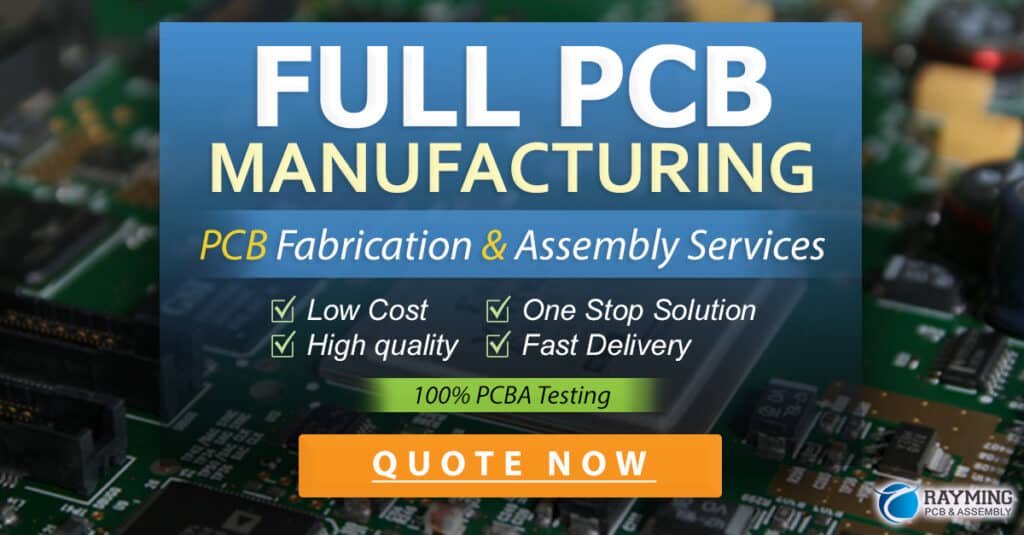
Common Pitfalls and Best Practices
Pitfalls to Avoid
- Insufficient ground plane coverage: Not providing enough ground plane coverage can lead to higher ground impedance and reduced performance.
- Improper via placement: Placing vias too far apart or using vias that are too small can increase the impedance of the ground connection and degrade performance.
- Creating ground loops: Splitting the ground plane incorrectly can create ground loops, which can lead to noise and signal integrity issues.
Best Practices
- Maximize ground plane coverage: Aim to cover as much of the PCB area as possible with the ground plane, while leaving room for signal traces and components.
- Use appropriate via sizes and spacing: Choose via sizes and spacing based on the current requirements and manufacturing capabilities of your PCB fabricator.
- Simulate and test your design: Always simulate your ground plane design and build a prototype to validate the simulation results before finalizing your PCB layout.
FAQ
-
Q: What is the ideal ground plane coverage for a small PCB?
A: For a small PCB (less than 50 cm²), aim for 70-80% ground plane coverage. -
Q: How do I determine the appropriate via size for connecting components to the ground plane?
A: The via size should be chosen based on the current requirements of the components. For currents less than 1 A, use vias with a diameter of 0.3-0.5 mm. For currents between 1-3 A, use vias with a diameter of 0.5-0.8 mm. For currents greater than 3 A, use vias with a diameter of 0.8-1.2 mm. -
Q: When should I split the ground plane in my PCB design?
A: You should split the ground plane when you need to isolate certain parts of the circuit to prevent noise from one part from affecting another part. However, ensure that the separate sections are still connected to the main ground at a single point to avoid creating ground loops. -
Q: What are antipads, and when should I use them in my ground plane design?
A: Antipads are cutouts in the ground plane used to avoid coupling between high-speed signals and the ground. They should be used for signals with frequencies above 1 GHz, with the size of the antipad increasing as the signal frequency increases. -
Q: What are some common pitfalls to avoid when designing a ground plane in my PCB?
A: Some common pitfalls include insufficient ground plane coverage, improper via placement, and creating ground loops. To avoid these issues, maximize ground plane coverage, use appropriate via sizes and spacing, and carefully consider any splits in the ground plane to prevent ground loops.
Leave a Reply