Introduction to High Frequency PCB Design
High frequency PCB design is a crucial aspect of modern electronics, particularly in the fields of telecommunications, radar systems, and high-speed digital circuits. As the demand for faster data transmission and higher bandwidth continues to grow, designers face numerous challenges in ensuring optimal performance and signal integrity. One of the key factors that significantly impact the efficiency and reliability of high frequency PCBs is the choice of copper and its utilization in the design process.
The Role of Copper in High Frequency PCBs
Copper is the most commonly used conductor material in PCB manufacturing due to its excellent electrical and thermal conductivity, as well as its cost-effectiveness. In high frequency applications, copper plays a vital role in:
- Signal transmission
- Power distribution
- Heat dissipation
- Electromagnetic shielding
However, the choice of copper and its implementation in the design process can greatly affect the overall performance and efficiency of the PCB.
Copper Thickness and Skin Effect
Understanding Skin Effect
At high frequencies, the skin effect becomes a significant factor in determining the resistance and inductance of copper traces. The skin effect is a phenomenon where the electric current tends to flow primarily on the outer surface (skin) of a conductor, rather than uniformly throughout its cross-section. This effect becomes more pronounced as the frequency increases, leading to a reduction in the effective cross-sectional area of the conductor and an increase in its resistance.
The skin depth (δ) is a measure of how far the current penetrates into the conductor, and it is given by the following formula:
δ = √(ρ / (π * f * μ))
Where:
– ρ is the resistivity of the conductor material
– f is the frequency of the signal
– μ is the permeability of the conductor material
Choosing the Right Copper Thickness
To minimize the impact of skin effect and ensure optimal signal transmission, it is crucial to select the appropriate copper thickness for high frequency PCBs. The copper thickness should be chosen based on the following factors:
- Frequency of operation
- Current carrying requirements
- Thermal management needs
- Manufacturing constraints
As a general rule of thumb, the copper thickness should be at least three times the skin depth at the highest operating frequency to ensure that the majority of the current flows through the conductor. However, increasing the copper thickness beyond this point may not provide significant benefits and can lead to increased manufacturing costs and design complexity.
Frequency (MHz) | Skin Depth (μm) | Recommended Copper Thickness (μm) |
---|---|---|
10 | 20.6 | 62 |
100 | 6.6 | 20 |
1000 | 2.1 | 6 |
10000 | 0.66 | 2 |
Table 1: Recommended copper thickness for different operating frequencies
Copper Surface Roughness and Losses
Impact of Surface Roughness on Signal Integrity
In addition to copper thickness, the surface roughness of the copper traces can also have a significant impact on signal integrity and losses in high frequency PCBs. At high frequencies, the skin effect confines the current flow to a thin layer near the surface of the conductor. As a result, any irregularities or roughness on the copper surface can lead to increased resistance and losses.
The surface roughness of copper is typically measured using the Root Mean Square (RMS) value, which represents the average deviation of the surface from a perfectly smooth plane. A higher RMS value indicates a rougher surface, which can result in greater signal attenuation and distortion.
Choosing the Right Copper Surface Finish
To minimize the impact of surface roughness on signal integrity, it is essential to select the appropriate copper surface finish for high frequency PCBs. Some common surface finishes used in high frequency applications include:
- Electroless Nickel Immersion Gold (ENIG)
- Immersion Silver (IAg)
- Immersion Tin (ISn)
- Direct Immersion Gold (DIG)
- Organic Solderability Preservative (OSP)
Each surface finish has its own advantages and disadvantages in terms of cost, durability, and signal performance. The choice of surface finish should be based on the specific requirements of the application, such as operating frequency, environmental conditions, and manufacturing constraints.
