What is a PCB Layer Stackup?
A PCB (Printed Circuit Board) layer stackup refers to the arrangement of copper and insulating layers that make up a printed circuit board. It is a critical aspect of PCB design, as it determines the board’s electrical properties, signal integrity, and manufacturability. Communicating your PCB layer stackup requirements effectively to your manufacturer is essential to ensure that your board meets your design specifications and functions as intended.
Key Elements of a PCB Layer Stackup
When defining your PCB layer stackup, you need to consider the following key elements:
- Number of layers
- Copper weight for each layer
- Dielectric material and thickness
- Impedance requirements
- Via structure and sizes
- Solder mask and silkscreen specifications
Why is Communicating PCB Layer Stackup Important?
Clearly communicating your PCB layer stackup requirements to your manufacturer is crucial for several reasons:
-
Ensuring design integrity: Your layer stackup directly impacts your board’s electrical performance and signal integrity. By providing clear specifications, you ensure that your manufacturer understands your design intent and can produce a board that meets your requirements.
-
Optimizing manufacturability: Different manufacturers may have different capabilities and constraints when it comes to PCB fabrication. By engaging with your manufacturer early and communicating your stackup needs, you can ensure that your design is manufacturable and avoid potential issues or delays.
-
Controlling costs: Your layer stackup choices can significantly impact the cost of your PCB. By working closely with your manufacturer and understanding their capabilities, you can optimize your stackup to balance performance and cost-effectiveness.
How to Communicate PCB Layer Stackup to Manufacturers
To effectively communicate your PCB layer stackup requirements to your manufacturer, follow these best practices:
1. Use a Standardized Stackup Table
Create a clear and concise stackup table that includes all the necessary information. A typical stackup table should include:
Layer | Material | Thickness (mil) | Copper Weight (oz) | Dielectric Constant (Dk) | Loss Tangent (Df) |
---|---|---|---|---|---|
Top Solder Mask | Solder Mask | 0.5 | – | – | – |
Top Copper | Copper | 1.4 | 1 | – | – |
Core | FR-4 | 6.7 | – | 4.5 | 0.02 |
Bottom Copper | Copper | 1.4 | 1 | – | – |
Bottom Solder Mask | Solder Mask | 0.5 | – | – | – |
2. Provide Detailed Layer Descriptions
In addition to the stackup table, provide a detailed description of each layer, including its purpose, routing requirements, and any special considerations. For example:
- Layer 1 (Top): Signal layer, 50-ohm single-ended traces, 100-ohm differential pairs
- Layer 2 (Ground): Solid ground plane
- Layer 3 (Power): Split power plane, 3.3V and 1.8V rails
- Layer 4 (Bottom): Signal layer, 50-ohm single-ended traces, 100-ohm differential pairs
3. Specify Impedance Requirements
If your design has specific impedance requirements, clearly communicate them to your manufacturer. Provide the target impedance values, tolerance, and any special considerations for each signal layer. For example:
- Single-ended traces: 50 ohms ±10%
- Differential pairs: 100 ohms ±10%, spacing between traces: 5 mil
4. Define Via Structure and Sizes
Clearly specify the via structure and sizes for your PCB. Include information on via types (through, blind, or buried), diameters, and drill sizes. For example:
- Through vias: 10 mil diameter, 6 mil drill
- Blind vias (Top to Layer 2): 8 mil diameter, 5 mil drill
- Buried vias (Layer 2 to Layer 3): 6 mil diameter, 4 mil drill
5. Communicate Solder Mask and Silkscreen Requirements
Provide detailed specifications for your solder mask and silkscreen requirements. Include information on color, finish, and any special markings or text. For example:
- Solder mask: Green, matte finish, clearance around pads: 2 mil
- Silkscreen: White, top side only, include company logo and part number
