Introduction
When it comes to protecting your printed circuit board (PCB) from the elements, you have two main options: coatings and resins. Both serve to shield your PCB from moisture, dust, and other environmental factors that can cause damage over time. However, each option has its own unique set of advantages and disadvantages. In this article, we’ll dive deep into the world of coatings and resins to help you determine which option is best for your specific needs.
What are Coatings?
Coatings are thin layers of protective material that are applied to the surface of a PCB. They can be made from a variety of materials, including acrylics, epoxies, urethanes, and silicones. Coatings are typically applied using a spray, brush, or dip method, and they cure at room temperature or with the application of heat.
Advantages of Coatings
- Easy to apply
- Can be applied selectively to specific areas of the PCB
- Provide good protection against moisture and dust
- Can be easily removed for repairs or modifications
Disadvantages of Coatings
- May not provide adequate protection against harsh chemicals or extreme temperatures
- Can be prone to cracking or peeling over time
- May not fully encapsulate components, leaving them vulnerable to damage
What are Resins?
Resins are thicker, more durable protective materials that are applied to a PCB using a molding or potting process. They are typically made from epoxies, urethanes, or silicones, and they cure through a chemical reaction or with the application of heat.
Advantages of Resins
- Provide excellent protection against moisture, dust, and harsh chemicals
- Can withstand extreme temperatures and physical stress
- Fully encapsulate components, providing maximum protection
- Have a longer lifespan than coatings
Disadvantages of Resins
- More difficult and time-consuming to apply than coatings
- Cannot be easily removed for repairs or modifications
- May require specialized equipment for application
- Can be more expensive than coatings
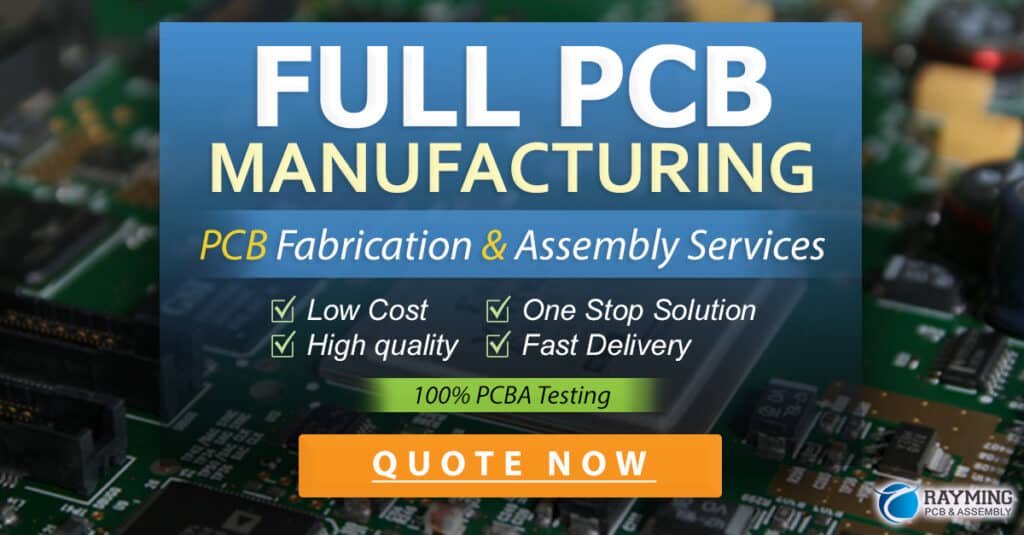
Factors to Consider When Choosing Between Coatings and Resins
When deciding between coatings and resins for your PCB, there are several key factors to consider:
Environmental Conditions
The environmental conditions your PCB will be exposed to should be a primary consideration when choosing between coatings and resins. If your PCB will be exposed to harsh chemicals, extreme temperatures, or high levels of moisture, a resin may be the better choice. However, if your PCB will be used in more moderate conditions, a coating may suffice.
Cost
Coatings are generally less expensive than resins, both in terms of material costs and application costs. If cost is a major factor in your decision-making process, a coating may be the more economical choice.
Repairability
If you anticipate needing to make repairs or modifications to your PCB in the future, a coating may be the better choice. Coatings can be easily removed, allowing you to access the components beneath. Resins, on the other hand, are much more difficult to remove and may require specialized equipment.
