Introduction to Subtractive and Semi-Additive Manufacturing
Subtractive manufacturing and semi-additive manufacturing are two distinct approaches to producing parts and components. Each method has its own advantages, limitations, and cost considerations.
What is Subtractive Manufacturing?
Subtractive manufacturing, also known as machining, involves starting with a solid block of material (such as metal or plastic) and removing material through cutting, drilling, milling, and turning to create the desired shape. Common subtractive processes include:
- CNC Machining
- Turning
- Milling
- Drilling
- Grinding
Subtractive manufacturing is a well-established and versatile method suitable for a wide range of materials and applications. It offers high precision, good surface finishes, and the ability to create complex geometries.
What is Semi-Additive Manufacturing?
Semi-additive manufacturing, also referred to as hybrid additive manufacturing, combines additive and subtractive processes to produce parts. It typically involves the following steps:
- Depositing a thin layer of material (usually metal) onto a substrate using additive techniques like electrochemical deposition or powder bed fusion.
- Selectively removing excess material using subtractive methods like milling or etching to achieve the desired shape and tolerances.
- Optionally, repeating steps 1 and 2 to build up additional layers and features.
Semi-additive manufacturing offers the benefits of both additive and subtractive processes, allowing for the creation of complex structures with high precision and surface quality.
Cost Factors in Subtractive Manufacturing
Several factors influence the cost of subtractive manufacturing:
Material Cost
The cost of the raw material is a significant contributor to the overall cost in subtractive manufacturing. Material prices vary depending on the type (e.g., aluminum, steel, titanium), grade, and supplier. Larger blocks of material are required to accommodate the removal of excess material during machining.
Machine and Tooling Cost
Subtractive manufacturing relies on specialized CNC machines and tooling, which can be expensive to acquire and maintain. The cost of the machines and tools depends on factors such as:
- Machine type and size
- Spindle speed and power
- Axis count and travel distances
- Tool holding and changing systems
- Coolant and chip management
Labor Cost
Skilled operators are required to set up, program, and oversee subtractive manufacturing processes. Labor costs can vary based on the complexity of the part, the experience of the operator, and the location of the manufacturing facility.
Production Time and Efficiency
Subtractive manufacturing can be time-consuming, especially for complex parts that require multiple setups and tool changes. The production time directly impacts the cost, as longer machining times result in higher labor and machine utilization costs.
Cost Factors in Semi-Additive Manufacturing
The cost of semi-additive manufacturing is influenced by several factors:
Material Cost
Semi-additive manufacturing typically uses metal powders or solutions as the raw material. The cost of these materials can be higher compared to traditional raw materials used in subtractive manufacturing. However, semi-additive processes often require less material overall, as they only deposit what is needed to create the part.
Equipment and Tooling Cost
Semi-additive manufacturing requires specialized equipment for both the additive and subtractive stages of the process. The cost of this equipment can be substantial, especially for high-precision systems. However, the tooling costs may be lower compared to subtractive manufacturing, as semi-additive processes often require fewer tools and setups.
Labor Cost
Semi-additive manufacturing requires skilled operators familiar with both additive and subtractive processes. The labor cost may be higher compared to subtractive manufacturing due to the specialized knowledge required. However, semi-additive processes can be more automated, potentially reducing labor costs in the long run.
Production Time and Efficiency
Semi-additive manufacturing can be faster than subtractive manufacturing for certain part geometries and complexities. The ability to deposit material only where needed and the reduced need for multiple setups and tool changes can lead to shorter production times and improved efficiency.
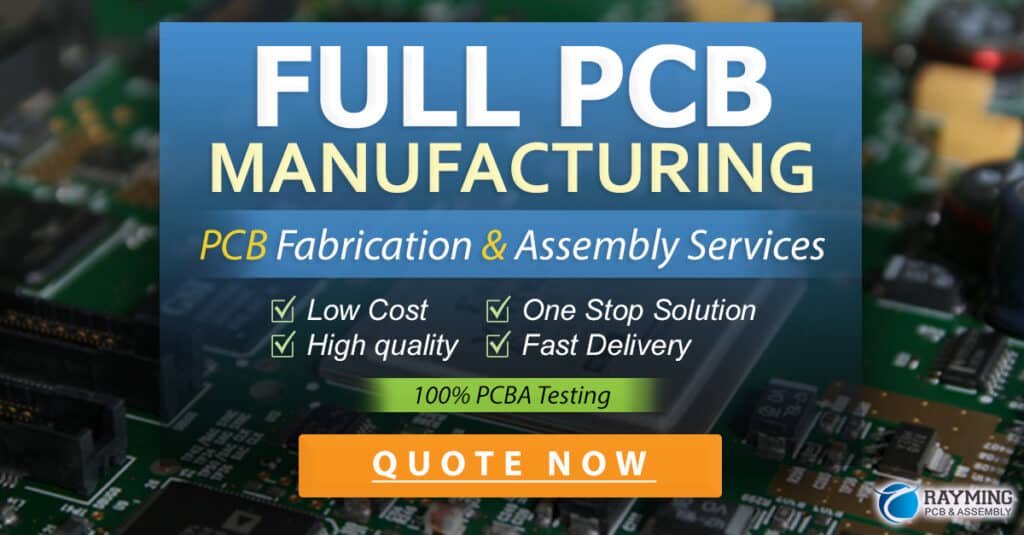
Cost Comparison: Subtractive vs Semi-Additive Manufacturing
The cost comparison between subtractive and semi-additive manufacturing depends on several factors, including part complexity, material, production volume, and available equipment.
