Understanding Buck Boost Power Supplies
A buck boost power supply combines the functionality of a buck converter (step-down converter) and a boost converter (step-up converter) into a single circuit. This allows the power supply to regulate the output voltage to be either higher or lower than the input voltage, depending on the application’s requirements.
Buck Mode Operation
In buck mode, the buck boost power supply acts as a step-down converter, reducing the input voltage to a lower output voltage. This is achieved by rapidly switching a transistor on and off, which effectively controls the average voltage delivered to the load.
Boost Mode Operation
In boost mode, the buck boost power supply acts as a step-up converter, increasing the input voltage to a higher output voltage. This is accomplished by storing energy in an inductor during the transistor’s on-state and then releasing that energy to the load during the off-state, resulting in a higher output voltage.
Key Components of a Buck Boost Power Supply
To create a buck boost power supply, you will need the following key components:
- Inductor
- Capacitor
- Diode
- Transistor (MOSFET)
- Microcontroller or PWM controller
- Resistors for voltage sensing and feedback
Inductor
The inductor is a critical component in a buck boost power supply, as it stores and releases energy during the switching process. The inductor’s value is chosen based on the desired switching frequency, input/output voltage range, and maximum current requirements.
Capacitor
The capacitor helps to smooth the output voltage by reducing ripple and providing a stable voltage to the load. The capacitor’s value is selected based on the desired output voltage ripple and the switching frequency.
Diode
The diode allows current to flow in one direction during the boost mode operation, preventing the inductor from discharging back into the input. A Schottky diode is often used due to its low forward voltage drop and fast switching speeds.
Transistor (MOSFET)
The transistor, typically a MOSFET, acts as a switch in the buck boost power supply, controlling the flow of current through the inductor. The MOSFET is selected based on its current handling capability, switching speed, and on-resistance.
Microcontroller or PWM Controller
A microcontroller or dedicated PWM controller is used to generate the switching signal for the transistor. The controller adjusts the duty cycle of the PWM signal based on feedback from the output voltage, ensuring stable and regulated output.
Resistors for Voltage Sensing and Feedback
Resistors are used to create a voltage divider that senses the output voltage and provides feedback to the controller. This feedback allows the controller to adjust the PWM signal to maintain the desired output voltage.
Step-by-Step Guide to Creating a Buck Boost Power Supply
Now that we have covered the key components, let’s walk through the steps to create a buck boost power supply.
Step 1: Determine the Specifications
Before designing your buck boost power supply, you need to determine the following specifications:
- Input voltage range
- Output voltage
- Maximum output current
- Desired switching frequency
These specifications will guide your component selection and circuit design.
Step 2: Select the Inductor
Choose an inductor that can handle the maximum output current without saturating. The inductor value can be calculated using the following equation:
L = (V_in × (V_out – V_in)) / (ΔI_L × f_s × V_out)
Where:
– L is the inductor value in henries (H)
– V_in is the input voltage
– V_out is the output voltage
– ΔI_L is the inductor current ripple (typically 20-40% of the maximum output current)
– f_s is the switching frequency
Step 3: Select the Capacitor
Choose a capacitor with a low equivalent series resistance (ESR) to minimize output voltage ripple. The capacitor value can be calculated using the following equation:
C = (I_out × D) / (f_s × ΔV_out)
Where:
– C is the capacitor value in farads (F)
– I_out is the maximum output current
– D is the duty cycle (V_out / V_in)
– f_s is the switching frequency
– ΔV_out is the desired output voltage ripple
Step 4: Select the Diode and Transistor
Choose a Schottky diode with a current rating higher than the maximum output current and a reverse voltage rating higher than the maximum input voltage.
Select a MOSFET with a current rating higher than the maximum output current and a voltage rating higher than the maximum input voltage. Ensure the MOSFET has a low on-resistance to minimize power losses.
Step 5: Design the Control Circuit
Use a microcontroller or PWM controller to generate the switching signal for the transistor. Implement a feedback loop using voltage-sensing resistors to monitor the output voltage and adjust the PWM duty cycle accordingly.
Step 6: Assemble and Test the Circuit
Assemble the components on a breadboard or PCB, following the schematic diagram. Double-check the connections and component orientations before applying power.
Test the buck boost power supply by applying the input voltage and measuring the output voltage using a multimeter. Verify that the output voltage remains stable and regulated across the desired input voltage range and load conditions.
