Introduction to SMT Assembly
Surface Mount Technology (SMT) has revolutionized the electronics manufacturing industry by enabling the production of smaller, faster, and more reliable electronic devices. SMT assembly involves placing surface mount components directly onto the surface of a printed circuit board (PCB) and soldering them in place. With the right tools and knowledge, it is possible to set up a DIY SMT assembly line in your office, allowing you to prototype and produce small batches of PCBs quickly and efficiently.
In this comprehensive guide, we will walk you through the process of setting up your own SMT assembly line, including the necessary equipment, materials, and techniques required for successful assembly.
Benefits of DIY SMT Assembly
There are several advantages to setting up your own SMT assembly line in your office:
-
Rapid prototyping: With your own assembly line, you can quickly prototype and test new designs without having to wait for external manufacturing services.
-
Cost savings: By assembling your own PCBs, you can save money on manufacturing costs, especially for small batches or one-off projects.
-
Flexibility: Having control over the assembly process allows you to make changes and adjustments on the fly, adapting to your specific needs and requirements.
-
Learning opportunity: Setting up and operating an SMT assembly line provides valuable hands-on experience and knowledge in electronics manufacturing.
Equipment and Materials Required
To set up your DIY SMT assembly line, you will need the following equipment and materials:
Essential Equipment
Equipment | Description |
---|---|
Soldering Station | A temperature-controlled soldering iron with adjustable heat settings. |
Reflow Oven | An oven designed for reflowing solder paste and creating permanent connections between components and the PCB. |
Stencil Printer | A machine used to apply solder paste to the PCB through a stencil. |
Pick and Place Machine | An automated machine that places surface mount components onto the PCB with precision. |
Microscope | A microscope with sufficient magnification for inspecting solder joints and component placement. |
Additional Tools and Accessories
- Tweezers
- Solder paste
- Solder wire
- Flux
- Isopropyl alcohol
- Cleaning brushes
- ESD-safe mats and wrist straps
PCB and Components
- Blank PCBs
- Surface mount components (resistors, capacitors, ICs, etc.)
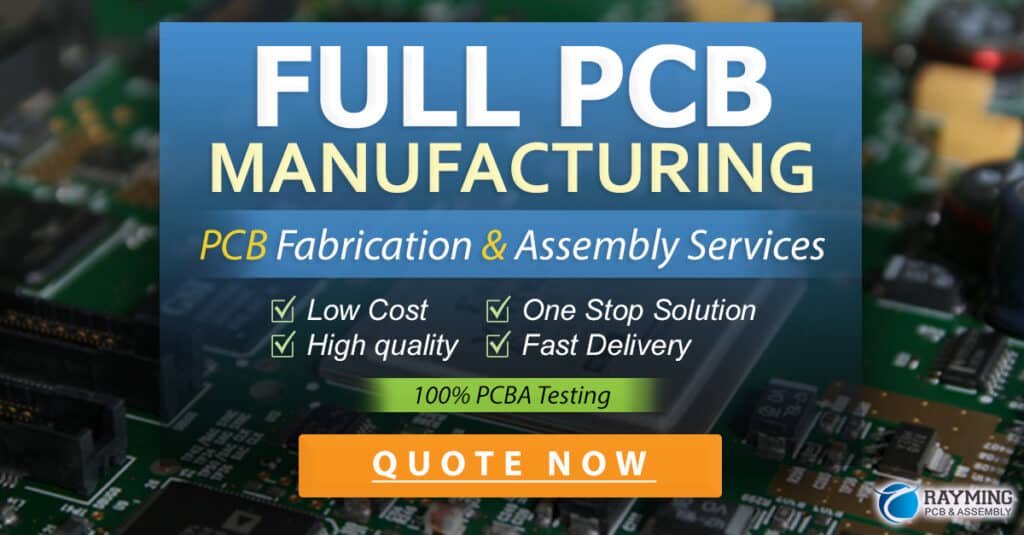
Setting Up Your Workspace
Before you begin assembling your PCBs, it is essential to set up a clean, organized, and ESD-safe workspace. Follow these steps to create an optimal environment for SMT assembly:
-
Choose a dedicated area in your office with sufficient space for your equipment and materials.
-
Install ESD-safe mats on your work surfaces and ground them properly to prevent electrostatic discharge damage to your components.
-
Ensure adequate lighting and ventilation in your workspace.
-
Organize your components and tools in labeled bins or drawers for easy access.
-
Maintain a clean environment by regularly cleaning your workspace and equipment with isopropyl alcohol.
SMT Assembly Process
The SMT assembly process consists of several steps, each requiring specific techniques and attention to detail. Let’s walk through the process step by step:
Step 1: PCB Design and Preparation
-
Design your PCB using EDA (Electronic Design Automation) software, ensuring that your component footprints and layout are correct.
-
Generate Gerber files and send them to a PCB manufacturer to fabricate your boards.
-
Upon receiving your PCBs, inspect them for any defects or irregularities.
-
Clean the PCBs with isopropyl alcohol to remove any dirt or grease.
