Introduction to Signal Integrity Pitfalls
Signal integrity is a critical aspect of electronic design that ensures the proper functioning and reliability of electronic systems. It involves the analysis and management of signal propagation through interconnects, such as printed circuit board (PCB) traces, cables, and connectors. However, designers often encounter various signal integrity pitfalls that can lead to system failures, performance degradation, and increased development time and costs. In this article, we will discuss some common signal integrity pitfalls and provide guidance on how to avoid them.
Understanding the Basics of Signal Integrity
Before delving into the common pitfalls, it is essential to understand the basics of signal integrity. Signal integrity refers to the ability of an electronic system to maintain the quality and integrity of signals as they propagate through interconnects. It involves the analysis of factors such as signal reflection, crosstalk, attenuation, and distortion.
Key Concepts in Signal Integrity
- Impedance Matching
- Importance of matching source and load impedances
-
Effects of impedance mismatches on signal quality
-
Transmission Line Effects
- Understanding the behavior of high-speed signals on PCB traces
-
Reflections and signal distortions caused by discontinuities
-
Crosstalk
- Coupling of signals between adjacent traces
-
Near-end and far-end crosstalk
-
Signal Attenuation and Dispersion
- Loss of signal strength over distance
- Frequency-dependent losses and their impact on signal integrity
Common Signal Integrity Pitfalls
1. Inadequate PCB Layout and Routing
One of the most common signal integrity pitfalls is improper PCB layout and routing. Poor layout practices can lead to signal integrity issues such as crosstalk, reflections, and electromagnetic interference (EMI).
Pitfalls in PCB Layout and Routing
- Insufficient trace spacing
- Inadequate spacing between signal traces can lead to crosstalk
-
Recommended spacing depends on signal speed and PCB material
-
Improper trace impedance control
- Inconsistent trace widths and spacing can cause impedance mismatches
-
Impedance discontinuities result in reflections and signal distortions
-
Lack of ground planes and power planes
- Absence of proper reference planes can lead to signal integrity issues
-
Ground and power planes provide a low-impedance return path for signals
-
Incorrect trace routing
- Routing traces with sharp corners or long parallel runs can cause reflections and crosstalk
- Proper routing techniques, such as 45-degree angles and avoiding parallel runs, should be followed
Best Practices for PCB Layout and Routing
- Use appropriate trace spacing based on signal speed and PCB material
- Maintain consistent trace widths and spacing for impedance control
- Implement ground planes and power planes for proper signal referencing
- Follow proper trace routing techniques, such as using 45-degree angles and avoiding long parallel runs
- Perform signal integrity simulations to validate PCB layout and routing
2. Inadequate Signal Termination
Signal termination is another critical aspect of signal integrity that is often overlooked. Improper termination can lead to signal reflections, overshoots, and undershoots, which can cause system malfunctions and reliability issues.
Pitfalls in Signal Termination
- Lack of termination
- Unterminated high-speed signals can lead to reflections and ringing
-
Reflections can cause false triggering and timing violations
-
Incorrect termination values
- Using incorrect termination resistor values can result in impedance mismatches
-
Mismatched impedances lead to reflections and signal distortions
-
Improper placement of termination components
- Placing termination resistors too far from the source or load can reduce their effectiveness
- Long trace lengths between the termination and the source/load can introduce reflections
Best Practices for Signal Termination
- Use appropriate termination techniques based on signal characteristics and system requirements
-
Common termination techniques include series termination, parallel termination, and AC termination
-
Select the correct termination resistor values to match the characteristic impedance of the transmission line
- Place termination components as close to the source or load as possible to minimize reflections
- Consider the use of on-chip termination for high-speed interfaces
3. Inadequate Power Integrity
Power integrity is closely related to signal integrity and plays a crucial role in ensuring the proper functioning of electronic systems. Inadequate power integrity can lead to signal degradation, noise, and system instability.
