Introduction to Polyregion on Multilayer PCBs
Polyregions are polygonal copper areas used in multilayer printed circuit board (PCB) designs. They allow designers to define custom copper shapes on inner layers of a PCB stack-up. Polyregions provide flexibility for creating power planes, ground planes, shielding, and other copper structures that span multiple layers.
When designing with polyregions on multilayer PCBs, it’s critical to properly define clearance constraints between the polyregion and other objects, especially pads on the top layer. Insufficient clearance can lead to manufacturing issues and potential short circuits. In this article, we’ll dive deep into the considerations and best practices for defining clearance constraints between polyregions on multilayer and pads on the top layer.
Importance of Clearance Constraints in PCB Design
Clearance constraints specify the minimum distance that must be maintained between copper objects in a PCB design. These constraints help ensure manufacturability, reliability, and proper functionality of the circuit. Some key reasons for defining clearance constraints include:
- Preventing short circuits: Adequate clearance prevents unintended electrical connections between adjacent copper features.
- Ensuring manufacturability: PCB manufacturers have specific clearance requirements based on their fabrication capabilities. Violating these requirements can lead to production delays or higher costs.
- Maintaining signal integrity: Proper clearance helps minimize crosstalk and electromagnetic interference (EMI) between signals.
- Meeting safety standards: Certain industries, such as automotive and medical, have stringent safety requirements that dictate minimum clearance distances.
Factors Affecting Clearance Constraints
Several factors influence the clearance constraints between polyregions on multilayer and pads on the top layer. Understanding these factors is essential for determining appropriate clearance values.
PCB Manufacturing Capabilities
The manufacturing capabilities of the PCB fabricator play a significant role in defining clearance constraints. Factors such as minimum trace width, minimum drill size, and layer registration accuracy impact the achievable clearance distances. It’s crucial to consult with the PCB manufacturer early in the design process to understand their specific capabilities and guidelines.
Manufacturing Capability | Typical Value Range |
---|---|
Minimum trace width | 3-5 mils (0.075-0.13 mm) |
Minimum drill size | 8-12 mils (0.2-0.3 mm) |
Layer registration accuracy | ±2-4 mils (0.05-0.1 mm) |
Voltage and Current Requirements
The voltage and current requirements of the circuit also influence clearance constraints. Higher voltages necessitate greater clearance distances to prevent dielectric breakdown and ensure proper insulation. Similarly, high-current traces may require increased clearance to minimize thermal effects and reduce the risk of shorts caused by copper migration.
Voltage Range | Minimum Clearance |
---|---|
<50V | 5 mils (0.13 mm) |
50-150V | 10 mils (0.25 mm) |
150-300V | 20 mils (0.51 mm) |
>300V | 50 mils (1.27 mm) |
Layer Stack-up and Dielectric Material
The layer stack-up and dielectric material of the PCB impact the clearance constraints. The thickness and dielectric constant of the insulating layers between the polyregion and the top layer pad affect the electrical isolation and parasitic capacitance. Thinner dielectrics and higher dielectric constants may require increased clearance to maintain signal integrity and prevent crosstalk.
Dielectric Material | Dielectric Constant (Dk) | Typical Thickness |
---|---|---|
FR-4 | 4.2-4.5 | 2-3 mils (0.05-0.08 mm) |
Rogers 4003 | 3.38 | 8-10 mils (0.2-0.25 mm) |
Polyimide | 3.5 | 1-2 mils (0.025-0.05 mm) |
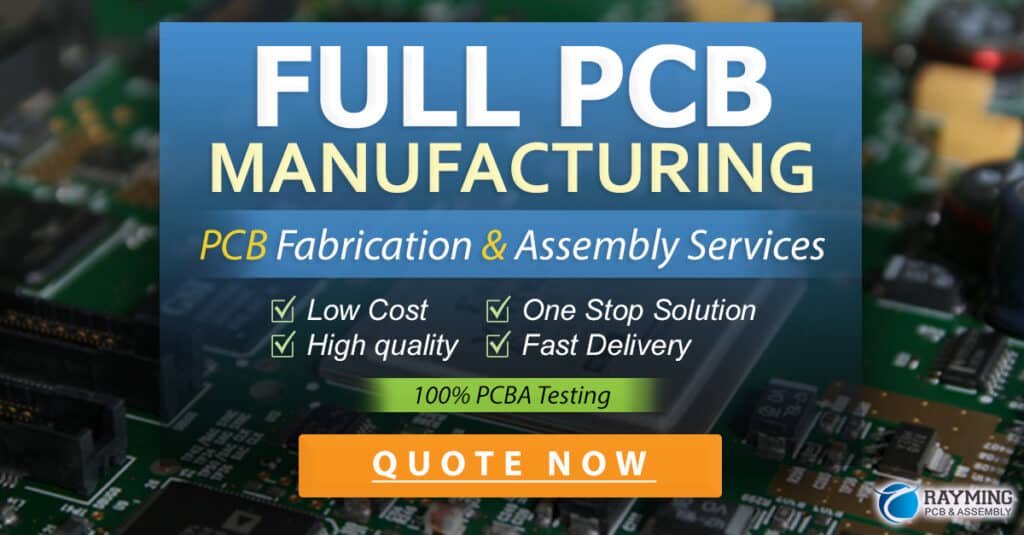
Defining Clearance Constraints in PCB Design Software
Most PCB design software packages provide tools for defining and managing clearance constraints. These tools allow designers to specify minimum clearance distances between various object types, including polyregions and pads.
