What is Copper Wrap Plating?
Copper wrap plating, also known as through-hole plating, is a process used in the manufacturing of printed circuit boards (PCBs) to create a conductive layer of copper on the walls of the drilled holes. This process is essential for creating reliable electrical connections between the different layers of a multi-layer PCB.
The Importance of Copper Wrap Plating
Copper wrap plating is crucial for several reasons:
- It ensures a reliable electrical connection between the different layers of a PCB.
- It provides mechanical strength to the PCB by reinforcing the drilled holes.
- It helps to prevent corrosion and oxidation of the exposed copper surfaces.
Without proper copper wrap plating, the reliability and longevity of a PCB can be significantly compromised.
The Copper Wrap Plating Process
The copper wrap plating process involves several steps, each of which is critical to ensuring a high-quality finished product.
Step 1: Drilling
The first step in the copper wrap plating process is drilling the holes in the PCB. These holes are used for mounting components and creating electrical connections between the different layers of the PCB.
Drill Bit Size (mm) | Hole Diameter (mm) |
---|---|
0.2 | 0.4 |
0.3 | 0.6 |
0.4 | 0.8 |
0.5 | 1.0 |
Step 2: Desmearing
After drilling, the holes must be cleaned to remove any debris or smear left behind by the drilling process. This step is called desmearing and is typically done using a chemical process or plasma etching.
Step 3: Electroless Copper Deposition
The next step is to deposit a thin layer of copper on the walls of the drilled holes using an electroless copper deposition process. This process involves immersing the PCB in a series of chemical baths that deposit a thin layer of copper on the exposed surfaces of the PCB, including the walls of the drilled holes.
Chemical Bath | Purpose |
---|---|
Cleaner/Conditioner | Removes contaminants and conditions the surface |
Microetch | Removes a thin layer of copper to improve adhesion |
Catalyst | Deposits a thin layer of palladium to initiate plating |
Electroless Copper | Deposits a thin layer of copper on the exposed surfaces |
Step 4: Electrolytic Copper Plating
After the electroless copper deposition, the PCB undergoes an electrolytic copper plating process to increase the thickness of the copper layer. This process involves immersing the PCB in an electrolytic copper plating bath and applying an electrical current to the PCB. The copper ions in the plating bath are attracted to the negatively charged PCB and deposit on the surfaces, including the walls of the drilled holes.
Parameter | Value |
---|---|
Current Density | 2-3 A/dm² |
Plating Time | 60-90 min |
Copper Thickness | 25-35 µm |
Bath Temperature | 25-30°C |
Step 5: Resist Stripping and Etching
After the electrolytic copper plating, the plating resist is stripped away, and the excess copper is etched using a chemical etching process. This process removes the unwanted copper, leaving only the desired copper patterns on the PCB.
Step 6: Inspection and Testing
The final step in the copper wrap plating process is inspection and testing. The PCB is visually inspected for any defects, and electrical tests are performed to ensure that the PCB meets the required specifications.
Benefits of Copper Wrap Plating
Copper wrap plating offers several benefits for PCB manufacturing:
-
Improved reliability: Copper wrap plating ensures a reliable electrical connection between the different layers of a PCB, reducing the risk of failures due to poor connections.
-
Increased mechanical strength: The copper plating reinforces the drilled holes, providing additional mechanical strength to the PCB.
-
Better thermal management: Copper is an excellent thermal conductor, helping to dissipate heat generated by the components on the PCB.
-
Enhanced signal integrity: Copper wrap plating helps to maintain signal integrity by providing a low-impedance path for high-frequency signals.
