Introduction
Coverlay is a critical component in the manufacturing of flexible printed circuits (FPCs) and other electronic devices. It serves as a protective layer, insulating the conductive traces and providing mechanical support to the overall structure. The selection of the appropriate coverlay type is crucial for ensuring the reliability, durability, and performance of the end product. This article will explore the various factors that influence the choice of coverlay type, with a focus on installation and end use requirements.
What is Coverlay?
Coverlay is a thin, flexible film that is laminated onto the surface of a flexible printed circuit or other electronic devices. It is typically made of polyimide, polyester, or other polymeric materials that exhibit excellent electrical insulation properties, thermal stability, and mechanical strength. Coverlay serves several key functions, including:
- Protecting the conductive traces from environmental factors such as moisture, dust, and abrasion.
- Providing electrical insulation between the conductive traces and other components.
- Enhancing the mechanical stability and flexibility of the FPC.
- Improving the aesthetic appearance of the end product.
Factors Influencing Coverlay Type Selection
The selection of the appropriate coverlay type is influenced by a variety of factors, including the specific application, the environmental conditions, and the manufacturing process. Some of the key factors to consider when choosing a coverlay type include:
1. Electrical Properties
The electrical properties of the coverlay material are critical for ensuring the proper functioning of the electronic device. Key electrical properties to consider include:
- Dielectric constant: The dielectric constant of the coverlay material should be low to minimize the capacitance between the conductive traces and other components.
- Dielectric strength: The coverlay should have a high dielectric strength to prevent electrical breakdown and ensure proper insulation.
- Volume resistivity: The coverlay should have a high volume resistivity to prevent current leakage and minimize the risk of short circuits.
2. Thermal Properties
The thermal properties of the coverlay material are important for ensuring the reliability and durability of the electronic device, especially in high-temperature applications. Key thermal properties to consider include:
- Glass transition temperature (Tg): The Tg of the coverlay should be higher than the maximum operating temperature of the device to prevent softening and deformation.
- Coefficient of thermal expansion (CTE): The CTE of the coverlay should be similar to that of the other components to minimize stress and prevent delamination during temperature cycling.
- Thermal conductivity: In some applications, such as heat sinks, the coverlay should have a high thermal conductivity to facilitate heat dissipation.
3. Mechanical Properties
The mechanical properties of the coverlay material are critical for ensuring the flexibility, durability, and reliability of the electronic device. Key mechanical properties to consider include:
- Tensile strength: The coverlay should have a high tensile strength to withstand the stresses encountered during installation and use.
- Elongation: The coverlay should have a high elongation to accommodate the flexing and bending of the FPC without cracking or delaminating.
- Modulus: The modulus of the coverlay should be appropriate for the specific application, balancing the need for flexibility and mechanical support.
4. Chemical Resistance
The chemical resistance of the coverlay material is important for ensuring the durability and reliability of the electronic device in harsh chemical environments. Key chemical resistance properties to consider include:
- Solvent resistance: The coverlay should be resistant to the solvents used in the manufacturing process and the end-use environment.
- Acid and base resistance: The coverlay should be resistant to acids and bases that may be encountered in the end-use environment.
- Moisture resistance: The coverlay should be resistant to moisture to prevent corrosion and degradation of the conductive traces.
5. Flammability
In some applications, such as aerospace and automotive, the flammability of the coverlay material is a critical consideration. Key flammability properties to consider include:
- UL 94 rating: The coverlay should have an appropriate UL 94 rating (e.g., V-0) for the specific application.
- Oxygen index: The oxygen index of the coverlay should be high to minimize the risk of ignition and flame spread.
6. Optical Properties
In some applications, such as displays and light-emitting devices, the optical properties of the coverlay material are important. Key optical properties to consider include:
- Transparency: The coverlay should have a high transparency to allow light to pass through without significant attenuation.
- Haze: The coverlay should have a low haze to minimize light scattering and ensure clear visibility.
- Yellowness index: The coverlay should have a low yellowness index to prevent discoloration and maintain the aesthetic appearance of the device.
