Introduction to Trace Impedance
In the world of high-speed digital and RF circuit design, understanding and controlling trace impedance is crucial for ensuring signal integrity and minimizing reflections. Trace impedance refers to the characteristic impedance of a conductive trace on a printed circuit board (PCB) or other substrate. Matching the trace impedance to the impedance of the source and load is essential for optimal signal transmission and reducing signal distortion.
What is Trace Impedance?
Trace impedance is the measure of opposition to the flow of alternating current (AC) in a transmission line, such as a PCB trace. It is determined by the physical properties of the trace, including its width, thickness, and the dielectric constant of the surrounding medium. The characteristic impedance of a trace is typically expressed in ohms (Ω).
Why is Trace Impedance Important?
Maintaining proper trace impedance is critical for several reasons:
- Signal Integrity: Mismatched impedances can lead to signal reflections, causing distortion, ringing, and other signal integrity issues.
- Power Efficiency: Impedance mismatches result in power loss due to reflections, reducing the overall efficiency of the system.
- Electromagnetic Compatibility (EMC): Poor impedance control can contribute to electromagnetic interference (EMI) and affect the EMC performance of the device.
Factors Affecting Trace Impedance
Several factors influence the characteristic impedance of a PCB trace:
Trace Geometry
The physical dimensions of the trace, including its width, thickness, and cross-sectional shape, play a significant role in determining its impedance. Generally, wider traces have lower impedance, while narrower traces have higher impedance.
Dielectric Constant
The dielectric constant (εr) of the PCB substrate material impacts the trace impedance. Materials with higher dielectric constants, such as FR-4, result in lower trace impedance compared to materials with lower dielectric constants, like Rogers laminates.
Trace Spacing
The distance between the trace and the reference plane (ground or power plane) affects the impedance. Increasing the spacing between the trace and the reference plane leads to higher impedance.
Frequency
Trace impedance is frequency-dependent. At higher frequencies, the effective dielectric constant of the substrate material changes, influencing the impedance. Additionally, skin effect and proximity effect become more pronounced at higher frequencies, affecting the current distribution within the trace.
Calculating Trace Impedance
To calculate the characteristic impedance of a PCB trace, various formulas and calculators are available. The choice of formula depends on the trace geometry and the accuracy required.
Microstrip Trace Impedance Formula
For a microstrip trace, which is a trace on the outer layer of a PCB with a single reference plane, the characteristic impedance can be approximated using the following formula:
Z0 = (87 / √(εr + 1.41)) * ln(5.98 * h / (0.8 * w + t))
Where:
– Z0 is the characteristic impedance in ohms (Ω)
– εr is the dielectric constant of the substrate material
– h is the distance between the trace and the reference plane in mils
– w is the width of the trace in mils
– t is the thickness of the trace in mils
Stripline Trace Impedance Formula
For a stripline trace, which is a trace embedded between two reference planes, the characteristic impedance can be calculated using the following formula:
Z0 = (60 / √εr) * ln(4 * b / (0.67 * π * (0.8 * w + t)))
Where:
– Z0 is the characteristic impedance in ohms (Ω)
– εr is the dielectric constant of the substrate material
– b is the distance between the two reference planes in mils
– w is the width of the trace in mils
– t is the thickness of the trace in mils
Online Trace Impedance Calculators
While the formulas provide a good starting point, online trace impedance calculators offer a more convenient and accurate way to determine the characteristic impedance of a trace. These calculators take into account various parameters such as trace geometry, dielectric constant, and layer stack-up to provide precise impedance values.
Some popular online trace impedance calculators include:
- Saturn PCB Toolkit: A comprehensive set of tools for PCB design, including a trace impedance calculator for microstrip and stripline traces.
- EEWeb Impedance Calculator: A simple calculator for microstrip trace impedance based on trace geometry and substrate properties.
- Mantaro Impedance Calculator: Calculates impedance for various trace geometries, including microstrip, stripline, and coplanar waveguide.
