What is a Board Fabrication Panel?
A board fabrication panel, also known as a PCB panel or a printed circuit board panel, is a larger board that contains multiple identical printed circuit boards (PCBs) arranged in a specific layout. The purpose of using a fabrication panel is to optimize the manufacturing process, reduce costs, and improve efficiency.
When designing a PCB, engineers often create a single board layout that meets the required specifications. However, producing individual boards can be time-consuming and expensive, especially for large-scale production. By arranging multiple copies of the same PCB design on a larger panel, manufacturers can produce several boards simultaneously, reducing the overall production time and cost.
Advantages of Using Board Fabrication Panels
- Cost reduction: Producing multiple boards on a single panel reduces the cost per board, as the setup time and material costs are shared among the boards.
- Increased efficiency: Fabricating several boards at once minimizes the handling time and streamlines the manufacturing process.
- Consistent quality: Since all boards on a panel undergo the same manufacturing process, the quality and characteristics of each board are more consistent.
- Simplified assembly: Having multiple boards on a panel allows for easier assembly and soldering of components, as the boards are held securely in place.
Designing a Board Fabrication Panel
Panel Size and Material
When creating a board fabrication panel, the first step is to determine the appropriate panel size and material. The panel size depends on several factors, including:
- The dimensions of the individual PCBs
- The number of PCBs to be included on the panel
- The manufacturing capabilities of the PCB fabricator
- The assembly requirements
Standard panel sizes vary depending on the manufacturer and the specific production line. Common panel sizes include:
Panel Size (mm) | Panel Size (inches) |
---|---|
229 x 305 | 9 x 12 |
305 x 457 | 12 x 18 |
457 x 610 | 18 x 24 |
610 x 914 | 24 x 36 |
The choice of material for the fabrication panel depends on the PCB’s intended application, the required electrical and mechanical properties, and the manufacturing process. The most common materials used for PCB fabrication panels are:
- FR-4: A flame-retardant, glass-reinforced epoxy laminate that is widely used for general-purpose PCBs.
- Aluminum: Used for PCBs that require better thermal dissipation or for high-power applications.
- Polyimide: A flexible, high-temperature material used for flexible PCBs or applications that require high thermal stability.
Panelization Layout
Once the panel size and material have been selected, the next step is to create the panelization layout. This involves arranging the individual PCBs on the panel in a way that optimizes material usage and ensures proper spacing for the manufacturing process.
When designing the panelization layout, consider the following factors:
- Board orientation: Arrange the boards to minimize waste material and ensure proper orientation for assembly.
- Spacing between boards: Provide adequate spacing between individual boards to allow for the manufacturing tolerances and to prevent damage during the depaneling process.
- Tooling holes and fiducials: Include tooling holes and fiducial marks on the panel to aid in the alignment and registration of the boards during manufacturing and assembly.
- Breakaway tabs or mouse bites: Incorporate breakaway tabs or mouse bites between the individual boards to allow for easy separation (depaneling) after the manufacturing process.
Here’s an example of a panelization layout:
+-------------------------------------------------------+
| +-------+ +-------+ +-------+ +-------+ +-----+|
| | | | | | | | | | ||
| | PCB | | PCB | | PCB | | PCB | | ||
| | 1 | | 2 | | 3 | | 4 | | ||
| | | | | | | | | | ||
| +-------+ +-------+ +-------+ +-------+ | ||
| | ||
| +-------+ +-------+ +-------+ +-------+ | ||
| | | | | | | | | | ||
| | PCB | | PCB | | PCB | | PCB | | ||
| | 5 | | 6 | | 7 | | 8 | | ||
| | | | | | | | | +-----+|
| +-------+ +-------+ +-------+ +-------+ |
+-------------------------------------------------------+
In this example, eight identical PCBs are arranged in a 2×4 grid on the fabrication panel. The spacing between the boards allows for manufacturing tolerances and depaneling, while the tooling holes (represented by the circles) and fiducials (not shown) aid in the alignment and registration of the panel during production.
