Introduction to IPC Standards for PCB Design
IPC (Association Connecting Electronics Industries) is a global trade association that develops and publishes standards for the electronic industry, including standards for printed circuit board (PCB) design and manufacturing. Complying with IPC standards ensures that PCBs are designed and manufactured to meet industry-recognized quality, reliability, and performance requirements. In this article, we will explore the key IPC standards for PCB design and provide guidance on how to comply with them.
What are IPC Standards?
IPC standards are a set of guidelines and requirements that define the best practices for designing, manufacturing, and testing electronic products, including PCBs. These standards are developed by committees of industry experts and are regularly updated to keep pace with technological advancements and changing market demands.
Some of the most important IPC standards for PCB design include:
- IPC-2221: Generic Standard on Printed Board Design
- IPC-2222: Sectional Design Standard for Rigid Organic Printed Boards
- IPC-2223: Sectional Design Standard for Flexible Printed Boards
- IPC-2226: Sectional Design Standard for High Density Interconnect (HDI) Printed Boards
- IPC-7351: Generic Requirements for Surface Mount Design and Land Pattern Standard
Benefits of Complying with IPC Standards
Complying with IPC standards offers several benefits for PCB designers and manufacturers, including:
-
Improved quality and reliability: IPC standards ensure that PCBs are designed and manufactured to meet strict quality and reliability requirements, reducing the risk of failures and defects.
-
Enhanced performance: By following IPC guidelines for signal integrity, thermal management, and other critical design aspects, PCBs can achieve optimal performance and functionality.
-
Increased consistency: IPC standards provide a common language and set of guidelines for PCB design and manufacturing, promoting consistency across different projects and suppliers.
-
Reduced costs: By minimizing design errors and manufacturing defects, complying with IPC standards can help reduce costs associated with rework, scrap, and warranty claims.
-
Improved communication: IPC standards facilitate better communication between PCB designers, manufacturers, and customers by providing a clear and standardized set of requirements and expectations.
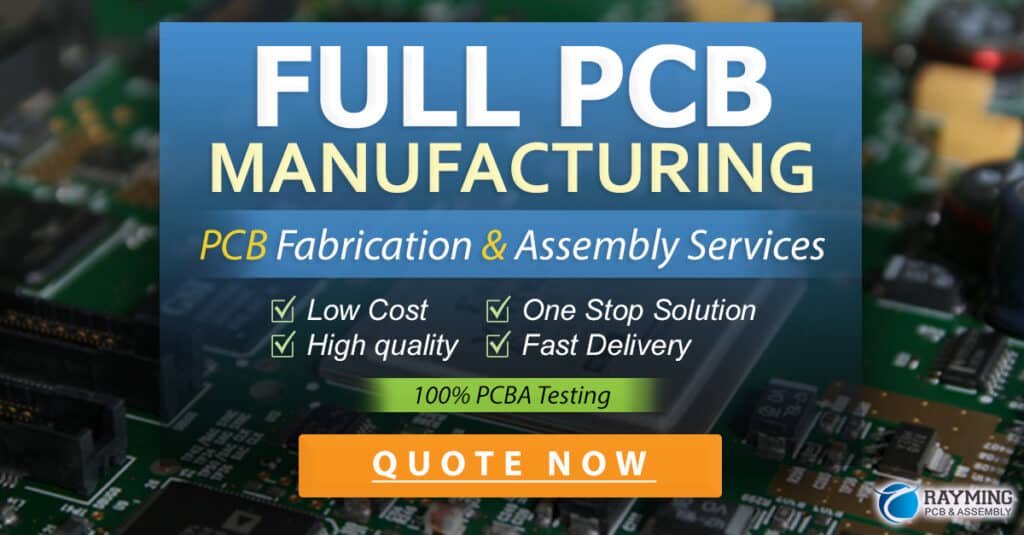
Key IPC Standards for PCB Design
IPC-2221: Generic Standard on Printed Board Design
IPC-2221 is a comprehensive standard that provides general requirements for the design of printed boards, including single-sided, double-sided, and multi-layer boards. This standard covers various aspects of PCB design, such as:
- Material selection
- Conductor width and spacing
- Hole size and placement
- Solder mask and silkscreen requirements
- Electrical clearances and creepage distances
- Thermal management considerations
To comply with IPC-2221, PCB designers should follow the guidelines and requirements specified in the standard, such as minimum conductor width and spacing based on the board’s voltage and current requirements, as well as the recommended hole sizes and placement for different component types.
