Introduction
Designing electronic circuits for humid environments can be challenging, as moisture can cause various issues such as corrosion, short circuits, and component failures. Proper PCB design and protection measures are crucial to ensure the reliability and longevity of electronic devices operating in high-humidity conditions. In this article, we will discuss circuit design tips and techniques for protecting PCBs from moisture in humid environments.
Understanding the Effects of Moisture on PCBs
Moisture Absorption
PCBs are susceptible to moisture absorption due to the hygroscopic nature of the materials used in their construction, such as FR-4 substrates and solder mask coatings. When exposed to high humidity levels, these materials can absorb moisture from the surrounding environment, leading to various issues.
Corrosion
Moisture can cause corrosion on PCBs, particularly on exposed metal surfaces such as component leads, solder joints, and copper traces. Corrosion can lead to increased resistance, intermittent connections, and eventual failure of the affected components or traces.
Electrochemical Migration
In the presence of moisture and an electric field, metal ions from the PCB’s conductive surfaces can migrate and form dendrites or conductive bridges between adjacent traces. This phenomenon, known as electrochemical migration, can cause short circuits and lead to device malfunction.
Delamination and Warpage
Moisture absorption can also cause delamination and warpage of the PCB substrate. Delamination occurs when the bonding between the copper layers and the substrate weakens, leading to separation and potential reliability issues. Warpage, on the other hand, is the physical deformation of the PCB due to uneven moisture absorption, which can cause stress on components and solder joints.
Circuit Design Tips for Moisture Protection
Choose Appropriate PCB Materials
When designing circuits for humid environments, it is essential to select PCB materials that offer better moisture resistance. Some options include:
- High-Tg FR-4: This is a variant of the standard FR-4 substrate with a higher glass transition temperature (Tg), which improves its resistance to moisture absorption and thermal stress.
- Polyimide: Polyimide-based substrates, such as Kapton, offer excellent moisture resistance and can withstand high temperatures, making them suitable for demanding applications.
- PTFE (Teflon): PTFE-based substrates provide superior moisture resistance and low dielectric constant, making them ideal for high-frequency applications.
Apply Conformal Coating
Conformal coating is a protective layer applied onto the PCB surface to shield it from moisture, dust, and other environmental contaminants. Common conformal coating materials include:
- Acrylic: Acrylic coatings offer good moisture resistance and are easy to apply and repair.
- Silicone: Silicone coatings provide excellent moisture and temperature resistance, as well as flexibility.
- Polyurethane: Polyurethane coatings offer good moisture resistance and mechanical protection.
- Parylene: Parylene coatings are applied through a vapor deposition process and provide excellent moisture barrier properties and conformality.
When selecting a conformal coating, consider factors such as moisture resistance, dielectric strength, thermal stability, and compatibility with the PCB materials and components.
Implement Proper Sealing and Encapsulation
Sealing and encapsulation techniques can provide additional protection against moisture ingress. Some methods include:
- Potting: Potting involves filling the enclosure or specific areas of the PCB with a liquid compound, such as epoxy or silicone, which hardens to form a protective barrier.
- Gaskets and O-rings: Using gaskets and O-rings can help seal the interfaces between the PCB, enclosure, and connectors, preventing moisture from entering the system.
- Conformal shielding: Conformal shielding is a process that involves spraying a conductive coating onto the PCB to provide both EMI shielding and moisture protection.
Optimize Component Selection and Placement
When designing circuits for humid environments, consider the following component selection and placement guidelines:
- Use moisture-resistant components: Select components that are rated for high-humidity environments, such as those with hermetically sealed packages or conformal coatings.
- Avoid moisture-sensitive components: Minimize the use of moisture-sensitive components, such as electrolytic capacitors or certain types of connectors, which can be prone to failure in high-humidity conditions.
- Provide adequate spacing: Ensure sufficient spacing between components and traces to minimize the risk of moisture bridging and electrochemical migration.
