Introduction to Fabrication and Assembly Drawings
Fabrication and assembly drawings are critical outputs from the PCB design process that communicate all the necessary information to physically manufacture the printed circuit board. Fabrication drawings (also known as fab drawings or fab prints) specify the physical properties and materials needed to fabricate the bare PCB. This includes the board outline, layer stackup, drill holes and sizes, special instructions, and other manufacturing details.
Assembly drawings document how to assemble and solder the components onto the fabricated PCB. They show component placement locations, reference designators, polarity indicators, and any special assembly instructions.
Altium Designer, a popular PCB design tool, has robust capabilities for generating professional fabrication and assembly drawings to include in the manufacturing data package that gets sent to the PCB fab and assembly shop. Let’s take an in-depth look at how to set up and create these drawings in Altium Designer.
Setting Up the PCB Project for Manufacturing Outputs
Before generating the fabrication and assembly drawings, it’s important to have the PCB project set up properly. This involves specifying the board shape, layer stackup, design rules, and component properties.
Defining the Board Shape and Mechanical Layers
The first step is to define the physical outline and shape of the PCB using the Board Shape object in Altium Designer. This will appear in the fab drawings. In addition to the outline, mechanical layers should be added for any holes, cutouts, keepouts, or other features. Mechanical layers can be used to communicate info to the manufacturer.
Configuring the Layer Stackup
The layer stackup specifies the number of copper and dielectric layers, their order, materials, and thicknesses. This is critical info for the fab house to have. In Altium Designer, the layer stackup is defined in the Layer Stack Manager. Common stackups are:
Layers | Stackup |
---|---|
2 | Top copper, dielectric core, bottom copper |
4 | Top copper, prepreg, core, prepreg, bottom copper |
6 | Top copper, prepreg, core, core, prepreg, bottom copper |
The fab drawing should include a diagram of the layer stackup.
Setting Up Design Rules
Design rules specify the manufacturing capabilities and requirements, such as minimum trace width, minimum clearances, hole sizes, etc. These are entered in the Design Rule Editor in Altium Designer. The Electrical Rules Check (ERC) and Design Rules Check (DRC) can then be run to verify the design meets the rules before generating manufacturing files.
Defining Component Properties and Parameters
For the assembly drawing, detailed component information needs to be defined in the schematic and/or PCB library. This includes:
- Reference designator (e.g. R1, C5, U3)
- Value (e.g. 4.7k, 100nF, ATMEGA328P)
- Footprint name
- Comment or description
Additionally, the component orientation, placement type (SMD/through-hole), and height should be specified. All this info will appear in the bill of materials and assembly drawings.
Generating Fabrication Drawings
With the project set up, the fab drawings can be generated. Altium has templates for this under the “File -> New -> PCB Fabrication Outputs” menu.
PCB Printouts and Drill Drawings
The basic fab drawing views needed are the top and bottom layers, solder mask layers, silkscreen layers, drill drawing, and drill guides/spot charts.
Printouts of each individual copper layer can be made by selecting the layer in the Layers panel and going to “File -> Print.” In the print dialog, select the “Color” option and click “OK.” Repeat for each necessary layer.
For the drill drawing, go to “File -> New -> PCB Fabrication Outputs -> Drill Drawing.” This will create a drawing showing the locations and sizes of the drills holes. The default template can be edited to add more information like the units, tolerances, numbering, symbols, etc.
Drill guides are used by the fab house to verify hole sizes. To create a drill guide, go to “File -> New -> PCB Fabrication Outputs -> NC Drill Report.” Select “Drill Symbol Legend” and click “OK.” This generates a printable guide of the drill symbols and sizes.
Dimensions, Notes, and Tables
The fab drawing should include key dimensions of the board outline, holes, and other features. Use the dimension objects in Altium to add dimensions lines and measurements.
Any special notes, instructions, stackup table, revision notes, logos, etc. can be added to the drawing sheet frame using text and table objects. Notes may include PCB material type, soldermask color, surface finish, standards needed (e.g. IPC 6012 Class 2), etc.
A drill table listing the hole sizes, number of hits, and plated/non-plated status should also be included. To add a drill table, go to “File -> New -> PCB Fabrication Outputs -> NC Drill Table.” Select the template and click “OK” to add it to the drawing.
