Overview of Active Cooling Techniques
Active cooling techniques involve the use of external devices or systems to remove heat from electronic components actively. These techniques are employed when passive cooling methods, such as heat sinks or natural convection, are insufficient to dissipate the generated heat effectively. Active cooling techniques can be categorized into several main types:
- Forced Air Cooling
- Liquid Cooling
- Thermoelectric Cooling
- Phase Change Cooling
- Vapor Chamber Cooling
Each of these techniques has its own characteristics, benefits, and drawbacks, which will be discussed in detail in the following sections.
Forced Air Cooling
Forced air cooling is one of the most common active cooling techniques used in electronic equipment. It involves the use of fans or blowers to create a flow of air over the electronic components, enhancing heat dissipation through convection.
Principles of Forced Air Cooling
Forced air cooling relies on the principle of convective heat transfer. When air flows over a heated surface, it absorbs heat from the surface, leading to cooling. The effectiveness of forced air cooling depends on several factors, including:
- Airflow rate: Higher airflow rates generally result in better cooling performance.
- Heat sink design: The design of the heat sink, including its surface area, fin spacing, and material, affects the heat dissipation capacity.
- Air temperature: Cooler air temperatures enhance the cooling effectiveness.
Types of Fans and Blowers
Fans and blowers are the primary components used in forced air cooling systems. They can be classified based on their design and airflow characteristics:
- Axial Fans: Axial fans generate airflow parallel to the fan’s axis of rotation. They are commonly used in computer cases and CPU coolers.
- Centrifugal Fans: Centrifugal fans, also known as blowers, generate airflow perpendicular to the fan’s axis of rotation. They are often used in high-pressure applications.
- Cross-Flow Fans: Cross-flow fans provide a wide, uniform airflow across a large area. They are suitable for cooling multiple components simultaneously.
Advantages and Limitations
Advantages of forced air cooling include:
- Cost-effective and widely available
- Easy to implement and maintain
- Suitable for a wide range of applications
Limitations of forced air cooling include:
- Limited cooling capacity compared to other techniques
- Noise generation from fans or blowers
- Dust accumulation on heat sinks and fans over time
Liquid Cooling
Liquid cooling is another popular active cooling technique that offers higher heat dissipation capacity compared to forced air cooling. It involves the use of a liquid coolant to absorb and transport heat away from electronic components.
Principles of Liquid Cooling
Liquid cooling systems typically consist of a cold plate, a pump, a radiator, and a reservoir. The cold plate is in direct contact with the heat-generating components, and the liquid coolant absorbs heat as it flows through the cold plate. The heated coolant is then pumped to the radiator, where it dissipates heat to the surrounding air. The cooled liquid is then recirculated back to the cold plate.
Types of Liquid Cooling Systems
Liquid cooling systems can be classified into two main types:
- Closed-Loop Liquid Cooling: Closed-loop systems are pre-assembled and sealed, requiring no maintenance. They are commonly used in high-performance computer systems.
- Custom Liquid Cooling: Custom liquid cooling systems allow for flexibility in design and component selection. They are often used in enthusiast-level PC builds and data centers.
Advantages and Limitations
Advantages of liquid cooling include:
- Higher heat dissipation capacity compared to air cooling
- Quieter operation due to reduced fan speeds
- Improved overclocking potential for high-performance systems
Limitations of liquid cooling include:
- Higher cost compared to air cooling
- Potential for leaks and maintenance requirements
- Complexity in installation and setup
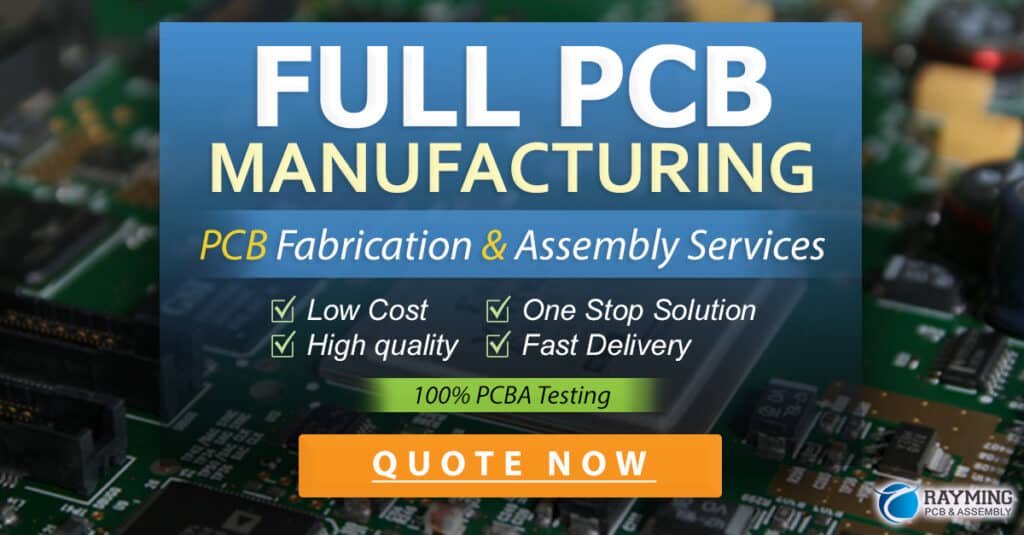
Thermoelectric Cooling
Thermoelectric cooling, also known as Peltier cooling, is based on the Peltier effect, which involves the creation of a temperature difference across a thermoelectric module when an electric current is applied.
