Introduction to PCB Bending
Flexible printed circuit boards (PCBs) have gained significant popularity in recent years due to their ability to conform to various shapes and configurations. Unlike traditional rigid PCBs, flexible PCBs can bend and twist, making them ideal for applications that require compact packaging or dynamic movement. In this article, we will explore the process of configuring and animating the bending of a PCB that is entirely flexible.
Understanding Flexible PCBs
Flexible PCBs, also known as flex circuits, are thin, lightweight, and highly durable circuit boards made from flexible materials such as polyimide or polyester. These materials allow the PCB to bend and flex without compromising its electrical functionality. Flex PCBs consist of a flexible substrate with conductive traces and components mounted on top, enabling them to be shaped and folded into various configurations.
Benefits of Flexible PCBs
Flexible PCBs offer several advantages over traditional rigid PCBs:
- Compact packaging: Flex PCBs can be folded and shaped to fit into tight spaces, reducing the overall size of electronic devices.
- Improved reliability: The flexibility of the PCB reduces stress on components and connections, enhancing the reliability and durability of the device.
- Reduced weight: Flex PCBs are significantly lighter than rigid PCBs, making them ideal for portable and wearable devices.
- Enhanced design freedom: The ability to bend and shape the PCB allows for unique and innovative product designs.
Configuring PCB Bending
To configure the bending of a flexible PCB, several factors need to be considered. These include the bend radius, bend angle, and the materials used in the PCB construction.
Bend Radius
The bend radius is the minimum radius at which a flexible PCB can be bent without causing damage to the circuit or components. It is determined by the thickness and material properties of the PCB. The bend radius should be carefully calculated to ensure the PCB can withstand the required bending without compromising its performance.
The following table provides general guidelines for bend radii based on the thickness of the flexible PCB:
PCB Thickness (mm) | Minimum Bend Radius (mm) |
---|---|
0.05 | 0.25 |
0.1 | 0.5 |
0.2 | 1.0 |
0.3 | 1.5 |
Bend Angle
The bend angle refers to the angle at which the flexible PCB is bent. It is important to consider the maximum bend angle allowed by the PCB material and the components mounted on the board. Exceeding the maximum bend angle can lead to damage or failure of the PCB.
Typical bend angles for flexible PCBs range from 0° to 180°, depending on the application and design requirements. It is crucial to consult the manufacturer’s specifications and guidelines to determine the appropriate bend angle for a specific PCB.
Material Selection
The choice of materials used in the construction of a flexible PCB plays a significant role in its bending capabilities. The substrate material, copper thickness, and coverlay material all contribute to the flexibility and durability of the PCB.
Common substrate materials for flexible PCBs include:
- Polyimide (PI): Known for its high temperature resistance and excellent mechanical properties.
- Polyester (PET): Offers good flexibility and electrical properties at a lower cost compared to polyimide.
- Flexible epoxy: Provides a balance between flexibility and durability.
The thickness of the copper traces on the PCB also affects its bending performance. Thinner copper layers allow for greater flexibility but may have limitations in terms of current carrying capacity. It is important to strike a balance between flexibility and electrical requirements when selecting the copper thickness.
Coverlay materials, such as polyimide or polyester films, provide protection and insulation to the PCB. The choice of coverlay material should consider its flexibility, durability, and compatibility with the substrate material.
Animating PCB Bending
Animating the bending of a flexible PCB involves creating a visual representation of how the PCB will bend and move in a specific application. This process helps designers and engineers evaluate the feasibility and performance of the PCB design before physical prototyping.
3D Modeling
The first step in animating PCB bending is to create a 3D model of the flexible PCB. This can be done using computer-aided design (CAD) software such as Autodesk Fusion 360, SolidWorks, or CATIA. The 3D model should accurately represent the dimensions, components, and material properties of the PCB.
When modeling the PCB, it is important to consider the following:
- PCB thickness and layer stackup
- Component placement and clearances
- Bend lines and fold locations
- Mechanical constraints and mounting points
Finite Element Analysis (FEA)
Once the 3D model is created, finite element analysis (FEA) can be used to simulate the bending behavior of the flexible PCB. FEA software, such as Ansys or COMSOL Multiphysics, divides the PCB model into small elements and applies the material properties and boundary conditions to predict the stress, strain, and deformation of the PCB under various loading scenarios.
FEA simulations help designers optimize the PCB layout, material selection, and bend radius to ensure the PCB can withstand the required bending without failure. It also allows for the identification of potential stress concentrations and areas of concern that may require design modifications.
Animation and Visualization
After conducting FEA simulations, the bending behavior of the flexible PCB can be animated and visualized using 3D rendering software. This step involves creating a series of frames that showcase the PCB bending and moving in the desired manner.
Animation software, such as Autodesk 3ds Max or Blender, can be used to create realistic animations of the PCB bending. These animations can include the movement of components, the flexing of the PCB substrate, and the interaction with other mechanical parts in the assembly.
Visualizing the PCB bending through animation helps designers communicate the design intent to stakeholders and enables better collaboration between teams. It also allows for the identification of potential interference or clearance issues that may arise during the bending process.