- Avoid moisture traps: Design the PCB layout to minimize moisture traps, such as closely spaced components or deep cavities, where moisture can accumulate.
Implement Proper Grounding and Shielding
Proper grounding and shielding techniques can help mitigate the effects of moisture on PCBs:
- Use ground planes: Incorporate ground planes in the PCB design to provide a low-impedance path for moisture-induced currents and to shield sensitive circuits from electromagnetic interference (EMI).
- Shield sensitive circuits: Use shielding techniques, such as metal enclosures or conductive coatings, to protect sensitive circuits from moisture and EMI.
- Implement guard rings: Place guard rings around critical components or traces to divert moisture-induced currents away from sensitive areas.
Enhance Solder Mask and Silkscreen Coverage
Solder mask and silkscreen coatings play a crucial role in protecting the PCB from moisture:
- Maximize solder mask coverage: Apply solder mask coating to as much of the PCB surface as possible, covering exposed copper traces and pads to prevent moisture ingress and corrosion.
- Use a thicker solder mask: Consider using a thicker solder mask layer to provide better moisture protection and mechanical strength.
- Extend silkscreen coverage: Apply silkscreen coating to label and protect components, connectors, and test points, as well as to provide additional moisture barriers.
Implement Moisture Barriers and Drainage
Incorporate moisture barriers and drainage features in the PCB design to prevent moisture accumulation:
- Use conformal coating as a moisture barrier: Apply conformal coating to create a moisture barrier on the PCB surface, preventing moisture from reaching sensitive components and traces.
- Include drainage holes: Incorporate drainage holes in the PCB design to allow moisture to escape and prevent accumulation in cavities or between components.
- Use hydrophobic materials: Apply hydrophobic coatings or materials, such as silicone or fluoropolymers, to repel moisture from critical areas of the PCB.
Consider Thermal Management
Proper thermal management can help reduce the effects of moisture on PCBs:
- Minimize heat generation: Design circuits to minimize heat generation, as high temperatures can accelerate moisture absorption and corrosion.
- Use thermal interface materials: Apply thermal interface materials, such as thermal pads or heat spreaders, to improve heat dissipation and prevent moisture accumulation near heat-generating components.
- Implement active cooling: Consider using active cooling methods, such as fans or thermoelectric coolers, to regulate the temperature and humidity levels within the enclosure.
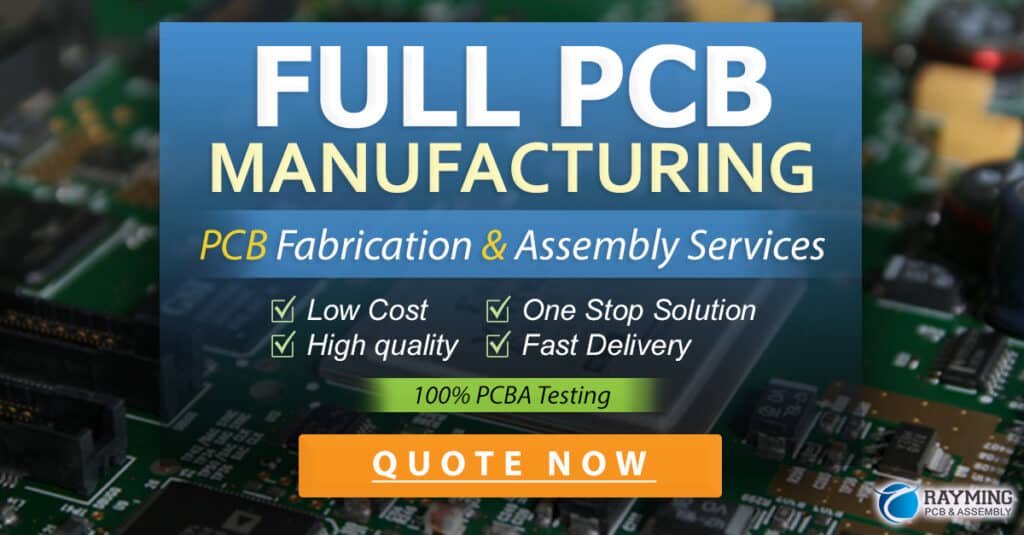
PCB Manufacturing and Assembly Considerations
Moisture-Sensitive Device (MSD) Handling
When working with moisture-sensitive components, follow proper MSD handling procedures:
- Use moisture barrier bags (MBBs): Store moisture-sensitive components in sealed MBBs with desiccants to prevent moisture absorption during storage and transportation.