Part Complexity and Geometry
Subtractive manufacturing excels at producing parts with simple to moderate complexity, while semi-additive manufacturing can be more cost-effective for parts with complex geometries, thin walls, and intricate features. The table below provides a general comparison:
Part Complexity | Subtractive Manufacturing | Semi-Additive Manufacturing |
---|---|---|
Simple | Cost-effective | Less cost-effective |
Moderate | Cost-effective | Comparable |
High | Less cost-effective | Cost-effective |
Material Considerations
The choice of material can impact the cost comparison between subtractive and semi-additive manufacturing. Some materials are more readily available and cost-effective for subtractive processes, while others may be better suited for semi-additive techniques.
Material | Subtractive Manufacturing | Semi-Additive Manufacturing |
---|---|---|
Aluminum | Cost-effective | Less common |
Steel | Cost-effective | Suitable |
Titanium | Expensive | Suitable |
Nickel Alloys | Expensive | Suitable |
Production Volume
The production volume can influence the cost-effectiveness of subtractive and semi-additive manufacturing. Subtractive manufacturing is generally more cost-effective for low to medium production volumes, while semi-additive manufacturing can be more economical for higher volumes due to its potential for automation and reduced material waste.
Production Volume | Subtractive Manufacturing | Semi-Additive Manufacturing |
---|---|---|
Low (1-100) | Cost-effective | Less cost-effective |
Medium (100-1000) | Cost-effective | Becoming more competitive |
High (1000+) | Less cost-effective | Cost-effective |
Equipment Availability and Investment
The availability and investment in equipment can impact the cost comparison. Companies with existing subtractive manufacturing equipment may find it more cost-effective to continue using those processes, while those investing in new equipment may consider semi-additive manufacturing for its potential benefits in certain applications.
Conclusion
The cost comparison between subtractive and semi-additive manufacturing depends on various factors, including part complexity, material, production volume, and equipment availability. Subtractive manufacturing is often more cost-effective for simple to moderately complex parts, traditional materials, and low to medium production volumes. Semi-additive manufacturing can be more economical for highly complex parts, advanced materials, and high production volumes.
Companies should carefully evaluate their specific requirements, existing equipment, and long-term goals when deciding between subtractive and semi-additive manufacturing. In some cases, a combination of both methods may provide the most cost-effective solution.
Frequently Asked Questions (FAQ)
1. What is the main difference between subtractive and semi-additive manufacturing?
Subtractive manufacturing involves removing material from a solid block to create the desired shape, while semi-additive manufacturing combines additive processes (material deposition) with subtractive processes (material removal) to produce parts.
2. Which manufacturing method is more suitable for complex part geometries?
Semi-additive manufacturing is generally more suitable for producing parts with complex geometries, thin walls, and intricate features. Subtractive manufacturing can be less cost-effective for highly complex parts due to the limitations of tool access and the need for multiple setups.
3. How does the choice of material affect the cost comparison between subtractive and semi-additive manufacturing?
The choice of material can impact the cost comparison. Some materials, such as aluminum and steel, are more cost-effective for subtractive manufacturing, while others, like titanium and nickel alloys, may be better suited for semi-additive processes.
4. Which manufacturing method is more cost-effective for high production volumes?
Semi-additive manufacturing can be more cost-effective for high production volumes due to its potential for automation and reduced material waste. Subtractive manufacturing may be less economical for large volumes due to longer machining times and higher material consumption.
5. Can subtractive and semi-additive manufacturing be used together?
Yes, in some cases, a combination of subtractive and semi-additive manufacturing methods may provide the most cost-effective solution. This approach allows companies to leverage the strengths of both processes, such as using semi-additive techniques for complex features and subtractive methods for simpler geometries or post-processing steps.
Leave a Reply