Introduction
Copper is a critical material in the electronics industry due to its excellent electrical and thermal conductivity properties. It is widely used in printed circuit boards (PCBs), wires, cables, and other electronic components. However, the rising cost of copper and the increasing demand for more compact and efficient electronic devices have led to a focus on copper efficiency in electronics design and manufacturing.
The Role of Copper in Electronics
Electrical Conductivity
Copper is the second-best electrical conductor among metals, surpassed only by silver. Its high electrical conductivity allows for efficient transmission of electrical signals and power throughout electronic devices. The electrical resistivity of copper is 1.68 × 10⁻⁸ Ω·m at 20°C, making it an ideal choice for low-resistance applications.
Thermal Conductivity
In addition to its excellent electrical conductivity, copper also has high thermal conductivity. This property enables efficient heat dissipation in electronic devices, preventing overheating and ensuring reliable operation. Copper’s thermal conductivity is 401 W/(m·K) at room temperature, which is significantly higher than most other metals used in electronics.
Mechanical Properties
Copper possesses good mechanical properties, including high ductility, malleability, and tensile strength. These properties allow for easy forming, shaping, and machining of copper components in electronics manufacturing. Copper’s mechanical properties also contribute to the durability and reliability of electronic devices.
Copper Efficiency in PCB Design
Trace Width and Thickness
One of the key factors in optimizing copper efficiency in PCB design is the proper selection of trace widths and thicknesses. Thinner traces allow for more compact designs and reduced copper usage, but they also have higher resistance and lower current-carrying capacity. Designers must strike a balance between copper efficiency and electrical performance when determining trace dimensions.
The following table provides a general guideline for trace width and thickness based on current requirements:
Current (A) | Trace Width (mm) | Trace Thickness (oz) |
---|---|---|
0.5 | 0.2 | 0.5 |
1.0 | 0.3 | 0.7 |
2.0 | 0.5 | 1.0 |
3.0 | 0.8 | 1.2 |
5.0 | 1.2 | 2.0 |
Via Optimization
Vias are essential for connecting traces on different layers of a PCB, but they also consume valuable board space and add to the overall copper usage. Optimizing via design can significantly improve copper efficiency in PCBs. Strategies for via optimization include:
- Minimizing the number of vias by careful routing and layer stackup planning
- Using smaller via diameters and pad sizes when possible
- Implementing via-in-pad design to reduce board space consumption
- Utilizing blind and buried vias to minimize the impact on other layers
Copper Thieving
Copper thieving is a technique used to balance the copper distribution on a PCB layer, reducing the risk of warpage and improving manufacturability. However, excessive copper thieving can lead to increased copper usage and higher production costs. To optimize copper efficiency, designers should:
- Use copper thieving only when necessary to meet manufacturing requirements
- Minimize the size and number of copper thieving patterns
- Consider alternative methods, such as strategic component placement or using a thicker base material, to minimize the need for copper thieving
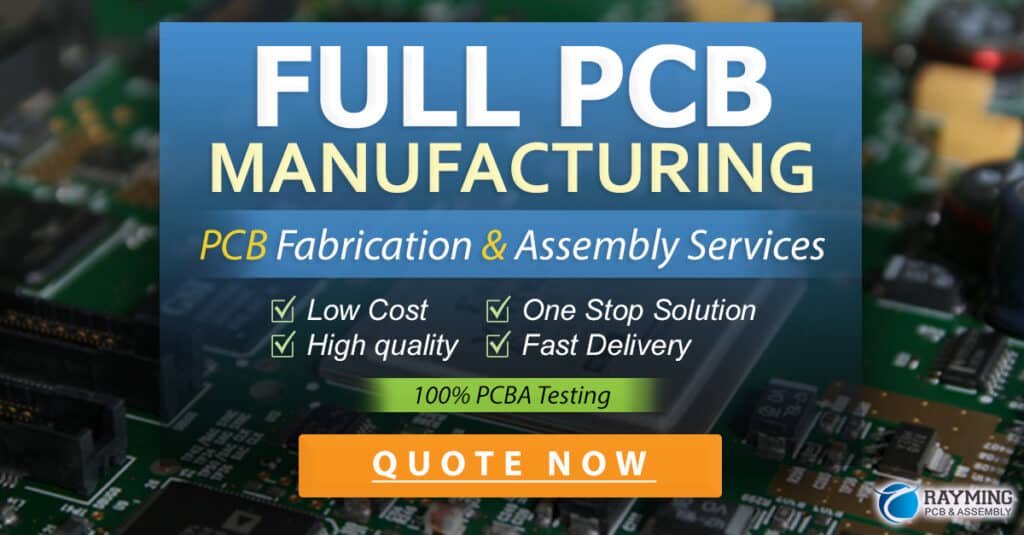
Copper Efficiency in Electronics Manufacturing
Copper Clad Laminate Selection
The choice of copper clad laminate (CCL) has a significant impact on copper efficiency in electronics manufacturing. Thinner copper foils allow for more compact designs and reduced copper usage, but they also have lower current-carrying capacity and may be more susceptible to damage during handling and assembly.
