Introduction to Flex PCBs and Mechanical Design Considerations
Flexible printed circuit boards (flex PCBs) offer many advantages over rigid PCBs in applications that require the circuit to bend, fold, twist, or fit into tight spaces. Flex PCBs can be designed for either static or dynamic flexing depending on the requirements. Static flex designs are intended for circuits that will be bent or folded into a fixed shape during installation and remain in that static position during use. Dynamic flex designs allow for repeated flexing and movement of the circuit during operation.
The mechanical design considerations for static vs dynamic flex PCBs differ significantly. Key factors that influence the mechanical performance and reliability of a flex PCB include:
- Copper weight and plating
- Dielectric material selection
- Number of layers and stacking
- Bend radius and bend locations
- Strain relief features
- Stiffeners and rigid areas
This article will explore these mechanical design topics in depth and compare the key considerations for static vs dynamic flex PCB applications. By understanding the critical design factors, PCB designers can create robust flex circuits that meet all mechanical and electrical requirements.
Copper Weight, Plating, and Flexibility Trade-offs
The copper weight used in the flex PCB construction is one of the main factors that determines the flexibility and mechanical strength of the circuit. Thinner copper enables a tighter bend radius and greater flexibility but provides less mechanical strength. Thicker copper improves strength and current carrying capacity but reduces flexibility.
Typical copper weights used for flex PCBs range from 0.5 oz to 2 oz (17 μm to 70 μm thickness). For most flex applications, 1 oz copper provides a good balance of flexibility, strength, and conductivity. Static flex designs can often use slightly thicker 1.5 oz or 2 oz copper for improved robustness, while dynamic flex circuits typically require 1 oz or thinner copper to allow repeated flexing.
Copper plating also impacts flexibility. Electrodeposited (ED) copper is more ductile than rolled annealed (RA) copper foil and therefore allows a tighter bend radius, but RA copper provides higher strength and fatigue resistance. For dynamic flex applications, RA copper is typically preferred.
The table below summarizes the trade-offs between copper weight, flexibility, and strength:
Copper Weight | Thickness | Flexibility | Strength |
---|---|---|---|
0.5 oz | 17 μm | High | Low |
1 oz | 35 μm | Medium | Medium |
2 oz | 70 μm | Low | High |
Dielectric Material Selection for Flex Circuits
The choice of dielectric material is critical for the mechanical performance and environmental resistance of a flex PCB. The dielectric must be flexible enough to allow the desired bending, provide good insulation between conductive layers, withstand environmental stresses, and meet the required electrical properties such as dielectric constant and loss tangent.
Polyimide (PI) is by far the most common dielectric material used for flex circuits. PI films offer excellent combination of mechanical, thermal, chemical, and electrical properties. The most widely used PI film is DuPont™ Kapton® which is available in various grades optimized for different flex applications and environmental requirements.
For extreme environments, specialized PI films or other polymers may be used. For example, Ube Upilex® polyimide offers higher heat resistance than Kapton, up to 400°C. Liquid crystal polymers (LCP) provide very low moisture absorption and high chemical resistance. Flexible solder masks and coverlay materials should also be carefully selected based on flexibility, durability, and environmental resistance requirements.
