Introduction to Copper Current Density Simulations
Copper current density simulations are an essential tool for engineers and designers working on electrical systems. These simulations help predict the behavior of copper conductors under various electrical loads, ensuring the safe and efficient operation of the system. In this article, we’ll explore the basics of copper current density simulations and discuss a quick and dirty approach to performing these simulations.
What is Current Density?
Current density is a measure of the electric current flowing through a unit area of a conductor. It is expressed in units of amperes per square meter (A/m²). The current density in a conductor is determined by the applied voltage, the conductor’s material properties, and its cross-sectional area.
Material | Resistivity (Ω·m) | Current Density (A/m²) |
---|---|---|
Copper | 1.68 × 10⁻⁸ | 5.95 × 10⁷ |
Aluminum | 2.82 × 10⁻⁸ | 3.55 × 10⁷ |
Gold | 2.44 × 10⁻⁸ | 4.10 × 10⁷ |
Importance of Current Density Simulations
Current density simulations are crucial for several reasons:
-
Safety: High current densities can lead to excessive heating, which may cause damage to the conductor or surrounding materials. Simulations help identify potential hotspots and ensure that the system operates within safe limits.
-
Efficiency: Optimizing current density can minimize power losses due to resistive heating, leading to more efficient electrical systems.
-
Reliability: By predicting the behavior of conductors under various conditions, simulations help designers create more reliable electrical systems that can withstand the intended operating conditions.
The Quick and Dirty Approach to Copper Current Density Simulations
While there are sophisticated software packages available for performing detailed current density simulations, sometimes a quick and dirty approach can provide valuable insights without the need for complex tools. Here’s a step-by-step guide to performing a basic copper current density simulation:
Step 1: Define the Conductor Geometry
The first step is to define the geometry of the copper conductor. This includes specifying the cross-sectional area, length, and any relevant geometric features such as bends or holes. For simple geometries, you can calculate the cross-sectional area using basic formulas:
- Circular cross-section: A = πr², where r is the radius
- Rectangular cross-section: A = width × height
Step 2: Determine the Electrical Properties
Next, you’ll need to determine the electrical properties of the copper conductor. The most important property for current density simulations is the electrical resistivity (ρ). For copper, the resistivity at room temperature is approximately 1.68 × 10⁻⁸ Ω·m.
Step 3: Calculate the Current Density
To calculate the current density (J), you’ll need to know the applied current (I) and the cross-sectional area (A) of the conductor. The current density is given by:
J = I / A
For example, if a current of 10 A is flowing through a copper wire with a cross-sectional area of 1 mm², the current density would be:
J = 10 A / (1 × 10⁻⁶ m²) = 10⁷ A/m²
Step 4: Evaluate the Results
Once you’ve calculated the current density, you can compare it to the maximum allowable current density for the conductor. The maximum allowable current density depends on factors such as the conductor’s insulation, ambient temperature, and cooling conditions. As a general rule of thumb, a current density of 5 × 10⁶ A/m² is considered safe for most copper conductors.
If the calculated current density exceeds the maximum allowable value, you may need to consider modifying the conductor geometry, reducing the applied current, or improving the cooling conditions to ensure safe operation.
Advanced Techniques for Copper Current Density Simulations
While the quick and dirty approach can provide useful insights, more advanced techniques are available for performing detailed copper current density simulations. These techniques often involve the use of specialized software packages that can model complex geometries, account for temperature effects, and simulate transient behavior.
Finite Element Analysis (FEA)
Finite Element Analysis (FEA) is a powerful numerical method for solving complex engineering problems, including current density simulations. FEA involves dividing the conductor geometry into small elements and solving the governing equations for each element. This allows for the accurate modeling of complex geometries and the inclusion of various physical phenomena such as heat transfer and magnetic fields.
Several commercial FEA software packages, such as ANSYS and COMSOL Multiphysics, offer dedicated modules for electrical and thermal simulations. These tools provide a user-friendly interface for setting up and running simulations, as well as post-processing and visualizing the results.
Multiphysics Simulations
In many cases, current density simulations need to account for the coupling between electrical, thermal, and mechanical phenomena. For example, high current densities can lead to temperature rises, which in turn affect the electrical properties of the conductor. Multiphysics simulations allow for the simultaneous modeling of these coupled effects, providing a more accurate representation of the system’s behavior.
Multiphysics simulations often require the use of specialized software packages that can handle the coupling between different physical domains. These tools typically offer a range of numerical methods, such as FEA and computational fluid dynamics (CFD), to solve the governing equations.
