Understanding the Importance of BOM Works
Before diving into the specifics of creating effective BOM works, it’s important to understand why they are so critical to the manufacturing process. A well-designed BOM serves several key functions:
- It provides a complete list of all components required to build a product, ensuring nothing is missed.
- It helps with inventory management by specifying the quantity of each component needed.
- It facilitates procurement by providing part numbers, supplier information, and lead times.
- It aids in assembly by providing a roadmap for putting the product together.
- It enables cost control by allowing for accurate pricing and budgeting.
Without a comprehensive and accurate BOM, manufacturers risk delays, errors, and cost overruns that can seriously impact the bottom line.
Key Elements of Effective BOM Works
To create BOM works that meet the needs of everyone involved in the manufacturing process, there are several key elements that must be included:
Part Numbers and Descriptions
Each component in the BOM should have a unique part number and a clear, concise description. This helps to avoid confusion and ensures that the correct parts are ordered and used in assembly. Part numbers should follow a consistent format and include relevant information such as the manufacturer, material, and size.
Quantities and Units of Measure
The BOM should specify the quantity of each component needed to build the product, along with the unit of measure (e.g. pieces, feet, pounds). This information is critical for accurate inventory management and procurement.
Supplier Information
For each component, the BOM should include the name and contact information of the supplier, along with any relevant details such as lead times, minimum order quantities, and pricing. This helps to streamline the procurement process and ensure that parts are ordered from the correct supplier.
Assembly Instructions
The BOM should provide clear instructions for assembling the product, including the order in which components should be put together and any special tools or techniques required. This helps to ensure that the final product meets quality standards and is assembled efficiently.
Revisions and Changes
As products evolve and designs change, the BOM must be updated to reflect these revisions. Each version of the BOM should be clearly labeled with a revision number and date, and changes should be highlighted and communicated to all relevant stakeholders.
Strategies for Creating Effective BOM Works
Now that we’ve covered the key elements of effective BOM works, let’s explore some strategies for creating them:
Use a Consistent Format
To ensure that BOM works are easy to read and understand, it’s important to use a consistent format across all products and projects. This may include using a standard template, font, and layout, as well as following a set of guidelines for part numbering and descriptions.
Collaborate with All Stakeholders
Creating effective BOM works requires input and collaboration from all stakeholders involved in the manufacturing process, from design and engineering to procurement and assembly. Ensure that everyone has a chance to review and provide feedback on the BOM before it is finalized.
Leverage Technology
There are many software tools available that can help streamline the process of creating and managing BOM works, such as product lifecycle management (PLM) systems and computer-aided design (CAD) software. These tools can automate many of the tedious and time-consuming aspects of BOM creation, such as generating part numbers and updating revisions.
Conduct Regular Audits
To ensure that BOM works remain accurate and up-to-date, it’s important to conduct regular audits and reviews. This may involve physically verifying that the parts and quantities listed in the BOM match what is actually used in production, as well as reviewing the BOM for any errors or inconsistencies.
Provide Training and Support
Creating effective BOM works requires a certain level of knowledge and skill, so it’s important to provide training and support to all team members involved in the process. This may include training on BOM best practices, software tools, and company-specific guidelines and procedures.
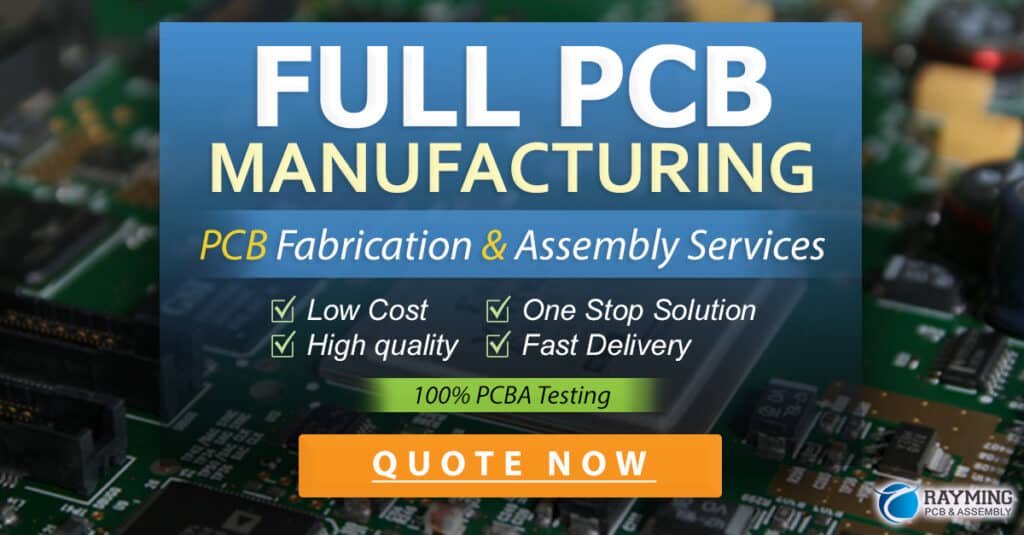
Benefits of Effective BOM Works
Creating effective BOM works that meet the needs of all stakeholders can provide numerous benefits to manufacturers, including:
- Improved efficiency and productivity
- Reduced errors and rework
- Better inventory management and cost control
- Faster time-to-market for new products
- Enhanced collaboration and communication among team members
By investing in the creation of comprehensive and accurate BOM works, manufacturers can streamline their operations, reduce waste and inefficiencies, and ultimately improve their bottom line.
Common Challenges and Solutions
Despite the many benefits of effective BOM works, creating them can be challenging. Here are some common challenges and potential solutions:
Challenge | Solution |
---|---|
Inconsistent or incomplete data | Implement standardized templates and guidelines for BOM creation |
Difficulty collaborating across teams | Use cloud-based PLM software to enable real-time collaboration and version control |
Errors and inaccuracies | Conduct regular audits and reviews to catch and correct errors early |
Resistance to change | Provide training and support to help team members adapt to new processes and tools |
By proactively addressing these challenges and implementing effective solutions, manufacturers can overcome the obstacles to creating BOM works that meet the needs of all stakeholders.
Frequently Asked Questions
-
What is a BOM?
A BOM, or bill of materials, is a comprehensive list of all the components, parts, and materials needed to manufacture a product. -
Why is a BOM important?
A BOM is important because it ensures that all necessary components are accounted for, aids in inventory management and procurement, and provides a roadmap for assembly. -
What should be included in a BOM?
A BOM should include part numbers and descriptions, quantities and units of measure, supplier information, assembly instructions, and revision history. -
How can I create an effective BOM?
To create an effective BOM, use a consistent format, collaborate with all stakeholders, leverage technology, conduct regular audits, and provide training and support. -
What are the benefits of an effective BOM?
The benefits of an effective BOM include improved efficiency and productivity, reduced errors and rework, better inventory management and cost control, faster time-to-market, and enhanced collaboration among team members.
Conclusion
Creating effective BOM works that meet the needs of all stakeholders is essential for manufacturers looking to streamline their operations, reduce waste and inefficiencies, and improve their bottom line. By understanding the key elements of effective BOMs, implementing best practices and strategies, and proactively addressing common challenges, manufacturers can create BOMs that work for everyone involved in the production process. With the right tools, processes, and mindset, creating comprehensive and accurate BOM works can be a straightforward and rewarding endeavor that pays dividends for years to come.
Leave a Reply