Understanding the Basics of PCB Services
Before diving into cost-cutting strategies, it’s essential to understand the fundamentals of PCB services. PCBs are the backbone of electronic devices, providing a platform for components to be mounted and interconnected. The PCB manufacturing process involves several stages, including design, fabrication, assembly, and testing.
PCB Design
The PCB design phase is critical in determining the overall cost and functionality of the final product. Factors such as board size, layer count, component placement, and routing complexity can significantly impact the manufacturing cost. Designers must strike a balance between optimizing the layout for performance and minimizing the cost of production.
PCB Fabrication
PCB fabrication involves the physical creation of the board. The process typically includes the following steps:
- Substrate preparation
- Copper foil lamination
- Drilling and plating through-holes
- Etching and patterning of copper traces
- Solder mask application
- Silkscreen printing
Each step contributes to the overall cost of fabrication, and manufacturers must carefully control the process to minimize waste and maintain quality.
PCB Assembly
Once the bare PCB is fabricated, electronic components are mounted onto the board through various assembly techniques, such as through-hole or surface-mount technology (SMT). The assembly process can be automated or manual, depending on the complexity of the board and the production volume.
PCB Testing
To ensure the reliability and functionality of the assembled PCBs, manufacturers conduct thorough testing procedures. These tests may include:
- Visual inspection
- Automated Optical Inspection (AOI)
- In-Circuit Testing (ICT)
- Functional testing
Rigorous testing helps identify defects early in the production process, preventing costly rework and failures in the field.
Strategies for Cost-cutting in PCB Services
Now that we have a basic understanding of PCB services, let’s explore various strategies for reducing costs without compromising quality.
1. Design Optimization
One of the most effective ways to cut costs in PCB services is through design optimization. By making informed decisions during the design phase, companies can significantly reduce manufacturing costs. Consider the following design optimization techniques:
a. Minimizing Board Size
Reducing the overall dimensions of the PCB can lead to substantial cost savings. Smaller boards require less material, reduce fabrication time, and often have lower assembly costs. Designers should carefully consider component placement and routing to minimize the board size while maintaining functionality.
b. Reducing Layer Count
PCBs with fewer layers are generally less expensive to manufacture than those with a higher layer count. Designers should strive to minimize the number of layers required by optimizing the component placement and routing. However, it’s essential to ensure that the reduced layer count does not compromise the board’s performance or signal integrity.
c. Standardizing Components
Using standardized components can help reduce costs in several ways. Standardized parts are often more readily available and less expensive than custom or specialized components. Additionally, standardization simplifies the procurement process and reduces the risk of obsolescence.
d. Optimizing Routing
Efficient routing is crucial for minimizing the board size and reducing the number of layers required. Designers should utilize routing techniques that minimize the overall trace length and avoid unnecessary vias. Automated routing tools can help optimize the routing process, saving time and reducing the chances of human error.
2. Strategic Sourcing
Another key aspect of cost-cutting in PCB services is strategic sourcing. By carefully selecting suppliers and materials, companies can significantly reduce their overall expenses. Consider the following sourcing strategies:
a. Supplier Selection
Choosing the right PCB manufacturer is critical for managing costs. When evaluating potential suppliers, consider factors such as:
- Manufacturing capabilities
- Quality control processes
- Lead times
- Pricing structure
- Reputation and customer reviews
Engage with multiple suppliers to compare offerings and negotiate competitive pricing. Building long-term relationships with reliable suppliers can lead to cost savings through volume discounts and improved communication.
b. Material Selection
The choice of materials used in PCB fabrication can have a significant impact on the overall cost. Consider the following material selection strategies:
- Use standard, readily available materials whenever possible
- Avoid exotic or specialty materials unless absolutely necessary
- Work with suppliers to identify cost-effective alternatives
- Consider the impact of material choice on the manufacturing process and yield
By making informed decisions about materials, companies can reduce costs without sacrificing the performance or reliability of their PCBs.
3. Process Optimization
Optimizing the PCB manufacturing process can lead to significant cost savings. By streamlining operations and reducing waste, companies can improve efficiency and lower production costs. Consider the following process optimization techniques:
a. Lean Manufacturing
Implementing lean manufacturing principles can help eliminate waste and improve the overall efficiency of the PCB production process. Lean manufacturing focuses on:
- Continuous improvement
- Reducing inventory
- Minimizing defects
- Optimizing workflow
By adopting lean practices, manufacturers can reduce costs associated with excess inventory, rework, and inefficient processes.
b. Automation
Automating certain aspects of the PCB manufacturing process can lead to cost savings through increased speed, accuracy, and consistency. Consider automating tasks such as:
- Component placement (SMT)
- Solder paste application
- Inspection and testing
While the initial investment in automation equipment may be higher, the long-term benefits can include reduced labor costs, improved quality, and faster production times.
c. Batch Processing
Grouping similar PCB designs into larger production batches can help reduce setup times and minimize waste. By processing multiple boards with similar specifications together, manufacturers can optimize equipment utilization and reduce the overall cost per board.
