Introduction to Rigid Flex PCBs
Rigid flex PCBs are a unique type of printed circuit board that combines the benefits of both rigid and flexible substrates. These boards consist of rigid PCB sections connected by flexible circuits, allowing for three-dimensional packaging and improved reliability in applications that require flexibility or space-saving designs. Rigid flex PCBs have gained popularity in various industries, including aerospace, medical devices, automotive, and consumer electronics.
Advantages of Rigid Flex PCBs
- Space savings: Rigid flex PCBs enable more compact designs by eliminating the need for connectors and cables between rigid boards.
- Increased reliability: The reduction in interconnects and the use of flexible substrates improve the overall reliability of the circuit.
- Enhanced flexibility: The flexible sections of the PCB allow for bending and folding, making it easier to fit the board into tight spaces or movable parts.
- Improved signal integrity: Rigid flex PCBs minimize signal loss and interference by reducing the distance between components and eliminating the need for external connectors.
- Weight reduction: By consolidating multiple rigid boards into a single rigid flex PCB, the overall weight of the assembly can be reduced.
Factors Affecting Rigid Flex PCB Cost
While rigid flex PCBs offer numerous benefits, they are generally more expensive than traditional rigid PCBs. Several factors contribute to the higher cost of rigid flex PCBs:
1. Material Costs
Rigid flex PCBs require specialized materials, such as flexible substrates (e.g., polyimide), adhesives, and coverlay films. These materials are more expensive than standard FR-4 substrates used in rigid PCBs.
2. Manufacturing Complexity
The fabrication process for rigid flex PCBs is more complex and time-consuming compared to rigid PCBs. It involves additional steps, such as laminating flexible layers, selective bonding, and creating controlled-depth cavities for components. This increased complexity contributes to higher manufacturing costs.
3. Design Considerations
Designing rigid flex PCBs requires expertise in both rigid and flexible circuit design. The designer must account for factors such as bend radius, layer stackup, and material selection to ensure the board’s reliability and functionality. The additional design effort and skill required can increase the overall cost of the project.
4. Quantity and Size
As with most PCB projects, the quantity and size of the rigid flex PCBs impact the cost. Smaller quantities and larger board sizes generally result in higher unit costs due to the fixed costs associated with setup and tooling.
5. Layer Count and Complexity
The number of layers and the complexity of the circuit design also affect the cost of rigid flex PCBs. More layers and intricate designs require additional processing steps and materials, leading to higher fabrication costs.
Rigid Flex PCB Cost Comparison
To better understand the cost differences between rigid flex PCBs and traditional rigid PCBs, let’s compare some hypothetical scenarios.
Scenario 1: Simple 2-Layer Board
Board Type | Quantity | Size (mm) | Layers | Material | Unit Cost |
---|---|---|---|---|---|
Rigid PCB | 100 | 50 x 50 | 2 | FR-4 | $5 |
Rigid Flex PCB | 100 | 50 x 50 | 2 | FR-4 + Polyimide | $15 |
In this scenario, the rigid flex PCB is approximately three times more expensive than the rigid PCB due to the additional materials and processing required.
Scenario 2: Complex 6-Layer Board
Board Type | Quantity | Size (mm) | Layers | Material | Unit Cost |
---|---|---|---|---|---|
Rigid PCB | 500 | 100 x 100 | 6 | FR-4 | $20 |
Rigid Flex PCB | 500 | 100 x 100 | 6 | FR-4 + Polyimide | $60 |
For a more complex 6-layer board, the rigid flex PCB is still about three times more expensive than the rigid PCB. However, the higher quantity helps to reduce the unit cost for both board types.
Scenario 3: High-Volume Production
Board Type | Quantity | Size (mm) | Layers | Material | Unit Cost |
---|---|---|---|---|---|
Rigid PCB | 10,000 | 75 x 75 | 4 | FR-4 | $8 |
Rigid Flex PCB | 10,000 | 75 x 75 | 4 | FR-4 + Polyimide | $25 |
In high-volume production, the unit cost for both rigid and rigid flex PCBs decreases significantly. However, the rigid flex PCB remains more expensive, with a unit cost just over three times that of the rigid PCB.
These scenarios demonstrate that rigid flex PCBs are generally more expensive than traditional rigid PCBs, with the cost difference being approximately three times higher in most cases. However, it’s essential to consider the unique benefits and applications of rigid flex PCBs when evaluating the cost-effectiveness of using them in a specific project.