IPC-2222: Sectional Design Standard for Rigid Organic Printed Boards
IPC-2222 is a sectional standard that provides specific requirements for the design of rigid organic printed boards. This standard builds upon the general requirements of IPC-2221 and includes additional guidelines for:
- Board thickness and dimensioning
- Copper foil thickness and weight
- Hole and via design
- Surface finish requirements
- Bow and twist tolerances
To comply with IPC-2222, PCB designers should adhere to the specific requirements outlined in the standard, such as the recommended board thickness and copper foil weight for different applications, as well as the acceptable bow and twist tolerances for the finished board.
IPC-2223: Sectional Design Standard for Flexible Printed Boards
IPC-2223 is a sectional standard that provides specific requirements for the design of flexible printed boards, including single-sided, double-sided, and multi-layer flex circuits. This standard covers various aspects of flexible PCB design, such as:
- Material selection and properties
- Conductor width and spacing
- Bend radius and flexibility requirements
- Coverlay and stiffener design
- Termination and interconnection methods
To comply with IPC-2223, PCB designers should follow the guidelines and requirements specified in the standard, such as the recommended material properties and bend radius for different flex circuit applications, as well as the appropriate coverlay and stiffener design to ensure the desired flexibility and durability.
IPC-2226: Sectional Design Standard for High Density Interconnect (HDI) Printed Boards
IPC-2226 is a sectional standard that provides specific requirements for the design of high-density interconnect (HDI) printed boards. HDI boards are characterized by fine pitch components, small vias, and high layer counts, enabling greater functionality in a smaller form factor. This standard covers various aspects of HDI PCB design, such as:
- Via types and structures (micro vias, buried vias, blind vias)
- Via filling and plugging requirements
- Conductor width and spacing for fine pitch components
- Pad and solder mask design for HDI assemblies
- Controlled impedance considerations
To comply with IPC-2226, PCB designers should adhere to the specific requirements outlined in the standard, such as the recommended via types and structures for different HDI applications, as well as the appropriate conductor width and spacing for fine pitch components and controlled impedance traces.
IPC-7351: Generic Requirements for Surface Mount Design and Land Pattern Standard
IPC-7351 is a standard that provides generic requirements for the design of surface mount technology (SMT) land patterns and component placement. This standard includes guidelines for:
- Land pattern dimensions and tolerances
- Solder mask and paste definitions
- Component placement and orientation
- Courtyard and assembly clearances
- Thermal relief and via design
To comply with IPC-7351, PCB designers should follow the recommended land pattern dimensions and tolerances for different component types and sizes, as well as the appropriate solder mask and paste definitions to ensure proper solder joint formation. Designers should also adhere to the guidelines for component placement, orientation, and clearances to facilitate efficient and reliable SMT assembly.
Designing PCBs to Comply with IPC Standards
To design PCBs that comply with IPC standards, designers should follow these best practices:
-
Familiarize yourself with the relevant IPC standards for your specific PCB application (e.g., rigid, flexible, HDI, SMT).
-
Use IPC-compliant CAD tools and libraries that include standard component footprints, land patterns, and design rules.
-
Establish a comprehensive design checklist that incorporates the key requirements and guidelines from the applicable IPC standards.
-
Collaborate with your PCB fabricator and assembly partner to ensure that your design meets their capabilities and complies with their specific manufacturing requirements.
-
Conduct thorough design reviews and simulations to verify that your PCB design meets the electrical, thermal, and mechanical requirements specified in the relevant IPC standards.
-
Document your design decisions and rationale, and maintain a clear and organized set of design files and specifications to facilitate communication and collaboration with your team and suppliers.
Common Pitfalls to Avoid
When designing PCBs to comply with IPC standards, it’s important to avoid these common pitfalls:
-
Overlooking the specific requirements for your PCB application: Make sure to use the appropriate sectional standard (e.g., IPC-2222 for rigid boards, IPC-2223 for flexible boards) in addition to the generic IPC-2221 standard.