Surface Finish | Typical RMS Roughness (μm) | Advantages | Disadvantages |
---|---|---|---|
ENIG | 0.1 – 0.3 | Excellent solderability, good durability | Higher cost, potential for nickel corrosion |
IAg | 0.1 – 0.2 | Good solderability, lower cost than ENIG | Limited shelf life, potential for silver migration |
ISn | 0.2 – 0.4 | Good solderability, low cost | Limited shelf life, potential for tin whiskers |
DIG | 0.05 – 0.1 | Excellent surface flatness, good durability | Higher cost, potential for gold embrittlement |
OSP | 0.2 – 0.4 | Low cost, good solderability | Limited shelf life, potential for oxidation |
Table 2: Comparison of common surface finishes for high frequency PCBs
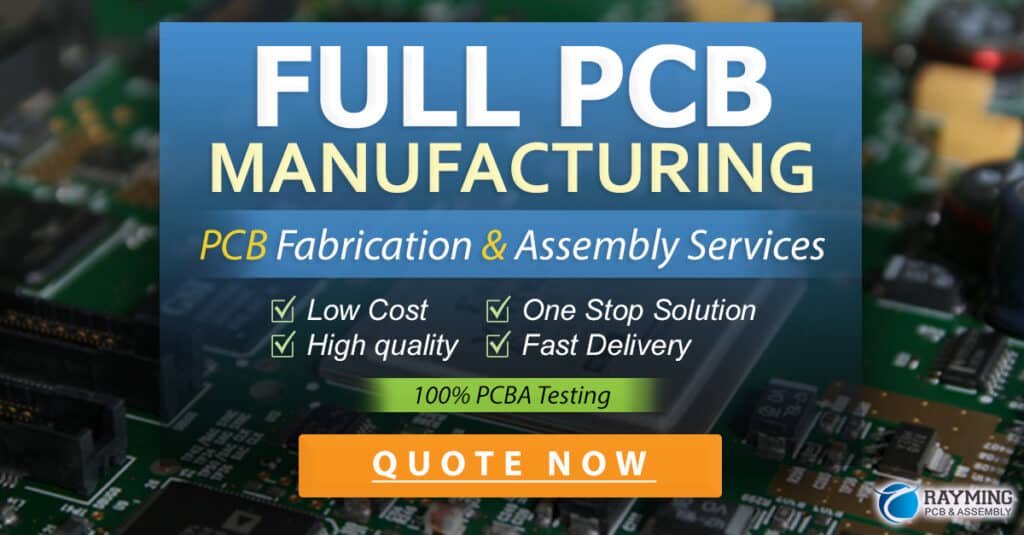
Copper Trace Geometry and Impedance Control
Importance of Controlled Impedance
In high frequency PCB design, controlling the characteristic impedance of copper traces is crucial for maintaining signal integrity and minimizing reflections. When the impedance of a trace is not matched to the source and load impedances, a portion of the signal energy is reflected back to the source, leading to signal distortion and degradation.
The characteristic impedance of a copper trace depends on several factors, including:
- Trace width and thickness
- Substrate material and thickness
- Presence of ground planes
- Proximity to other traces and components
To achieve controlled impedance, designers must carefully select the appropriate trace geometry and substrate properties to match the desired impedance value.
Microstrip and Stripline Traces
Two common trace geometries used in high frequency PCB design are microstrip and stripline traces. Microstrip traces are placed on the outer layers of the PCB, with a single ground plane below the trace. Stripline traces, on the other hand, are embedded within the PCB, with ground planes above and below the trace.
Microstrip traces offer several advantages, such as easier access for probing and modification, as well as lower manufacturing costs. However, they are more susceptible to external noise and interference, and their impedance is more sensitive to variations in substrate thickness and trace width.
Stripline traces provide better shielding and isolation from external noise, and their impedance is less sensitive to manufacturing variations. However, they are more challenging to access for probing and modification, and they require more complex manufacturing processes, leading to higher costs.
Trace Geometry | Advantages | Disadvantages |
---|---|---|
Microstrip | Easier access for probing and modification, lower cost | Higher susceptibility to noise, sensitive to manufacturing variations |
Stripline | Better shielding and noise isolation, more consistent impedance | Difficult to access for probing, higher manufacturing cost |
Table 3: Comparison of microstrip and stripline trace geometries
Calculating Trace Dimensions for Controlled Impedance
To calculate the required trace dimensions for a given characteristic impedance, designers can use various formulas and online calculators. For microstrip traces, the characteristic impedance (Z0) is given by:
Z0 = (87 / √(εr + 1.41)) * ln(5.98 * h / (0.8 * w + t))
Where:
– εr is the relative permittivity of the substrate material
– h is the substrate thickness
– w is the trace width
– t is the trace thickness
For stripline traces, the characteristic impedance is given by:
Z0 = (60 / √εr) * ln(4 * h / (0.67 * (0.8 * w + t)))
By using these formulas or online calculators, designers can determine the appropriate trace dimensions to achieve the desired characteristic impedance, ensuring optimal signal integrity in high frequency PCBs.
copper efficiency Optimization Techniques
Continuous Ground Planes
Incorporating continuous ground planes in the PCB design can greatly improve copper efficiency and signal integrity. Ground planes provide a low-impedance return path for high frequency signals, reducing loop area and minimizing electromagnetic interference (EMI). Continuous ground planes also help to maintain consistent trace impedance and reduce crosstalk between adjacent traces.