The table below compares key properties of common flex dielectric materials:
Material | Dielectric Constant | Moisture Absorption | Bend Radius (1 oz Cu) | Temp Rating |
---|---|---|---|---|
Kapton | 3.5 | 1.8% | 6X thickness | -269 to 400°C |
Upilex-S | 3.5 | 1.3% | 4X thickness | -269 to 500°C |
LCP | 2.9 | <0.04% | 4X thickness | -269 to 300°C |
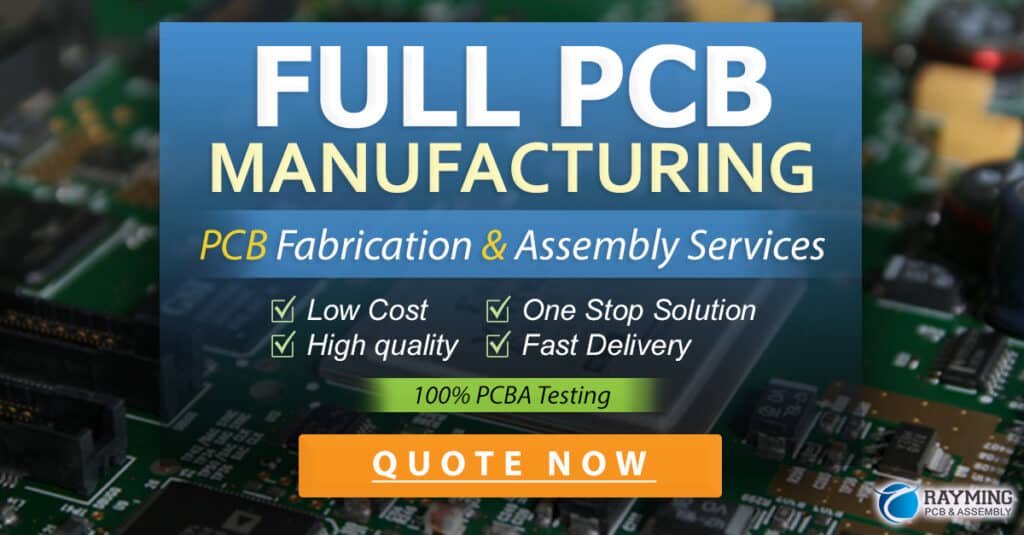
Number of Layers and Stacking Considerations
The number of conductive layers and the layer stacking significantly impact the mechanical properties of a flex circuit. In general, fewer layers enables greater flexibility and a tighter bend radius. Single and double sided flex circuits are the most common and offer the greatest flexibility. Multi-layer flex circuits with 4-16 layers are used for more complex designs but have reduced flexibility due to the increased thickness.
Stacking the layers symmetrically around the neutral bend axis is important to prevent the circuit from warping or twisting during flexing. For dynamic flex applications, keeping the copper layers close to the neutral axis minimizes the bending stress on the conductors. Additional dielectric layers can be added to create a more symmetrical stack while maintaining flexibility.
Bookbinder construction is a common technique used to improve flexibility in multi-layer flex circuits. In this construction, single or double sided flex layers are laminated together with bondply (prepreg) layers in between, rather than laminating all the layers together at once. This allows the individual flex layers to slide relative to each other during bending, reducing mechanical stress.
The table below shows typical layer counts and stacking configurations for different flex applications:
Flex Type | Layers | Typical Stacking |
---|---|---|
Single-sided | 1 | Coverlay-Cu-PI |
Double-sided | 2 | Coverlay-Cu-PI-Cu-Coverlay |
Multi-layer | 4 | Cov-Cu-PI-Cu-Core-Cu-PI-Cu-Cov |
Rigid-flex | Varies | Rigid-Flex-Rigid |
Bookbinder | Varies | (Cov-Cu-PI-Cu-Cov)n |
Bend Radius and Bend Location Design
The minimum bend radius is a critical design parameter for flex circuits that determines the maximum allowable curvature of the circuit during installation and use. Exceeding the minimum bend radius can cause damage to the copper conductors, dielectric, or plated through holes, leading to mechanical failure or degraded electrical performance.
The minimum bend radius depends on several factors including the copper weight, number of layers, dielectric thickness, and coverlay material. In general, the minimum bend radius is specified as a multiple of the total thickness of the flex circuit. For example, a typical specification is 6X the thickness for static flex applications and 10X the thickness for dynamic flexing.
Locating the bend zones in the flex circuit design is also important to ensure reliable flexing performance. Bends should be located away from rigid components, stiffeners, or connectors to avoid stress concentrations. The transition from rigid to flexible zones should be tapered to gradually reduce the stiffness and prevent kinking or tearing of the flex circuit.