Level of Protection Required
The level of protection required for your PCB should also be a key consideration. If your PCB requires maximum protection against moisture, dust, and other environmental factors, a resin may be the better choice. However, if your PCB only requires moderate protection, a coating may be sufficient.
Coating Options
There are several types of coatings available for PCBs, each with its own unique properties and advantages.
Acrylic Coatings
Acrylic coatings are a popular choice for PCBs due to their ease of application and good moisture resistance. They are typically applied using a spray or dip method and cure at room temperature. Acrylic coatings are also relatively inexpensive compared to other coating options.
Epoxy Coatings
Epoxy coatings offer excellent chemical resistance and can withstand high temperatures. They are typically applied using a spray or brush method and require heat to cure. Epoxy coatings are more expensive than acrylic coatings but provide a higher level of protection.
Urethane Coatings
Urethane coatings provide excellent abrasion resistance and can withstand exposure to oils and solvents. They are typically applied using a spray method and cure at room temperature. Urethane coatings are more flexible than epoxy coatings but may not provide as much chemical resistance.
Silicone Coatings
Silicone coatings offer excellent temperature resistance and can withstand exposure to moisture and chemicals. They are typically applied using a spray or dip method and cure at room temperature. Silicone coatings are more expensive than other coating options but provide a high level of protection.
Coating Type | Advantages | Disadvantages |
---|---|---|
Acrylic | – Easy to apply – Good moisture resistance – Inexpensive |
– May not withstand high temperatures – Limited chemical resistance |
Epoxy | – Excellent chemical resistance – Can withstand high temperatures |
– Requires heat to cure – More expensive than acrylic |
Urethane | – Excellent abrasion resistance – Can withstand exposure to oils and solvents – Flexible |
– May not provide as much chemical resistance as epoxy |
Silicone | – Excellent temperature resistance – Can withstand exposure to moisture and chemicals |
– More expensive than other coating options |
Resin Options
There are two main types of resins used for PCB protection: epoxy resins and urethane resins.
Epoxy Resins
Epoxy resins are the most common type of resin used for PCB protection. They offer excellent chemical resistance and can withstand high temperatures. Epoxy resins are typically applied using a potting or molding process and require heat to cure. They are more expensive than urethane resins but provide a higher level of protection.
Urethane Resins
Urethane resins provide excellent moisture resistance and can withstand exposure to oils and solvents. They are typically applied using a potting process and cure at room temperature. Urethane resins are more flexible than epoxy resins but may not provide as much chemical resistance.
Resin Type | Advantages | Disadvantages |
---|---|---|
Epoxy | – Excellent chemical resistance – Can withstand high temperatures |
– Requires heat to cure – More expensive than urethane |
Urethane | – Excellent moisture resistance – Can withstand exposure to oils and solvents – Flexible |
– May not provide as much chemical resistance as epoxy |
Application Methods
The application method you choose for your coating or resin will depend on several factors, including the size and shape of your PCB, the type of coating or resin you are using, and the level of protection required.
Spray Coating
Spray coating is a popular method for applying coatings to PCBs. It involves using a spray gun to apply a thin, even layer of coating to the surface of the PCB. Spray coating is a fast and efficient method that can be used to coat large numbers of PCBs quickly. However, it may not provide as much coverage as other methods, and it can be difficult to control the thickness of the coating.
Brush Coating
Brush coating involves using a brush to apply a coating to the surface of the PCB. This method is often used for small batches of PCBs or for applying coatings to specific areas of the PCB. Brush coating provides good coverage and allows for precise application, but it can be time-consuming and may not provide as smooth a finish as other methods.
Dip Coating
Dip coating involves immersing the PCB in a bath of coating material and then allowing it to drip dry. This method provides excellent coverage and a smooth finish, but it can be messy and may not be suitable for larger PCBs or those with complex shapes.
Potting
Potting involves filling a mold or enclosure with resin and then inserting the PCB into the resin. This method provides maximum protection for the PCB and its components, but it can be time-consuming and may require specialized equipment.
Curing Methods
Once a coating or resin has been applied to a PCB, it must be cured in order to harden and provide maximum protection. There are two main curing methods: room temperature curing and heat curing.