When designing ground planes, it is essential to ensure that they are as uninterrupted as possible, with minimal gaps or splits. Stitching vias should be used to connect ground planes on different layers, providing a continuous return path for high frequency currents.
Copper Pour and Thieving
Copper pouring is a technique where unused areas of the PCB are filled with copper, connected to the ground plane. This technique helps to improve copper efficiency by:
- Reducing the amount of unused copper on the board
- Providing additional shielding against EMI
- Improving heat dissipation
- Balancing copper distribution for better etching uniformity
Copper thieving is a similar technique where small, isolated copper shapes are added to the PCB layout to balance the copper distribution and improve etching uniformity. Thieving patterns should be carefully designed to avoid creating unintended resonant structures or affecting signal integrity.
Trace Routing and Length Matching
Proper trace routing and length matching are crucial for maintaining signal integrity and minimizing timing skew in high frequency PCBs. When routing high-speed signals, it is essential to keep the traces as short and direct as possible, minimizing the use of vias and layer transitions. Trace length matching should be used for differential pairs and critical signal paths to ensure that the signals arrive at their destinations at the same time, minimizing skew and distortion.
To optimize trace routing, designers can use various techniques, such as:
- Avoiding sharp corners and using curved or 45-degree bends
- Providing adequate spacing between traces to minimize crosstalk
- Using guard traces or shielding to isolate sensitive signals
- Incorporating delay lines or serpentine traces for fine-tuning length matching
By carefully planning and optimizing trace routing and length matching, designers can significantly improve the performance and reliability of high frequency PCBs.
Frequently Asked Questions (FAQ)
1. What is the main purpose of optimizing copper efficiency in high frequency PCB design?
The main purpose of optimizing copper efficiency in high frequency PCB design is to ensure optimal signal integrity, minimize losses, and improve the overall performance and reliability of the PCB.
2. How does the skin effect impact copper efficiency in high frequency PCBs?
The skin effect causes the electric current to flow primarily on the outer surface of the copper conductor at high frequencies, reducing the effective cross-sectional area and increasing resistance. This effect can lead to increased losses and signal attenuation if not properly accounted for in the design process.
3. What are the key factors to consider when choosing the copper thickness for high frequency PCBs?
The key factors to consider when choosing the copper thickness for high frequency PCBs include the frequency of operation, current carrying requirements, thermal management needs, and manufacturing constraints. The copper thickness should be at least three times the skin depth at the highest operating frequency to ensure optimal signal transmission.
4. How does copper surface roughness affect signal integrity in high frequency PCBs?
Copper surface roughness can lead to increased resistance and losses in high frequency PCBs, as the skin effect confines the current flow to a thin layer near the surface of the conductor. A rougher surface (higher RMS value) can result in greater signal attenuation and distortion, making it essential to choose the appropriate surface finish for the application.
5. What are some common techniques for optimizing copper efficiency in high frequency PCB design?
Common techniques for optimizing copper efficiency in high frequency PCB design include incorporating continuous ground planes, using copper pour and thieving to balance copper distribution, optimizing trace routing and length matching, and selecting the appropriate trace geometry (microstrip or stripline) for the specific application requirements.
Conclusion
Copper choice and copper efficiency optimization are critical aspects of high frequency PCB design, directly impacting signal integrity, performance, and reliability. By understanding the effects of skin depth, surface roughness, and trace geometry on signal transmission, designers can make informed decisions when selecting copper thickness, surface finish, and trace dimensions.
Implementing optimization techniques such as continuous ground planes, copper pour and thieving, and careful trace routing and length matching can further enhance copper efficiency and minimize losses in high frequency PCBs.
As the demand for high-speed and high-bandwidth electronics continues to grow, mastering the principles of copper efficiency optimization will be increasingly important for PCB designers to meet the evolving challenges of high frequency applications.
Leave a Reply