What is Copper Pour?
Copper pour, also known as copper fill or copper flooding, is a technique used in printed circuit board (PCB) layout where large areas of the PCB are filled with solid copper. This copper is connected to a specific net, usually ground (GND) or power (VCC), to provide a low-impedance path for current flow and to improve the overall electrical and thermal performance of the board.
Copper pour serves several purposes in PCB design:
-
Electrical shielding: Copper pour helps to shield sensitive signals from electromagnetic interference (EMI) by providing a low-impedance path for return currents.
-
Thermal management: Large areas of copper help to dissipate heat generated by components on the board, improving thermal performance.
-
Improved power distribution: Copper pour provides a low-impedance path for power distribution, reducing voltage drops and improving power integrity.
-
Mechanical stability: Copper pour can help to strengthen the PCB and reduce warping, especially for larger boards.
Types of Copper Pour
There are two main types of copper pour used in PCB layout:
-
Solid pour: In a solid pour, the entire area is filled with solid copper, with no gaps or voids. This provides the best electrical and thermal performance but can make it more difficult to route traces through the poured area.
-
Hatched pour: In a hatched pour, the area is filled with a pattern of copper traces, usually in a crosshatch or grid pattern. This allows for easier routing of traces through the poured area but may not provide as much shielding or thermal performance as a solid pour.
When to Use Copper Pour
Copper pour is typically used in the following scenarios:
-
High-speed designs: In high-speed designs, copper pour is essential for providing a low-impedance return path for signals and reducing EMI.
-
Power-hungry devices: Devices that consume a lot of power, such as FPGAs or processors, benefit from copper pour for improved power distribution and thermal management.
-
Analog circuits: Analog circuits, such as audio or RF designs, often require copper pour for shielding and to provide a stable reference plane.
-
Large boards: Larger PCBs benefit from copper pour for mechanical stability and to reduce warping.
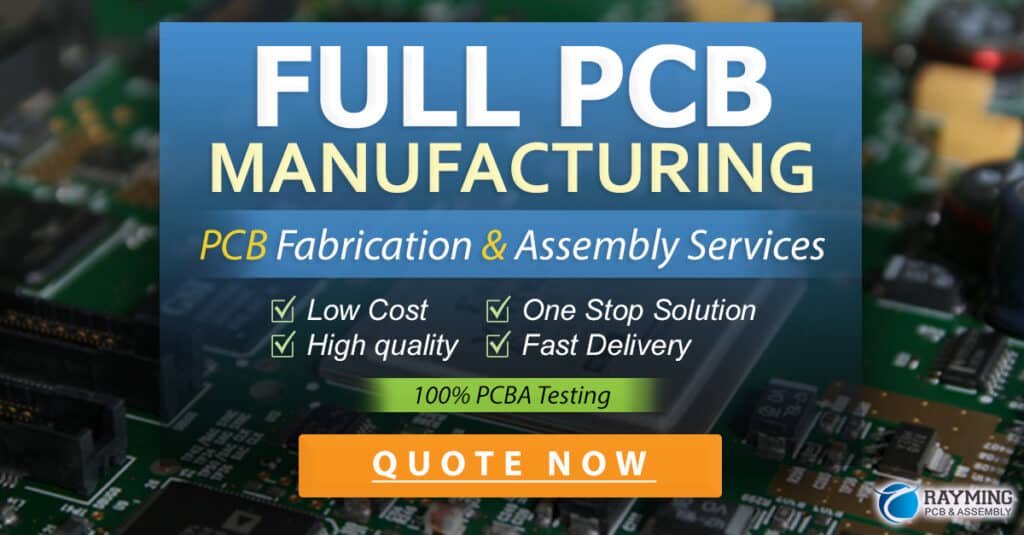
Copper Pour Best Practices
When using copper pour in PCB layout, there are several best practices to follow:
-
Use a solid pour whenever possible: Solid pours provide the best electrical and thermal performance, so use them whenever possible. Use hatched pours only when necessary for routing or manufacturing reasons.
-
Connect pour to a single net: Each copper pour should be connected to a single net, usually ground or power. Avoid connecting pours to multiple nets, as this can create unintended current paths and degrade performance.
-
Use thermal relief pads: When connecting components to a copper pour, use thermal relief pads to prevent heat from being drawn away from the component during soldering. Thermal relief pads are small traces that connect the component pad to the pour, allowing for better heat transfer during soldering.
-
Maintain proper clearance: Ensure that there is proper clearance between the copper pour and other features on the board, such as traces, vias, and components. The specific clearance requirements will depend on the manufacturing capabilities of your PCB fabricator.
-
Consider the impact on routing: Copper pour can make it more difficult to route traces through the poured area, especially for solid pours. Consider the impact on routing when deciding where to place copper pour on the board.
What is Stitching?
Stitching, also known as stitching vias or via stitching, is a technique used in PCB layout where a series of closely spaced vias are used to connect copper pour on different layers of the board. Stitching helps to improve the electrical and thermal performance of the board by providing a low-impedance path for current flow between layers.
Stitching serves several purposes in PCB design:
-
Improved EMI shielding: Stitching helps to improve EMI shielding by providing a continuous, low-impedance path for return currents between layers.
-
Better thermal management: Stitching helps to transfer heat between layers, improving the overall thermal performance of the board.
-
Enhanced power distribution: Stitching provides a low-impedance path for power distribution between layers, reducing voltage drops and improving power integrity.