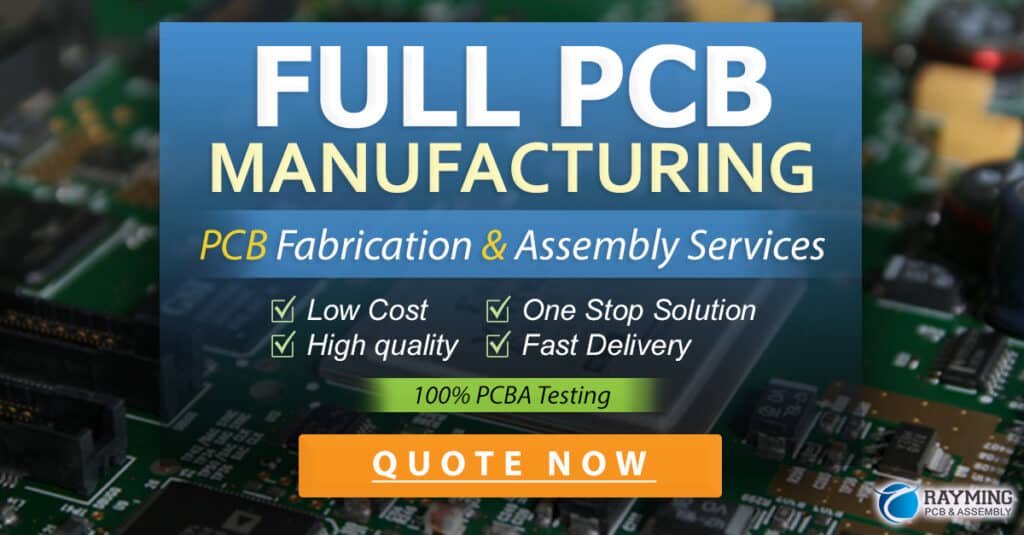
Common Coverlay Materials
Several materials are commonly used for coverlay, each with its own unique set of properties and advantages. Some of the most common coverlay materials include:
1. Polyimide
Polyimide is a high-performance polymer that exhibits excellent thermal stability, mechanical strength, and chemical resistance. It is widely used in high-temperature applications and harsh environmental conditions. Some of the key advantages of polyimide coverlay include:
- High glass transition temperature (>300°C)
- Excellent dielectric properties
- High tensile strength and modulus
- Good chemical resistance
- UL 94 V-0 rating
2. Polyester
Polyester is a cost-effective and versatile polymer that is commonly used in low-temperature applications and consumer electronics. It exhibits good mechanical properties and electrical insulation. Some of the key advantages of polyester coverlay include:
- Lower cost compared to polyimide
- Good dielectric properties
- Adequate tensile strength and elongation
- Moderate chemical resistance
- UL 94 VTM-0 rating
3. Epoxy
Epoxy-based coverlay materials are known for their excellent adhesion, chemical resistance, and mechanical strength. They are commonly used in applications that require high reliability and durability. Some of the key advantages of epoxy coverlay include:
- Excellent adhesion to various substrates
- High chemical resistance
- Good mechanical strength and toughness
- UL 94 V-0 rating
4. Acrylic
Acrylic-based coverlay materials are known for their transparency, flexibility, and UV resistance. They are commonly used in applications that require clear visibility and outdoor exposure. Some of the key advantages of acrylic coverlay include:
- High transparency
- Excellent flexibility and elongation
- Good UV resistance
- Moderate chemical resistance
Installation Considerations
The installation process for coverlay can vary depending on the specific application and the type of coverlay material used. Some of the key installation considerations include:
1. Surface Preparation
The surface of the FPC or electronic device should be properly cleaned and prepared before coverlay installation. This typically involves:
- Cleaning the surface with solvents to remove contaminants
- Roughening the surface to improve adhesion
- Applying a primer or adhesion promoter, if necessary
2. Lamination Process
The lamination process involves bonding the coverlay to the surface of the FPC or electronic device. The specific lamination process can vary depending on the coverlay material and the application, but typically involves:
- Aligning the coverlay with the FPC or device
- Applying heat and pressure to activate the adhesive and bond the coverlay
- Cooling the laminated assembly to allow the adhesive to set
3. Curing
Some coverlay materials, such as epoxy-based coverlays, require a curing step after lamination to achieve their final properties. The curing process typically involves:
- Exposing the laminated assembly to elevated temperatures for a specific duration
- Allowing the assembly to cool to room temperature
4. Inspection and Testing
After installation, the coverlay should be inspected and tested to ensure proper adhesion, insulation, and performance. This may involve:
- Visual inspection for defects such as bubbles, wrinkles, or delamination
- Electrical testing to verify insulation resistance and dielectric strength
- Mechanical testing to evaluate adhesion, flexibility, and durability
End Use Requirements
The end use requirements for coverlay can vary widely depending on the specific application and the environmental conditions. Some of the key end use requirements to consider include:
1. Operating Temperature Range
The coverlay should be able to withstand the expected operating temperature range of the electronic device. This may involve:
- Ensuring the glass transition temperature of the coverlay is higher than the maximum operating temperature
- Selecting a coverlay material with a low CTE to minimize stress during temperature cycling
2. Environmental Exposure
The coverlay should be able to withstand the expected environmental conditions, such as:
- Humidity and moisture exposure
- UV radiation and outdoor weathering
- Chemical exposure to solvents, fuels, or other aggressive agents
3. Mechanical Stress
The coverlay should be able to withstand the expected mechanical stresses encountered during use, such as:
- Flexing and bending of the FPC
- Vibration and shock loading
- Abrasion and wear