-
Using non-standard or outdated component footprints and land patterns: Always use IPC-compliant libraries and verify that your component footprints and land patterns meet the current IPC-7351 guidelines.
-
Neglecting thermal management considerations: Ensure that your PCB design includes adequate thermal relief, copper pours, and heat sinking to meet the thermal requirements specified in the relevant IPC standards.
-
Failing to account for manufacturing tolerances and variations: Design your PCB with appropriate tolerances and clearances to accommodate fabrication and assembly variations, as specified in the applicable IPC standards.
-
Not involving your PCB fabricator and assembly partner early in the design process: Collaborate with your suppliers from the start to ensure that your design is manufacturable and complies with their specific requirements and capabilities.
By avoiding these pitfalls and following the best practices outlined in this article, you can design PCBs that comply with IPC standards and achieve optimal quality, reliability, and performance.
Frequently Asked Questions
Q1: What is the difference between IPC-2221 and IPC-2222?
A1: IPC-2221 is a generic standard that provides general requirements for the design of printed boards, while IPC-2222 is a sectional standard that provides specific requirements for the design of rigid organic printed boards. IPC-2222 builds upon the general requirements of IPC-2221 and includes additional guidelines for board thickness, copper foil weight, and other rigid board-specific aspects.
Q2: Do I need to comply with all IPC standards for every PCB design?
A2: Not necessarily. The specific IPC standards you need to comply with will depend on the type of PCB you are designing (e.g., rigid, flexible, HDI) and the specific application requirements. It’s important to identify the relevant standards for your project and focus on complying with those specific guidelines and requirements.
Q3: Can I use non-IPC-compliant components in my PCB design?
A3: While it’s generally recommended to use IPC-compliant components and footprints, there may be cases where you need to use non-standard components due to specific project requirements or availability constraints. In such cases, it’s important to work closely with your PCB fabricator and assembly partner to ensure that the non-standard components can be accommodated in your design and that any necessary adjustments are made to ensure manufacturability and reliability.
Q4: How can I verify that my PCB design complies with IPC standards?
A4: To verify compliance with IPC standards, you can use a combination of methods, such as:
- Using IPC-compliant CAD tools and libraries that include standard design rules and checks.
- Conducting thorough design reviews and simulations to verify that your design meets the electrical, thermal, and mechanical requirements specified in the relevant IPC standards.
- Collaborating with your PCB fabricator and assembly partner to review your design and ensure that it meets their specific manufacturing requirements and capabilities.
- Using automated design rule checking (DRC) and design for manufacturability (DFM) tools to identify and correct any design issues or violations of IPC guidelines.
Q5: Are IPC standards mandatory for all PCB designs?
A5: While IPC standards are not legally mandatory, they are widely recognized and adopted by the electronics industry as best practices for ensuring the quality, reliability, and performance of PCBs. Many PCB fabricators and assembly providers require compliance with specific IPC standards as part of their manufacturing process, and non-compliance may result in higher costs, longer lead times, or reduced reliability. Therefore, it’s generally in the best interest of PCB designers and product developers to comply with relevant IPC standards to the greatest extent possible.
Conclusion
Complying with IPC standards is essential for designing and manufacturing high-quality, reliable, and performance-optimized PCBs. By understanding the key IPC standards for PCB design, such as IPC-2221, IPC-2222, IPC-2223, IPC-2226, and IPC-7351, and following the best practices and guidelines outlined in these standards, PCB designers can ensure that their designs meet industry-recognized requirements and are manufacturable, cost-effective, and fit for purpose.
To successfully comply with IPC standards, PCB designers should familiarize themselves with the relevant standards for their specific application, use IPC-compliant tools and libraries, establish comprehensive design checklists, collaborate with their fabrication and assembly partners, conduct thorough design reviews and simulations, and document their design decisions and rationale.
By avoiding common pitfalls and following the guidance provided in this article, PCB designers can navigate the complexities of IPC standards compliance and create PCBs that meet the highest standards of quality, reliability, and performance.
Leave a Reply