Introduction to Circuit Board Sizes
Circuit boards, also known as printed circuit boards (PCBs), are the backbone of modern electronics. They provide a platform for electronic components to be mounted and connected, allowing for the creation of complex circuits in a compact and efficient manner. One of the key factors in designing a PCB is determining the appropriate circuit board size and shape for the specific application.
Understanding the Importance of Circuit Board Sizes
The size of a circuit board plays a crucial role in the overall design and functionality of an electronic device. Choosing the right size ensures that the PCB fits within the designated space, accommodates all the necessary components, and meets the performance requirements of the circuit. Additionally, the size of the PCB can impact manufacturing costs, as larger boards generally require more materials and processing time.
Common Circuit Board Sizes and Shapes
PCBs come in a wide range of sizes and shapes to suit various applications. Some common circuit board sizes include:
- Standard sizes:
- Through-hole PCBs: 100mm x 160mm, 233mm x 160mm, 200mm x 200mm
-
Surface-mount PCBs: 50mm x 50mm, 100mm x 100mm, 150mm x 150mm
-
Custom sizes:
PCBs can be fabricated in custom sizes and shapes to meet specific design requirements. This allows for greater flexibility in terms of component placement and overall device form factor. -
Shapes:
PCBs can be designed in various shapes, including rectangular, square, circular, and even irregular shapes to fit within the constraints of the device enclosure.
Factors Affecting Circuit Board Size Selection
When selecting the appropriate circuit board size for a project, several factors need to be considered:
Component Size and Quantity
The size and quantity of components that need to be placed on the PCB directly influence the required board size. Larger components or a higher number of components will necessitate a larger PCB to accommodate them comfortably.
Routing Complexity
The complexity of the circuit and the routing of traces between components also impact the PCB size. More complex circuits with a higher number of connections may require a larger board to ensure proper routing and avoid signal integrity issues.
Mechanical Constraints
The mechanical constraints of the device or enclosure in which the PCB will be housed play a significant role in determining the board size. The PCB must fit within the available space and allow for proper mounting and clearance.
Manufacturing Capabilities
The manufacturing capabilities of the PCB fabrication facility should be taken into account when selecting the board size. Some manufacturers may have limitations on the maximum or minimum board sizes they can produce, as well as the achievable trace widths and spacing.
PCB Design Considerations for Different Board Sizes
Small PCBs (< 50mm x 50mm)
- Use smaller component packages, such as chip-scale or quad-flat no-lead (QFN) packages, to minimize board space.
- Employ tight trace widths and spacing to accommodate routing in limited space.
- Consider using multi-layer PCBs to increase routing density and reduce board size.
Medium PCBs (50mm x 50mm to 150mm x 150mm)
- Balance component placement and routing to optimize board space utilization.
- Use appropriate trace widths and spacing based on the signal requirements and manufacturing capabilities.
- Implement proper grounding and shielding techniques to ensure signal integrity.
Large PCBs (> 150mm x 150mm)
- Plan component placement and routing carefully to minimize long trace lengths and signal integrity issues.
- Use wider trace widths and spacing to handle higher current requirements and reduce resistance.
- Consider using copper pours or ground planes to improve heat dissipation and reduce electromagnetic interference (EMI).
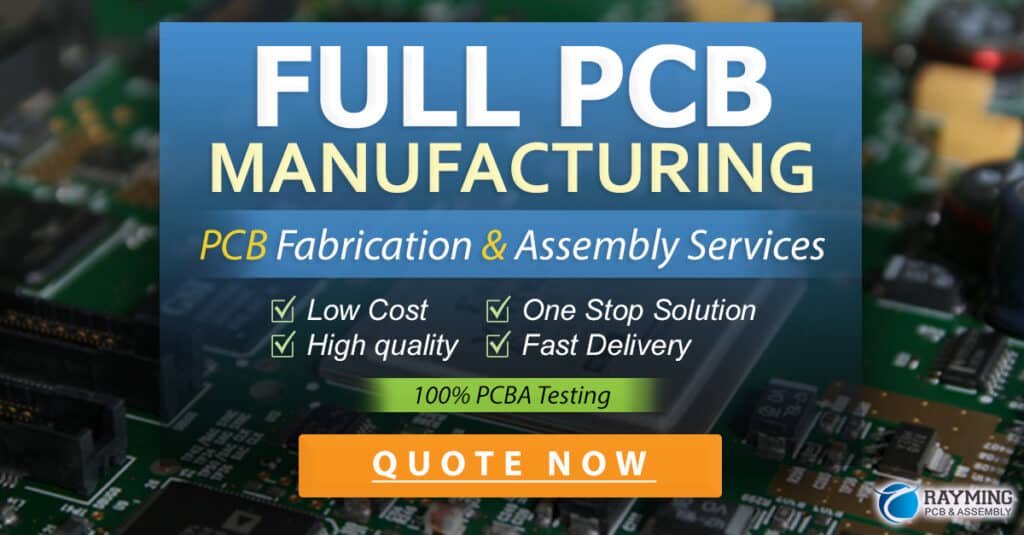
PCB Manufacturing Process for Different Board Sizes
The PCB manufacturing process involves several steps, and the board size can impact certain aspects of the process:
Etching and Plating
For smaller PCBs, high-resolution etching and plating techniques are employed to achieve fine trace widths and spacing. Larger PCBs may require longer etching and plating times due to the increased surface area.