4. Electrical Performance
The coverlay should maintain its electrical insulation properties throughout the expected life of the electronic device, including:
- Dielectric strength to prevent electrical breakdown
- Insulation resistance to prevent current leakage
- Capacitance control to minimize signal distortion
Conclusion
The selection of the appropriate coverlay type is a critical factor in ensuring the reliability, durability, and performance of flexible printed circuits and other electronic devices. The choice of coverlay material should be based on a careful consideration of the specific application requirements, including electrical, thermal, mechanical, chemical, and optical properties. Additionally, the installation process and end use requirements should be thoroughly evaluated to ensure the coverlay can withstand the expected environmental conditions and mechanical stresses. By understanding the key factors influencing coverlay type selection and working closely with material suppliers and manufacturing partners, designers and engineers can develop high-quality, reliable electronic devices that meet the demands of today’s challenging applications.
FAQ
1. What is the difference between polyimide and polyester coverlay?
Polyimide and polyester are two common materials used for coverlay, but they have different properties and are suited for different applications. Polyimide coverlay has a higher temperature resistance, better chemical resistance, and higher mechanical strength compared to polyester. However, polyester coverlay is typically less expensive and has better transparency.
2. Can coverlay be used in high-temperature applications?
Yes, certain types of coverlay, such as polyimide, can be used in high-temperature applications. Polyimide coverlay has a high glass transition temperature (>300°C) and excellent thermal stability, making it suitable for use in environments with elevated temperatures.
3. How does the installation process affect the performance of coverlay?
The installation process can have a significant impact on the performance of coverlay. Proper surface preparation, lamination, and curing are essential for achieving good adhesion, insulation, and durability. Inadequate installation can lead to defects such as bubbles, wrinkles, or delamination, which can compromise the electrical and mechanical properties of the coverlay.
4. What environmental factors should be considered when selecting a coverlay type?
When selecting a coverlay type, it is important to consider the environmental factors that the electronic device will be exposed to during use. These factors may include humidity, moisture, UV radiation, chemical exposure, and temperature variations. The coverlay material should be chosen based on its ability to withstand these environmental conditions and maintain its properties over the expected life of the device.
5. How can designers and engineers ensure they select the appropriate coverlay type for their application?
To ensure the selection of the appropriate coverlay type, designers and engineers should work closely with material suppliers and manufacturing partners who have expertise in coverlay materials and processes. They should thoroughly evaluate the specific application requirements, including electrical, thermal, mechanical, chemical, and optical properties, as well as the installation process and end use requirements. By conducting a comprehensive assessment and leveraging the knowledge of experts, designers and engineers can make informed decisions and select the coverlay type that best meets the needs of their application.
Property | Polyimide | Polyester | Epoxy | Acrylic |
---|---|---|---|---|
Temperature Resistance | High | Moderate | High | Low |
Dielectric Strength | Excellent | Good | Good | Moderate |
Mechanical Strength | High | Moderate | High | Low |
Chemical Resistance | Excellent | Moderate | High | Moderate |
Transparency | Low | High | Low | High |
Cost | High | Low | Moderate | Moderate |
This table compares the key properties of common coverlay materials, including polyimide, polyester, epoxy, and acrylic. It provides a quick reference for designers and engineers to evaluate the relative performance of each material in terms of temperature resistance, dielectric strength, mechanical strength, chemical resistance, transparency, and cost. This information can help guide the selection of the appropriate coverlay type based on the specific application requirements and priorities.
Leave a Reply