Pitfalls in Power Integrity
- Insufficient decoupling capacitors
- Lack of proper decoupling can lead to power supply noise and voltage fluctuations
-
High-frequency noise can couple into sensitive circuits and degrade signal quality
-
Improper placement of decoupling capacitors
- Placing decoupling capacitors too far from the power pins of ICs can reduce their effectiveness
-
Long trace lengths between the capacitors and the ICs can introduce inductance and limit the decoupling performance
-
Inadequate power plane design
- Thin or discontinuous power planes can lead to high impedance and voltage drops
- Poor power plane design can result in noise coupling and signal integrity issues
Best Practices for Power Integrity
- Use appropriate decoupling capacitors with the right values and package sizes
- Select capacitor values based on the frequency range of the noise to be filtered
-
Use a combination of bulk and ceramic capacitors to cover a wide frequency range
-
Place decoupling capacitors as close to the power pins of ICs as possible
-
Minimize the trace lengths between the capacitors and the ICs to reduce inductance
-
Design robust power planes with adequate thickness and continuity
- Use wide and uninterrupted power planes to minimize impedance and voltage drops
-
Avoid splitting power planes or creating narrow necks that can cause noise coupling
-
Perform power integrity simulations to analyze voltage drops, current density, and noise
4. Inadequate Signal Integrity Simulations
Signal integrity simulations are essential for identifying and mitigating potential signal integrity issues early in the design process. Neglecting or inadequate simulations can lead to costly redesigns and delayed product launches.
Pitfalls in Signal Integrity Simulations
- Lack of pre-layout simulations
- Failing to perform signal integrity simulations before PCB layout can lead to suboptimal designs
-
Pre-layout simulations help in identifying potential issues and optimizing the design
-
Inaccurate or incomplete simulation models
- Using inaccurate or incomplete models of components and interconnects can lead to misleading simulation results
-
Inaccurate models can result in over-design or under-design of the system
-
Neglecting the impact of manufacturing variations
- Not considering the effects of manufacturing tolerances and variations can lead to signal integrity issues in production
- Manufacturing variations can affect impedance, crosstalk, and signal propagation
Best Practices for Signal Integrity Simulations
- Perform pre-layout simulations to optimize the design and identify potential issues early
-
Use schematic-level simulations to analyze signal integrity before PCB layout
-
Use accurate and validated simulation models for components and interconnects
-
Obtain models from component manufacturers or create custom models based on measurements
-
Consider the impact of manufacturing variations in simulations
- Perform Monte Carlo simulations to analyze the effects of manufacturing tolerances
-
Use corner case analysis to assess the worst-case scenarios
-
Validate simulation results with measurements on prototypes or test boards
5. Inadequate High-Speed Connector Selection
Connectors play a critical role in high-speed systems, and selecting the wrong connectors can lead to signal integrity issues. Inadequate connector selection can result in impedance mismatches, crosstalk, and signal degradation.