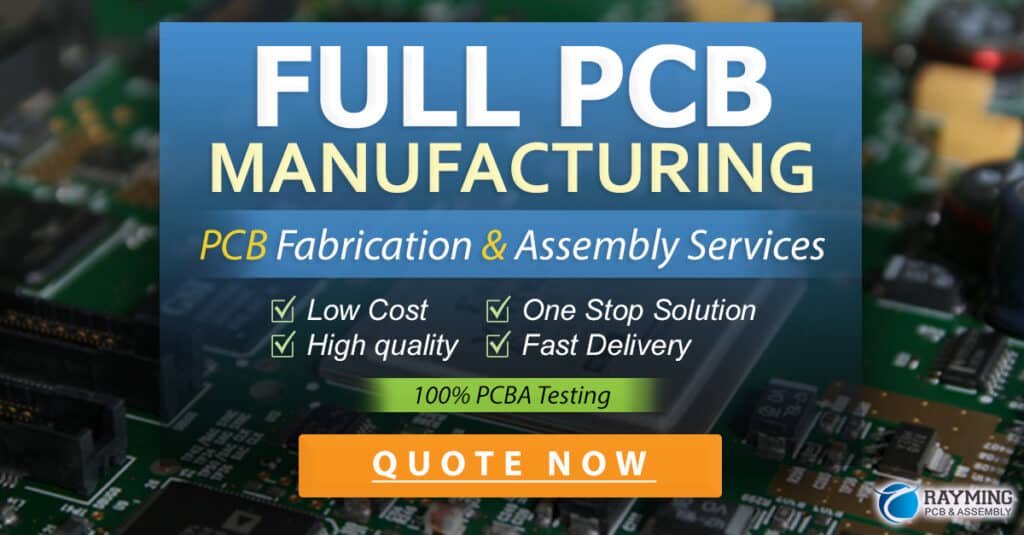
Challenges in Copper Wrap Plating
Despite its many benefits, copper wrap plating also presents some challenges:
-
Complexity: The copper wrap plating process is complex and requires specialized equipment and expertise.
-
Cost: The process can be costly, especially for high-volume production runs.
-
Environmental concerns: The chemical baths used in the copper wrap plating process can be harmful to the environment if not properly managed and disposed of.
Alternatives to Copper Wrap Plating
While copper wrap plating is the most common method for creating electrical connections in PCBs, there are some alternatives:
Press-Fit Connectors
Press-fit connectors are a mechanical alternative to copper wrap plating. These connectors are inserted into the drilled holes and create a mechanical connection between the different layers of the PCB.
Advantage | Disadvantage |
---|---|
Eliminates plating process | Higher cost compared to plated through-holes |
Faster assembly | Limited hole sizes and tolerances |
Easier repairs and rework | Requires specialized equipment for insertion |
Conductive Adhesives
Conductive adhesives are another alternative to copper wrap plating. These adhesives are applied to the walls of the drilled holes and create an electrical connection between the different layers of the PCB.
Advantage | Disadvantage |
---|---|
Lower cost than plating | Lower conductivity than copper |
Simpler process | Limited temperature stability |
Suitable for flexible PCBs | Requires careful process control |
FAQ
1. What is the difference between electroless and electrolytic copper plating?
Electroless copper plating is a chemical process that deposits a thin layer of copper on the exposed surfaces of the PCB without the use of an external electrical current. Electrolytic copper plating, on the other hand, uses an electrical current to deposit a thicker layer of copper on top of the electroless copper layer.
2. How thick is the copper layer after the wrap plating process?
The typical thickness of the copper layer after the wrap plating process is between 25 and 35 micrometers (µm).
3. Can copper wrap plating be used on flexible PCBs?
Yes, copper wrap plating can be used on flexible PCBs, but the process may need to be adapted to account for the unique properties of the flexible substrate.
4. What is the purpose of the desmearing step in the copper wrap plating process?
The desmearing step is used to remove any debris or smear left behind by the drilling process. This step is critical for ensuring good adhesion of the copper layer to the walls of the drilled holes.
5. How can the environmental impact of copper wrap plating be minimized?
The environmental impact of copper wrap plating can be minimized by properly managing and disposing of the chemical baths used in the process, as well as by implementing waste reduction and recycling strategies. Additionally, some manufacturers are exploring the use of more environmentally friendly alternative processes, such as conductive adhesives or press-fit connectors.
Conclusion
Copper wrap plating is a critical process in the manufacturing of high-quality PCBs. By creating a reliable electrical connection between the different layers of a PCB, copper wrap plating ensures the proper functioning and longevity of electronic devices. While the process can be complex and costly, the benefits it offers in terms of reliability, mechanical strength, and signal integrity make it an essential part of PCB manufacturing. As the electronics industry continues to evolve, it is likely that copper wrap plating will remain a key technology for the foreseeable future.
Leave a Reply