Introduction
Designing a printed circuit board (PCB) can be a complex and challenging process, especially when considering the various aspects of fabrication and assembly. To ensure a smooth and successful production process, it is crucial to avoid common design errors that can lead to delays, increased costs, and even product failures. In this article, we will discuss the most common fab and assembly design errors and provide guidance on how to avoid them, ensuring your designs are ready for AltiumLive 2024 and beyond.
Understanding the Fabrication and Assembly Process
Before diving into the common design errors, it is essential to have a basic understanding of the PCB fabrication and assembly process. The fabrication process involves creating the bare PCB, which includes the following steps:
- Material selection and preparation
- Imaging and etching
- Drilling
- Plating
- Solder mask application
- Silkscreen printing
- Surface finish application
Once the bare PCB is fabricated, it moves on to the assembly process, which involves:
- Solder paste application
- Component placement
- Reflow soldering
- Inspection and testing
Understanding these processes will help you make informed decisions during the design phase to avoid potential issues down the line.
Common Fab Design Errors
Incorrect Layer Stack-up
One of the most common fab design errors is an incorrect layer stack-up. The layer stack-up defines the arrangement of copper layers, insulating layers, and their thicknesses. An incorrect stack-up can lead to signal integrity issues, manufacturability problems, and increased costs.
To avoid this error:
- Consult with your fabricator early in the design process to determine the optimal layer stack-up for your design
- Consider the required impedance, signal integrity, and power distribution needs
- Ensure the stack-up is clearly communicated in your design files
Incorrect Drill Sizes and Tolerances
Another common error is specifying incorrect drill sizes and tolerances. This can lead to manufacturing issues, such as incomplete plating, poor hole quality, and difficulty in component assembly.
To avoid this error:
- Use standard drill sizes whenever possible
- Ensure the drill tolerances are appropriate for the hole size and board thickness
- Clearly communicate the drill requirements in your design files
Insufficient Copper Clearance
Insufficient copper clearance between traces, pads, and vias can lead to short circuits and manufacturing defects. It is essential to maintain adequate clearance to ensure proper insulation and prevent unintended connections.
To avoid this error:
- Follow the minimum clearance guidelines provided by your fabricator
- Use design rule checks (DRCs) in your PCB design software to identify and resolve clearance issues
- Consider the manufacturing tolerances when defining clearances
Incorrect Solder Mask and Silkscreen
Solder mask and silkscreen errors can lead to assembly issues and poor board aesthetics. Common errors include insufficient solder mask expansion, incorrect silkscreen polarity, and overlapping silkscreen with exposed copper.
To avoid these errors:
- Follow the solder mask and silkscreen guidelines provided by your fabricator
- Ensure the solder mask expansion is sufficient to prevent solder bridging
- Use a contrasting color for the silkscreen to improve readability
- Verify that the silkscreen does not overlap with exposed copper or solder mask openings
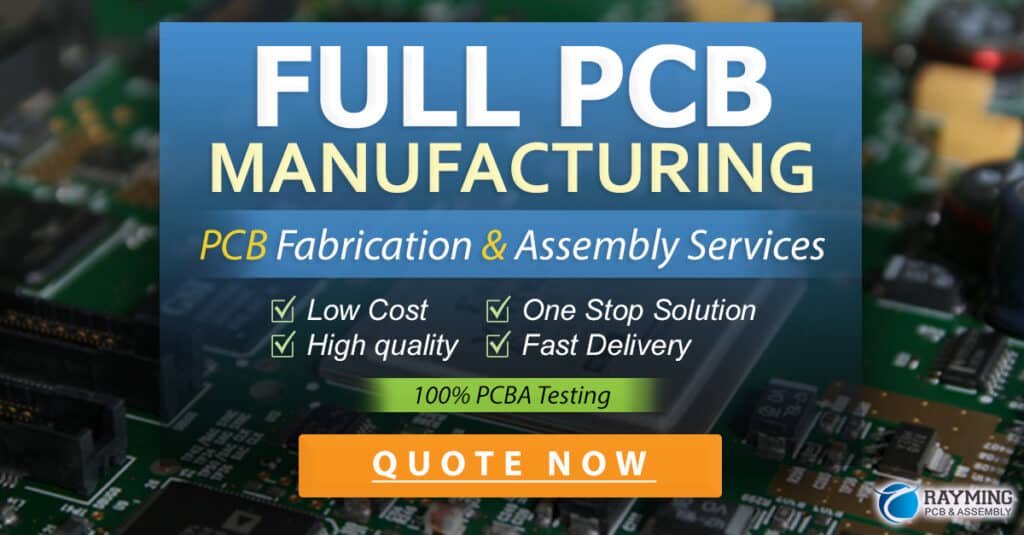
Common Assembly Design Errors
Incorrect Component Footprints
Using incorrect component footprints is a common assembly design error that can lead to component misalignment, soldering issues, and even non-functional boards.
