Understanding 3D Component Bodies
What are 3D Component Bodies?
3D component bodies are digital representations of electronic components that accurately depict their physical dimensions, shape, and appearance. These models are used in EDA software to visualize how components will look and fit on a printed circuit board (PCB) during the design process.
The Importance of 3D Component Bodies
Incorporating 3D component bodies into your PCB design workflow offers several benefits:
-
Improved Visualization: 3D models provide a realistic representation of components, allowing designers to better understand how they will appear on the finished PCB.
-
Enhanced Collaboration: Sharing 3D models with colleagues, clients, or manufacturers facilitates clearer communication and reduces the likelihood of misinterpretations.
-
Collision Detection: EDA software can use 3D component bodies to detect potential collisions between components, helping to identify and resolve issues before manufacturing.
-
Better Documentation: Including 3D models in design documentation provides a more comprehensive view of the PCB, aiding in assembly and maintenance processes.
Creating 3D Component Bodies
Step 1: Gather Component Information
To create an accurate 3D component body, you’ll need to collect the following information:
- Physical dimensions (length, width, height)
- Package type (e.g., SOIC, QFP, BGA)
- Lead or pin configuration
- Material properties (color, texture)
This information can typically be found in the component’s datasheet or by measuring a physical sample.
Step 2: Choose a 3D Modeling Tool
There are several software options available for creating 3D component bodies, including:
- Autodesk Fusion 360
- SolidWorks
- SketchUp
- FreeCAD
Choose a tool that fits your budget, skill level, and integrates well with your EDA software.
Step 3: Create the Basic Shape
Begin by creating the basic shape of the component body using the dimensions gathered in Step 1. Most 3D modeling tools offer primitive shapes like cubes, cylinders, and spheres that can be combined and modified to form the desired shape.
Step 4: Add Details
Once the basic shape is created, add details such as leads, pins, or surface features. Pay close attention to the component’s datasheet to ensure accuracy.
Step 5: Apply Material Properties
Assign material properties to the 3D model to give it a realistic appearance. This may include color, texture, and reflectivity. Some 3D modeling tools offer libraries of common materials, while others allow you to create custom materials.
Step 6: Export the Model
Export the completed 3D component body in a format compatible with your EDA software. Common formats include STEP, IGES, and OBJ.
Integrating 3D Component Bodies into a Footprint Library
What is a Footprint Library?
A footprint library is a collection of component footprints used in PCB design. Each footprint defines the copper pad layout and silkscreen outline for a specific component.
Adding 3D Models to Footprints
To integrate a 3D component body into a footprint library, follow these steps:
- Open your EDA software and navigate to the footprint library manager.
- Select the footprint for the component you wish to add a 3D model to.
- Import the 3D model file (e.g., STEP, IGES, OBJ) into the footprint properties.
- Align and scale the 3D model to match the footprint’s dimensions.
- Save the updated footprint library.
EDA Software | 3D Model Import Format |
---|---|
Altium Designer | STEP |
KiCad | STEP, IGES, OBJ |
Eagle | STEP |
OrCAD | STEP, IGES |
Best Practices for Footprint Library Management
- Keep footprint names consistent and descriptive
- Organize footprints into categories based on component type or manufacturer
- Regularly update and maintain footprint libraries to ensure accuracy
- Share footprint libraries with team members to maintain consistency across designs
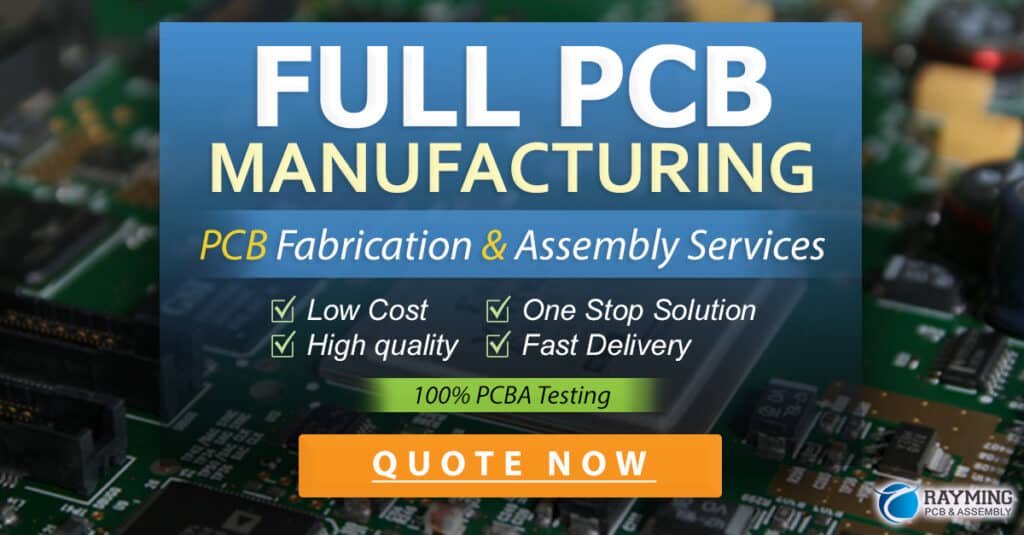
Advanced Techniques
Parametric Modeling
Parametric modeling involves creating 3D models with adjustable parameters, allowing you to quickly generate variations of a component body. This is particularly useful for families of components with similar shapes but different dimensions.
Photorealistic Rendering
Some 3D modeling tools offer photorealistic rendering capabilities, which can be used to create highly detailed and visually appealing images of your 3D component bodies. These renderings can be used in marketing materials, presentations, or design documentation.
Collision Detection and Clearance Checking
By integrating 3D component bodies into your EDA software, you can perform collision detection and clearance checking to ensure that components fit properly on the PCB and do not interfere with one another. This helps to catch potential issues early in the design process, reducing the risk of costly manufacturing errors.
Frequently Asked Questions (FAQ)
-
Can I use 3D models from component manufacturers in my designs?
Many component manufacturers provide 3D models of their products that can be used in your designs. However, it’s essential to check the licensing terms and ensure that you have permission to use the models in your specific application. -
How accurate do 3D component bodies need to be?
The accuracy of 3D component bodies depends on the purpose of the model. For visualization and general design purposes, a close approximation of the component’s shape and dimensions is usually sufficient. However, if the model will be used for collision detection or manufacturing purposes, a higher level of accuracy is required. -
Are there any online resources for pre-made 3D component bodies?
Yes, there are several online libraries and marketplaces where you can find pre-made 3D component bodies, such as: - GrabCAD
- 3D ContentCentral
- Digi-Key 3D Model Library
-
Ultra Librarian
-
How can I ensure compatibility between my 3D modeling tool and EDA software?
Most EDA software supports common 3D file formats like STEP, IGES, and OBJ. To ensure compatibility, check your EDA software’s documentation for supported file formats and export options from your 3D modeling tool. -
What if I don’t have access to a component’s exact dimensions?
If you don’t have access to a component’s exact dimensions, you can use a caliper or micrometer to measure a physical sample of the component. Alternatively, you can search for the component’s datasheet online, which often includes detailed dimensional information.
Conclusion
Creating 3D component bodies and integrating them into a footprint library is a valuable skill for any PCB designer. By following the steps and best practices outlined in this article, you can create accurate and visually appealing 3D models that enhance your design process and improve collaboration with colleagues and clients.
Remember to keep your footprint libraries organized, up-to-date, and consistent to ensure the best possible results in your PCB designs. With practice and attention to detail, you’ll be creating professional-quality 3D component bodies in no time.
Leave a Reply