Step 2: Solder Paste Application
-
Create a stencil for your PCB design, either by ordering one from a manufacturer or by making your own using a laser cutter or CNC machine.
-
Place the stencil over your PCB and secure it in place using tape or clamps.
-
Apply solder paste to the stencil using a squeegee, ensuring an even distribution of paste across the pads.
-
Carefully remove the stencil and inspect the PCB to ensure that the solder paste has been applied correctly.
Step 3: Component Placement
-
Load your components into the pick and place machine, following the machine’s instructions for proper orientation and feeding.
-
Program the pick and place machine with your PCB design and component placement data.
-
Run the pick and place machine to automatically place the components onto the PCB.
-
Visually inspect the PCB after component placement to ensure that all components are correctly positioned and aligned.
Step 4: Reflow Soldering
-
Preheat your reflow oven according to the manufacturer’s instructions and the solder paste specifications.
-
Place your PCB with the placed components into the reflow oven.
-
Run the reflow profile, which typically involves a preheat stage, a soak stage, a reflow stage, and a cooling stage.
-
Remove the PCB from the oven once the reflow process is complete and allow it to cool down.
Step 5: Inspection and Rework
-
Visually inspect the soldered PCB under a microscope to check for any defects, such as bridging, tombstoning, or insufficient solder joints.
-
If necessary, perform rework using a soldering iron, flux, and solder wick to correct any issues.
-
Clean the PCB with isopropyl alcohol to remove any flux residue.
Tips and Tricks for Successful SMT Assembly
-
Always handle PCBs and components with care, using ESD-safe equipment and practices to prevent damage.
-
Ensure that your solder paste is fresh and stored properly to maintain its quality and performance.
-
Regularly calibrate and maintain your equipment to ensure consistent and accurate results.
-
Keep your workspace clean and organized to minimize the risk of contamination and errors.
-
Practice proper soldering techniques, such as maintaining the correct temperature and applying the right amount of solder.
Troubleshooting Common Issues
Issue | Possible Causes | Solutions |
---|---|---|
Bridging | Excessive solder paste, incorrect component placement | Use a soldering iron and solder wick to remove excess solder, realign components |
Tombstoning | Uneven heating, incorrect paste application | Ensure even heating during reflow, check paste application for consistency |
Poor Adhesion | Contaminated PCB surface, insufficient solder paste | Clean PCB thoroughly, check paste application and stencil alignment |
Insufficient Solder Joints | Insufficient solder paste, incorrect reflow profile | Adjust paste application, optimize reflow profile |
Frequently Asked Questions (FAQ)
-
Q: Can I use a regular oven for reflow soldering?
A: While it is possible to use a regular oven for reflow soldering, it is not recommended. Reflow ovens are specifically designed to provide accurate temperature control and even heating, which is crucial for successful SMT assembly. Regular ovens may not distribute heat evenly and can lead to inconsistent results or damage to your components. -
Q: How do I choose the right solder paste for my project?
A: When selecting solder paste, consider factors such as the alloy composition, particle size, and melting temperature. The most common alloy for SMT assembly is SAC305 (Sn96.5/Ag3.0/Cu0.5). Particle size affects the printing and reflow process, with smaller sizes (e.g., Type 3 or Type 4) being suitable for finer pitch components. Consult your component datasheets and PCB design to determine the appropriate solder paste for your project. -
Q: Can I mix different brands or types of components in the same PCB?
A: While it is possible to mix different brands or types of components, it is essential to ensure that they are compatible with each other and with your PCB design. Pay attention to factors such as package size, pitch, and temperature ratings. Mixing components from different manufacturers may also lead to variations in performance and reliability. It is advisable to stick to a consistent set of components from reputable suppliers whenever possible. -
Q: How often should I clean my stencil and other equipment?
A: Regular cleaning of your stencil and other equipment is crucial for maintaining the quality and consistency of your SMT assembly process. Clean your stencil after every use with a specialized stencil cleaner or isopropyl alcohol to remove any solder paste residue. Other equipment, such as your pick and place machine and reflow oven, should be cleaned according to the manufacturer’s recommendations or whenever you notice any buildup of contamination. -
Q: What safety precautions should I take when setting up and operating my SMT assembly line?
A: SMT assembly involves working with high temperatures, chemicals, and sensitive electronic components. Always wear appropriate personal protective equipment (PPE), such as ESD-safe gloves and safety glasses, when handling PCBs and components. Ensure proper ventilation in your workspace to minimize exposure to fumes from solder paste and flux. Follow the manufacturer’s instructions and safety guidelines for all equipment and materials used in the assembly process.
Conclusion
Setting up a DIY SMT assembly line in your office can be a rewarding and cost-effective way to prototype and produce small batches of PCBs. By following the steps and guidelines outlined in this guide, you can create a functional and efficient assembly process that meets your specific needs and requirements.
Remember to invest in quality equipment and materials, maintain a clean and organized workspace, and practice proper technique and safety precautions throughout the assembly process. With patience, persistence, and attention to detail, you can successfully assemble your own PCBs and take your electronics projects to the next level.
Leave a Reply