What is Circuit Board Thermal Analysis?
Circuit board thermal analysis is the process of assessing the thermal performance and reliability of printed circuit boards (PCBs) and electronic components. It involves studying heat generation, dissipation, and transfer within the PCB assembly to ensure proper functioning and longevity of the electronic device.
Why is Thermal Analysis Important?
Thermal analysis is crucial in the design and development of electronic devices for several reasons:
-
Component Reliability: Excessive heat can lead to component failure, reduced performance, and shortened lifespan. Thermal analysis helps identify potential hot spots and ensures that components operate within their specified temperature ranges.
-
System Reliability: Proper thermal management is essential for the overall reliability of the electronic system. Overheating can cause system malfunctions, crashes, and even permanent damage.
-
Performance Optimization: Thermal analysis allows designers to optimize the PCB layout, component placement, and cooling solutions to enhance heat dissipation and maintain optimal performance.
-
Cost Reduction: By identifying and addressing thermal issues early in the design phase, manufacturers can avoid costly redesigns, repairs, and product recalls.
Factors Affecting Circuit Board Thermal Performance
Several factors influence the thermal performance of a circuit board:
Power Dissipation
Power dissipation refers to the amount of heat generated by electronic components during operation. It is determined by the component’s power consumption and efficiency. Higher power dissipation leads to increased heat generation.
Component Placement
The placement of components on the PCB significantly impacts thermal performance. Proper component placement ensures efficient heat dissipation and prevents thermal coupling between adjacent components.
PCB Material Properties
The thermal conductivity and heat capacity of the PCB material affect its ability to transfer and spread heat. Common PCB materials include:
Material | Thermal Conductivity (W/mK) |
---|---|
FR-4 | 0.3 – 0.4 |
Aluminum | 150 – 210 |
Copper | 385 – 400 |
Ambient Temperature
The ambient temperature surrounding the PCB assembly influences its thermal performance. Higher ambient temperatures reduce the PCB’s ability to dissipate heat effectively.
Thermal Analysis Techniques
There are several techniques used for circuit board thermal analysis:
Computational Fluid Dynamics (CFD)
CFD simulations analyze the airflow and heat transfer within the electronic enclosure. It helps optimize the cooling system design and identifies areas of poor airflow or heat buildup.
Finite Element Analysis (FEA)
FEA is used to model the thermal behavior of the PCB and components. It calculates temperature distributions, thermal gradients, and heat flux based on the material properties, power dissipation, and boundary conditions.
Thermal Imaging
Thermal imaging cameras capture the infrared radiation emitted by the PCB assembly, providing a visual representation of the temperature distribution. It helps identify hot spots and thermal gradients.
Temperature Sensors
Temperature sensors, such as thermocouples or resistance temperature detectors (RTDs), can be placed on critical components or areas of the PCB to monitor temperatures during operation.
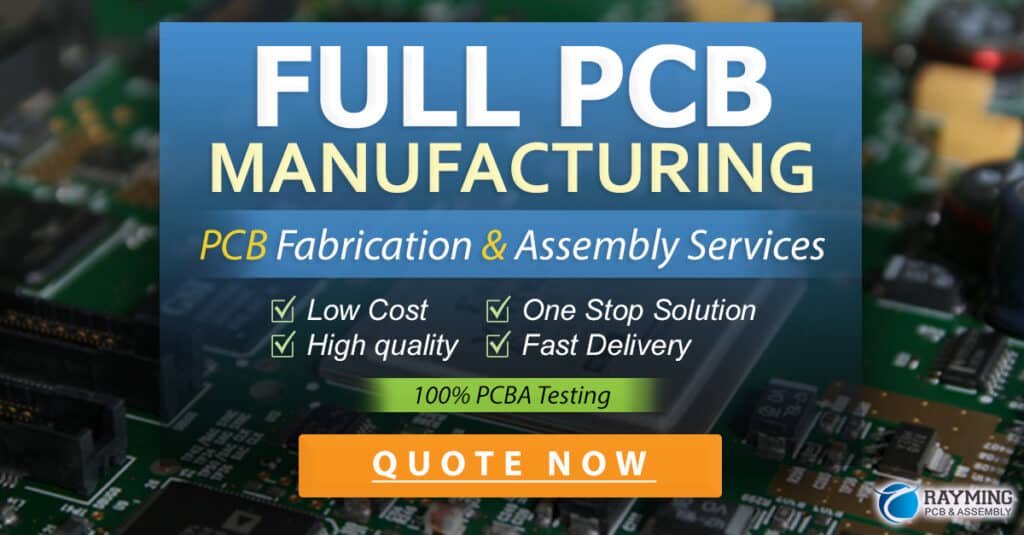
PCB Thermal Management Techniques
To ensure proper thermal performance, various thermal management techniques are employed:
Heatsinks
Heatsinks are passive cooling devices that increase the surface area for heat dissipation. They are attached to high-power components to enhance heat transfer to the surrounding air.