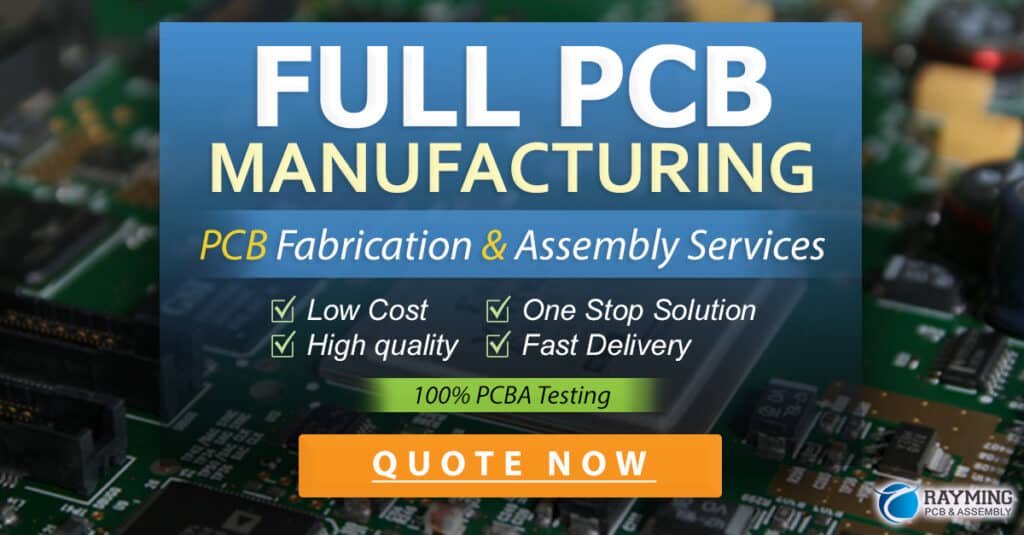
Generating Assembly Drawings
The assembly drawing shows the component locations and reference designators for assembly. It also usually includes a bill of materials table.
Component Placement and Overlay
To create the assembly drawing views, go to “File -> New -> PCB Assembly Outputs” and select “Component Locater – Top” or “Component Locater – Bottom.” This generates a drawing of the component bodies and reference designators.
For a more realistic view with component bodies, you can export a 3D view of the PCB by going to “File -> Export -> 3D -> 3D PDF.”
Bill of Materials
The bill of materials (BOM) is a table listing all the components used on the PCB along with quantities and part numbers. To generate a BOM, go to “File -> New -> BOM.” Select the template and options (Excel, CSV, text, etc.) and click “OK.” The BOM will be created using the component properties from the schematic and PCB library.
The BOM can be edited and formatted as needed. It’s also good practice to include the BOM as a separate file along with the fabrication and assembly drawings in the manufacturing package.
Design for Manufacturing Checks
Before sending the fabrication and assembly drawings and files to the manufacturer, it’s crucial to do design for manufacturing (DFM) checks. These ensure the PCB is manufacturable and meets the fab and assembly houses’ capabilities.
Common DFM checks include:
- Minimum trace width and clearance spacings
- Minimum drill hole sizes
- Soldermask and silkscreen clearances
- Copper-to-board edge clearance
- Solder bridge and tombstoning analysis
- Acid trap analysis
- Soldermask slivers and dams
Altium Designer includes a DFM check utility under “Reports -> DFM Checks.” It can check against a set of manufacturing rules and guidelines. Any violations will be flagged for correction before proceeding.
Reviewing and Finalizing
With the fab and assembly drawings generated, carefully review them for accuracy and completeness. Have other team members check them over as well.
Some items to double-check:
- Board shape and dimensions are correct
- Layer stackup matches the design intent
- Drills holes and sizes are correct
- All components are accounted for
- Reference designators are correct
- Special notes and instructions are present
- Title block is complete with revision, date, etc.
Once reviewed and verified, the drawings can be saved, printed, and sent to the manufacturer along with the other manufacturing files like Gerber files, NC drill files, pick & place, etc.
Frequently Asked Questions
What’s the difference between fabrication and assembly drawings?
Fabrication drawings communicate how to fabricate and manufacture the bare PCB, including materials, stackup, copper weights, drill holes, and dimensions. Assembly drawings show how to assemble the components onto the fabricated PCB, including component locations and bill of materials.
What file formats should I use for fabrication and assembly drawings?
The most common formats are PDF and DXF/DWG. Gerber (RS-274X) is the standard for sending copper artworks and drill files to fabrication. Check with your manufacturer on their preferred file formats.
Do I need to include the Gerber and drill files with the drawings?
Yes, fabrication and assembly drawings are a visual aid and quick reference, but the manufacturer will still need the Gerber and NC drill files to physically produce the PCB. Include those along with the pick & place file and drawings in the manufacturing package.
How do I communicate PCB stackup and material requirements?
The fabrication drawing should have a stackup diagram and table showing the layer order, materials, and thicknesses. Special material callouts can be put in a note, for example: “FR-4 Tg135, Mid-Tg, lead-free compatible.”
What if I need to make changes to the drawings after sending them to the manufacturer?
If you discover an error or need to make a change, contact the manufacturer immediately. They may be able to accommodate the change depending on how far along they are. You’ll need to update the drawings, increment the revision, and resend the files. Emphasize what was changed. Consider using engineering change orders (ECO) to document and track changes.
Conclusion
Creating clear, accurate, and complete fabrication and assembly drawings is essential for successfully manufacturing PCBs. Altium Designer provides the tools and features to generate these drawings and outputs efficiently.
By taking the time to properly set up the PCB project, create the drawings, and review them thoroughly, you can minimize the risk of errors and miscommunication with the manufacturer. This helps ensure a smooth handoff to fabrication and assembly, and ultimately a successful product build.
Leave a Reply