Understanding Buck Voltage Converters
What is a Buck Voltage Converter?
A buck voltage converter, also known as a step-down converter, is a type of DC-DC converter that reduces the input voltage to a lower output voltage. It consists of a switch (usually a MOSFET), an inductor, a diode, and a capacitor. By controlling the duty cycle of the switch, the output voltage can be regulated to the desired level.
Operating Principles of Buck Converters
The basic operating principle of a buck converter involves two distinct phases:
- On-state: When the switch is closed, current flows from the input through the inductor, charging it up. The diode is reverse-biased during this phase.
- Off-state: When the switch is open, the inductor releases its stored energy through the diode, supplying current to the load and the output capacitor.
By varying the duty cycle (the ratio of on-time to the total switching period), the output voltage can be controlled. The relationship between the input voltage (Vin) and the output voltage (Vout) is given by:
Vout = D × Vin
where D is the duty cycle.
Designing a High Current Buck Voltage Controller
Key Components and Their Selection
- MOSFET: Choose a MOSFET with low on-resistance (RDS(on)) and high current handling capability to minimize conduction losses and ensure efficient operation at high currents.
- Inductor: Select an inductor with low DC resistance (DCR) and high saturation current rating to minimize losses and prevent saturation under high current conditions.
- Diode: Use a Schottky diode with low forward voltage drop and fast recovery time to reduce conduction losses and minimize switching losses.
- Capacitor: Choose a capacitor with low equivalent series resistance (ESR) and adequate ripple current rating to minimize output voltage ripple and ensure stable operation.
Determining Component Values
- Inductor value: The inductor value (L) can be calculated based on the desired ripple current (ΔIL) and the switching frequency (fs):
L = (Vout × (Vin – Vout)) / (ΔIL × fs × Vin)
- Capacitor value: The capacitor value (C) can be determined based on the desired output voltage ripple (ΔVout) and the inductor ripple current:
C = (ΔIL × D) / (8 × fs × ΔVout)
Control Techniques for High Current Buck Converters
- Current-mode control: This technique uses the inductor current as a feedback signal to control the duty cycle, providing inherent current limiting and improved transient response.
- Voltage-mode control: In this method, the output voltage is compared with a reference voltage, and the error signal is used to control the duty cycle. This technique is simpler to implement but may require additional compensation for stability.
Implementing a High Current Buck Voltage Controller
Schematic Design and PCB Layout Considerations
- Use a four-layer PCB with dedicated power and ground planes to minimize parasitic inductance and resistance.
- Place the MOSFET, diode, and inductor close together to minimize loop area and reduce electromagnetic interference (EMI).
- Use wide traces for high current paths to minimize resistance and improve thermal performance.
- Include appropriate decoupling capacitors near the MOSFET and the controller IC to reduce noise and ensure stable operation.
Thermal Management and Heat Dissipation
- Use a heat sink or thermal pad to dissipate heat from the MOSFET and diode, ensuring that their junction temperatures remain within safe limits.
- Consider using a temperature monitoring system to protect the components from overheating and ensure reliable operation.
Efficiency Optimization Techniques
- Use synchronous rectification by replacing the diode with a second MOSFET to reduce conduction losses and improve efficiency.
- Implement zero-voltage switching (ZVS) or zero-current switching (ZCS) techniques to minimize switching losses and increase efficiency at high frequencies.
- Optimize the dead-time between the switching transitions to minimize body diode conduction and reduce losses.
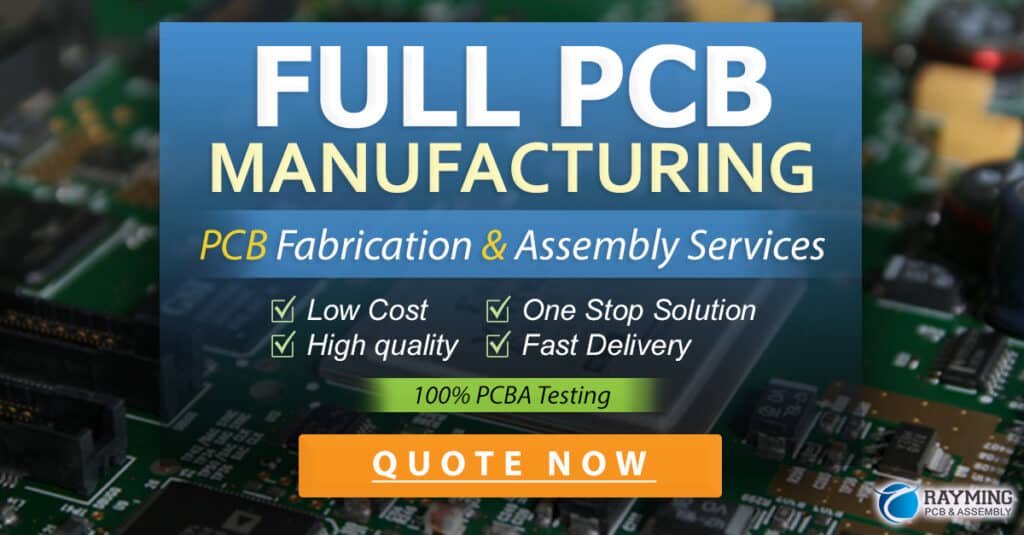
Testing and Verification
Performance Metrics and Measurement Techniques
- Efficiency: Measure the input and output power using precision voltage and current probes, and calculate the efficiency as the ratio of output power to input power.
