Introduction to Copper Panels and Their Importance
Copper panels are widely used in various industries due to their excellent electrical and thermal conductivity, corrosion resistance, and durability. These panels play a crucial role in the manufacturing of electronic devices, printed circuit boards (PCBs), and other applications where efficient heat dissipation and electrical conductivity are essential. The distribution of copper on a panel is a critical factor that determines its performance and reliability.
Key Characteristics of Copper Panels
Copper panels possess several key characteristics that make them ideal for various applications:
- High electrical conductivity
- Excellent thermal conductivity
- Corrosion resistance
- Malleability and ductility
- Antimicrobial properties
These properties enable copper panels to be used in a wide range of industries, including:
- Electronics
- Telecommunications
- Automotive
- Aerospace
- Construction
Factors Affecting Copper Distribution on a Panel
The distribution of copper on a panel is influenced by several factors, which can impact its performance and functionality. Understanding these factors is crucial for optimizing the design and manufacturing process of copper panels.
Panel Thickness and Copper Weight
The thickness of the panel and the weight of the copper used play a significant role in determining the distribution of copper on the panel. Thicker panels with higher copper weights generally have a more uniform copper distribution compared to thinner panels with lower copper weights.
Panel Thickness (mm) | Copper Weight (oz/ft²) | Copper Distribution Uniformity |
---|---|---|
0.5 | 0.5 | Low |
1.0 | 1.0 | Medium |
1.5 | 2.0 | High |
2.0 | 3.0 | Very High |
Manufacturing Process and Techniques
The manufacturing process and techniques used to produce copper panels can also influence the distribution of copper. Some common manufacturing methods include:
- Electroplating
- Foil lamination
- Sputtering
- Chemical vapor deposition (CVD)
Each method has its advantages and disadvantages, and the choice of manufacturing process depends on the specific requirements of the application and the desired copper distribution.
Surface Treatments and Finishes
Surface treatments and finishes applied to copper panels can affect the distribution of copper. These treatments are used to enhance the panel’s properties, such as corrosion resistance, solderability, and adhesion. Some common surface treatments and finishes include:
- Oxide treatment
- ENIG (Electroless Nickel Immersion Gold)
- HASL (Hot Air Solder Leveling)
- OSP (Organic Solderability Preservative)
The choice of surface treatment or finish depends on the specific requirements of the application and the desired copper distribution.
Measuring and Analyzing Copper Distribution
To ensure the optimal performance and reliability of copper panels, it is essential to measure and analyze the distribution of copper accurately. Several techniques and tools are available for this purpose.
Microscopic Analysis
Microscopic analysis involves using high-magnification microscopes to examine the surface of the copper panel. This technique allows for the identification of any irregularities or defects in the copper distribution, such as voids, cracks, or uneven plating.
X-Ray Fluorescence (XRF) Spectroscopy
X-Ray Fluorescence (XRF) spectroscopy is a non-destructive technique that measures the thickness and composition of the copper layer on the panel. XRF spectroscopy works by exciting the atoms in the copper layer with high-energy X-rays and analyzing the fluorescent X-rays emitted by the atoms. This technique provides accurate and reliable measurements of the copper distribution across the panel.
Electrical Resistance Measurements
Electrical resistance measurements can be used to assess the uniformity of copper distribution on a panel. By measuring the electrical resistance at different points on the panel, any variations in the copper thickness or conductivity can be detected. This method is particularly useful for identifying areas with insufficient or excessive copper plating.
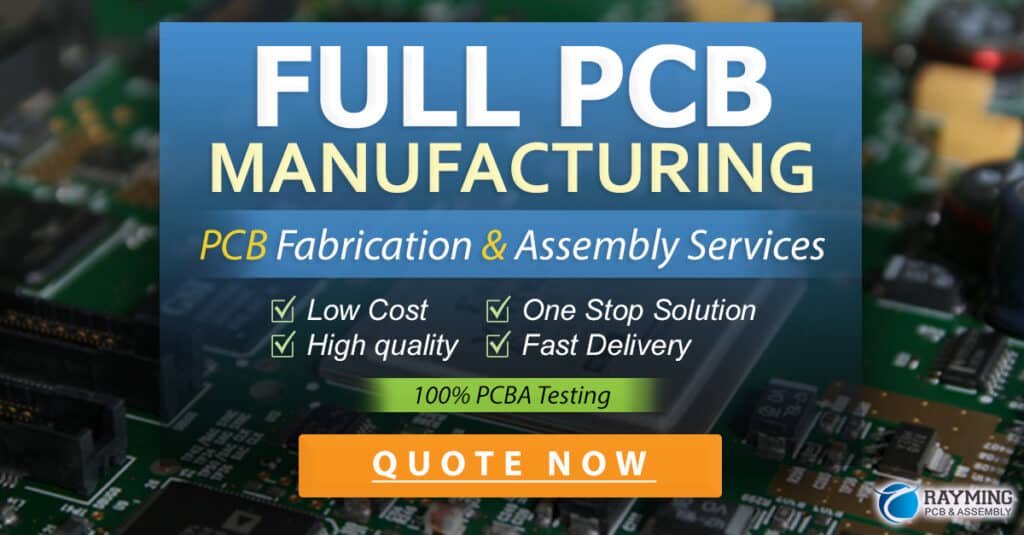
Optimizing Copper Distribution for Specific Applications
Different applications may require specific copper distribution patterns to achieve optimal performance and functionality. Some examples of application-specific copper distribution requirements include:
High-Frequency PCBs
High-frequency PCBs, such as those used in 5G communication devices, require a highly uniform copper distribution to minimize signal loss and ensure consistent electrical properties. In these applications, the copper thickness and surface roughness must be carefully controlled to achieve the desired performance.