Room Temperature Curing
Room temperature curing involves allowing the coating or resin to harden at room temperature over a period of time. This method is often used for coatings that do not require a high level of protection, such as acrylic coatings. Room temperature curing is a simple and inexpensive method, but it can take several hours or even days for the coating to fully cure.
Heat Curing
Heat curing involves exposing the coating or resin to elevated temperatures in order to speed up the curing process. This method is often used for coatings and resins that require a high level of protection, such as epoxy coatings and resins. Heat curing provides a faster curing time and a harder finish than room temperature curing, but it requires specialized equipment and can be more expensive.
Testing and Inspection
Once a coating or resin has been applied and cured, it is important to test and inspect the PCB to ensure that it meets the required level of protection. There are several methods for testing and inspecting coated and potted PCBs.
Visual Inspection
Visual inspection involves examining the PCB for any defects or irregularities in the coating or resin. This can include looking for bubbles, cracks, or other imperfections that could compromise the protection provided by the coating or resin.
Electrical Testing
Electrical testing involves testing the PCB to ensure that it functions properly and meets the required specifications. This can include testing for continuity, resistance, and other electrical properties.
Environmental Testing
Environmental testing involves exposing the PCB to various environmental conditions, such as high temperatures, humidity, or chemical exposure, to ensure that the coating or resin provides adequate protection. This can help to identify any weaknesses or vulnerabilities in the coating or resin that could lead to failure in real-world conditions.
Choosing the Right Coating or Resin
Choosing the right coating or resin for your PCB can be a complex decision that requires careful consideration of several factors. Here are some tips to help you make the right choice:
- Consider the environmental conditions your PCB will be exposed to and choose a coating or resin that provides adequate protection against those conditions.
- Consider the level of protection required for your PCB and choose a coating or resin that provides the appropriate level of protection.
- Consider the cost of the coating or resin and choose an option that fits within your budget while still providing the necessary level of protection.
- Consider the application and curing methods required for the coating or resin and choose an option that is compatible with your manufacturing process and equipment.
- Consider the repairability of the coating or resin and choose an option that allows for easy repairs or modifications if necessary.
Frequently Asked Questions (FAQ)
1. What is the difference between a coating and a resin?
A coating is a thin layer of protective material that is applied to the surface of a PCB, while a resin is a thicker, more durable material that is applied using a molding or potting process. Coatings provide moderate protection against moisture and dust, while resins provide excellent protection against harsh chemicals and extreme temperatures.
2. How do I choose between a coating and a resin for my PCB?
The choice between a coating and a resin depends on several factors, including the environmental conditions your PCB will be exposed to, the level of protection required, the cost, and the repairability. Consider these factors carefully and choose the option that best meets your specific needs.
3. Can I apply a coating or resin myself, or do I need to hire a professional?
While it is possible to apply some coatings yourself using a spray or brush method, applying a resin typically requires specialized equipment and expertise. Unless you have experience with these processes, it is generally recommended to hire a professional to ensure that the coating or resin is applied correctly and provides the necessary level of protection.
4. How long does it take for a coating or resin to cure?
The curing time for a coating or resin depends on the specific material and curing method used. Room temperature curing can take several hours or even days, while heat curing can be completed in a matter of minutes or hours. Consult the manufacturer’s instructions for specific curing times and requirements.
5. Can a coating or resin be removed if necessary?
Coatings can generally be removed using solvents or abrasive methods, although this may damage the PCB or its components. Resins, on the other hand, are much more difficult to remove and may require specialized equipment or processes. If repairability is a key concern, a coating may be the better choice.
Conclusion
Protecting your PCB from the elements is essential to ensure its long-term reliability and performance. Coatings and resins are two popular options for providing this protection, each with its own unique advantages and disadvantages. When choosing between a coating and a resin, consider factors such as the environmental conditions your PCB will be exposed to, the level of protection required, the cost, and the repairability.
By carefully evaluating your specific needs and choosing the right coating or resin, you can ensure that your PCB is protected against moisture, dust, chemicals, and other environmental hazards. Whether you choose a simple acrylic coating or a durable epoxy resin, investing in the right protection for your PCB can help to extend its lifespan and ensure reliable performance for years to come.
Leave a Reply