What is DFM Analysis?
DFM (Design for Manufacturability) analysis is a process of evaluating the design of a product to ensure that it can be manufactured efficiently and cost-effectively. The goal of DFM analysis is to identify potential manufacturing issues early in the design process, allowing for modifications to be made before the product enters production. This approach helps to reduce manufacturing costs, improve product quality, and shorten time-to-market.
Benefits of DFM Analysis
- Cost reduction
- Improved product quality
- Faster time-to-market
- Enhanced collaboration between design and manufacturing teams
- Reduced waste and scrap
Key Elements of DFM Analysis
1. Material Selection
Choosing the right materials is crucial for ensuring the manufacturability of a product. During DFM analysis, designers should consider the following factors when selecting materials:
- Material properties (e.g., strength, durability, thermal stability)
- Cost
- Availability
- Compatibility with manufacturing processes
- Environmental impact
2. Manufacturing Process Selection
Selecting the appropriate manufacturing processes is essential for optimizing production efficiency and reducing costs. Some common manufacturing processes include:
- Injection molding
- CNC machining
- 3D printing
- Sheet metal fabrication
- Casting
During DFM analysis, designers should evaluate the suitability of different manufacturing processes based on factors such as:
- Part geometry
- Material properties
- Production volume
- Tolerances
- Surface finish requirements
3. Tolerance Analysis
Tolerance analysis involves evaluating the dimensional variations of a product’s features to ensure that they can be manufactured consistently and within acceptable limits. During DFM analysis, designers should:
- Specify appropriate tolerances for each feature
- Analyze the impact of tolerance stackup on product functionality and assembly
- Consider the capabilities of the selected manufacturing processes
Tolerance Types
Tolerance Type | Description |
---|---|
Bilateral | Specifies a symmetric range around a nominal dimension (e.g., 10 ± 0.1 mm) |
Unilateral | Specifies a one-sided limit (e.g., 10 +0.1/-0 mm) |
Geometric | Defines the allowable variations in form, orientation, location, and runout |
4. Design for Assembly (DFA)
DFA is a subset of DFM that focuses on optimizing product design for efficient assembly. During DFA analysis, designers should:
- Minimize the number of parts
- Standardize components
- Design parts for easy insertion and alignment
- Avoid the need for specialized assembly tools
- Consider the ergonomics of the assembly process
5. Cost Analysis
Cost analysis is an integral part of DFM, as it helps designers to make informed decisions about product design and manufacturing processes. During cost analysis, designers should:
- Estimate the cost of materials, manufacturing processes, and assembly
- Identify cost drivers and opportunities for cost reduction
- Evaluate the impact of design changes on overall product cost
- Consider the trade-offs between cost and other factors such as performance and quality
DFM Analysis Tools and Techniques
Several tools and techniques can be used to support DFM analysis, including:
- CAD (Computer-Aided Design) software
- CAM (Computer-Aided Manufacturing) software
- FEA (Finite Element Analysis)
- Mold flow analysis
- Value engineering
- Failure Mode and Effects Analysis (FMEA)
- Design for Six Sigma (DFSS)
CAD and CAM Software
CAD and CAM software play a crucial role in DFM analysis by enabling designers to create, modify, and analyze product designs digitally. These tools allow for:
- 3D modeling and visualization
- Tolerance analysis
- Manufacturability checks
- Generation of CNC machine code
- Simulation of manufacturing processes
CAD/CAM Software | Key Features |
---|---|
AutoCAD | 2D and 3D drafting, customization with APIs |
SolidWorks | 3D modeling, simulation, design validation |
Fusion 360 | Cloud-based CAD/CAM, collaboration tools |
Siemens NX | Advanced modeling, simulation, and manufacturing capabilities |