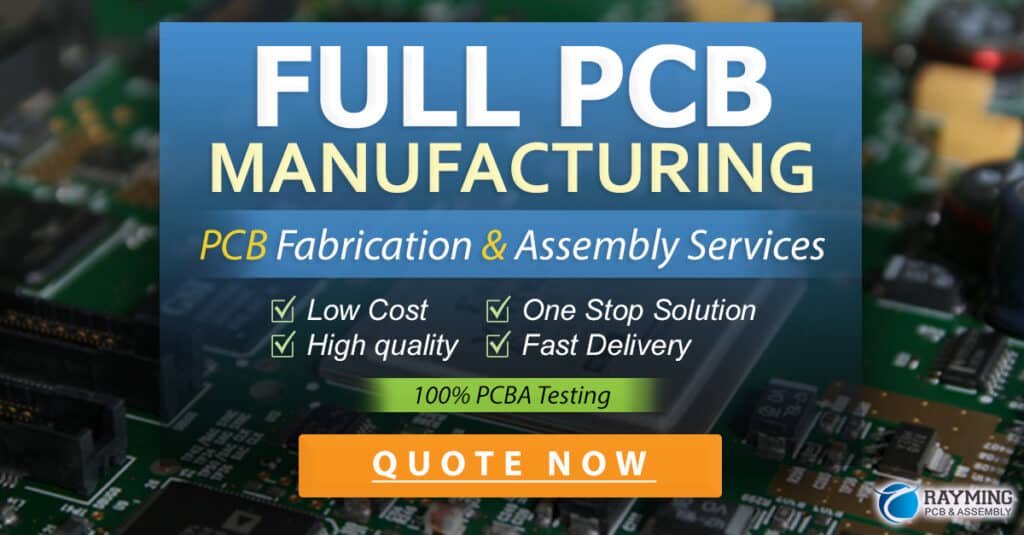
Cost Optimization Strategies for Rigid Flex PCBs
Despite the inherently higher costs associated with rigid flex PCBs, there are several strategies that can help optimize costs without compromising functionality or reliability.
1. Design Optimization
Collaborating closely with experienced rigid flex PCB designers can help identify opportunities for design optimization. This may include minimizing the number of layers, optimizing the placement of components, and reducing the overall board size. By streamlining the design, it’s possible to reduce material and manufacturing costs.
2. Material Selection
While flexible substrates like polyimide are essential for rigid flex PCBs, there may be opportunities to use lower-cost materials in certain areas of the board. For example, using FR-4 for the rigid sections and reserving the more expensive flexible materials for the flexible regions can help balance cost and performance.
3. Panelization
Panelizing multiple rigid flex PCBs on a single panel can help reduce manufacturing costs by minimizing setup and tooling expenses. This approach is particularly effective for high-volume production runs.
4. Prototype and Testing
Investing in thorough prototyping and testing can help identify and address any design issues early in the development process. By catching and correcting problems before full-scale production, it’s possible to avoid costly redesigns and rework later on.
5. Supplier Selection
Choosing the right rigid flex PCB supplier is crucial for managing costs and ensuring quality. Look for suppliers with experience in rigid flex PCB fabrication, a proven track record of quality, and competitive pricing. Building a strong relationship with a reliable supplier can lead to cost savings over the long term.
Frequently Asked Questions (FAQ)
-
Q: Are rigid flex PCBs always more expensive than rigid PCBs?
A: In most cases, yes. Rigid flex PCBs require specialized materials, more complex manufacturing processes, and additional design considerations, which contribute to higher costs compared to traditional rigid PCBs. -
Q: How much more expensive are rigid flex PCBs compared to rigid PCBs?
A: The cost difference between rigid flex PCBs and rigid PCBs can vary depending on factors such as board size, layer count, and quantity. However, rigid flex PCBs are typically about three times more expensive than comparable rigid PCBs. -
Q: Can the cost of rigid flex PCBs be reduced through high-volume production?
A: Yes, higher production volumes can help reduce the unit cost of rigid flex PCBs. As the quantity increases, fixed costs such as setup and tooling are spread across more units, resulting in a lower cost per board. -
Q: Are there any ways to optimize the cost of rigid flex PCBs without compromising quality?
A: Yes, several strategies can help optimize the cost of rigid flex PCBs, including design optimization, material selection, panelization, thorough prototyping and testing, and choosing the right supplier. -
Q: When is it cost-effective to use rigid flex PCBs instead of rigid PCBs?
A: Rigid flex PCBs are cost-effective when the unique benefits they offer, such as space savings, increased reliability, and enhanced flexibility, are essential to the application. In projects where these factors are critical, the higher cost of rigid flex PCBs can be justified by the improved performance and functionality they provide.
Conclusion
Rigid flex PCBs offer a unique combination of benefits, including space savings, increased reliability, and enhanced flexibility. However, these advantages come at a higher cost compared to traditional rigid PCBs. The cost difference can be attributed to specialized materials, manufacturing complexity, design considerations, and other factors.
When evaluating the cost-effectiveness of using rigid flex PCBs in a project, it’s essential to consider the specific requirements and priorities of the application. In some cases, the improved performance and functionality provided by rigid flex PCBs can justify the higher cost. Additionally, strategies such as design optimization, material selection, panelization, and supplier selection can help manage and optimize the cost of rigid flex PCBs.
Ultimately, the decision to use rigid flex PCBs should be based on a careful analysis of the project’s needs, budget, and long-term goals. By understanding the factors that influence rigid flex PCB costs and employing cost optimization strategies, it’s possible to leverage the benefits of this technology while maintaining a competitive edge in the market.
Leave a Reply