Principles of Thermoelectric Cooling
A thermoelectric module consists of two ceramic plates with a series of p-type and n-type semiconductor elements sandwiched between them. When a DC current is applied, heat is absorbed on one side of the module (cold side) and released on the other side (hot side). By placing the cold side in contact with the electronic component and the hot side with a heat sink, heat can be effectively removed from the component.
Advantages and Limitations
Advantages of thermoelectric cooling include:
- No moving parts, resulting in high reliability
- Precise temperature control
- Compact size and lightweight
Limitations of thermoelectric cooling include:
- Limited cooling capacity compared to other techniques
- High power consumption and low efficiency
- Expensive for large-scale applications
Phase Change Cooling
Phase change cooling leverages the latent heat of vaporization to absorb heat from electronic components. It involves the use of a refrigerant that undergoes a phase change from liquid to vapor and vice versa.
Principles of Phase Change Cooling
In a phase change cooling system, the refrigerant absorbs heat from the electronic component, causing it to evaporate. The vapor is then compressed, raising its temperature and pressure. The hot vapor is then cooled and condensed back into a liquid in a condenser, releasing the heat to the environment. The liquid refrigerant is then expanded and returned to the evaporator, completing the cycle.
Advantages and Limitations
Advantages of phase change cooling include:
- High heat dissipation capacity
- Efficient cooling performance
- Suitable for high-power electronic components
Limitations of phase change cooling include:
- Complexity in design and implementation
- Higher cost compared to other cooling techniques
- Potential for refrigerant leaks and environmental concerns
Vapor Chamber Cooling
Vapor chamber cooling is a passive cooling technique that uses a sealed chamber filled with a working fluid to distribute heat evenly across a large surface area.
Principles of Vapor Chamber Cooling
A vapor chamber consists of a hollow chamber with a wick structure lining its inner walls. The chamber is partially filled with a working fluid, such as water or alcohol. When heat is applied to one side of the vapor chamber, the working fluid evaporates, absorbing heat. The vapor then travels to the cooler regions of the chamber, where it condenses back into a liquid, releasing the heat. The liquid is then drawn back to the hot spot through the wick structure by capillary action, completing the cycle.
Advantages and Limitations
Advantages of vapor chamber cooling include:
- Uniform heat distribution across a large surface area
- Passive operation without moving parts
- Compact and lightweight design
Limitations of vapor chamber cooling include:
- Limited heat dissipation capacity compared to active cooling techniques
- Higher cost compared to traditional heat spreaders
- Potential for performance degradation if the wick structure is damaged
Comparison of Active Cooling Techniques
To summarize the comparison of active cooling techniques for electronic equipment, the following table provides an overview of their key characteristics:
Cooling Technique | Heat Dissipation Capacity | Noise Level | Cost | Complexity |
---|---|---|---|---|
Forced Air Cooling | Moderate | High | Low | Low |
Liquid Cooling | High | Low | High | Moderate |
Thermoelectric Cooling | Low to Moderate | Low | High | Moderate |
Phase Change Cooling | High | Moderate | High | High |
Vapor Chamber Cooling | Moderate | Low | Moderate | Low |
The choice of the most suitable active cooling technique depends on various factors, including the specific application, heat dissipation requirements, available space, budget, and environmental conditions.
Frequently Asked Questions (FAQ)
-
Q: What is the main difference between active and passive cooling techniques?
A: Active cooling techniques involve the use of external devices or systems to actively remove heat from electronic components, while passive cooling techniques rely on natural heat transfer mechanisms such as conduction and convection without the use of external power. -
Q: Can multiple active cooling techniques be combined for better performance?
A: Yes, multiple active cooling techniques can be used in combination to achieve enhanced cooling performance. For example, liquid cooling can be used in conjunction with forced air cooling to dissipate heat more effectively. -
Q: What factors should be considered when selecting an active cooling technique?
A: When selecting an active cooling technique, factors such as the heat dissipation requirements, available space, noise level, cost, and complexity should be considered. The specific application and environmental conditions also play a role in determining the most suitable cooling technique. -
Q: Are active cooling techniques necessary for all electronic equipment?
A: Active cooling techniques are not always necessary for all electronic equipment. In some cases, passive cooling techniques such as heat sinks or natural convection may be sufficient to dissipate the generated heat. Active cooling is typically required when the heat generation exceeds the capacity of passive cooling methods. -
Q: What are the common maintenance requirements for active cooling systems?
A: Common maintenance requirements for active cooling systems include regular cleaning of heat sinks and fans to remove dust accumulation, checking for proper operation of fans or pumps, and inspecting for any leaks or damage in liquid cooling systems. Proper maintenance ensures optimal cooling performance and extends the lifespan of the cooling components.
Conclusion
Active cooling techniques play a vital role in maintaining optimal operating temperatures for electronic equipment. This article explored and compared various active cooling techniques, including forced air cooling, liquid cooling, thermoelectric cooling, phase change cooling, and vapor chamber cooling. Each technique has its own principles, advantages, and limitations, and the choice of the most suitable technique depends on the specific application and requirements.
Understanding the principles and characteristics of different active cooling techniques enables engineers and designers to make informed decisions when selecting the appropriate cooling solution for their electronic systems. By implementing effective active cooling techniques, the performance, reliability, and longevity of electronic equipment can be significantly enhanced.
As electronic devices continue to advance and generate more heat, the development and optimization of active cooling techniques will remain crucial. Future research and innovations in active cooling technologies aim to improve cooling efficiency, reduce noise levels, and address the challenges associated with high-power electronic components.
Leave a Reply