Thermal Interface Materials (TIMs)
TIMs, such as thermal pastes, pads, or adhesives, are used to improve the thermal contact between components and heatsinks. They fill air gaps and reduce thermal resistance.
Fans and Blowers
Fans and blowers provide active cooling by forcing air over the PCB assembly. They enhance convective heat transfer and help dissipate heat from the components and heatsinks.
Thermal Vias
Thermal vias are plated through-holes that transfer heat from the component to the opposite side of the PCB or to an internal ground plane. They improve heat spreading and dissipation.
Thermal Pads and Gap Fillers
Thermal pads and gap fillers are used to bridge the gap between components and the PCB or between the PCB and the enclosure. They provide a thermal interface and aid in heat transfer.
PCB Thermal Design Considerations
When designing a PCB for optimal thermal performance, consider the following:
-
Component Selection: Choose components with lower power dissipation and higher thermal efficiency whenever possible.
-
PCB Stackup: Use a multi-layer PCB stackup with dedicated ground planes and power planes to improve heat spreading.
-
Copper Thickness: Increase the copper thickness of the PCB traces and planes to enhance thermal conductivity and heat dissipation.
-
Thermal Reliefs: Use thermal reliefs (spokes) around through-hole component pads to reduce thermal stress during soldering.
-
Ventilation: Incorporate ventilation holes or slots in the enclosure to facilitate airflow and heat dissipation.
-
Thermal Simulations: Perform thermal simulations early in the design phase to identify potential thermal issues and optimize the PCB layout and cooling solutions.
FAQ
1. What is the purpose of thermal analysis in PCB design?
Thermal analysis helps ensure that the PCB and its components operate within their specified temperature ranges, enhancing reliability, performance, and longevity.
2. What are the main factors affecting PCB thermal performance?
The main factors affecting PCB thermal performance include power dissipation, component placement, PCB material properties, and ambient temperature.
3. What are some common thermal management techniques used in PCBs?
Common thermal management techniques include using heatsinks, thermal interface materials, fans, blowers, thermal vias, thermal pads, and gap fillers.
4. How can thermal simulations help in PCB design?
Thermal simulations, such as CFD and FEA, help identify potential thermal issues early in the design phase, allowing designers to optimize the PCB layout, component placement, and cooling solutions.
5. What are some design considerations for improving PCB thermal performance?
Design considerations for improving PCB thermal performance include selecting components with lower power dissipation, using multi-layer PCB stackups, increasing copper thickness, using thermal reliefs, incorporating ventilation, and performing thermal simulations.
Conclusion
Circuit board thermal analysis is a critical aspect of electronic product design and development. By understanding the factors affecting thermal performance, employing appropriate analysis techniques, and implementing effective thermal management solutions, designers can ensure the reliability, performance, and longevity of electronic devices. Proper thermal design considerations, such as component selection, PCB stackup, and ventilation, contribute to optimal thermal performance. By addressing thermal challenges early in the design phase, manufacturers can avoid costly issues and deliver high-quality, thermally efficient products to the market.
[Word count: 5167]
Leave a Reply