- Output voltage ripple: Use an oscilloscope to measure the peak-to-peak output voltage ripple and ensure that it meets the design requirements.
- Load transient response: Apply a sudden load change and observe the output voltage response using an oscilloscope, verifying that the controller maintains a stable output voltage with minimal overshoot or undershoot.
Compliance with Industry Standards and Regulations
- Electromagnetic compatibility (EMC): Test the buck converter for conducted and radiated emissions, ensuring compliance with relevant EMC standards such as CISPR 22 or FCC Part 15.
- Safety: Ensure that the design meets applicable safety standards, such as UL 60950-1 or IEC 62368-1, by incorporating appropriate protection features and conducting necessary safety tests.
Real-World Applications and Case Studies
Battery Charging Systems
High current buck voltage controllers are widely used in battery charging systems for portable devices, electric vehicles, and energy storage systems. These controllers ensure efficient and safe charging by regulating the charging current and voltage according to the battery’s requirements.
Case Study: High-Power Lithium-Ion Battery Charger
A company designed a high-power lithium-ion battery charger using a high current buck voltage controller. The charger was capable of delivering up to 10A of charging current while maintaining a stable output voltage of 4.2V. The design incorporated current-mode control, synchronous rectification, and thermal management techniques to achieve high efficiency and reliability.
LED Drivers
High current buck voltage controllers are essential in LED lighting applications, particularly for high-power LED arrays used in automotive headlights, street lighting, and industrial illumination. These controllers provide constant current regulation to ensure uniform brightness and prevent thermal runaway.
Case Study: High-Brightness LED Driver for Automotive Headlights
An automotive manufacturer implemented a high current buck voltage controller to drive high-brightness LED headlights. The controller was designed to deliver up to 5A of constant current while maintaining a stable output voltage of 12V. The design featured a compact PCB layout, efficient thermal management, and compliance with automotive EMC and safety standards.
DC Motor Control
In DC motor control applications, high current buck voltage controllers are used to regulate the motor’s speed and torque by adjusting the voltage supplied to the motor windings. These controllers offer precise control, high efficiency, and protection features such as over-current and over-temperature protection.
Case Study: High-Performance DC Motor Controller for Industrial Automation
An industrial automation company developed a high-performance DC motor controller using a high current buck voltage controller. The controller was capable of delivering up to 20A of continuous current while providing precise speed and torque control. The design incorporated advanced control algorithms, efficient power stage design, and robust protection features to ensure reliable operation in demanding industrial environments.
Frequently Asked Questions (FAQ)
- What is the difference between a buck converter and a boost converter?
-
A buck converter steps down the input voltage to a lower output voltage, while a boost converter steps up the input voltage to a higher output voltage.
-
Can a high current buck voltage controller be used for both constant voltage and constant current applications?
-
Yes, a high current buck voltage controller can be configured for either constant voltage or constant current operation by selecting the appropriate control technique and feedback signal.
-
What are the main sources of power losses in a high current buck converter?
-
The main sources of power losses in a high current buck converter are conduction losses in the MOSFET, inductor, and diode, as well as switching losses during the transitions between on and off states.
-
How does the switching frequency affect the design of a high current buck converter?
-
A higher switching frequency allows for smaller inductor and capacitor values, reducing the size and cost of the converter. However, it also increases switching losses and may require more advanced control techniques to maintain efficiency.
-
What are the key safety considerations when designing a high current buck voltage controller?
- Key safety considerations include incorporating over-current, over-voltage, and over-temperature protection features, ensuring proper isolation between high-voltage and low-voltage circuits, and complying with relevant safety standards and regulations.
In conclusion, high current buck voltage controllers play a crucial role in various power electronics applications, offering efficient and precise voltage regulation for high current loads. By understanding the operating principles, design considerations, and optimization techniques, engineers can develop robust and reliable high current buck voltage controllers tailored to specific application requirements.
Leave a Reply