4. Collaborative Design and Development
Fostering collaboration between PCB designers, manufacturers, and end-users can lead to cost savings by identifying potential issues early in the development process. Consider the following collaborative strategies:
a. Design for Manufacturability (DFM)
Engaging with manufacturers during the design phase can help ensure that the PCB layout is optimized for production. Manufacturers can provide valuable feedback on design decisions that may impact the manufacturing process, such as:
- Component placement
- Trace spacing
- Drill sizes
- Solder mask and silkscreen requirements
By incorporating DFM principles, designers can avoid costly redesigns and improve the overall manufacturability of the PCB.
b. Early Supplier Involvement (ESI)
Involving suppliers early in the development process can help identify potential cost-saving opportunities. Suppliers can provide insights into:
- Material availability and pricing
- Manufacturing capabilities and limitations
- Lead times and minimum order quantities
By collaborating with suppliers early on, companies can make informed decisions about component selection, design, and production planning.
Frequently Asked Questions (FAQ)
-
Q: What is the most effective way to reduce PCB manufacturing costs?
A: Design optimization is one of the most effective ways to reduce PCB manufacturing costs. By minimizing board size, reducing layer count, standardizing components, and optimizing routing, designers can significantly lower production expenses. -
Q: How can strategic sourcing help cut costs in PCB services?
A: Strategic sourcing involves carefully selecting suppliers and materials to minimize costs. By choosing reliable suppliers with competitive pricing and selecting cost-effective materials, companies can reduce their overall PCB manufacturing expenses. -
Q: What role does process optimization play in cost-cutting for PCB services?
A: Process optimization techniques, such as lean manufacturing, automation, and batch processing, can help streamline PCB production and reduce waste. By improving efficiency and minimizing defects, manufacturers can lower production costs and improve overall profitability. -
Q: How can collaboration between designers, manufacturers, and suppliers lead to cost savings?
A: Collaborative design and development practices, such as Design for Manufacturability (DFM) and Early Supplier Involvement (ESI), can help identify potential cost-saving opportunities early in the development process. By working together, stakeholders can make informed decisions that optimize the PCB design for production and minimize the risk of costly redesigns. -
Q: Are there any risks associated with cost-cutting strategies in PCB services?
A: While cost-cutting strategies can lead to significant savings, it’s essential to balance cost reduction with maintaining the quality and reliability of the PCBs. Overemphasizing cost-cutting at the expense of performance or functionality can result in subpar products and damage a company’s reputation. It’s crucial to carefully evaluate the impact of cost-cutting measures and ensure that they do not compromise the overall value delivered to customers.
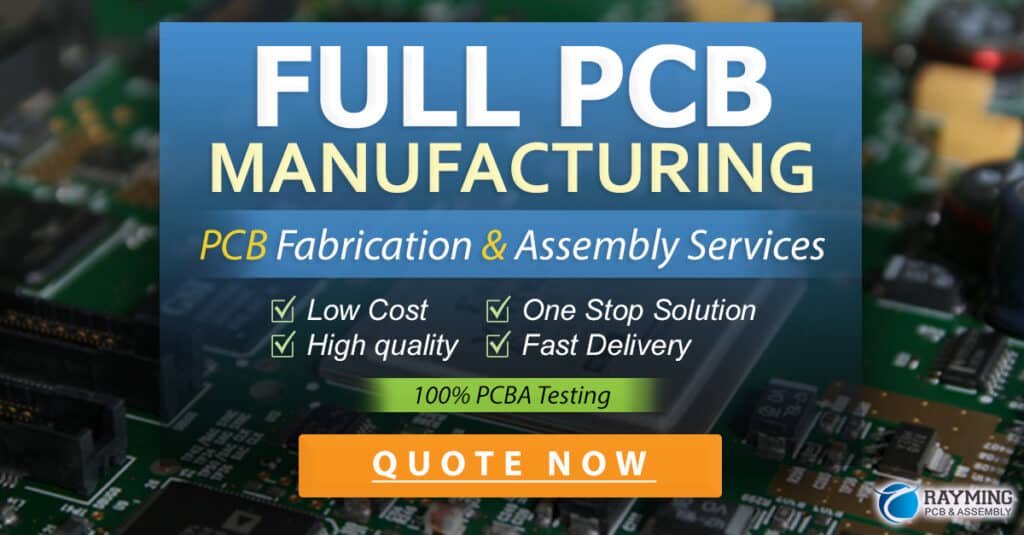
Conclusion
In today’s competitive electronics industry, cost-cutting in PCB services is essential for businesses to remain profitable and sustainable. By implementing strategies such as design optimization, strategic sourcing, process optimization, and collaborative development, companies can significantly reduce their PCB manufacturing expenses.
However, it’s crucial to approach cost-cutting with a balanced perspective, ensuring that the quality and reliability of the PCBs are not compromised in the pursuit of lower costs. By carefully evaluating the impact of cost-cutting measures and maintaining a focus on delivering value to customers, businesses can successfully navigate the challenges of the PCB industry and thrive in the long run.
Strategy | Key Aspects |
---|---|
Design Optimization | – Minimizing board size – Reducing layer count – Standardizing components – Optimizing routing |
Strategic Sourcing | – Supplier selection – Material selection |
Process Optimization | – Lean manufacturing – Automation – Batch processing |
Collaborative Development | – Design for Manufacturability (DFM) – Early Supplier Involvement (ESI) |
By embracing these cost-cutting strategies and continually seeking opportunities for improvement, companies can position themselves for success in the dynamic and ever-evolving world of PCB services.
Leave a Reply