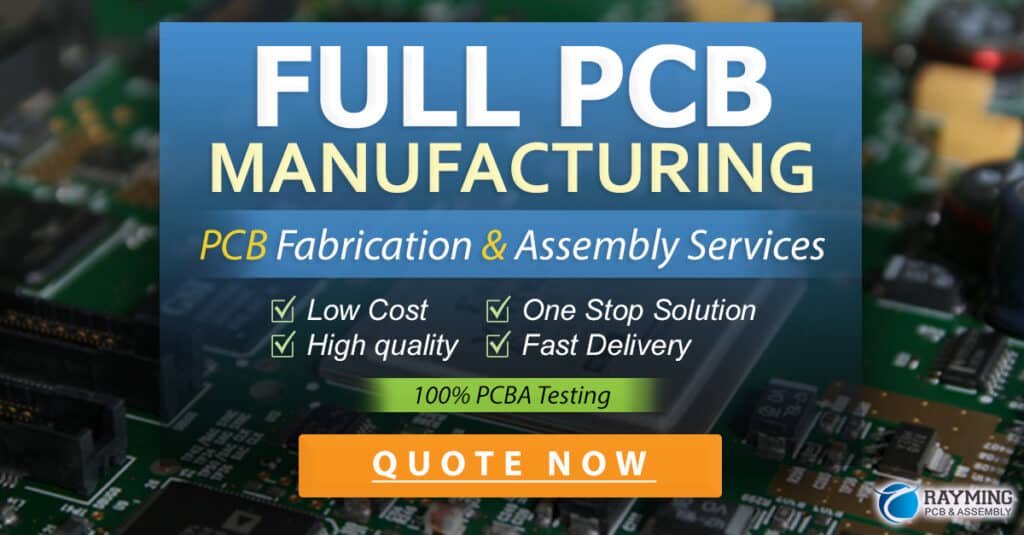
Case Study: Optimizing Current Density in a Copper Busbar
To illustrate the application of copper current density simulations, let’s consider a case study involving the optimization of a copper busbar. Busbars are thick strips of copper used to distribute high currents in electrical systems, such as in switchgear and power distribution panels.
Problem Statement
A designer is tasked with optimizing a copper busbar for a new power distribution panel. The busbar must carry a current of 1000 A and maintain a maximum temperature rise of 30°C above ambient. The designer wants to minimize the cross-sectional area of the busbar to reduce material costs while ensuring safe operation.
Simulation Setup
To optimize the busbar design, the designer decides to use a multiphysics simulation software package. The software allows for the coupled modeling of electrical and thermal phenomena, taking into account the temperature-dependent resistivity of copper.
The designer creates a 3D model of the busbar geometry and specifies the relevant material properties, such as the electrical resistivity and thermal conductivity of copper. The model is then meshed using a suitable element size to ensure accurate results.
Boundary Conditions and Loads
The designer applies the appropriate boundary conditions and loads to the model:
- A current of 1000 A is applied to one end of the busbar, with the other end set as the ground.
- The ambient temperature is set to 25°C, and convective heat transfer coefficients are applied to the busbar surfaces to model cooling by natural convection.
Simulation Results
After running the simulation, the designer analyzes the results to determine the optimal busbar geometry. The software provides visualizations of the current density distribution and temperature profile within the busbar.
The designer iterates on the busbar geometry, adjusting the cross-sectional area and shape until the maximum temperature rise is within the specified limit of 30°C. The optimized design achieves a current density of 4.5 × 10⁶ A/m², which is below the safe limit for copper conductors.
Implementation and Validation
With the optimized busbar geometry determined through simulations, the designer proceeds to create detailed manufacturing drawings and specifications. The busbar is then fabricated and installed in the power distribution panel.
To validate the simulation results, the designer measures the temperature of the busbar during operation using infrared thermography. The measured temperature rise closely matches the predicted value from the simulation, confirming the accuracy of the model.
Frequently Asked Questions (FAQ)
-
What is the maximum safe current density for copper conductors?
The maximum safe current density for copper conductors depends on various factors, such as insulation, ambient temperature, and cooling conditions. As a general rule of thumb, a current density of 5 × 10⁶ A/m² is considered safe for most applications. -
Can copper current density simulations account for temperature effects?
Yes, advanced copper current density simulations can account for temperature effects by considering the temperature-dependent resistivity of copper. Multiphysics simulation software packages often provide the ability to model coupled electrical and thermal phenomena. -
How can I determine the appropriate boundary conditions for my simulation?
Determining the appropriate boundary conditions requires a good understanding of the physical system being modeled. Consider factors such as the applied current or voltage, grounding points, and cooling conditions. Consult with experienced engineers or refer to relevant standards and guidelines when setting boundary conditions. -
What are some common applications of copper current density simulations?
Copper current density simulations are widely used in the design of electrical systems, such as power distribution networks, transformers, motors, and generators. They are also valuable in the development of electronic devices, printed circuit boards, and heat sinks. -
How can I validate the results of my copper current density simulation?
Validating simulation results often involves comparing them with experimental measurements or data from similar systems. Methods such as infrared thermography, voltage and current measurements, and temperature sensors can be used to collect experimental data for validation purposes. It’s essential to consider the uncertainties and limitations of both the simulation and experimental methods when validating results.
Conclusion
Copper current density simulations are a valuable tool for engineers and designers working on electrical systems. By predicting the behavior of copper conductors under various electrical loads, these simulations help ensure the safe, efficient, and reliable operation of the system.
While the quick and dirty approach outlined in this article can provide useful insights, advanced techniques such as FEA and multiphysics simulations offer more accurate and comprehensive results. These simulations can account for complex geometries, temperature effects, and coupled physical phenomena, providing a detailed understanding of the system’s behavior.
As demonstrated in the case study, copper current density simulations can be used to optimize conductor designs, minimizing material costs while ensuring safe operation. By combining simulations with experimental validation, designers can create robust and reliable electrical systems that meet the demands of modern applications.
Leave a Reply