The Importance of Copper in PCB Design
Copper is a crucial component in the design and manufacturing of printed circuit boards (PCBs). Its excellent electrical conductivity, thermal conductivity, and resistance to corrosion make it the ideal material for creating the conductive pathways that allow electronic components to communicate with each other. In this article, we will explore the importance of copper in PCB design, with a particular focus on the Copper Edge and its role in ensuring the reliability and performance of electronic devices.
The Role of Copper in PCB Manufacturing
Copper is used to create the conductive layers of a PCB, which are typically referred to as copper traces or copper tracks. These traces are responsible for carrying electrical signals between components on the board. The thickness of the copper layer is measured in ounces per square foot (oz/ft²), with common thicknesses ranging from 0.5 oz/ft² to 2 oz/ft².
The copper used in PCB manufacturing is typically electrodeposited onto a dielectric substrate, such as FR-4, which is a glass-reinforced epoxy laminate. The copper layer is then etched away using a photolithographic process to create the desired circuit pattern.
The Importance of the Copper Edge
The copper edge refers to the exposed copper on the edges of a PCB. This exposed copper is critical for several reasons:
-
Grounding: The copper edge provides a low-impedance path to ground, which helps to minimize electromagnetic interference (EMI) and ensure the stability of the electronic system.
-
Shielding: The copper edge acts as a shield against external electromagnetic fields, helping to protect the sensitive electronic components on the board from interference.
-
Structural Integrity: The copper edge helps to reinforce the structural integrity of the PCB, particularly in applications where the board may be subjected to mechanical stress or vibration.
Designing for the Copper Edge
When designing a PCB, it is important to consider the copper edge and how it will affect the performance and reliability of the electronic system. Here are some key considerations:
-
Clearance: It is important to maintain adequate clearance between the copper edge and any adjacent components or traces. This helps to prevent short circuits and ensures that the copper edge can effectively serve its grounding and shielding functions.
-
Plating: The copper edge should be plated with a protective finish, such as gold or nickel, to prevent oxidation and ensure long-term reliability.
-
Grounding: The copper edge should be connected to the ground plane of the PCB using a low-impedance path, such as a via or a dedicated ground trace.
-
Shielding: In applications where EMI is a concern, it may be necessary to extend the copper edge around the perimeter of the board to provide additional shielding.
The Benefits of Using Copper in PCB Design
Copper offers several key benefits in PCB design, including:
Excellent Electrical Conductivity
Copper has the second-highest electrical conductivity of any metal, surpassed only by silver. This makes it an ideal material for creating the conductive pathways on a PCB. The high conductivity of copper helps to minimize resistive losses and ensure that electrical signals can propagate efficiently across the board.
Thermal Conductivity
Copper also has excellent thermal conductivity, which means that it can effectively dissipate heat away from electronic components on the board. This is particularly important in high-power applications, where the buildup of heat can lead to component failure and reduced reliability.
Resistance to Corrosion
Copper is naturally resistant to corrosion, which helps to ensure the long-term reliability of electronic systems. When exposed to air, copper forms a thin layer of copper oxide on its surface, which acts as a protective barrier against further oxidation. This natural resistance to corrosion makes copper an ideal material for use in harsh environmental conditions.
Cost-Effectiveness
While copper is more expensive than some other conductive materials, such as aluminum, it is still relatively cost-effective compared to other high-performance materials, such as gold or silver. The widespread availability of copper and its ease of processing also contribute to its cost-effectiveness in PCB manufacturing.
Common Copper Thicknesses in PCB Design
The thickness of the copper layer on a PCB is typically measured in ounces per square foot (oz/ft²). Here are some common copper thicknesses used in PCB design:
Copper Thickness (oz/ft²) | Typical Applications |
---|---|
0.5 | Low-power, high-density designs |
1.0 | General-purpose designs |
2.0 | High-power, high-current designs |
3.0 | Extreme high-power designs |
The choice of copper thickness depends on several factors, including the power requirements of the electronic system, the desired current-carrying capacity of the traces, and the manufacturing capabilities of the PCB fabricator.
Copper Thickness and Current-Carrying Capacity
The current-carrying capacity of a copper trace is directly related to its cross-sectional area, which is determined by its width and thickness. Increasing the copper thickness allows for higher current-carrying capacity without increasing the width of the trace.
For example, a 1 oz/ft² copper trace that is 10 mils wide can carry approximately 1.4 amps of current. Doubling the copper thickness to 2 oz/ft² increases the current-carrying capacity to approximately 2.8 amps, without increasing the width of the trace.
Copper Thickness and Manufacturing Considerations
The choice of copper thickness also has implications for the manufacturing process. Thicker copper layers require longer etching times and may be more challenging to process, particularly for high-density designs with fine pitch features.
In addition, thicker copper layers may be more prone to warping or bowing during the manufacturing process, particularly if the copper is not evenly distributed across the board. This can lead to manufacturing defects and reduced yields.