Creating Clearance Rules
To define clearance constraints, designers typically create clearance rules within their PCB design software. These rules specify the minimum allowable distance between objects based on their type, layer, net, or other attributes. For example, a clearance rule might state: “Minimum clearance between polyregion on inner layers and pad on top layer must be 10 mils.”
Here’s an example of how clearance rules might be defined in a popular PCB design software:
(clearance
(type "Polyregion to Pad")
(layerset "Inner Layers to Top Layer")
(object_types "POLYREGION, PAD")
(constraints
(min_clearance 10)
(min_connected_distance 8)
(max_via_diameter 20)
)
)
Running Design Rule Checks (DRC)
Once clearance rules are defined, designers can run Design Rule Checks (DRC) to verify that the PCB layout complies with the specified constraints. DRC tools analyze the design and flag any violations, providing designers with the opportunity to make necessary adjustments before finalizing the layout.
Most PCB design software packages offer customizable DRC settings, allowing designers to select which rules to check and configure rule parameters. It’s essential to run comprehensive DRC checks, including clearance checks, to ensure the design is manufacturable and meets all requirements.
Best Practices for Managing Clearance Constraints
To effectively manage clearance constraints between polyregions on multilayer and pads on the top layer, consider the following best practices:
-
Collaborate with PCB manufacturers: Engage with PCB manufacturers early in the design process to understand their capabilities, guidelines, and recommendations for clearance constraints.
-
Use a comprehensive layer stack-up: Develop a well-defined layer stack-up that considers the dielectric materials, thicknesses, and impedance requirements of the design. This information helps determine appropriate clearance values.
-
Define clear naming conventions: Establish clear and consistent naming conventions for layers, nets, and object types in the PCB design software. This makes it easier to create and manage clearance rules effectively.
-
Utilize rule hierarchies: Take advantage of rule hierarchies in PCB design software to define general clearance rules at the board level and more specific rules for particular areas or object types.
-
Run frequent DRC checks: Perform DRC checks regularly throughout the design process to catch and resolve clearance violations early, avoiding costly revisions later.
-
Document and communicate constraints: Clearly document clearance constraints and communicate them to all stakeholders, including design team members, manufacturers, and assembly partners.
Frequently Asked Questions (FAQ)
- What is the typical clearance between polyregion on multilayer and pad on top layer?
-
The typical clearance between polyregion on multilayer and pad on top layer varies depending on factors such as manufacturing capabilities, voltage and current requirements, and layer stack-up. Common values range from 5 to 20 mils (0.13 to 0.51 mm), but it’s essential to consult with the PCB manufacturer for their specific guidelines.
-
How do I define clearance constraints in my PCB design software?
-
Most PCB design software packages provide tools for defining clearance constraints through the creation of clearance rules. These rules specify the minimum allowable distance between objects based on their type, layer, net, or other attributes. Consult your software’s documentation or support resources for specific instructions on defining clearance rules.
-
What happens if I violate clearance constraints in my PCB design?
-
Violating clearance constraints can lead to various issues, including manufacturing delays, increased costs, reduced reliability, and potential short circuits. PCB manufacturers may reject designs that do not meet their clearance requirements, forcing designers to revise the layout and causing project delays.
-
Can I use different clearance values for different areas of my PCB?
-
Yes, most PCB design software allows you to define specific clearance rules for different areas, object types, or net classes. This enables designers to optimize clearance values based on the unique requirements of each section of the PCB, such as power regions, high-speed signals, or dense component areas.
-
How often should I run DRC checks for clearance constraints?
- It’s recommended to run DRC checks, including clearance checks, frequently throughout the PCB design process. This helps identify and resolve issues early, minimizing the need for extensive revisions later. Run DRC checks after making significant changes to the layout and before finalizing the design for manufacturing.
Conclusion
Defining and managing clearance constraints between polyregions on multilayer and pads on the top layer is crucial for ensuring the manufacturability, reliability, and functionality of PCB designs. By understanding the factors that influence clearance requirements, utilizing PCB design software tools effectively, and following best practices, designers can create robust and error-free layouts.
Collaborating closely with PCB manufacturers, developing comprehensive layer stack-ups, and regularly running DRC checks are essential steps in the clearance management process. By prioritizing clearance constraints and incorporating them into the design workflow, PCB designers can minimize issues, accelerate time to market, and achieve successful product outcomes.
As PCB technologies continue to evolve, with increasing complexity and miniaturization, the importance of clearance constraints will only grow. Designers must stay informed about the latest manufacturing capabilities, design tools, and industry standards to effectively navigate the challenges of clearance management in multilayer PCB designs.
Leave a Reply