-
Mechanical reinforcement: Stitching can help to reinforce the mechanical structure of the board, reducing warping and improving overall stability.
When to Use Stitching
Stitching is typically used in the following scenarios:
-
High-speed designs: In high-speed designs, stitching is essential for providing a low-impedance path for return currents and reducing EMI.
-
Multilayer boards: Stitching is particularly useful in multilayer boards, where it helps to connect copper pour on different layers and improve overall performance.
-
Power-hungry devices: Devices that consume a lot of power benefit from stitching for improved power distribution and thermal management.
-
Mechanically challenging designs: Boards that are subject to mechanical stress or vibration can benefit from stitching for added reinforcement and stability.
Stitching Best Practices
When using stitching in PCB layout, there are several best practices to follow:
-
Use a sufficient number of vias: The number of stitching vias required will depend on the size of the board and the specific performance requirements. As a general rule, use as many vias as practical to provide a low-impedance path between layers.
-
Space vias closely: Stitching vias should be spaced as closely as possible to provide a continuous, low-impedance path. The specific spacing will depend on the manufacturing capabilities of your PCB fabricator.
-
Use appropriate via sizes: The size of the stitching vias should be appropriate for the current carrying requirements and the manufacturing capabilities of your PCB fabricator. Larger vias can handle more current but may be more difficult to manufacture.
-
Consider the impact on routing: Stitching vias can make it more difficult to route traces through the area, especially if the vias are closely spaced. Consider the impact on routing when deciding where to place stitching vias on the board.
-
Balance performance and manufacturability: While more stitching vias generally provide better performance, there is a point of diminishing returns. Strike a balance between performance and manufacturability to ensure that the board can be reliably and cost-effectively produced.
Combining Copper Pour and Stitching
Copper pour and stitching are often used together in PCB layout to provide the best possible electrical and thermal performance. By combining these techniques, designers can create a continuous, low-impedance path for current flow and heat dissipation across the entire board.
When combining copper pour and stitching, follow these guidelines:
-
Use stitching to connect pour on different layers: Stitching vias should be used to connect copper pour on different layers of the board, providing a low-impedance path between layers.
-
Place stitching vias strategically: Stitching vias should be placed strategically to provide the most effective connection between layers. This may involve placing vias along the edges of the pour or in a grid pattern across the pour.
-
Consider the impact on manufacturing: The combination of copper pour and stitching can make the board more complex and difficult to manufacture. Consider the impact on manufacturing when deciding how to combine these techniques.
-
Simulate and test the design: Before finalizing the design, simulate and test the board to ensure that the combination of copper pour and stitching provides the desired electrical and thermal performance.
FAQ
1. Is copper pour always necessary in PCB layout?
No, copper pour is not always necessary in PCB layout. The decision to use copper pour depends on the specific requirements of the design, such as EMI shielding, thermal management, and power distribution needs. In some cases, a design may not require copper pour at all.
2. Can copper pour be used on both sides of the board?
Yes, copper pour can be used on both sides of the board. In fact, it is common to use copper pour on both the top and bottom layers of the board to provide shielding and improve overall performance.
3. How does the thickness of the copper pour affect performance?
The thickness of the copper pour, also known as the copper weight, affects the electrical and thermal performance of the board. Thicker copper pour provides better conductivity and heat dissipation but may be more expensive and difficult to manufacture. The specific copper weight required will depend on the current carrying requirements and thermal demands of the design.
4. Can stitching vias be used with through-hole components?
Yes, stitching vias can be used with through-hole components. However, the vias should be placed strategically to avoid interfering with the component leads and to ensure proper soldering. In some cases, it may be necessary to use thermal relief pads to connect the component to the copper pour.
5. How do you determine the appropriate spacing for stitching vias?
The appropriate spacing for stitching vias depends on several factors, including the current carrying requirements, the size of the vias, and the manufacturing capabilities of the PCB fabricator. As a general rule, stitching vias should be spaced as closely as possible while still allowing for reliable manufacturing. The specific spacing requirements can be determined through simulation and testing, as well as consultation with the PCB fabricator.
Conclusion
Copper pour and stitching are powerful techniques for improving the electrical and thermal performance of PCBs. By providing a low-impedance path for current flow and heat dissipation, these techniques can help to reduce EMI, improve power integrity, and enhance overall reliability.
When using copper pour and stitching in PCB layout, it is important to follow best practices and consider the impact on manufacturing. By carefully balancing performance and manufacturability, designers can create boards that are both highly functional and cost-effective to produce.
Ultimately, the decision to use copper pour and stitching depends on the specific requirements of the design. By understanding the benefits and limitations of these techniques, and by following best practices in implementation, designers can effectively leverage copper pour and stitching to create high-performance PCBs that meet the demands of today’s complex electronic systems.
Technique | Benefits | Considerations |
---|---|---|
Copper Pour | – EMI shielding – Thermal management – Improved power distribution – Mechanical stability |
– Can make routing more difficult – Must be connected to a single net – Requires proper clearance from other features |
Stitching | – Improved EMI shielding – Better thermal management – Enhanced power distribution – Mechanical reinforcement |
– Can make routing more difficult – Requires sufficient number and spacing of vias – Must balance performance and manufacturability |
By carefully considering the benefits and limitations of copper pour and stitching, and by following best practices in implementation, designers can create high-performance PCBs that meet the demands of today’s complex electronic systems.
Leave a Reply