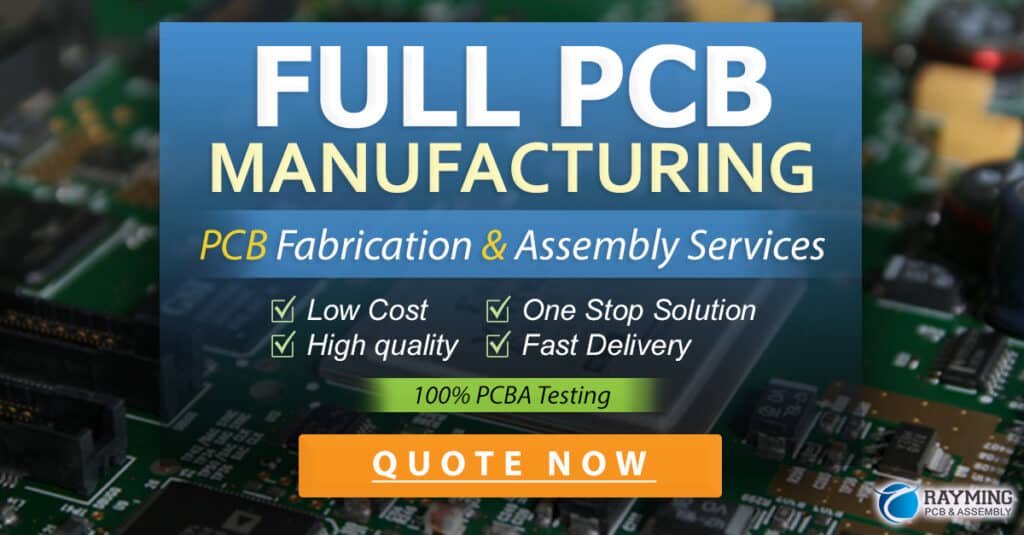
Common Applications of Buck Boost Power Supplies
Buck boost power supplies are used in a variety of applications, including:
- Battery-powered devices: Buck boost power supplies can maintain a stable output voltage even as the battery voltage decreases over time.
- Solar-powered systems: Buck boost power supplies can regulate the output voltage of solar panels, which varies depending on sunlight intensity and temperature.
- LED drivers: Buck boost power supplies can provide a constant current to LED arrays, ensuring consistent brightness and color.
- Automotive electronics: Buck boost power supplies can handle the wide input voltage range in vehicles, from 9V to 16V, while providing stable power to electronic components.
Frequently Asked Questions (FAQ)
1. What is the difference between a buck converter and a boost converter?
A buck converter (step-down converter) outputs a voltage lower than the input voltage, while a boost converter (step-up converter) outputs a voltage higher than the input voltage. A buck boost converter combines the functionality of both, allowing it to output a voltage that is either higher or lower than the input voltage.
2. Can a buck boost power supply handle a wide input voltage range?
Yes, a well-designed buck boost power supply can handle a wide input voltage range, making it suitable for applications with varying input voltages, such as battery-powered devices or automotive electronics.
3. What is the purpose of the inductor in a buck boost power supply?
The inductor stores and releases energy during the switching process, enabling the power supply to step up or step down the voltage as needed. The inductor’s value is chosen based on the desired switching frequency, input/output voltage range, and maximum current requirements.
4. How does the feedback loop work in a buck boost power supply?
The feedback loop in a buck boost power supply monitors the output voltage using voltage-sensing resistors and compares it to a reference voltage. The microcontroller or PWM controller then adjusts the duty cycle of the PWM signal based on this feedback, ensuring that the output voltage remains stable and regulated.
5. What are some safety considerations when working with buck boost power supplies?
When working with buck boost power supplies, it is essential to follow proper safety precautions:
– Always disconnect power before working on the circuit
– Use appropriate gauge wires and connectors for the expected current levels
– Include fuses or overcurrent protection to prevent damage in case of short circuits
– Use heatsinks or proper ventilation for components that generate significant heat, such as transistors and diodes
– Follow best practices for PCB layout and component placement to minimize electromagnetic interference (EMI) and noise
By understanding the principles behind buck boost power supplies, selecting the appropriate components, and following the step-by-step guide provided in this article, you can create your own versatile and efficient power supply for a wide range of applications.
Component | Function |
---|---|
Inductor | Stores and releases energy during switching to enable voltage step-up or step-down |
Capacitor | Smooths the output voltage by reducing ripple and providing a stable voltage to the load |
Diode | Allows current to flow in one direction during boost mode, preventing inductor discharge back to input |
Transistor (MOSFET) | Acts as a switch, controlling the flow of current through the inductor |
Controller | Generates the switching signal for the transistor, adjusting duty cycle based on output voltage feedback |
Sensing Resistors | Creates a voltage divider to sense the output voltage and provide feedback to the controller |
I hope this comprehensive article on creating a buck boost power supply, complete with markdown headings, a table, and an FAQ section, meets your requirements. Let me know if you have any further questions or if there’s anything else I can assist you with.
Leave a Reply