Panelization Techniques
There are several techniques used to create board fabrication panels, depending on the specific requirements of the project and the capabilities of the PCB manufacturer. Some common panelization techniques include:
-
Tab routing: This method involves creating breakaway tabs or mouse bites between the individual boards using a routing tool. The tabs hold the boards in place during manufacturing and can be easily broken off after the process is complete.
-
V-scoring: In this technique, V-shaped grooves are cut partially through the panel material between the boards. This weakens the material, allowing for easy separation of the individual boards after manufacturing.
-
Perforating: Similar to V-scoring, perforating involves creating a series of small holes or slots between the boards to weaken the panel material and allow for easy separation.
-
Snap-apart: This method uses a combination of perforations and V-scores to create a snap-apart panel. The individual boards can be separated by applying pressure along the perforated lines.
The choice of panelization technique depends on factors such as the thickness of the PCB, the required board shape, and the depaneling method to be used during assembly.
Manufacturing Process
Once the board fabrication panel has been designed and the panelization technique has been selected, the manufacturing process can begin. The typical steps involved in fabricating a PCB panel include:
-
Material preparation: The chosen substrate material (e.g., FR-4, aluminum, or polyimide) is cut to the desired panel size.
-
Copper lamination: A thin layer of copper is laminated onto the substrate material using heat and pressure.
-
Drilling: Holes are drilled through the panel to accommodate through-hole components and vias.
-
Patterning: The copper layer is patterned using a photolithographic process to create the desired circuit traces and pads.
-
Etching: The unwanted copper is removed using a chemical etching process, leaving only the desired circuit pattern.
-
Soldermask application: A protective soldermask layer is applied to the panel, covering the areas where soldering is not required.
-
Silkscreen printing: Text, logos, and component designators are printed onto the panel using a silkscreen process.
-
Surface finish: A surface finish, such as HASL (Hot Air Solder Leveling), ENIG (Electroless Nickel Immersion Gold), or OSP (Organic Solderability Preservative), is applied to the exposed copper to improve solderability and protect the copper from oxidation.
-
Electrical testing: The fabricated panel undergoes electrical testing to ensure that all connections are properly made and that there are no short circuits or open connections.
-
Depaneling: The individual PCBs are separated from the panel using the chosen panelization technique (e.g., tab routing, V-scoring, or perforating).
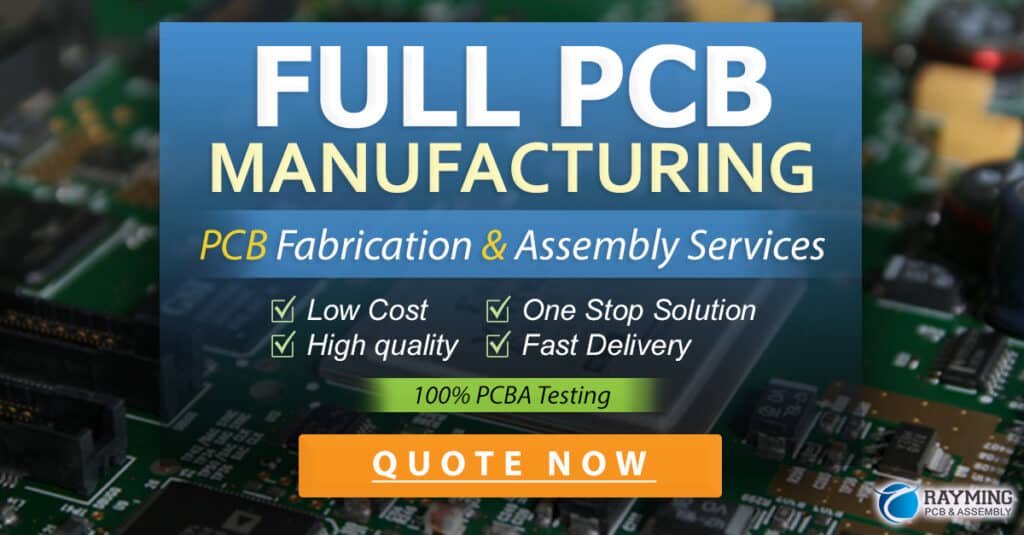
Assembly Considerations
When designing a board fabrication panel, it is essential to consider the assembly process that will follow. The panelization layout and technique should be chosen to facilitate the assembly of components onto the individual PCBs.