For dynamic flex applications, the bend locations should be designed to minimize the stress on the conductors during repeated flexing. One technique is to use “horseshoe” shaped bends that distribute the stress over a larger area compared to a simple 180° bend. Accordion folds or serpentine routing can also be used to allow a greater range of motion in a small space.
The table below provides recommendations for minimum bend radius and location based on IPC-2223 guidelines:
Flex Type | Layers | Minimum Bend Radius | Preferred Bend Location |
---|---|---|---|
Single-sided | 1 | 6X thickness | Away from components |
Double-sided | 2 | 10X thickness | Between components |
Multi-layer | 4+ | 20X thickness | Balanced stack |
Dynamic Flex | Varies | 10-20X thickness | Horseshoe or accordion |
Strain Relief and Stiffener Design
Strain relief and stiffeners are important mechanical features in flex PCBs that help to reduce stress concentrations, prevent damage during assembly or use, and maintain the desired shape of the circuit.
Strain relief is typically provided at the transition between flexible and rigid sections of the circuit, such as at connectors or component interfaces. Without proper strain relief, repeated flexing can cause the copper conductors to crack or delaminate from the dielectric. Common strain relief features include:
- Gradual taper of the dielectric thickness at the rigid-flex interface
- Round or teardrop shaped pads at component leads
- Meanders or curves in the conductor routing near the flex-to-rigid transition
- Slots or cutouts in the rigid area to allow some compliance
Stiffeners are used to selectively increase the rigidity of certain areas of the flex circuit, such as at connector locations or to maintain a specific shape. Stiffeners are typically made from rigid FR-4 material, polyimide, or metal and can be laminated to one or both sides of the flex circuit. The shape and thickness of the stiffener should be designed to provide the necessary support without restricting the flexibility of the adjacent areas.
The table below summarizes common strain relief and stiffener design features:
Feature | Purpose | Design Guidelines |
---|---|---|
Taper | Gradual transition from rigid to flex | 30-45° angle, 0.5-1 mm length |
Pad shape | Prevent copper cracking at component interface | Teardrop or rounded shape |
Conductor relief | Reduce stress concentration near rigid areas | Curved or meandered routing |
Stiffener | Increase local rigidity, maintain shape | FR-4, polyimide, or metal, 0.2-1 mm thick |
Mechanical Testing and Reliability Validation
Mechanical testing and reliability validation are essential to ensure that a flex PCB design meets the required performance and durability specifications. The specific tests required depend on the application and environmental conditions, but common mechanical tests for flex circuits include:
- Bend testing: Measures the flexibility and mechanical strength of the circuit under static or dynamic bending conditions. Typically performed using a custom fixture or mandrel to control the bend radius and angle.
- Twist testing: Evaluates the torsional flexibility and resistance to damage under twisting motions. Often used for circuits that will be subjected to torsional stress during assembly or use.
- Lifetime testing: Determines the number of flex cycles the circuit can withstand before failure. Dynamic flex applications may require testing to millions of cycles, while static flex designs may only require a few hundred cycles.
- Thermal cycling: Assesses the resistance to damage from repeated thermal expansion and contraction. Flex circuits may be subjected to hundreds or thousands of thermal cycles from -40°C to 125°C or higher.
- Shock and vibration: Tests the mechanical robustness of the circuit and solder joints under high acceleration or vibrational stresses. Test conditions are based on the expected environmental conditions such as MIL-STD-810 for military applications.
In addition to testing, finite element analysis (FEA) simulations are often used to predict the mechanical stress and strain distributions in a flex circuit design. FEA can help identify potential failure points and optimize the design for improved reliability.