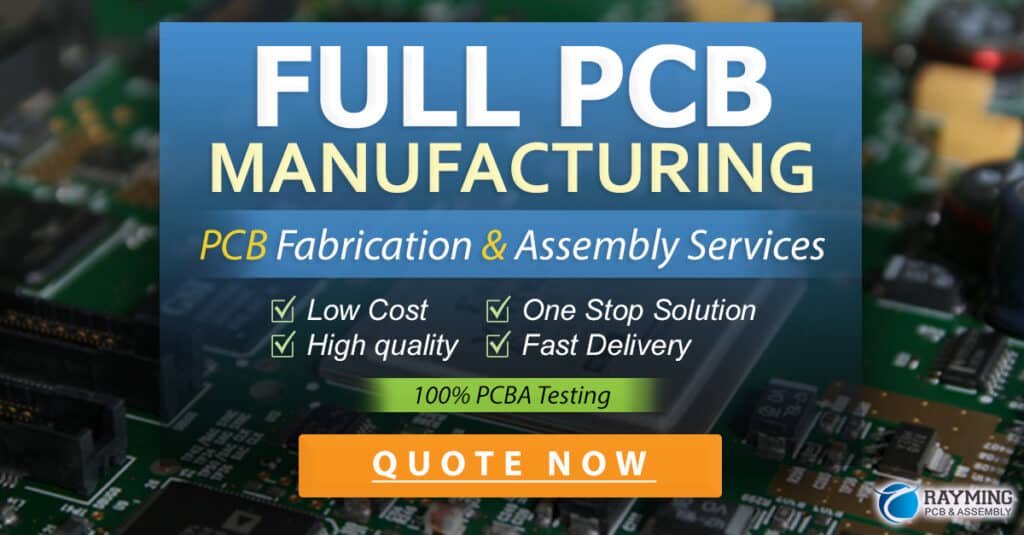
The Copper Edge and EMI
The copper edge plays a critical role in mitigating electromagnetic interference (EMI) in electronic systems. EMI refers to the unwanted coupling of electromagnetic energy between electronic components, which can lead to signal integrity issues and reduced reliability.
The Role of the Copper Edge in EMI Mitigation
The copper edge acts as a low-impedance path to ground, which helps to minimize the buildup of electromagnetic fields around the perimeter of the board. By providing a continuous, uninterrupted ground path, the copper edge helps to contain electromagnetic energy within the board and prevent it from radiating outward.
In addition, the copper edge acts as a shield against external electromagnetic fields, helping to protect the sensitive electronic components on the board from interference. By extending the copper edge around the perimeter of the board, designers can create a Faraday cage that effectively blocks external electromagnetic fields.
Designing for EMI Mitigation
When designing a PCB for EMI mitigation, it is important to consider the following factors:
-
Ground Plane: The ground plane of the PCB should be continuous and uninterrupted, with a low-impedance connection to the copper edge. This helps to minimize the buildup of electromagnetic fields and ensure that any induced currents can be quickly shunted to ground.
-
Component Placement: Electronic components should be placed as close to the ground plane as possible, with short, direct connections to ground. This helps to minimize the loop area of the current path and reduce the potential for EMI.
-
Signal Routing: High-speed signals should be routed away from the edges of the board, with adequate spacing between adjacent traces to minimize crosstalk. Differential signaling techniques can also be used to reduce the potential for EMI.
-
Shielding: In applications where EMI is a significant concern, additional shielding measures may be necessary. This can include the use of shielded connectors, shielded cables, and conductive gaskets around the perimeter of the board.
Frequently Asked Questions (FAQ)
1. What is the purpose of the copper edge on a PCB?
The copper edge serves several important functions in PCB design, including providing a low-impedance path to ground, acting as a shield against external electromagnetic fields, and reinforcing the structural integrity of the board.
2. How does the copper edge help to mitigate EMI?
The copper edge acts as a low-impedance path to ground, which helps to minimize the buildup of electromagnetic fields around the perimeter of the board. By providing a continuous, uninterrupted ground path, the copper edge helps to contain electromagnetic energy within the board and prevent it from radiating outward.
3. What are some common copper thicknesses used in PCB design?
Common copper thicknesses used in PCB design include 0.5 oz/ft² for low-power, high-density designs, 1.0 oz/ft² for general-purpose designs, 2.0 oz/ft² for high-power, high-current designs, and 3.0 oz/ft² for extreme high-power designs.
4. How does copper thickness affect the current-carrying capacity of a trace?
The current-carrying capacity of a copper trace is directly related to its cross-sectional area, which is determined by its width and thickness. Increasing the copper thickness allows for higher current-carrying capacity without increasing the width of the trace.
5. What are some design considerations for EMI mitigation in PCB design?
When designing a PCB for EMI mitigation, it is important to consider factors such as the continuity of the ground plane, the placement of electronic components, the routing of high-speed signals, and the use of additional shielding measures such as shielded connectors and conductive gaskets.
Conclusion
Copper is a critical component in the design and manufacturing of printed circuit boards, offering excellent electrical conductivity, thermal conductivity, and resistance to corrosion. The copper edge, in particular, plays a crucial role in ensuring the reliability and performance of electronic systems, providing a low-impedance path to ground, shielding against external electromagnetic fields, and reinforcing the structural integrity of the board.
When designing a PCB, it is important to consider the copper edge and how it will affect the performance and reliability of the electronic system. Factors such as clearance, plating, grounding, and shielding should all be carefully considered to ensure that the copper edge can effectively serve its intended functions.
By understanding the importance of copper in PCB design and the role of the copper edge in particular, designers can create electronic systems that are reliable, efficient, and resistant to electromagnetic interference. As electronic devices continue to become more complex and sophisticated, the effective use of copper in PCB design will remain a critical factor in ensuring their success.
Leave a Reply