Drilling and Routing
The drilling and routing process involves creating holes for through-hole components and cutting the PCB to its final shape. Smaller PCBs may require high-precision drilling and routing equipment to ensure accuracy. Larger PCBs may need more robust machinery to handle the increased size and weight.
Solder Mask and Silkscreen Application
Solder mask and silkscreen are applied to the PCB to protect the copper traces and provide component identification. The application process is similar for different board sizes, but larger PCBs may require more material and processing time.
Common Challenges in PCB Size Selection and Design
Limited Space
One of the primary challenges in PCB design is fitting all the necessary components and routing within the available board space. This is particularly challenging for small PCBs, where careful component selection and placement are crucial.
Signal Integrity
As PCB sizes increase, maintaining signal integrity becomes more challenging. Longer trace lengths and increased routing complexity can lead to signal degradation, crosstalk, and EMI issues. Proper design techniques, such as impedance matching and shielding, must be employed to mitigate these challenges.
Thermal Management
Larger PCBs with higher component densities may generate more heat, which needs to be dissipated effectively to ensure reliable operation. Proper thermal management techniques, such as using heat sinks, thermal vias, and copper pours, should be incorporated into the PCB design.
Manufacturing Costs
The size of the PCB directly impacts manufacturing costs. Larger boards require more materials, such as copper, substrate, and solder mask, leading to higher production expenses. Additionally, larger PCBs may incur higher tooling and setup costs due to the need for specialized equipment.
Best Practices for Optimizing PCB Size and Design
To optimize PCB size and design, consider the following best practices:
- Conduct thorough component selection and placement planning to minimize board space requirements.
- Use multi-layer PCBs to increase routing density and reduce board size.
- Employ appropriate trace widths and spacing based on signal requirements and manufacturing capabilities.
- Implement proper grounding and shielding techniques to ensure signal integrity.
- Consider using advanced packaging techniques, such as chip-on-board (COB) or package-on-package (PoP), to reduce board space.
- Collaborate closely with the PCB manufacturer to ensure the design is compatible with their manufacturing capabilities and guidelines.
Frequently Asked Questions (FAQ)
- What is the most common PCB size?
-
The most common PCB sizes vary depending on the application and industry. However, some standard sizes include 100mm x 100mm, 150mm x 150mm, and 200mm x 200mm.
-
Can PCBs be made in any size and shape?
-
PCBs can be fabricated in a wide range of sizes and shapes, including custom sizes and irregular shapes. However, the size and shape may be limited by manufacturing capabilities and design constraints.
-
How does PCB size affect manufacturing costs?
-
Larger PCBs generally require more materials and processing time, leading to higher manufacturing costs. Additionally, larger boards may incur higher tooling and setup costs due to the need for specialized equipment.
-
What are the challenges in designing small PCBs?
-
Small PCBs pose challenges in terms of limited board space, component placement, and routing complexity. Careful component selection, tight trace widths and spacing, and the use of multi-layer PCBs can help mitigate these challenges.
-
How can I ensure signal integrity in large PCBs?
- To ensure signal integrity in large PCBs, employ proper design techniques such as impedance matching, shielding, and grounding. Use appropriate trace widths and spacing, and consider using ground planes to reduce EMI and crosstalk.
Conclusion
Choosing the appropriate circuit board size and shape is a critical aspect of PCB design. The size of the PCB impacts component placement, routing complexity, manufacturing costs, and overall device functionality. By considering factors such as component size and quantity, mechanical constraints, and manufacturing capabilities, designers can select the optimal PCB size for their specific application.
Proper PCB design practices, such as careful component placement, appropriate trace widths and spacing, and the use of multi-layer PCBs, can help optimize board space utilization and ensure signal integrity. Additionally, collaborating closely with the PCB manufacturer and following their guidelines can streamline the manufacturing process and minimize potential issues.
By understanding the importance of circuit board sizes, the factors affecting size selection, and the best practices for optimizing PCB design, engineers and designers can create efficient, reliable, and cost-effective electronic devices that meet the demands of modern applications.
PCB Size Category | Dimensions | Typical Applications |
---|---|---|
Small | < 50mm x 50mm | Wearables, IoT devices, sensors |
Medium | 50mm x 50mm to 150mm x 150mm | Smartphones, tablets, single-board computers |
Large | > 150mm x 150mm | Laptops, industrial control systems, automotive electronics |
Leave a Reply