The table below lists some common mechanical testing specifications for flex circuits:
Test | Specification | Conditions |
---|---|---|
Bend | IPC-TM-650 2.4.3 | 180° bend, 6-10X thickness radius |
Twist | IPC-TM-650 2.4.18 | ±180° twist, 50 mm length |
Dynamic Flex | IPC-TM-650 2.4.3 | 1-10 million cycles, 10-20X radius |
Thermal Cycling | IPC-TM-650 2.6.7 | -40 to 125°C, 100-1000 cycles |
Shock & Vibration | MIL-STD-810 | Application specific |
Flex PCB Design Guidelines and Best Practices
To ensure a robust and reliable flex PCB design, consider the following guidelines and best practices:
-
Choose the appropriate copper weight, dielectric material, and stacking for the application requirements. Thinner copper and fewer layers generally provide greater flexibility.
-
Design the bend radius and bend locations based on the flexibility and mechanical stress requirements. Use a larger bend radius for dynamic flex applications and locate bends away from rigid areas.
-
Incorporate strain relief features at rigid-flex interfaces and component pads. Gradual tapers, rounded pads, and curved conductor routing can help reduce stress concentrations.
-
Use stiffeners strategically to support connectors or maintain specific shapes without restricting flexibility in dynamic areas.
-
Route conductors perpendicular to the bend direction to minimize stretching or compression of the copper. Avoid routing conductors along the bend centerline.
-
Specify a symmetrical layer stack with copper layers close to the neutral bend axis for dynamic flex applications. Use bookbinder construction for multi-layer designs.
-
Allow for adequate spacing between conductors, pads, and vias to accommodate any movement or misalignment during flexing.
-
Perform mechanical simulations and testing to validate the design and ensure it meets the required reliability and durability specifications.
By following these guidelines and carefully considering the mechanical requirements, PCB designers can create robust and reliable flex circuits for a wide range of static and dynamic applications.
Flex PCB Design FAQs
What is the minimum bend radius for a single-sided flex PCB?
The minimum recommended bend radius for a single-sided flex PCB is typically 6 times the total thickness of the circuit. For example, a 0.2 mm thick single-sided flex PCB would have a minimum bend radius of 1.2 mm.
Can I use the same design rules for static and dynamic flex PCBs?
No, dynamic flex PCBs have more stringent design requirements than static flex PCBs. Dynamic flex circuits typically require a larger bend radius (10-20X thickness), thinner copper (0.5-1 oz), and additional strain relief features to withstand repeated flexing. Static flex designs can often use tighter bend radii and thicker copper for improved robustness.
What is bookbinder construction and when is it used?
Bookbinder construction is a technique used to fabricate multi-layer flex circuits with improved flexibility. In this construction, individual double-sided flex layers are laminated together with bondply (prepreg) layers in between, rather than laminating all layers at once. This allows the layers to slide relative to each other during bending, reducing stress. Bookbinder construction is commonly used for designs with 6 or more layers that require high flexibility.
How do I select the right stiffener material and thickness?
The choice of stiffener material and thickness depends on the specific application requirements. Common stiffener materials include FR-4, polyimide, and metal (stainless steel or aluminum). FR-4 is a cost-effective option for most applications, while polyimide provides better flexibility and thermal stability. Metal stiffeners offer the highest rigidity and thermal conductivity but add weight. The stiffener thickness typically ranges from 0.2 mm to 1 mm depending on the required stiffness and space constraints. Thicker stiffeners provide more rigidity but may restrict flexibility in adjacent areas.
What testing should I perform to validate my flex PCB design?
The specific testing requirements for a flex PCB depend on the application and environmental conditions, but common mechanical tests include bend testing, twist testing, lifetime cycling, thermal cycling, and shock/vibration. Bend and twist testing evaluate the flexibility and mechanical strength under static or dynamic bending conditions. Lifetime cycling determines the number of flex cycles the circuit can withstand before failure. Thermal cycling and shock/vibration testing assess the resistance to damage from environmental stresses. In addition to mechanical testing, electrical testing (continuity, insulation resistance, etc.) and visual inspection should be performed to ensure the circuit meets all functional and quality requirements.
Leave a Reply