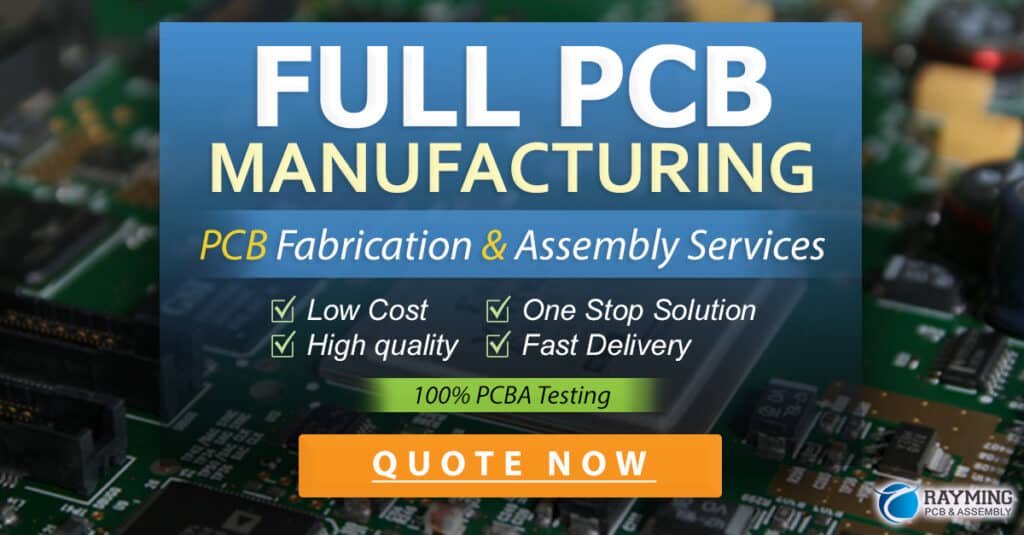
PCB Layer Stackup Design Considerations
When designing your PCB layer stackup, keep the following considerations in mind:
Signal Integrity
Your layer stackup plays a critical role in maintaining signal integrity. Consider the following factors:
- Proper grounding and power distribution
- Impedance control for critical signals
- Minimizing crosstalk and electromagnetic interference (EMI)
- Adequate spacing between traces and planes
Manufacturability
Ensure that your layer stackup is manufacturable by considering:
- Your manufacturer’s capabilities and constraints
- Standard materials and thicknesses
- Minimum via sizes and spacing
- Copper weight limitations
Cost Optimization
Optimize your layer stackup for cost-effectiveness by:
- Minimizing the number of layers when possible
- Using standard materials and thicknesses
- Avoiding unnecessary features or tight tolerances
- Considering the impact of your stackup choices on yield and throughput
Frequently Asked Questions (FAQ)
1. What is the difference between a symmetrical and asymmetrical stackup?
A symmetrical stackup has an equal number of layers above and below the center core, while an asymmetrical stackup has an unequal number of layers. Symmetrical stackups are generally preferred for their better mechanical and thermal properties, as they minimize warping and stress on the board.
2. How do I determine the number of layers needed for my PCB?
The number of layers in your PCB stackup depends on factors such as the complexity of your design, routing density, signal integrity requirements, and power distribution needs. Work with your design team and manufacturer to determine the optimal number of layers for your specific application.
3. What are the most common materials used in PCB layer stackups?
The most common materials used in PCB layer stackups are:
- FR-4: A glass-reinforced epoxy laminate, widely used for its good mechanical and electrical properties.
- Rogers: High-frequency laminates with low dielectric loss, used for RF and microwave applications.
- Isola: A range of high-performance laminates for demanding applications, such as automotive and aerospace.
4. How do I ensure proper impedance control in my PCB layer stackup?
To ensure proper impedance control in your PCB layer stackup:
- Define your target impedance values and tolerances for critical signals.
- Work with your manufacturer to select suitable dielectric materials and thicknesses.
- Use appropriate trace widths and spacing based on your impedance calculations.
- Consider the use of dedicated reference planes for critical signals.
5. Can I mix different copper weights within the same PCB layer stackup?
Yes, it is possible to mix different copper weights within the same PCB layer stackup. This is often done to optimize cost and performance, with thicker copper used for power layers and thinner copper for signal layers. However, mixing copper weights can impact the manufacturability and cost of your board, so it is essential to consult with your manufacturer early in the design process.
Conclusion
Communicating your PCB layer stackup requirements effectively to your manufacturer is essential for ensuring that your board meets your design specifications and functions as intended. By providing clear and concise stackup tables, detailed layer descriptions, impedance requirements, via structures, and solder mask and silkscreen specifications, you can help your manufacturer understand your design intent and optimize your board for manufacturability and cost-effectiveness.
Remember to consider signal integrity, manufacturability, and cost optimization when designing your PCB layer stackup, and work closely with your design team and manufacturer throughout the process. By following these best practices and maintaining open communication with your manufacturer, you can ensure the success of your PCB project and bring your electronic designs to life.
Leave a Reply