FEA and Mold Flow Analysis
FEA and mold flow analysis are simulation techniques used to predict the behavior of products under various conditions. These tools help designers to:
- Evaluate the structural integrity of a design
- Identify potential failure points
- Optimize material usage and wall thicknesses
- Predict the flow of molten plastic during injection molding
- Identify potential manufacturing defects, such as warpage and sink marks
Value Engineering and FMEA
Value engineering and FMEA are systematic approaches to analyzing and improving product design and manufacturing processes. These techniques involve:
- Identifying the functions of a product and its components
- Evaluating the value of each function relative to its cost
- Identifying potential failure modes and their effects on product performance
- Assessing the risk associated with each failure mode
- Developing strategies to mitigate or eliminate potential failures
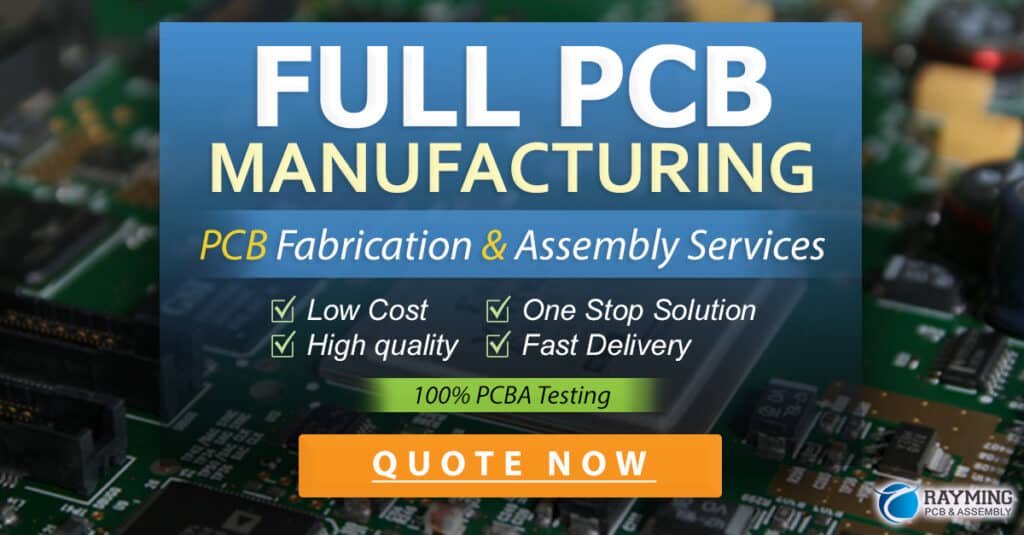
Implementing DFM Analysis in the Product Development Process
To effectively implement DFM analysis, organizations should follow these best practices:
- Integrate DFM analysis early in the design process
- Foster collaboration between design and manufacturing teams
- Establish clear design guidelines and standards
- Use appropriate tools and techniques for analysis
- Continuously monitor and improve the DFM process
DFM Analysis Workflow
A typical DFM analysis workflow includes the following steps:
- Conceptual design
- Detailed design
- DFM analysis
- Design optimization
- Prototyping and testing
- Manufacturing planning
- Production ramp-up
- Continuous improvement
Case Studies
Case Study 1: Automotive Component Redesign
A leading automotive supplier used DFM analysis to redesign a complex engine component. By applying DFM principles, the company achieved:
- 30% reduction in manufacturing costs
- 20% improvement in production efficiency
- 50% reduction in scrap rates
- Improved component performance and reliability
Case Study 2: Consumer Electronics Product Launch
A consumer electronics company employed DFM analysis to optimize the design of a new smartphone. The results included:
- Streamlined product design with fewer parts
- Improved assembly efficiency
- Reduced time-to-market by 25%
- Enhanced product quality and customer satisfaction
Frequently Asked Questions (FAQ)
- What is the difference between DFM and DFA?
-
DFM focuses on optimizing product design for efficient manufacturing, while DFA emphasizes designing products for easy assembly.
-
At what stage of the product development process should DFM analysis be performed?
-
DFM analysis should be integrated early in the design process, ideally during the conceptual and detailed design stages.
-
What are the key benefits of implementing DFM analysis?
-
The main benefits of DFM analysis include cost reduction, improved product quality, faster time-to-market, and enhanced collaboration between design and manufacturing teams.
-
How does DFM analysis help to reduce manufacturing costs?
-
DFM analysis helps to reduce manufacturing costs by identifying potential issues early in the design process, allowing for design optimizations that improve production efficiency and minimize waste.
-
What tools and techniques are commonly used in DFM analysis?
- Common tools and techniques used in DFM analysis include CAD/CAM software, FEA, mold flow analysis, value engineering, and FMEA.
Conclusion
DFM analysis is a powerful approach to optimizing product design for efficient and cost-effective manufacturing. By integrating DFM principles early in the product development process, organizations can reduce costs, improve quality, and accelerate time-to-market. Effective implementation of DFM analysis requires collaboration between design and manufacturing teams, the use of appropriate tools and techniques, and a commitment to continuous improvement. As industries continue to evolve and competition intensifies, DFM analysis will remain a critical strategy for companies seeking to maintain a competitive edge in the global marketplace.
Leave a Reply