The following table lists common copper foil thicknesses and their typical applications:
Copper Foil Thickness (oz) | Typical Applications |
---|---|
0.5 | Low-power, high-density PCBs |
1.0 | General-purpose PCBs, moderate power applications |
2.0 | High-power applications, automotive electronics |
3.0 | Very high-power applications, heavy copper PCBs |
Copper Recycling and Recovery
Copper recycling and recovery play a crucial role in improving copper efficiency and reducing waste in electronics manufacturing. Copper can be recovered from various sources, including:
- PCB manufacturing scrap, such as etching solutions and copper foils
- End-of-life electronic devices and components
- Manufacturing process by-products, such as copper dust and shavings
Implementing effective copper recycling and recovery processes can help reduce the environmental impact of electronics manufacturing and lower the overall cost of copper usage.
Design for Manufacturing (DFM)
Designing electronic products with manufacturing in mind can significantly improve copper efficiency and reduce production costs. Some DFM strategies for optimizing copper usage include:
- Standardizing component sizes and layouts to minimize custom tooling and processes
- Designing PCBs with uniform copper distribution to reduce the need for copper balancing
- Optimizing panelization to maximize material utilization and minimize waste
- Collaborating with manufacturing partners early in the design process to identify opportunities for copper efficiency improvements
Emerging Trends and Technologies
High-Density Interconnect (HDI) PCBs
HDI PCBs feature finer trace widths, smaller via sizes, and higher layer counts compared to traditional PCBs. These advanced design techniques allow for more compact and efficient copper usage, enabling the development of smaller and more powerful electronic devices. HDI PCBs are increasingly being adopted in applications such as smartphones, wearables, and IoT devices.
Copper Mesh Shielding
Copper mesh shielding is an innovative approach to electromagnetic interference (EMI) shielding that offers several advantages over traditional solid copper shields. By using a mesh pattern instead of a solid sheet, copper mesh shields provide effective EMI protection while reducing copper usage and weight. This technology is particularly promising for applications in the automotive and aerospace industries, where weight reduction is a critical concern.
Additive Manufacturing
Additive manufacturing, also known as 3D printing, is an emerging technology that has the potential to revolutionize electronics manufacturing and improve copper efficiency. By selectively depositing copper material only where needed, additive manufacturing techniques can significantly reduce copper waste and enable the creation of complex, high-performance electronic components. As the technology matures, additive manufacturing is expected to play an increasingly important role in the electronics industry.
FAQ
Q1: What are the main factors affecting copper efficiency in electronics design?
A1: The main factors affecting copper efficiency in electronics design include trace width and thickness, via optimization, copper thieving, and the selection of appropriate copper clad laminates. Designers must balance copper efficiency with electrical performance, manufacturability, and cost considerations.
Q2: How does copper recycling contribute to improving copper efficiency in electronics manufacturing?
A2: Copper recycling helps improve copper efficiency by reducing the need for virgin copper and minimizing waste in the manufacturing process. By recovering copper from PCB manufacturing scrap, end-of-life electronic devices, and process by-products, manufacturers can lower their overall copper consumption and production costs.
Q3: What are HDI PCBs, and how do they improve copper efficiency?
A3: High-Density Interconnect (HDI) PCBs are advanced printed circuit boards that feature finer trace widths, smaller via sizes, and higher layer counts compared to traditional PCBs. These design techniques allow for more compact and efficient copper usage, enabling the development of smaller and more powerful electronic devices.
Q4: How can additive manufacturing techniques help improve copper efficiency in electronics manufacturing?
A4: Additive manufacturing techniques, such as 3D printing, can improve copper efficiency by selectively depositing copper material only where needed. This approach significantly reduces copper waste and enables the creation of complex, high-performance electronic components that would be difficult or impossible to produce using traditional manufacturing methods.
Q5: What role does Design for Manufacturing (DFM) play in optimizing copper efficiency?
A5: Design for Manufacturing (DFM) plays a crucial role in optimizing copper efficiency by considering the manufacturing process during the product design phase. DFM strategies, such as standardizing component sizes and layouts, optimizing panelization, and collaborating with manufacturing partners, can help reduce copper usage, minimize waste, and lower production costs.
Conclusion
Copper efficiency is a critical consideration in electronics design and manufacturing, as it directly impacts product performance, cost, and environmental sustainability. By adopting strategies such as trace optimization, via minimization, copper recycling, and Design for Manufacturing, the electronics industry can significantly improve copper efficiency and reduce its environmental footprint.
As new technologies and trends, such as HDI PCBs, copper mesh shielding, and additive manufacturing, continue to emerge, the potential for further copper efficiency improvements grows. By staying at the forefront of these developments and prioritizing copper efficiency in their design and manufacturing processes, electronics companies can create more compact, cost-effective, and eco-friendly products that meet the evolving needs of consumers and businesses alike.
Leave a Reply