- Bake components before assembly: Bake moisture-sensitive components according to the manufacturer’s recommendations before assembly to remove absorbed moisture.
- Monitor humidity levels: Monitor and control the humidity levels in the manufacturing and assembly environment to minimize moisture exposure.
Cleaning and Drying
Proper cleaning and drying techniques are essential to remove moisture and contaminants from the PCB:
- Clean PCBs after assembly: Clean the PCB assembly using appropriate cleaning agents, such as isopropyl alcohol or specialized PCB cleaners, to remove flux residues and other contaminants.
- Dry PCBs thoroughly: Ensure that the PCBs are thoroughly dried after cleaning, using methods such as air drying, oven drying, or vacuum drying, to remove any remaining moisture.
- Verify cleanliness: Inspect the PCBs after cleaning and drying to verify that they are free from moisture and contaminants.
Storage and Packaging
Proper storage and packaging methods can help protect PCBs from moisture during transportation and storage:
- Use moisture barrier bags: Store PCBs in moisture barrier bags with desiccants to prevent moisture absorption during storage and transportation.
- Include humidity indicators: Include humidity indicator cards or labels inside the packaging to monitor the humidity levels and ensure that the PCBs remain dry.
- Control storage environment: Store PCBs in a controlled environment with regulated temperature and humidity levels to minimize moisture exposure.
Testing and Validation
Moisture Resistance Testing
Perform moisture resistance testing to evaluate the effectiveness of moisture protection measures:
- Conduct damp heat tests: Subject the PCBs to damp heat tests, such as the IEC 60068-2-78 test, to assess their moisture resistance under high-humidity conditions.
- Perform salt spray tests: Conduct salt spray tests, such as the IEC 60068-2-11 test, to evaluate the PCB’s resistance to corrosion in a salt-laden humid environment.
- Evaluate conformal coating performance: Test the conformal coating’s adhesion, coverage, and moisture barrier properties using methods such as cross-hatch adhesion tests or moisture vapor transmission rate (MVTR) measurements.
Accelerated Life Testing
Perform accelerated life testing to assess the long-term reliability of the PCB in humid environments:
- Conduct temperature cycling tests: Subject the PCBs to temperature cycling tests, such as the IEC 60068-2-14 test, to evaluate their performance under thermal stress and humidity variations.
- Perform humidity-bias testing: Combine humidity exposure with electrical bias to assess the PCB’s resistance to electrochemical migration and other moisture-related failures.
- Evaluate long-term performance: Conduct extended-duration tests under realistic humidity levels to assess the PCB’s long-term reliability and identify potential failure modes.
Frequently Encountered Issues and Solutions
Conformal Coating Defects
- Issue: Poor conformal coating coverage or adhesion.
- Solution: Ensure proper surface cleaning, apply the coating evenly, and follow the manufacturer’s recommendations for curing and thickness.
Moisture Ingress through Connectors
- Issue: Moisture entering the PCB through improperly sealed connectors.
- Solution: Use moisture-resistant connectors, apply conformal coating or sealants around the connector base, and ensure proper mating and sealing.
Component Failures Due to Moisture
- Issue: Moisture-related component failures, such as corrosion or electrical shorting.
- Solution: Use moisture-resistant components, apply conformal coating, and implement proper sealing and encapsulation techniques.