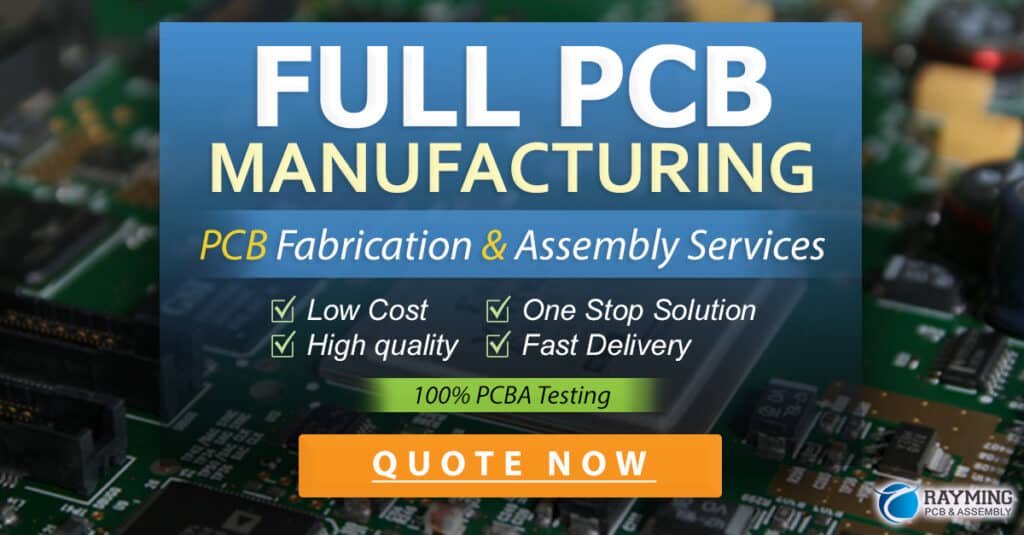
Best Practices for PCB Bending Design
To ensure the successful implementation of flexible PCB bending in a product, consider the following best practices:
-
Minimize component placement on bend lines: Avoid placing components directly on the bend lines to reduce stress and prevent damage to the components during bending.
-
Use strain relief features: Incorporate strain relief features, such as slots or cutouts, near the bend lines to distribute stress and prevent cracking or tearing of the PCB substrate.
-
Consider the bend direction: Design the PCB layout and component placement to accommodate the intended bend direction and minimize stress on the components and traces.
-
Use flexible components: Select components that are designed for flexible PCB applications, such as flexible connectors and surface-mount devices (SMDs) with flexible terminations.
-
Perform physical testing: Conduct physical bending tests on prototype PCBs to validate the design and ensure the PCB can withstand the required bending without failure.
Conclusion
Configuring and animating the bending of a flexible PCB is a critical process in the design and development of products that require compact packaging or dynamic movement. By understanding the factors that influence PCB bending, such as bend radius, bend angle, and material selection, designers can create robust and reliable flexible PCB designs.
The use of 3D modeling, finite element analysis, and animation tools enables designers to visualize and optimize the bending behavior of the PCB before physical prototyping. This approach reduces development time, minimizes design iterations, and improves the overall quality of the final product.
By following best practices and considering the unique requirements of flexible PCB bending, designers can unlock new possibilities in product design and push the boundaries of electronic packaging.
Frequently Asked Questions (FAQ)
-
Q: What is the difference between a flexible PCB and a rigid PCB?
A: Flexible PCBs are made from flexible materials, such as polyimide or polyester, which allow them to bend and flex without damaging the circuit. Rigid PCBs, on the other hand, are made from a rigid substrate material, such as FR-4, and cannot bend or flex. -
Q: Can all types of components be used on flexible PCBs?
A: Not all components are suitable for use on flexible PCBs. It is important to select components that are designed for flexible applications, such as those with flexible terminations or packages that can withstand bending stresses. Surface-mount devices (SMDs) are generally preferred over through-hole components for flexible PCBs. -
Q: How do I determine the appropriate bend radius for my flexible PCB?
A: The appropriate bend radius depends on the thickness and material properties of the flexible PCB. As a general rule, the minimum bend radius should be at least 6 to 10 times the thickness of the PCB. It is important to consult the manufacturer’s specifications and guidelines to determine the recommended bend radius for a specific PCB material and thickness. -
Q: Can flexible PCBs be used in high-temperature environments?
A: The suitability of flexible PCBs for high-temperature environments depends on the materials used in their construction. Polyimide (PI) is a common substrate material known for its high temperature resistance and can withstand temperatures up to 200°C. However, the temperature rating of the components and the overall assembly should also be considered when designing a flexible PCB for high-temperature applications. -
Q: How can I ensure the reliability of my flexible PCB design?
A: To ensure the reliability of a flexible PCB design, consider the following practices: - Use appropriate materials and components that can withstand the required bending and environmental conditions.
- Minimize component placement on bend lines and use strain relief features to reduce stress concentrations.
- Conduct thorough FEA simulations to optimize the PCB layout and identify potential failure points.
- Perform physical bending tests on prototype PCBs to validate the design and make necessary adjustments.
- Follow industry standards and guidelines for flexible PCB design and manufacturing.
By addressing these common questions and concerns, designers can confidently approach the configuration and animation of flexible PCB bending in their projects.
Leave a Reply