To avoid this error:
- Use verified component footprints from reliable libraries
- Double-check the footprint dimensions against the component datasheet
- Consider the component tolerances and assembly process when designing footprints
Insufficient Solder Paste Clearance
Insufficient solder paste clearance can result in solder bridging, poor joint formation, and difficulty in component placement.
To avoid this error:
- Follow the solder paste clearance guidelines provided by your assembly partner
- Consider the solder paste stencil thickness and aperture design when defining clearances
- Use solder mask defined (SMD) pads when appropriate to improve solder paste control
Incorrect Component Orientation
Incorrect component orientation can lead to assembly errors and non-functional boards. This is particularly important for polarized components, such as capacitors, diodes, and ICs.
To avoid this error:
- Clearly indicate the component orientation on the silkscreen and assembly drawings
- Use consistent and unambiguous orientation markers, such as pin 1 indicators
- Verify the component orientation against the datasheet and schematic
Inadequate Component Spacing
Inadequate component spacing can make assembly difficult, increase the risk of solder bridging, and limit the ability to rework or repair the board.
To avoid this error:
- Follow the component spacing guidelines provided by your assembly partner
- Consider the component size, placement tolerances, and assembly process when defining spacing
- Use component placement optimization tools to ensure adequate spacing and efficient board layout
Best Practices for Fab and Assembly Design
To minimize the risk of design errors and ensure a smooth production process, consider the following best practices:
- Collaborate with your fabricator and assembly partner early in the design process
- Use design for manufacturing (DFM) and design for assembly (DFA) guidelines
- Perform thorough design rule checks (DRCs) and electrical rule checks (ERCs)
- Use reliable component libraries and verify footprints against datasheets
- Create comprehensive and clear design documentation, including fab drawings and assembly drawings
- Consider the manufacturing tolerances and process capabilities when defining design parameters
- Conduct design reviews with stakeholders to identify and address potential issues
By following these best practices and avoiding common design errors, you can create designs that are optimized for fabrication and assembly, reducing the risk of delays, additional costs, and product failures.
Conclusion
Designing PCBs for successful fabrication and assembly requires careful attention to detail and an understanding of the common design errors that can derail the production process. By avoiding errors related to layer stack-up, drill sizes, copper clearance, solder mask, silkscreen, component footprints, solder paste clearance, component orientation, and spacing, you can create designs that are optimized for manufacturing and assembly.
Additionally, by collaborating with your fabrication and assembly partners, using DFM and DFA guidelines, performing thorough design checks, and creating clear documentation, you can further reduce the risk of design errors and ensure a smooth production process.
As you prepare for AltiumLive 2024, keep these guidelines in mind to create high-quality, manufacturable designs that showcase your skills and expertise in PCB design.
FAQs
- What are the most common fab design errors to avoid?
- Incorrect layer stack-up
- Incorrect drill sizes and tolerances
- Insufficient copper clearance
-
Incorrect solder mask and silkscreen
-
What are the most common assembly design errors to avoid?
- Incorrect component footprints
- Insufficient solder paste clearance
- Incorrect component orientation
-
Inadequate component spacing
-
How can I ensure my design is optimized for fabrication and assembly?
- Collaborate with your fabricator and assembly partner early in the design process
- Use design for manufacturing (DFM) and design for assembly (DFA) guidelines
- Perform thorough design rule checks (DRCs) and electrical rule checks (ERCs)
-
Use reliable component libraries and verify footprints against datasheets
-
What should I include in my design documentation?
- Fab drawings with clear layer stack-up, drill sizes, and tolerances
- Assembly drawings with component placement, orientation, and spacing information
- Bill of materials (BOM) with accurate component information
-
Any special instructions or requirements for fabrication and assembly
-
How can I stay up-to-date with best practices for fab and assembly design?
- Attend industry events like AltiumLive to learn from experts and peers
- Participate in online forums and communities dedicated to PCB design
- Read industry publications and blogs to stay informed about the latest trends and techniques
- Collaborate with experienced designers and engineers to gain insights and advice
By understanding and avoiding common fab and assembly design errors, following best practices, and staying informed about industry developments, you can create successful PCB designs that meet the demands of modern electronics manufacturing.
Leave a Reply