Pitfalls in High-Speed Connector Selection
- Choosing connectors with incompatible impedance
- Using connectors with impedance that does not match the system impedance can cause reflections and signal distortions
-
Impedance mismatches at the connector interfaces can degrade signal quality
-
Neglecting connector crosstalk
- High-density connectors with closely spaced pins can lead to crosstalk between adjacent signals
-
Crosstalk can cause signal integrity issues and reduce the overall system performance
-
Ignoring connector bandwidth limitations
- Using connectors with insufficient bandwidth for the desired signal speeds can result in signal attenuation and distortion
- Bandwidth limitations can limit the maximum data rates that can be achieved
Best Practices for High-Speed Connector Selection
- Choose connectors with compatible impedance to match the system impedance
- Select connectors with well-controlled impedance characteristics
-
Consider the use of impedance-matched connectors for critical high-speed interfaces
-
Evaluate connector crosstalk performance
- Review connector specifications and crosstalk data provided by the manufacturer
-
Consider the use of shielded connectors or connectors with improved crosstalk isolation
-
Ensure connector bandwidth is sufficient for the desired signal speeds
- Select connectors with adequate bandwidth to support the maximum data rates
-
Consider the use of high-performance connectors for high-speed applications
-
Perform signal integrity simulations and measurements to validate connector performance
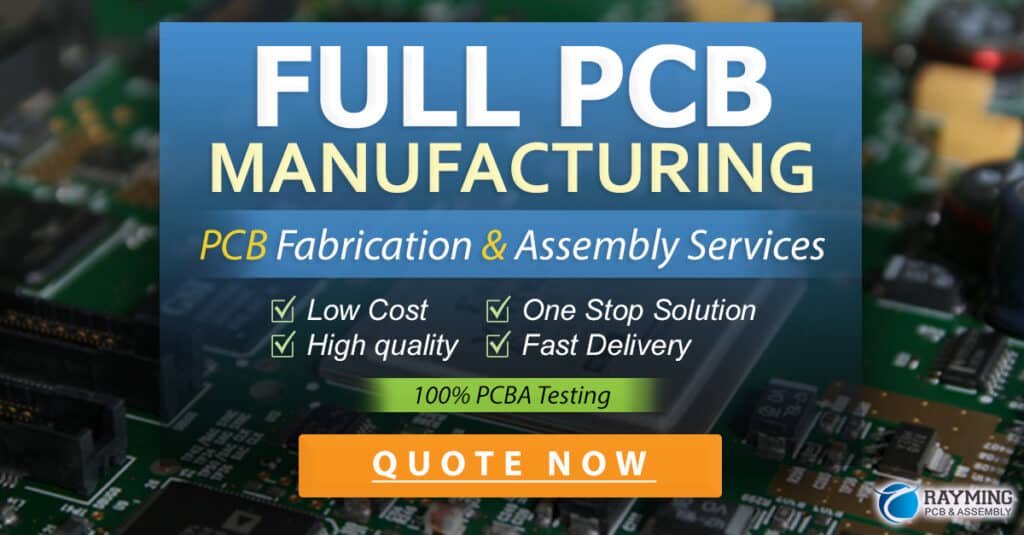
Frequently Asked Questions (FAQ)
-
What is signal integrity, and why is it important?
Signal integrity refers to the ability of an electronic system to maintain the quality and integrity of signals as they propagate through interconnects. It is important because poor signal integrity can lead to system malfunctions, performance degradation, and reliability issues. -
What are some common signal integrity pitfalls?
Some common signal integrity pitfalls include inadequate PCB layout and routing, inadequate signal termination, inadequate power integrity, inadequate signal integrity simulations, and inadequate high-speed connector selection. -
How can I avoid signal integrity issues in my PCB design?
To avoid signal integrity issues in PCB design, follow best practices such as appropriate trace spacing, consistent trace impedance control, proper ground and power plane design, correct trace routing techniques, and performing signal integrity simulations. -
What is the importance of signal termination in signal integrity?
Signal termination is important in signal integrity because it helps to minimize signal reflections, overshoots, and undershoots. Proper termination ensures that the signal is absorbed at the end of the transmission line, preventing reflections that can cause system malfunctions and reliability issues. -
How can signal integrity simulations help in identifying and mitigating issues?
Signal integrity simulations help in identifying potential signal integrity issues early in the design process. They allow designers to analyze factors such as impedance mismatches, crosstalk, reflections, and signal attenuation. By performing pre-layout simulations and using accurate models, designers can optimize their designs and mitigate signal integrity issues before PCB fabrication.
Conclusion
Signal integrity is a critical aspect of electronic design that requires careful consideration and attention to detail. By understanding the common signal integrity pitfalls and following best practices, designers can minimize the risk of system failures, performance degradation, and development delays. Proper PCB layout and routing, adequate signal termination, robust power integrity, comprehensive signal integrity simulations, and appropriate high-speed connector selection are essential for ensuring the success of electronic systems. By addressing these pitfalls and adopting a proactive approach to signal integrity, designers can create reliable and high-performance electronic products.
Leave a Reply