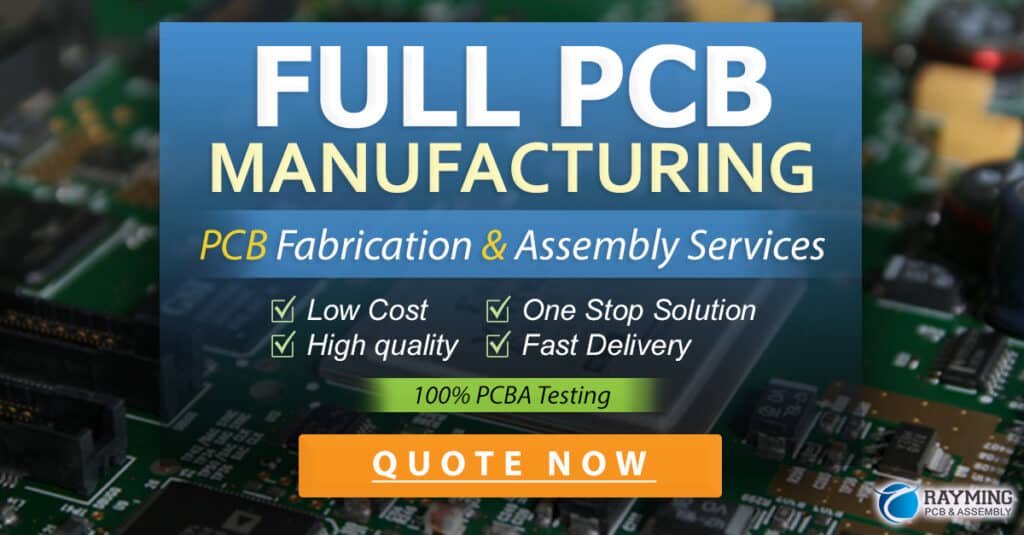
Controlling Trace Impedance
To ensure proper trace impedance in PCB design, consider the following guidelines:
Choose the Right Substrate Material
Select a substrate material with a dielectric constant suitable for your application. Common materials include FR-4, Rogers laminates, and polyimide. Consider the frequency range, cost, and manufacturing constraints when making your choice.
Adjust Trace Geometry
Modify the trace width and thickness to achieve the desired impedance. Use impedance calculators or formulas to determine the appropriate dimensions. Keep in mind the manufacturing limitations and the current-carrying capacity of the trace.
Maintain Consistent Spacing
Ensure consistent spacing between the trace and the reference plane(s) throughout the length of the trace. Avoid abrupt changes in spacing, as they can cause impedance discontinuities.
Use Ground Planes
Incorporate ground planes in the PCB stack-up to provide a stable reference for the traces. Ground planes help maintain consistent impedance and reduce crosstalk between traces.
Perform Impedance Simulation
Utilize PCB design software with built-in impedance simulation tools to analyze and optimize trace impedance. These tools consider the entire PCB stack-up and provide accurate impedance results.
Frequently Asked Questions (FAQ)
- What is the typical impedance value for a PCB trace?
-
Common impedance values for PCB traces are 50Ω and 75Ω, depending on the application. 50Ω is widely used in digital systems, while 75Ω is common in video and RF applications.
-
How does trace impedance affect signal integrity?
-
Mismatched trace impedance can lead to signal reflections, causing distortion, ringing, and other signal integrity issues. Reflections occur when the impedance of the trace does not match the impedance of the source or load, resulting in a portion of the signal being reflected back.
-
Can I use a wider trace to achieve lower impedance?
-
Yes, increasing the trace width generally results in lower impedance. However, it’s important to consider the available space on the PCB and the potential impact on crosstalk and EMI.
-
What is the difference between microstrip and stripline traces?
-
Microstrip traces are located on the outer layer of a PCB, with a single reference plane underneath. Stripline traces are embedded between two reference planes, typically ground planes, providing better shielding and reduced crosstalk compared to microstrip traces.
-
How can I verify the impedance of my PCB traces?
- PCB manufacturers often offer impedance testing services, where they measure the actual impedance of the traces using a time-domain reflectometer (TDR) or other specialized equipment. Additionally, you can perform on-board measurements using a vector network analyzer (VNA) to characterize the impedance of your traces.
Trace Type | Impedance Formula |
---|---|
Microstrip | Z0 = (87 / √(εr + 1.41)) * ln(5.98 * h / (0.8 * w + t)) |
Stripline | Z0 = (60 / √εr) * ln(4 * b / (0.67 * π * (0.8 * w + t))) |
Conclusion
Understanding and controlling trace impedance is essential for designing high-speed digital and RF circuits with optimal signal integrity. By considering factors such as trace geometry, dielectric constant, and spacing, designers can calculate and adjust trace impedance using formulas and online calculators.
Maintaining proper trace impedance ensures efficient power transfer, minimizes reflections, and reduces signal distortion. Following best practices such as selecting the right substrate material, adjusting trace dimensions, maintaining consistent spacing, and utilizing ground planes helps achieve the desired impedance and improves overall system performance.
As PCB designs become more complex and operating frequencies continue to increase, the importance of accurate trace impedance control cannot be overstated. By leveraging the available tools, formulas, and guidelines, designers can effectively manage trace impedance and ensure the reliability and integrity of their high-speed circuits.
Leave a Reply