Solder Joint Deterioration
- Issue: Solder joint deterioration due to moisture-induced corrosion or thermal stress.
- Solution: Use a robust solder mask, apply conformal coating, and ensure proper cleaning and drying after assembly.
Electrochemical Migration
- Issue: Electrochemical migration causing short circuits between adjacent traces.
- Solution: Increase trace spacing, use conformal coating, implement guard rings, and maintain proper grounding and shielding.
Table: Comparison of PCB Materials for Moisture Resistance
Material | Moisture Resistance | Temperature Resistance | Dielectric Constant | Cost |
---|---|---|---|---|
High-Tg FR-4 | Good | Good | 4.5 | Medium |
Polyimide | Excellent | Excellent | 3.5 | High |
PTFE (Teflon) | Excellent | Excellent | 2.1 | Very High |
Standard FR-4 | Fair | Fair | 4.7 | Low |
Frequently Asked Questions (FAQ)
-
Q: What is the best conformal coating for moisture protection?
A: The best conformal coating depends on the specific application requirements, such as moisture resistance, thermal stability, and dielectric strength. Common options include acrylic, silicone, polyurethane, and parylene coatings. It is essential to consider the compatibility of the coating with the PCB materials and components, as well as the ease of application and repair. -
Q: How can I test the moisture resistance of my PCB?
A: Moisture resistance testing can be performed using various methods, such as damp heat tests (IEC 60068-2-78), salt spray tests (IEC 60068-2-11), and humidity-bias testing. These tests expose the PCB to controlled humid environments and assess its performance and reliability under these conditions. Additionally, accelerated life testing can be conducted to evaluate the long-term performance of the PCB in humid environments. -
Q: Can I apply conformal coating selectively on my PCB?
A: Yes, conformal coating can be applied selectively to specific areas of the PCB using techniques such as brush coating, spray coating with masking, or automated dispensing. Selective coating allows for the protection of critical components or areas while leaving other parts of the PCB uncoated for easier access or to avoid coating-related issues, such as interference with connectors or switches. -
Q: How do I store moisture-sensitive components before assembly?
A: Moisture-sensitive components should be stored in moisture barrier bags (MBBs) with desiccants to prevent moisture absorption during storage and transportation. The components should be baked according to the manufacturer’s recommendations before assembly to remove any absorbed moisture. It is crucial to monitor and control the humidity levels in the storage environment to ensure that the components remain dry. -
Q: What is the impact of moisture on PCB reliability?
A: Moisture can have a significant impact on PCB reliability, causing issues such as corrosion, electrochemical migration, delamination, and component failures. Moisture-related problems can lead to intermittent connections, short circuits, and overall device malfunction. Proper circuit design, manufacturing processes, and protection measures are essential to mitigate the effects of moisture and ensure the long-term reliability of PCBs in humid environments.
Conclusion
Designing electronic circuits for humid environments requires careful consideration of moisture protection measures to ensure the reliability and longevity of the PCBs. By following the circuit design tips and techniques discussed in this article, such as selecting appropriate PCB materials, applying conformal coating, implementing proper sealing and encapsulation, optimizing component selection and placement, and enhancing solder mask and silkscreen coverage, designers can effectively mitigate the effects of moisture on their PCBs.
Additionally, proper manufacturing and assembly processes, including MSD handling, cleaning, drying, and storage, play a crucial role in protecting PCBs from moisture during production and transportation. Thorough testing and validation, including moisture resistance testing and accelerated life testing, can help evaluate the effectiveness of the moisture protection measures and identify potential issues.
By addressing common moisture-related problems and implementing the solutions provided, designers can overcome the challenges associated with PCB moisture protection in humid environments. The key to success lies in understanding the effects of moisture on PCBs, applying appropriate design and manufacturing techniques, and continuously monitoring and improving the moisture protection measures to ensure the long-term reliability of electronic devices operating in high-humidity conditions.
Leave a Reply