High-Power Electronics
High-power electronic devices, such as power converters and motor drives, generate significant amounts of heat that must be dissipated efficiently. Copper panels with a uniform and thick copper distribution are essential for effective thermal management in these applications. The copper distribution must be optimized to ensure adequate heat spreading and minimize thermal hotspots.
Flexible Electronics
Flexible electronics, such as wearable devices and flexible displays, require copper panels that can withstand repeated bending and stretching without cracking or delaminating. In these applications, the copper distribution must be designed to accommodate the mechanical stresses associated with flexing, while maintaining good electrical conductivity and connectivity.
Challenges and Future Developments in Copper Panel Technology
As the demand for high-performance electronic devices continues to grow, the requirements for copper panels are becoming increasingly stringent. Some of the challenges and future developments in copper panel technology include:
Miniaturization and High-Density Interconnects
The trend towards miniaturization and high-density interconnects in electronic devices presents challenges for copper panel manufacturing. As feature sizes decrease and circuit density increases, maintaining a uniform and reliable copper distribution becomes more difficult. Advanced manufacturing techniques, such as semi-additive processes (SAP) and modified semi-additive processes (mSAP), are being developed to address these challenges.
Advanced Materials and Coatings
Researchers are exploring new materials and coatings that can enhance the performance and functionality of copper panels. For example, graphene-based coatings have been shown to improve the thermal conductivity and corrosion resistance of copper panels. Other materials, such as carbon nanotubes and metal-matrix composites, are also being investigated for their potential applications in copper panel technology.
Sustainable and Eco-Friendly Manufacturing
As environmental concerns continue to grow, there is an increasing focus on developing sustainable and eco-friendly manufacturing processes for copper panels. This includes the use of recycled copper, the reduction of hazardous chemicals in the manufacturing process, and the development of biodegradable or recyclable substrate materials.
Frequently Asked Questions (FAQ)
-
Q: What is the importance of copper distribution on a panel?
A: Copper distribution on a panel is crucial for ensuring optimal electrical and thermal conductivity, as well as the overall performance and reliability of the device or application in which the panel is used. -
Q: How does panel thickness affect copper distribution?
A: Thicker panels generally have a more uniform copper distribution compared to thinner panels, as the increased thickness allows for a more even distribution of the copper layer. -
Q: What are some common surface treatments and finishes applied to copper panels?
A: Common surface treatments and finishes include oxide treatment, ENIG (Electroless Nickel Immersion Gold), HASL (Hot Air Solder Leveling), and OSP (Organic Solderability Preservative). These treatments enhance the panel’s properties, such as corrosion resistance, solderability, and adhesion. -
Q: How can copper distribution be measured and analyzed?
A: Copper distribution can be measured and analyzed using techniques such as microscopic analysis, X-Ray Fluorescence (XRF) spectroscopy, and electrical resistance measurements. These methods help identify irregularities, defects, and variations in the copper distribution. -
Q: What are some challenges and future developments in copper panel technology?
A: Challenges include miniaturization and high-density interconnects, which require advanced manufacturing techniques to maintain uniform and reliable copper distribution. Future developments involve the exploration of new materials and coatings, such as graphene-based coatings, and the development of sustainable and eco-friendly manufacturing processes.
Conclusion
Copper distribution on a panel is a critical factor that determines the performance, reliability, and functionality of various electronic devices and applications. Understanding the factors that influence copper distribution, such as panel thickness, manufacturing processes, and surface treatments, is essential for optimizing the design and production of copper panels.
As the demand for high-performance electronic devices continues to grow, the requirements for copper panels are becoming increasingly stringent. Challenges such as miniaturization and high-density interconnects must be addressed through advanced manufacturing techniques and the exploration of new materials and coatings.
Moreover, the development of sustainable and eco-friendly manufacturing processes for copper panels is becoming increasingly important as environmental concerns continue to grow. By addressing these challenges and embracing new technologies, the copper panel industry can continue to innovate and meet the evolving needs of the electronics industry.
Leave a Reply