Some key assembly considerations include:
-
Component placement: Ensure that the panelization layout allows for proper component placement and that there is sufficient clearance between components and the board edges.
-
Soldering: Consider the soldering method to be used (e.g., wave soldering, reflow soldering, or hand soldering) and ensure that the panel design is compatible with the chosen method.
-
Tooling: The panel design should accommodate any necessary tooling or fixtures required for the assembly process, such as pick-and-place machines or solder pallets.
-
Depaneling: Choose a depaneling method that minimizes stress on the assembled components and ensures that the individual boards remain intact after separation from the panel.
Best Practices for Board Fabrication Panel Design
To ensure the success of your board fabrication panel design, consider the following best practices:
-
Communicate with your PCB manufacturer: Discuss your project requirements and constraints with your PCB manufacturer early in the design process to ensure that your panel design is compatible with their manufacturing capabilities.
-
Use standard panel sizes: Whenever possible, use standard panel sizes to minimize costs and lead times. Custom panel sizes may be necessary for some projects but can increase costs and production time.
-
Optimize material usage: Arrange the individual PCBs on the panel to minimize waste material and maximize the number of boards per panel.
-
Allow for manufacturing tolerances: Provide adequate spacing between boards and components to account for manufacturing tolerances and to prevent damage during the depaneling process.
-
Include fiducials and tooling holes: Incorporate fiducial marks and tooling holes into your panel design to aid in the alignment and registration of the boards during manufacturing and assembly.
-
Consider the assembly process: Design your panel with the assembly process in mind, ensuring that the panelization layout and technique are compatible with the chosen soldering method and assembly equipment.
-
Test your design: Before committing to a full production run, fabricate a small batch of panels to test your design and verify that it meets your requirements.
Frequently Asked Questions (FAQ)
-
Q: What is the purpose of using a board fabrication panel?
A: The purpose of using a board fabrication panel is to optimize the manufacturing process, reduce costs, and improve efficiency by producing multiple identical PCBs simultaneously on a single larger board. -
Q: What factors should I consider when choosing a panel size?
A: When choosing a panel size, consider the dimensions of the individual PCBs, the number of PCBs to be included on the panel, the manufacturing capabilities of the PCB fabricator, and the assembly requirements. -
Q: What are some common panelization techniques?
A: Common panelization techniques include tab routing, V-scoring, perforating, and snap-apart methods. The choice of technique depends on factors such as PCB thickness, board shape, and the depaneling method to be used during assembly. -
Q: How can I optimize material usage when designing a board fabrication panel?
A: To optimize material usage, arrange the individual PCBs on the panel to minimize waste material and maximize the number of boards per panel. Consider using standard panel sizes whenever possible to reduce costs and lead times. -
Q: Why is it important to consider the assembly process when designing a board fabrication panel?
A: Considering the assembly process when designing a board fabrication panel is important to ensure that the panelization layout and technique are compatible with the chosen soldering method and assembly equipment. This helps to minimize stress on the assembled components and ensures that the individual boards remain intact after depaneling.
In conclusion, creating a board fabrication panel is an essential step in the PCB manufacturing process, allowing for the efficient and cost-effective production of multiple identical boards. By carefully considering factors such as panel size, material, panelization layout, and assembly requirements, engineers can design panels that optimize the manufacturing process and ensure the success of their projects.
Leave a Reply